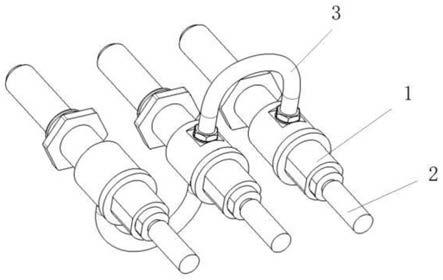
1.本发明属于充电设备制造技术领域,具体涉及一种端子冷却结构及一种直流充电装置冷却系统。
背景技术:2.随着电动汽车逐渐的普及,新能源汽车的市场越来越大,与其息息相关的充电设备也变得尤为重要,在对新能源汽车充电时,端子温度会急剧上升,温度过高会带来安全隐患,造成人员烧伤烫伤,甚至车辆起火燃烧等事故;温度过高也会使得充电功率受限,充电功率越大,发热就越严重,若充电功率过小,又会导致充电时间过长,造成用户时间成本增加,同时温度过高会降低端子的使用寿命,带来过高的维护成本。当前的端子冷却方式也有采用液冷的,但是端子内部虽然设置有用于液冷的小直径圆柱空腔,但是不能形成有效地循环,所以只能通过传导散热,不能通过循环散热,散热效率很低。因此,现有技术中亟需一种新的方案来解决上述问题。
技术实现要素:3.为了提高端子的冷却效率,本发明提供了一种端子冷却结构及一种直流充电装置冷却系统,能够快速、有效地降低端子温度。
4.本发明解决其技术问题所采用的技术方案是:
5.一方面,本发明提供了一种端子冷却结构,包括连接管、导电端子和冷却管,所述导电端子具有密封腔体,所述冷却管的至少一端设置在所述密封腔体内;
6.所述导电端子为至少两个,每个所述导电端子的密封腔体上均设置有连接孔,所述连接孔通过所述连接管连通。
7.所述密封腔体和所述冷却管的横截面均为圆形,所述密封腔体的内径大于所述冷却管的外径。
8.所述密封腔体横截面的半径与所述冷却管横截面的半径的比为1:0.25-1:0.92。
9.所述连接管的横截面为圆形,所述密封腔体横截面的半径与所述连接管横截面的半径的比为1:0.3-1:0.86。
10.所述密封腔体和所述冷却管同心设置。
11.所述密封腔体与所述冷却管一体成型。
12.所述冷却管设置在所述密封腔体内的一端为内端口,所述内端口与所述连接孔的距离与所述密封腔体长度的比为0.35:1-0.9:1。
13.所述导电端子的表面设置有漏液传感器。
14.所述密封腔体内部设置有液体泄漏传感器。
15.所述连接孔上设置有水管接头,所述连接管套接在所述水管接头上。
16.所述水管接头外周设置有一个或多个凸起,所述连接管为弹性材质,所述水管接头与所述连接管过盈配合。
17.所述凸起为倒钩状。
18.所述水管接头上设置有外螺纹,所述连接管与所述水管接头螺接。
19.所述冷却管包括设置在密封腔体内的弯曲段。
20.所述弯曲段为螺旋状。
21.所述弯曲段的长度与所述冷却管位于所述密封腔体内总长度的比值为10%-100%。
22.所述密封腔体内设置有分割板,所述分割板将所述密封腔体分为连通的两个容腔,一个容腔内设置冷却管,另一个容腔上设置所述连接孔。
23.所述密封腔体与所述冷却管的连接处为入口,两个所述容腔的连通处位于所述密封腔体内距离所述入口的最远端。
24.所述冷却管位于容腔内的长度小于等于5cm。
25.所述导电端子上设置有温度传感器。
26.本发明还提供了一种直流充电装置冷却系统,包括如上所述的端子冷却结构、输入泵、冷却介质和冷却装置;
27.两个所述导电端子分别为正极导电端子和负极导电端子;所述正极导电端子和所述负极导电端子内中的一个所述冷却管为输入管,另一个为输出管,所述输入管与所述输入泵连接,所述冷却装置一端与所述输出管连接,另一端与所述输入泵连接,所述输入泵用于将所述冷却介质输入输入管。
28.所述冷却介质为冷却气体、冷却液体或冷却固体。
29.所述冷却介质的冷却速率大于等于0.5℃/min。
30.本发明的有益效果是:通过至少两个导电端子内设置冷却管,并由水管接头导通密封腔体,使端子的冷却结构形成一个完整的回路,可以快速、有效地降低端子温度。冷却液从冷却管的端口进入密封腔体,从连接管流出密封腔体的结构使冷却液与导电端子内部的接触更充分,冷却效率更高。水管接头能够使连接管的安装更方便,密封更彻底。温度传感器能够监控导电端子的冷却效果,能为工作人员调节冷却液的供给速度提供依据。
