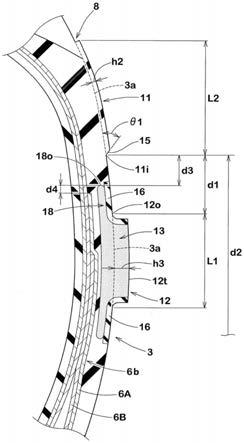
1.本发明涉及一种充气轮胎。
背景技术:2.在下述专利文献1中提出了在胎侧部形成有凸状花纹的充气轮胎。所述充气轮胎在胎侧部的内部具有非黑色橡胶层,所述非黑色橡胶层的一部分在所述凸状花纹的隆起面露出。由此,提高凸状花纹的可视性。另外,非黑色橡胶层在胎侧部的内部以向所述凸状花纹的轮胎径向内外伸出的方式延伸(参照专利文献1、图8)。
3.专利文献1:日本特开2016-203420号公报
技术实现要素:4.近年来,有时希望在胎侧部的外表面,在轮胎径向的内外分别分开形成沿轮胎轴向凸出的隆起部。在一个例子中,轮胎径向外侧的隆起部例如是所谓的胎壁设计部,轮胎径向内侧的隆起部例如是如上所述的凸状花纹。
5.例如,为了提高轮胎的外观,需要使胎壁设计部在轮胎径向上大型化。在这种情况下,在胎侧部的内部,非黑色橡胶层有可能进入到胎壁设计部的内侧。非黑色橡胶与构成由炭黑加强的轮胎的主要部分的黑色橡胶相比,耐切割性显著变差。因此,在上述那样的胎侧部结构中,存在胎壁设计部的耐切割性降低的问题。另外,如果在胎壁设计部产生割伤,则存在非黑色橡胶非本意地从胎壁设计部向外部露出的问题。
6.本发明是鉴于以上的实际情况而提出的,主要目的在于提供一种能够提高胎侧部的耐切割性和外观的充气轮胎。
7.本发明是一种充气轮胎,其具有一对胎侧部,其中,在所述一对胎侧部中的至少一方的胎侧部的外表面上,以向轮胎轴向外侧凸出的方式分别形成有轮胎径向的外侧的第一隆起部和该轮胎径向的内侧的第二隆起部,所述第二隆起部的隆起顶面由与所述第一隆起部的外表面不同颜色的异色橡胶材料形成,所述第一隆起部的轮胎径向的内缘与所述第二隆起部的轮胎径向的外缘之间的轮胎径向的距离d1为所述第二隆起部的轮胎径向的长度l1的40%~220%。
8.在本发明的充气轮胎中,优选为,所述距离d1为所述长度l1的60%~140%。
9.在本发明的充气轮胎中,优选为,所述第一隆起部的最大隆起高度为所述距离d1的20%以下。
10.在本发明的充气轮胎中,优选为,所述第一隆起部在包含轮胎的旋转轴的横截面中包含从所述内缘起以15
°
~80
°
的角度延伸的内侧面。
11.在本发明的充气轮胎中,优选为,所述第一隆起部是包含排列有多个线状突起的锯齿花纹的胎壁设计部。
12.在本发明的充气轮胎中,优选为,所述第一隆起部在胎壁部中包含沿轮胎周向延伸的保护部。
13.在本发明的充气轮胎中,优选为,所述第二隆起部是表示文字或符号的标记部。
14.在本发明的充气轮胎中,优选为,所述第二隆起部的所述异色橡胶材料在所述胎侧部的内部包含延伸部,该延伸部向轮胎径向外侧延伸而超过所述第二隆起部。
15.在本发明的充气轮胎的胎侧部的外表面,以向轮胎轴向外侧凸出的方式分别形成有轮胎径向的外侧的第一隆起部以及该轮胎径向的内侧的第二隆起部。所述第二隆起部的隆起顶面由与所述第一隆起部的外表面不同颜色的异色橡胶材料形成。
16.在本发明的充气轮胎中,优选为,所述第一隆起部的轮胎径向的内缘与所述第二隆起部的轮胎径向的外缘之间的轮胎径向的距离d1为所述第二隆起部的轮胎径向的长度l1的40%~220%。由此,所述异色橡胶材料与所述第一隆起部充分远离地配置。因此,所述第一隆起部的内缘附近的耐切割性提高。另外,防止所述异色橡胶材料在第一隆起部的内缘附近向外部露出,提高胎侧部的外观。
