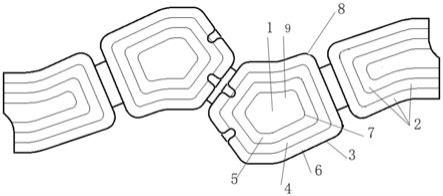
1.本实用新型涉及轮胎,尤其是涉及一种轮胎的块状花纹块。
背景技术:2.如图3所示,普通花纹块结构,花纹块表面是在轮胎胎冠曲面上切割形成,而胎冠曲面为一段或多段曲线以轮胎轴线为旋转轴旋转形成。因此,普通花纹块表面表现为一段平整的曲面,而边部多为近似直角的尖锐棱边。
3.这样的花纹块结构,在接地受压状态下,花纹块受径向和侧向压缩力,花纹块挤压变形,因橡胶材料的不可压缩性,花纹块橡胶将会产生横向膨胀,橡胶向花纹块边部膨胀,而花纹块边沿的尖锐棱边切入地面导致膨胀受阻,这样就造成橡胶材料在花纹块边部堆积,在花纹块边部形成接地压力及应力集中;同时,花纹块边部材料堆积,间接导致花纹块中心区域接地应力减小;在非接地中心区域,花纹块同时受横向挤压变形,在这些区域,受复杂作用力影响,花纹块表面应力变现为极度不均匀的状态。借助有限元仿真手段,我们可以直观的看到这种因花纹块橡胶材料在边部堆积、及花纹块受复杂作用力影响而造成的不均匀应力分布状态,从而造成花纹块的不均匀磨损,具体表现为花纹块边部快速磨损、切割严重,以及花纹块的畸形磨损,严重影响轮胎整体寿命和外观。
技术实现要素:4.为解决上述问题,本实用新型提供一种轮胎的块状花纹块,有效缓解传统结构的花纹块边部堆积效应及由此造成的接地压力/应力不均匀分布状态,从而提高轮胎使用寿命。
5.本实用新型的目的是以下述方式实现的:一种轮胎的块状花纹块,花纹块表面为不平整的曲面,且花纹块周边边沿比花纹块周边边沿内侧低。
6.轮胎的块状花纹块上设有至少一圈环状凸起,并且环状凸起使得花纹块周边边沿比花纹块周边边沿内侧低。
7.花纹块中心点与花纹块周边边沿之间设有环状凸起,花纹块中心点位于环状凸起的内部。
8.环状凸起的内外轮廓线与环状凸起所在的花纹块整体的外侧轮廓分别平行。
9.花纹块中心点与花纹块周边边沿之间设有一圈环状凸起,花纹块中心点位于环状凸起的内部。
10.花纹块中心点与花纹块周边边沿之间设有至少两圈环状凸起,花纹块中心点位于这些环状凸起的内部。
11.沿轮胎花纹表面法向方向,环状凸起最高点位置比花纹块中心点0.5~3mm。
12.沿轮胎花纹表面法向方向,环状凸起最高点位置比花纹块周边边沿高0.5~3mm。
13.环状凸起与花纹块中心点、花纹块周边边沿之间分别通过平滑曲面平滑连接。
14.环状凸起位于花纹块中心点到花纹块边沿距离的1/2~3/4区域。
15.本实用新型提供的轮胎的块状花纹块,花纹块表面为不平整的曲面,且花纹块周边边沿比花纹块周边内侧低,从而花纹块周边内侧部位先接地,边部尚未接地,从而有横向膨胀的空间,可以有效缓解边部堆积效应。
16.花纹块中心点与花纹块周边边沿之间设有一圈环状凸起,花纹块中心点位于环状凸起的内部,借助仿生学原理,参照动物脚/手掌结构,如人类脚/手掌、大象脚掌等,表面表现为内部凹陷,向外有一圈环形凸起。这类结构在接地受压时,环状凸起先接地,此时花纹块周边边沿及花纹块中心点尚未接地,给橡胶的横向膨胀留出空间,环状凸起受压产生横向膨胀,既可以填补环状凸起内部的凹陷区域,也可以填补环状凸起外部的凹陷区域,可以有效缓解传统结构的花纹块边部堆积效应及由此造成的接地压力/应力不均匀分布状态,从而提高轮胎使用寿命。