附图说明
31.构成本技术的一部分的说明书附图用来提供对本发明的进一步理解,本发明的示意性实施例及其说明用于解释本发明,并不构成对本发明的不当限定。
32.图1是本发明一种端子冷却结构的结构示意图。
33.图2是本发明一种端子冷却结构的剖视图。
34.图3是本发明一种端子冷却结构导电端子为两个的结构示意图。
35.图4是本发明一种端子冷却结构的水管接头的结构示意图。
36.图5是本发明一种端子冷却结构的弯曲段结构示意图。
37.图6是本发明一种端子冷却结构的分割板的结构示意图。
38.图中:1-导电端子、2-冷却管、3-连接管、4-水管接头、5-分割板、12-密封腔体、13-连接孔、21-内端口、22-弯曲段。
具体实施方式
39.需要说明的是,在不冲突的情况下,本技术中的实施例及实施例中的特征可以相互组合。下面将参考附图并结合实施例来详细说明本发明。
40.一方面,本发明公开了一种端子冷却结构,如图1-图3所示,包括连接管3、导电端子1和冷却管2,所述导电端子1具有密封腔体12,所述冷却管2的至少一端设置在所述密封腔体12内;所述导电端子1为至少两个,每个所述导电端子1上均设置有连接孔13,所述连接孔13通过所述连接管3连通。以两个端子为例,如图3所示,冷却管2的一端位于密封腔体12内,另一端位于密封腔体2外,冷却液或者冷却气体从一个冷却管2进入一个导电端子1的密封腔体12,从该密封腔体12的连接孔13经连接管3进入另一个导电端子1的密封腔体12,再从该密封腔体12内的冷却管2流出,冷却液或冷却气体经冷却设备冷却后再进入冷却管2形成一个完整的循环过程,从而达到对充电端子1冷却的目的。连接管3与连接孔13间可以设置密封垫或者通过密封胶进行密封连接。导电端子1也可以为3个或更多,冷却液从其中一个导电端子1内的冷却管2进入,从其他导电端子1的冷却管2输出。或者,冷却液从多个导电端子1的冷却管2进入,从一个导电端子1的冷却管2输出。
41.在一些实施方式中,所述密封腔体12和所述冷却管2的横截面均为圆形,所述密封腔体12的内径大于所述冷却管2的外径。圆形的设计更方便插拔,不容易对密封腔体12表面造成伤害。冷却管2比密封腔体12半径小,冷却液从冷却管2进入密封腔体12,再从连接管3流出该密封腔体12。此外,密封腔体12和所述冷却管2的截面也可以是椭圆形、多边形等根据需要设计的各种图形。
42.在一些实施方式中,所述密封腔体12横截面的半径与所述冷却管2横截面的半径的比为1:0.25-1:0.92。冷却管2过细则冷却液会出现供给不足的情况,而冷却管2过粗则冷却管2和密封腔体12之间的空隙过小,单位时间流过的冷却液不足也会导致冷却不充分。为了选择合理的密封腔体12横截面的半径与所述冷却管2横截面的半径的比为,发明人进行了相关试验,试验方法是选用相同的导电端子1,每个导电端子1具有相同的密封腔体12,选择半径不相同的冷却管2,对导电端子1的温度进行测量,将采集的温度值收集,温度最小的为最佳温度,将所有温度值与最佳温度做差取绝对值,绝对值大于0.5℃为不合格,结果记录在表1中。
43.表1:密封腔体横截面的半径与所述冷却管横截面的半径的比对冷却效果的影响
44.比值1:0.231:0.251:0.321:0.401:0.501:0.581:0.661:0.731:0.851:0.921:0.94温差(℃)0.510.480.420.330.280.110.0.180.380.460.52
45.从表1可以看出,密封腔体12横截面的半径与所述冷却管2横截面的半径的比为1:0.66时,冷却效果最佳。密封腔体12横截面的半径与所述冷却管2横截面的半径的比大于1:0.25或小于1:0.92时,测量的温度和最佳温度的温差超过0.5℃,当密封腔体12横截面的半径与所述冷却管2横截面的半径的比小于等于1:0.25或大于等于1:0.92后,测量的温度与最佳温度相同的温差在0.5℃以内,均为合格。因此,发明人优选的密封腔体12横截面的半径与所述冷却管2横截面的半径的比为1:0.25-1:0.92。