17.另外,在本发明中,由于所述距离d1的上限被规定为所述长度l1的220%,因此能够使所述第一隆起部在轮胎径向上大型化,能够进一步提高胎侧部的外观。
附图说明
18.图1是示出本发明的轮胎的一个实施方式的横剖视图。
19.图2是图1的胎侧部的放大剖视图。
20.图3的(a)~(c)是使第二隆起部硫化成型时的说明图。
21.标号说明
22.3:胎侧部;11:第一隆起部;11i:内缘;12:第二隆起部;12t:隆起顶面;12o:外缘:13:异色橡胶材料。
具体实施方式
23.下面,根据附图对本发明的一个实施方式进行说明。
24.图1示出了本实施方式的标准状态下的充气轮胎(以下,有时简称为“轮胎”。)1的横剖视图。另外,图1是包含轮胎的旋转轴c的横剖视图。如图1所示,本实施方式的轮胎1例如适合使用于设想在柏油路以及不平整地双方行驶的suv用轮胎。但是,本发明并不限定于这样的方式。
[0025]“标准状态”是指在轮胎被安装于标准轮辋(未图示)并且填充了标准内压的无负载的状态。下面,在没有特别说明的情况下,轮胎的各部分的尺寸等是在该标准状态下测定的值。
[0026]“标准轮辋”是在包含有轮胎所依据的规格的规格体系中按照每个轮胎来确定该规格的轮辋,例如如果是jatma则为“标准轮辋”,如果是tra则为“design rim”,如果是etrto则为“measuring rim”。
[0027]“标准内压”是在包含有轮胎所依据的规格的规格体系中按照每个轮胎来确定各规格的空气压,如果是jatma则为“最高空气压”,如果是tra则为表“tire load limits at various cold inflation pressures”中记载的最大值,如果是etrto则为“inflation pressure”。
[0028]
本实施方式的轮胎1具备:胎面部2;一对胎侧部3;分别埋设有胎圈芯5的一对胎圈
部4;以及在胎圈部4之间以环状延伸的胎体6。
[0029]
胎体6例如由第一胎体帘布层6a和第二胎体帘布层6b构成。第一胎体帘布层6a以及第二胎体帘布层6b分别包括胎体帘线和覆盖胎体帘线的贴胶。胎体帘线例如相对于轮胎周向以75
°
~90
°
的角度排列。胎体帘线优选采用例如尼龙、聚酯或人造丝等有机纤维帘线等。
[0030]
胎体6具有主体部6a及折返部6b。主体部6a在一对胎圈部4的胎圈芯5之间延伸。折返部6b与主体部6a相连且绕着胎圈芯5折返而向轮胎径向外侧延伸。本实施方式的折返部6b绕着胎圈芯5从轮胎轴向内侧向外侧折返。另外,在折返部6b中,第一胎体帘布层6a的外端与第二胎体帘布层6b的外端在轮胎径向上错位。
[0031]
本实施方式的胎面部2例如包括带束层7。带束层7例如包括两个带束帘布层7a、7b。各带束帘布层7a、7b例如包括相对于轮胎周向倾斜配置的带束帘线和覆盖该带束帘线的贴胶。各带束帘线优选相对于轮胎周向以10
°
~45
°
的角度倾斜。
[0032]
图2表示胎侧部3的放大剖视图。如图2所示,在一对胎侧部3的至少一方的胎侧部3的外表面形成有轮胎径向的外侧的第一隆起部11以及该轮胎径向的内侧的第二隆起部12。第一隆起部11和第二隆起部12分别形成为从胎侧部3的基准轮廓3a向轮胎轴向的外侧凸出。另外,基准轮廓3a是未设置第一隆起部11及第二隆起部12时的胎侧部3的外表面的轮廓,例如由平滑的弯曲面构成。
