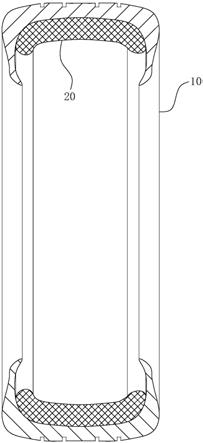
1.本实用新型属于轮胎静音技术领域,具体涉及一种静音轮胎。
背景技术:2.近年来,随着汽车的普及,消费者对汽车的使用舒适性提出了更高的要求,其中降低轮胎空腔共振噪声就是一项非常重要的指标。轮胎空腔共振噪声是由路面输入激励,使轮胎和盘式车轮构成的超低压声响系统共振引起的噪声,通常也被称为轮胎共鸣音。空腔噪声频率在200
‑
300hz之间,是由轮胎空腔结构决定的。在行驶过程中,空腔共振频率会分离成两个,产生两个急剧峰值,产生的声压压迫耳膜,给司乘人员带来非常不适的感觉。目前降低轮胎空腔噪声最常用的技术,是在轮胎胎面内壁上粘附海绵等吸音材料,从而吸收空腔噪声,市面上的静音轮胎由此而来。虽然这种方法可以有效降低轮胎的空腔噪声,但仍存在以下问题:其一,现有的技术采用的是轮胎内壁涂抹胶水,然后把吸音材料贴上去,这种状态下,吸音材料没有张力。当在轮胎内表面的胎面部相对应的区域内粘合了带状的吸音材料时,伴随着轮胎的行驶,用来固定吸音材料的粘合层会因发热而发生软化或劣化,随后存在吸音材料容易从轮胎内表面剥离的问题。在高速行驶时,吸音材料甚至可能会突然脱落,严重危及行车安全。其二,当轮胎被刺穿胎面后,需打磨修补,此时需拆除原有吸音材料,这会对原有吸音材料造成不可逆的损坏,使静音轮胎失去其降噪效果,这也是传统静音轮胎所亟待解决的一个重大问题。
技术实现要素:3.本实用新型的目的是克服上述现有技术的不足,提供一种静音轮胎,其能在确保降低轮胎空腔噪声的前提下,实现了轮胎内吸音材料的便拆装功能,其使用可靠性及安全性亦可得到有效保证。
4.为实现上述目的,本实用新型采用了以下技术方案:
5.一种静音轮胎,包括轮胎本体以及布置于轮胎本体内腔中的起吸音功能的弹性吸音层,其特征在于:弹性吸音层的两侧边分别向轮胎本体的两胎侧部处延伸并抵紧在相应胎侧部上,从而使弹性吸音层与胎侧部间形成胀紧式的固接配合关系。
6.优选的,所述弹性吸音层为吸音海绵。
7.优选的,弹性吸音层外形呈与轮胎本体同轴的圆环构造。
8.优选的,在轮胎本体的轴向截面上,弹性吸音层的截面外形呈与轮胎本体的内腔外形匹配的槽口朝向轮胎本体轴线的扩口槽状。
9.优选的,所述弹性吸音层的最大宽度比两胎侧部之间距离大5%~10%。
10.优选的,所述弹性吸音层的外侧面与轮胎本体的胎面部形成面贴合配合。
11.优选的,所述弹性吸音层与胎面部之间夹设有一层自封胶层;弹性吸音层、自封胶层及胎面部由内而外逐一叠合且两两间形成面贴合配合。
12.本实用新型的有益效果在于:
13.1)、抛弃了传统的弹性吸音层必然依靠粘合层粘附在胎面部的固有构造,转而取消粘合层,并将弹性吸音层向胎侧部延伸,直至胀紧在胎侧部。工作时,利用弹性吸音层与轮胎本体的胎侧部的胀紧力所产生的摩擦力,以及轮胎本体高速回转时所产生的离心力,足以确保轮胎内壁与弹性吸音层的附着力满足安全使用需求。这样,一方面,由于抛弃了粘合层,就不存在可能发生的吸音材料的意外掉落问题;另一方面,当轮胎需要打磨修补时,可直接拆下弹性吸音层,待修补完毕后重新装配上即可,操作极为方便快捷。
14.综上,本实用新型能在确保降低轮胎空腔噪声的前提下,实现了轮胎内吸音材料的便拆装功能,其使用可靠性及安全性亦可得到有效保证。
15.2)、作为上述方案的进一步优选方案,弹性吸音层可使用多种方式实现,如采用吸音橡胶或其他材质的多孔板体等;甚至在必要时,使用无弹力或少弹力的中间吸音结构,并在中间吸音结构的两边设置弹力部件或弹力层等来抵靠胎侧层,该类复合结构一样能实现其在轮胎本体宽度方向上的弹性胀紧功能,当然也均属于弹性吸音层的范畴内。本实用新型优选采用吸音海绵,吸音海绵本身既可制作为一体式的带状体或环状体等固定形态,本身又具备天然的弹性,显然能满足本实用新型的便捷使用需求。
16.3)、具体使用时,弹性吸音层为圆环结构,也即闭环式而非传统吸音海绵的带式结构。采用闭环结构的弹性吸音层,不仅可以依靠自身向外的径向张力,来提升弹性吸音层相对轮胎本体内壁的抵紧力,同时在进行装拆操作时,整出整入,显然操作便捷度也能得到进一步提升。
17.4)、进一步的,弹性吸音层的横截面为扩口槽状,这样可使得弹性吸音层的两槽壁能更好的撑住相应的胎侧部,以进一步提升弹性吸音层与轮胎本体内壁的附着力,确保其工作安全性及可靠性。更具体而言,弹性吸音层的最大宽度比两胎侧部之间距离大5%~10%,目的均在于提升前述附着力,此处就不再赘述。