46.在一些实施方式中,所述连接管3的横截面为圆形,所述密封腔体12横截面的半径与所述连接管3横截面的半径的比为1:0.3-1:0.86。密封腔体12与冷却管2的和合理比值有助于冷却液的充分流动,但是冷却液的流动也和连接管3有关。为了寻找合适的密封腔体12
横截面的半径与所述连接管3横截面的半径的比,发明人进行了相关试验,试验方法是选用相同的导电端子1,每个导电端子1具有相同的密封腔体12,选择半径不相同的连接管3,通电一段事件后,对导电端子1的温度进行测量,将采集的温度值收集,温度最小的为最佳温度,将所有采集的温度值与最佳温度做差取绝对值,绝对值大于0.5℃为不合格,结果记录在表2中。
47.表2:密封腔体横截面的半径与所述连接管横截面的半径的比对冷却效果的影响
48.比值1:0.281:0.31:0.381:0.461:0.521:0.591:0.661:0.721:0.801:0.861:0.88温差(℃)0.520.480.410.350.270.210.150.10.0300
49.如表2所示,当所述密封腔体12横截面的半径与所述连接管3横截面的半径的比大于等于1:0.86时,冷却效果最好,导电端子1的温度为最佳温度。当所述密封腔体12横截面的半径与所述连接管3横截面的半径的比为小于1:0.3后,也就是说连接管3过细时,冷却效果不足,导电端子1的温度与最佳温度的差值大于0.5℃,因此,发明人选择当所述密封腔体12横截面的半径与所述连接管3横截面的半径的比的最大值为1:0.3,而当比值小于1:0.86后,继续增加连接管3的半径已经没有意义,且由于导电端子1自身半径的限制,也使得连接管3很难增加半径。因此发明人优选所述密封腔体12横截面的半径与所述连接管3横截面的半径的比为1:0.3-1:0.86。
50.在一些实施方式中,所述密封腔体12和所述冷却管2同心设置。这样冷却液与密封腔体12各个位置的接触更均匀,能达到更好的冷却效果。
51.在一些实施方式中,所述密封腔体12与所述冷却管2一体成型。一体成型的连接位置可以在冷却管2插入密封腔体12的连接处。一体成型能够使密封效果更好,能够避免因为有连接处导致的漏液或漏气。
52.在一些实施方式中,冷却管2设置在所述密封腔体12内的一端为内端口21,所述内端口21到所述连接孔13的距离与所述密封腔体12长度的比为0.35:1-0.9:1。内端口21与连接孔13的距离越远,冷却液在密封腔体12内流动的距离越长,对导电端子1的冷却效果越好,但是也要考虑连接口13能否设置。为了选择合理的内端口21与所述连接孔13的距离与所述密封腔体12长度的比,发明人进行了相关试验,试验方法是选用相同的导电端子1,每个导电端子1具有相同的密封腔体12,选择半径相同的冷却管2,冷却管2的内端口21与连接孔13的距离不同,对导电端子1的温度进行测量,温度最小值为最佳温度,将所有测量得到的温度与最佳温度做差取绝对值,绝对值大于0.5℃为不合格,结果记录在表3中。
53.表3:内端口21到连接孔13的距离与密封腔体12长度的比对冷却效果的影响
54.比值0.32:10.35:10.43:10.51:10.58:10.66:10.72:10.78:10.85:10.9:10.92:1温差(℃)0.510.480.420.330.280.230.190.120.100
55.从表3可以看出,内端口21与连接孔13的距离与密封腔体12长度的比大于等于0.9:1时,降温效果最好,为最佳温度。内端口21与连接孔13的距离与密封腔体12长度的比小于0.32:1时,测量的温度和最佳温度的温差超过0.5℃,当内端口21与连接孔13的距离与密封腔体12长度的比大于等于0.35:1后,测量的温度与最佳温度相同的温差在0.5℃以内,均为合格。当内端口21与连接孔13的距离与密封腔体12长度的比大于等于0.9:1时,测量的温度和最佳温度已经没有差别,而当内端口21与连接孔13的距离与密封腔体12长度的比更大时,连接管3很难找到合适的安装位置,因此,发明人优选的内端口21与连接孔13的距离