附图说明
17.图1是本实用新型的块状花纹块的结构示意图。
18.图2是图1中块状花纹块的侧视轮廓线结构示意图。
19.图3是现有技术中普通花纹块的结构示意图。
具体实施方式
20.下面结合具体实施例对本实用新型进行具体描述,有必要在此指出的是本实施例只用于对本实用新型进行进一步说明,不能理解为对本实用新型保护范围的限制,该领域的技术熟练人员可以根据上述本实用新型的内容做出一些非本质的改进和调整。
21.如图1和图2所示,一种轮胎的块状花纹块,花纹块表面为不平整的曲面,且花纹块周边边沿3比花纹块周边边沿内侧低。花纹块周边边沿3比花纹块周边边沿内侧低,从而花纹块周边边沿内侧部位先接地,花纹块周边边沿3尚未接地,从而有横向膨胀的空间,可以有效缓解传统结构的花纹块边部堆积效应及由此造成的接地压力/应力不均匀分布状态,从而提高轮胎使用寿命。
22.轮胎的块状花纹块上设有至少一圈环状凸起2,并且环状凸起2使得花纹块周边边沿3比花纹块周边边沿内侧低。
23.块状花纹块的中心点的简称花纹块中心点1。这里块状花纹块的中心点为如图1所示的块状花纹块的平面图形的重心。
24.花纹块中心点1与花纹块周边边沿3之间设有环状凸起2,花纹块中心点1位于环状凸起2的内部,从而花纹块在接地受压时,环形凸起2先接地,此时环状凸起2内部及环状凸起2外部尚未接地,给橡胶的横向膨胀留出空间,环状凸起2受压产生横向膨胀,既可以向环状凸起2内部填补比环状凸起2低的凹陷区域,也可以向环状凸起2外部填补比环状凸起2低的区域,可以有效缓解传统结构的花纹块边部堆积效应及由此造成的接地压力/应力不均匀分布状态,从而提高轮胎使用寿命。
25.花纹块中心点1也可以不位于环状凸起2的内部。
26.花纹块中心点1与花纹块周边边沿3之间设有一圈环状凸起2,花纹块中心点1位于环状凸起2的内部。借助仿生学原理,参照动物脚/手掌结构,如人类脚/手掌、大象脚掌等,表面表现为内部凹陷,向外有一圈环状凸起。这类结构在接地受压时,环状凸起2先接地,此
时花纹块周边边沿3及花纹块中心点1及它们紧邻区域尚未接地,给橡胶的横向膨胀留出空间,环状凸起2受压产生横向膨胀,既可以填补环状凸起2内部的凹陷区域,也可以填补环状凸起2外部填补比环状凸起2低的区域,可以有效缓解传统结构的花纹块边部堆积效应及由此造成的接地压力/应力不均匀分布状态,从而提高轮胎使用寿命。
27.本技术花纹块的表面设计为在现有普通花纹设计基础上增加环状凸起2。
28.花纹块中心点1与花纹块周边边沿3之间也可以设有2圈环状凸起2、3圈环状凸起2、4圈环状凸起2、5圈环状凸起2或5圈以上环状凸起2,花纹块中心点1都位于这些环状凸起2的内部。
29.环状凸起2可以圆环状凸起,椭圆环状凸起、方形环状凸起、不规则形状的环状凸起或两圈不规则曲线形成的环状凸起。
30.沿轮胎花纹表面法向方向,环状凸起最高点位置比花纹块中心点1高0.5~3mm。
31.沿轮胎花纹表面法向方向,环状凸起最高点位置比花纹块周边边沿3高0.5~3mm,这样有利于轮胎花纹整体均匀磨损。