[0033]
第二隆起部12的隆起顶面12t由与第一隆起部11的外表面不同颜色的异色橡胶材料13形成。在本实施方式中,包含第一隆起部11的外表面的轮胎的大致整体由黑色橡胶形成,异色橡胶材料13为白色橡胶。
[0034]
在本发明中,第一隆起部的轮胎径向的内缘11i与第二隆起部12的轮胎径向的外缘12o之间的轮胎径向的距离d1是第二隆起部的轮胎径向的长度l1的40%~220%。
[0035]
由此,异色橡胶材料13与第一隆起部11充分远离地配置。因此,第一隆起部11的内缘11i附近的耐切割性提高。另外,通常,当第一隆起部11和第二隆起部12接近配置时,它们之间的厚度小的区域容易局部变形,在所述区域容易发生损伤。在本发明中,由于确保了第一隆起部11与第二隆起部12之间的距离,因此抑制了它们之间的区域的局部变形,提高了其耐久性。通过上述作用,防止异色橡胶材料13在第一隆起部11的内缘11i附近露出到外部,提高胎侧部3的外观。
[0036]
另外,在本发明中,由于所述距离d1的上限被规定为所述长度l1的220%,因此能够使第一隆起部11在轮胎径向上大型化,能够进一步提高胎侧部3的外观。
[0037]
为了可靠地发挥上述效果,所述距离d1优选为所述长度l1的60%~140%。
[0038]
第一隆起部11整体由黑色橡胶构成。因此,第一隆起部11的轮胎轴向内侧的区域由黑色橡胶构成。
[0039]
第一隆起部11形成为由文字、符号或图形构成的花纹。本实施方式的第一隆起部11构成为包含排列有多个线状突起的锯齿花纹的胎壁设计部。第一隆起部11也可以包括在胎壁部8中沿轮胎周向延伸的保护部。另外,胎壁部8是胎侧部3中与胎面部2(图1所示)的端部比较接近的区域。
[0040]
第一隆起部11例如配置于比轮胎1的最大宽度位置靠轮胎径向外侧。从胎圈基线bl(图1所示)到第一隆起部11的内缘11i的轮胎径向的距离d2例如为轮胎截面高度h1(图1
所示,以下相同。)的60%~80%。另外,如图1所示,胎圈基线bl是指通过由轮胎所基于的规格确定的轮辋径向位置的轮胎轴向线。轮胎截面高度h1相当于从胎圈基线bl到胎面部2的轮胎径向的外端2t的轮胎径向的距离。
[0041]
如图2所示,第一隆起部11的最大隆起高度h2例如为所述距离d1的20%以下,优选为3%~10%。由此,第二隆起部12的异色橡胶材料13难以向第一隆起部11侧移动,能够防止异色橡胶材料13在第一隆起部11的内缘11i附近露出。
[0042]
从同样的观点出发,第一隆起部11的轮胎径向的长度l2例如优选为轮胎截面高度h1的10%~20%。
[0043]
第一隆起部11包括从内缘11i延伸的内侧面15。内侧面15在包含轮胎的旋转轴的横截面中朝向轮胎轴向外侧向轮胎径向外侧倾斜。内侧面15相对于基准轮廓3a的角度θ1例如为15
°
~80
°
,优选为30
°
~50
°
。由此,第一隆起部11的内缘11i处的耐切割性能提高。
[0044]
第二隆起部12例如形成为包括轮胎最大宽度位置。但是,本发明并不限定于这样的方式。
[0045]
第二隆起部12的轮胎径向的长度l1例如是轮胎截面高度h1的5%~15%。第二隆起部12的最大隆起高度h3优选大于第一隆起部11的最大隆起高度h2。第二隆起部12的所述隆起高度h3例如是第一隆起部11的所述隆起高度h2的2.0倍~5.0倍。由此,异色橡胶材料13难以向第一隆起部11侧移动。