18.5)、实际装配时,对于普通轮胎,弹性吸音层的外侧面与轮胎本体的胎面部形成面贴合配合即可,这样,弹性吸音层的两侧抵紧在胎侧部,外侧面抵紧在胎面部,在轮胎本体的高速旋转下,可保证弹性吸音层的工作可靠性。而对于防爆轮胎,可在弹性吸音层与胎面部之间夹设有一层自封胶层;弹性吸音层、自封胶层及胎面部由内而外逐一叠合且两两间形成面贴合配合。在防爆轮胎中增加上述结构后,不仅弹性吸音层可正常可靠工作,同时自封胶层自带的粘性也更好的固定弹性吸音层,确保在不影响弹性吸音层正常装拆的同时,进一步提升其工作可靠性及稳定性,一举多得。
附图说明
19.图1为本实用新型的其中一种实施例的剖视示意图;
20.图2为图1所示结构的局部结构立体图;
21.图3为图1所示结构的局部剖面图;
22.图4为本实用新型的另一种实施例的剖视示意图;
23.图5为图4所示结构的局部结构立体图;
24.图6为图4所示结构的局部剖面图;
25.图7为弹性吸音层的立体结构示意图。
26.本实用新型各标号与部件名称的实际对应关系如下:
27.10
‑
轮胎本体 11
‑
胎侧部 12
‑
胎面部
28.20
‑
弹性吸音层 30
‑
自封胶层
具体实施方式
29.为便于理解,此处结合图1
‑
7,对本实用新型的具体结构及工作方式作以下进一步描述:
30.本实用新型的具体实施例构造,有图1
‑
3及图4
‑
6两种,其根本目的均在于采用如图7所示的环形吸音海绵或其他具备弹性力的吸音材料来形成弹性吸音层20,并根据轮胎本体10的内腔尺寸一次成型。其中:
31.在图1
‑
3所示具体实施例中,可看出,弹性吸音层20的外侧面或者说是外侧槽底是直接贴合在胎面部12的,而弹性吸音层20的两外侧槽壁则胀紧配合在胎面部12两侧的两胎侧部11上。实际设计时,甚至可使弹性吸音层20的最大宽度比轮胎本体10处两胎侧部11之间距离要大%5~10%;这样,当弹性吸音层20放进轮胎本体10的内腔中,弹性吸音层20的两侧会迅速和胎侧部11接触,并依靠弹性吸音层20的张力产生弹性吸音层20与胎侧部11的摩擦力,不需要粘合层即可稳定的配合在轮胎本体10内腔中。尤其是在高速行驶时,由于离心力作用,弹性吸音层20的使用可靠性反而会进一步提升,且不会脱落。修补轮胎本体10时,只需拿下弹性吸音层20,也不会对轮胎本体10造成破坏;修补完毕后甚至可重新将拿下的弹性吸音层20装配上去,仍然能够正常实现静音效果。此外,由于弹性吸音层20需要胀紧配合两侧的胎侧部11,这使得弹性吸音层20整个的体积比较大,显然吸收噪音的面积也大,整体吸音效果相对普通静音轮胎而言也更好。
32.图4
‑
6所示的具体实施例与图1
‑
3区别不大,唯一在于在弹性吸音层20与轮胎本体10的胎面部12之间增设了一层自封胶层30,从而使得本实用新型兼具了防爆和静音双重功能。值得注意的是,图4
‑
6所示的轮胎结构,不仅弹性吸音层20可正常可靠工作,同时自封胶层30自带的粘性也更好的固定弹性吸音层20,确保在不影响弹性吸音层20正常装拆的同时,进一步提升其工作可靠性及稳定性,成效显著。
33.优选的,弹性吸音层20呈现如图7所示的槽口朝内的环形扩口槽结构,这使得当弹性吸音层20实际装配时,能如图3及图6所示的以可靠的抵紧力和足够的配合面积胀紧配合在胎侧部11上。在高速行驶时,由于离心力作用,阔口槽状的弹性吸音层20的两外侧槽壁也会因与轮胎本体10内壁的斜面配合而进一步提升弹性吸音层20相对轮胎本体10内壁的附着力,使用安全性可得到进一步提升。
34.值得注意的是:实际使用时,弹性吸音层20也可以为开式的带状或其他外形,只需能确保实现相对轮胎本体10内腔的胀紧紧固目的即可。在必要时,如槽体采用无弹力或弹力不足的吸音板而两侧槽壁使用高弹性材料,或者槽体与槽壁均为无弹性力或弹力不足的吸音材料,但两者之间通过弹力圈等弹性结构衔接,也能确保整个弹性吸音层20在宽度方向上的弹性力,诸如这类结构均应当在弹性吸音层20这一概念的保护范围内。
35.当然,对于本领域技术人员而言,本实用新型不限于上述示范性实施例的细节,而且在不背离本实用新型的精神或基本特征的情况下,能够以其他的具体形式实现本实用新型。因此,无论从哪一点来看,均应将实施例看作是示范性的,而且是非限制性的,本实用新型的范围由所附权利要求而不是上述说明限定,因此旨在将落在权利要求的等同要件的含
义和范围内的所有变化囊括在本实用新型内。不应将权利要求中的任何附图标记视为限制所涉及的权利要求。
36.此外,应当理解,虽然本说明书按照实施方式加以描述,但并非每个实施方式仅包含一个独立的技术方案,说明书的这种叙述方式仅仅是为清楚起见,本领域技术人员应当将说明书作为一个整体,各实施例中的技术方案也可以经适当组合,形成本领域技术人员可以理解的其他实施方式。
37.本实用新型未详细描述的技术、形状、构造部分均为公知技术。