与密封腔体12长度的比为0.35:1-0.9:1。为达到这种比例,可以有两种选择,一种是如图2所示,内端口21接近密封腔体12的最里面,但是不与密封腔体12贴合以便冷却液流出,而将连接孔13的设置位置尽可能的远离内端口21,以达到冷却液和密封腔体12充分接触的目的。另一种选择是将连接孔13设置在密封腔体12的最远处,内端口21设置在刚刚进入密封腔体12的位置,也能达到使冷却液与密封腔体12充分接触的目的,但是可能存在某些冷却液没有充分流动的情况,因此发明人优选第一种设置方式。
56.在一些实施方式中,所述导电端子1的表面设置有漏液传感器。一旦密封腔体12中有液体泄漏出来,漏液传感器就会检测到并通过数据线将发生漏液的信息传递出来,工作人员可以立刻进行处理。具体的漏液传感器可以为漏水感应绳。
57.在一些实施方式中,所述密封腔体12内部设置有液体泄漏传感器。液体泄漏传感器可以通过监测密封腔体12内的压强、压力、流量或流速来判断密封腔体是否出现泄漏的情况。当有异常发生,工作人员能够通过液体泄漏传感器了解异常并及时处理。
58.在一些实施方式中,所述连接孔13上设置有水管接头4,如图4所示,所述连接管3套接在所述水管接头4上。水管接头4一端与连接孔13连通,另一端与连接管3连通,单独设置水管接头4更容易与连接孔13连接也更容易进行密封。
59.进一步的,所述水管接头4外周设置有一个或多个凸起,所述连接管3为弹性材质,所述水管接头4与所述连接管3过盈配合。连接管3可以为橡胶材质,通过与水管接头4上的凸起过盈配合来达到密封的效果。
60.更进一步的,所述凸起为倒钩状。如图2所示,倒钩状能够增加凸起与水管接头4的接触强度,起到更好的密封效果。
61.在一些实施例中,所述水管接头4上设置有外螺纹,所述连接管3与所述水管接头4螺接。连接管3上可以设置与连接管3套接的螺帽,螺帽可以转动以拧在外螺纹上,水管接头4和螺帽之间可以设置密封圈增强防漏性能。
62.在一些实施例中,所述冷却管2包括设置在密封腔体内12的弯曲段22。如图5所示当冷却管2的材质为硬质材料时,可以将冷却管2设计成一部分为弯曲段22,弯曲段22能够增加密封腔体内的冷却管2的长度,增加冷却效果。
63.在一些实施例中,所述弯曲段22为螺旋状。螺旋状能够使冷却管2内与冷却管2外的冷却液接触更充分,热交换更均匀。
64.在一些实施例中,所述弯曲段22的长度与所述冷却管1位于所述密封腔体12内总长度的比值为10%-100%。也就是说,密封腔体12内的冷却管1可以全为弯曲段22,也可以只有部分为弯曲段22。如果弯曲段22的长度过小,对冷却效果的提升帮助不大,因此,发明人进行了相关试验来选择合适的密封腔体12内冷却管1中弯曲段22的长度。试验方法为选择相同的导电端子1,不同的弯曲段22占比,进行测量,测量的温度值与最佳温度值进行比较,将所有测量得到的温度与最佳温度做差取绝对值,绝对值大于0.5℃为不合格,。结果如表4所示。
65.表4:弯曲段的长度与所述冷却管位于所述密封腔体内总长度的比值却效果的影响
66.比值(%)8%10%2030405060708090100温差(℃)0.510.480.450.330.280.220.150.1000
67.从表4可知,当弯曲段22的长度与所述冷却管2位于所述密封腔体12内总长度的比值大于等于80%后,为最佳温度。同样可知,当弯曲段22的长度与所述冷却管2位于所述密封腔12体内总长度的比值小于10%时,测量温度与最佳温度的差大于0.5℃。所以发明人优选弯曲段22的长度与所述冷却管2位于所述密封腔体12内总长度的比值为10%-100%。
68.在一些实施例中,所述密封腔体12内设置有分割板,如图6所示,所述分割板将所述密封腔体分为连通的两个容腔,一个容腔内设置冷却管,另一个容腔上设置所述连接孔13。冷却管2中的冷却液只进入一个容腔,然后从两个容腔的连接处进入另个一容腔,再从连接孔13及连接管3进入另一个导电端子1