32.环状凸起2与花纹块中心点1、花纹块周边边沿3之间分别通过平滑的曲面平滑连接,增强花纹表面整体性及降低模具加工难度。这里的曲面包括特殊的曲面——平面。
33.环状凸起2位于花纹块中心点1到花纹块周边边沿3距离的1/2~3/4区域之内,可以充分降低轮胎接地时的花纹表面应力分布。如环状凸起2可以完全占有花纹块中心点7到花纹块周边边沿3距离的1/2~3/4区域,也可以完全占有花纹块中心点7到花纹块周边边沿3距离的1/2~2/7区域,也可以完全占有花纹块中心点7到花纹块周边边沿3距离的3/8~9/14区域。
34.实验验证:
35.在相同充气压力、相同负荷状态(800kpa充气压力、63000kg负荷)下,比较本实用新型提供的花纹块结构与普通花纹块结构的应力,本技术的花纹块与普通花纹块除花纹块上表面结构不同外,其他都相同。
36.如图3示意图所示,普通花纹块表面为一段平整的曲面。
37.如图1示意图所示,本实用新型的花纹块表面结构为:花纹块中心点1与花纹块周边边沿3之间设有一圈环状凸起2,这里环状凸起2的宽度相同,且环状凸起2的内外轮廓线与环状凸起所在的花纹块整体的外侧轮廓—花纹块周边边沿3分别平行。环状凸起2在宽度方向的中心设有等宽的等高面4,等高面4也为环状;等高面4内侧连接通过与等高面4等宽的内平滑过渡曲面5平滑连接环状凸起2的内轮廓线7,等高面4内侧通过与等高面4等宽的外平滑过渡曲面6平滑连接环状凸起2的外轮廓线8,环状凸起2内部形成花纹块中心区域9,花纹块中心区域9等高,这里环状凸起2的外轮廓线与花纹块周边边沿3重合,也即环状凸起2包括内平滑过渡曲面5、等高面4和外平滑过渡曲面6。
38.本技术的花纹块中心区域9与在普通花纹块中的设置相同,即无修改。如图2示意图所示,等高面4的宽度为25mm,等高面4与花纹块中心区域9、花纹块周边边沿3之间分别通过与等高面4等宽的、平滑的曲面—内平滑过渡曲面5和外平滑过渡曲面6平滑连接。沿轮胎花纹表面法向方向,等高面4的高度比花纹块中心区域9的高度高1.5mm,沿轮胎花纹表面法向方向,等高面4的高度比花纹块周边边沿3的高度高2.0mm。花纹块中心区域9的面积为11260mm2,内平滑过渡曲面5面积为12737mm2,等高面4面积为17356mm2,外平滑过渡曲面6面
积为21601mm2。
39.通过仿真技术,得到接地表面应力分布状态图,在相同表征尺度下,与普通花纹块相比,本实用新型的花纹块结构表面应力分布更均匀,边部应力集中效应明显改善。
40.结果:在相同充气压力、相同负荷状态下,相比于普通花纹块结构,本实用新型所述的花纹块结构表面最大接地应力降低50%,本实用新型的花纹块结构相较于现有技术中普通花纹块设计可以使花纹块接地最大压力可以降低25%,可有效缓解轮胎使用过程中出现的花纹块畸形磨损及花纹块边沿割伤、快速磨损问题,从而提升轮胎使用寿命。
41.以上所述的仅是本实用新型的优选实施方式,但本实用新型的保护范围并不局限于此,应当指出,对于本领域的及任何熟悉本技术领域的技术人员来说,在不脱离本实用新型整体构思前提下,根据本实用新型的技术方案及其实用新型构思加以等同替换或改变,及作出的若干改变和改进,这些也应该视为本实用新型的保护范围。