[0046]
图3的(a)~(c)是表示轮胎制造时的第二隆起部12的形成工序的说明图。如图3的(a)~(c)所示,第二隆起部12是通过硫化模具17使异色橡胶材料13以及由覆盖该异色橡胶材料13的黑色橡胶构成的覆盖橡胶层16硫化成型而形成的。第二隆起部12在硫化成型后通过抛光等除去配置在其上表面的覆盖橡胶层16,形成由异色橡胶材料13构成的隆起顶面12t。
[0047]
因此,如图2所示,第二隆起部12的隆起顶面12t由异色橡胶材料13形成,侧面通过由黑色橡胶构成的覆盖橡胶层16形成。
[0048]
异色橡胶材料13包括在胎侧部3的内部向轮胎径向外侧延伸而超过第二隆起部12的延伸部18。从第一隆起部11的内缘11i到延伸部18的轮胎径向的外端18o的轮胎径向的距离d3例如为所述距离d1的30%以上,优选为40%以上。由此,能够可靠地防止异色橡胶材料13在第一隆起部11的内缘11i附近露出。另一方面,若所述距离d3过大,则有可能在第二隆起部12的隆起顶面12t残留黑色橡胶。因此,所述距离d3例如为所述距离d1的70%以下,优选为60%以下。
[0049]
优选在延伸部18的轮胎轴向内侧配置有胎体6的折返部6b。在本实施方式中,仅折返部6b的第一胎体帘布层6a配置在延伸部18的轮胎轴向的内侧。另外,折返部6b的第二胎体帘布层6b配置在第二隆起部12的轮胎轴向的内侧。更具体而言,折返部6b的第二胎体帘布层6b的轮胎径向的外端配置在比第二隆起部12的外缘12o靠轮胎径向内侧。由此,适当地提高延伸部18周边的刚性,抑制延伸部18周边的变形。因此,能够抑制第一隆起部11和第二隆起部12之间的区域中的覆盖橡胶层16的剥离。
[0050]
延伸部18的外端18o与折返部6b的外端之间的轮胎径向的距离d4例如为所述距离d1的20%以下,优选为15%以下。由此,能够可靠地得到上述的作用效果。
[0051]
以上,对本发明的充气轮胎的优选实施方式详细地进行了说明,但是本发明不限
于上述具体的实施方式,能够变更为各种方式来实施。
[0052]
【实施例】
[0053]
根据表1的规格试制了具有图1的基本结构的尺寸265/70r17的充气轮胎。作为比较例1~比较例3,试制出第一隆起部的轮胎径向的内缘与第二隆起部的轮胎径向的外缘之间的轮胎径向的距离d1小于第二隆起部的轮胎径向的长度l1的40%的轮胎。比较例1~比较例3的轮胎除了上述的结构以外,具有与实施例的轮胎实质上相同的结构。对于每个测试轮胎,测试了耐切割性能。各测试轮胎的共通规格和测试方法如下。
[0054]
轮辋:17
×
8.0
[0055]
轮胎内压:220kpa
[0056]
<耐切割性能>
[0057]
在鼓试验机上加载固定的纵向载荷,使测试轮胎以固定的速度行驶。另外,使测试轮胎行驶至在第一隆起部与第二隆起部之间的区域产生切割等损伤为止,测定产生所述损伤时的轮胎的行驶距离。结果是将比较例1的所述行驶距离设为100的指数,数值越大,表示胎侧部的耐切割性能越优异。
[0058]
测试的结果在表1~2中示出。
[0059]
【表1】
[0060][0061]
【表2】
[0062][0063]
从测试的结果能够确认出,实施例的轮胎发挥了优异的耐切割性能。另外,能够确认出,实施例的测试轮胎均充分地确保了第一隆起部的长度,胎侧部的外观也得到了提高。