69.在一些实施例中,所述密封腔体12与所述冷却管的连接处为入口,两个所述容腔的连通处位于所述密封腔体内距离所述入口的最远端。也就是说,尽量增加冷却液在两个容腔的流动行程以达到更好的冷却效果。
70.在一些实施例中,所述冷却管2位于容腔内的长度小于等于5cm。当连通处远离入口,冷却管2在容腔内的长度尽量减小以增加冷却液的流动距离。为了验证冷却管2位于容腔内的长度对冷却效果的影响,发明人进行了相关实验。选择相同的导电端子1,且每个导电端子1的内部容腔也相同,导电端子1通电一段时间后,发明人对容腔内的不同长度的冷却管2的导电端子1进行测量,温度最小值为最佳温度,将所有测量得到的温度与最佳温度做差取绝对值,绝对值大于0.5℃为不合格,结果记录在表5中。
71.表5:冷却管位于容腔内的长度对冷却效果的影响
72.长度(cm)5.254.64.13.63.22.51.81.20.50温差(℃)0.510.480.420.330.280.230.190.120.100
73.从表5可以看出,冷却管2位于容腔内的长度小于等于0.5cm降温效果最好,为最佳温度。冷却管2位于容腔内的长度大于5.2cm时,测量的温度和最佳温度的温差超过0.5℃,当冷却管2位于容腔内的长度小于等于5cm时,测量的温度和最佳温度的温差不大于0.5℃,因此发明人优选冷却管2位于容腔内的长度小于等于0.5cm
74.在一些实施方式中,所述导电端子1上设置有温度传感器。温度传感器能够实时监控导电端子1的工作温度,工作人员可以根据测量的工作温度调整冷却液的供给力度,获得更高的冷却效率。在本实施例中,温度传感器为ntc温度传感器或ptc温度传感器。采用这两种温度传感器的好处是体积小,能够测量其他温度计无法测量的空隙;使用方便,电阻值可在0.1~100kω间任意选择;易加工成复杂的形状,可大批量生产,稳定性好、过载能力强,适用于转换接头这种要求体积小,性能稳定的产品中。
75.温度传感器可以设置在导电端子1的内部或外部,优选设置在导电端子1内流动的末端,此时的冷却液经过之前的冷却,温度已经有所升高,冷却效果已经降低,端子此处的温度更容易超过预警值,因此在此处设置温度传感器效果最好。
76.本发明还公开了一种直流充电装置冷却系统,包括如上所述的端子冷却结构、输入泵、冷却介质和冷却装置;
77.两个所述导电端子1分别为正极导电端子和负极导电端子;所述正极导电端子和所述负极导电端子内中的一个所述冷却管2为输入管,另一个为输出管,所述输入管与所述输入泵连接,所述冷却装置一端与所述输出管连接,另一端与所述输入泵连接,所述输入泵用于将所述冷却介质输入输入管。以输入管设置在正极导电端子内且输出管设置在负极导
电端子为例,输入泵驱动冷却介质进入输入管,冷却介质从内端口21进入正极导电端子的封闭腔体12,再从连接孔13经水管接头4及连接管3进入负极导电端子的封闭腔体12,经负极导电端子内的输出管流出进入冷却装置,冷却装置将冷却介质进行冷却,输入泵再将冷却后的冷却介质输入输入管,完成整个冷却循环。冷却装置为散热片或其他冷却设备。
78.在一些实施例中,所述冷却介质为冷却气体、冷却液体或冷却固体。冷却气体可以为制冷后的空气吹入冷却管2再进入密封腔体12内进行冷却。冷却液体可以为绝缘水、乙二醇、蓖麻油、椰子油、玉米油、棉籽油、亚麻子油、橄榄油、棕榈油、花生油、葡萄籽油、菜籽油、红花油、向日葵油,大豆油,各种植物油的高油酸变体、癸烯-4-酸、癸烯酸、月桂烯酸、天台乌药酸、十四碳烯酸、抹香鲸酸、粗租酸、棕榈油酸、芹岩酸、油酸、十八碳烯酸、鳕烯酸、巨头鲸鱼酸、鲸蜡烯酸、芥酸、和神经酸、甘油、变压器油、车轴油、内燃机油或压缩机油的一种或几种;也可在冷却液中加入添加剂,所述添加剂选自抗氧化剂、倾点抑制剂、缓蚀剂、抗菌剂、粘度改性剂中一种或几种。冷却油具有灵敏的热平衡能力,超强的热传导能力,超宽的工作温度区间,杜绝沸腾开锅,冷却系统微压力,低温环境不用添加防冻剂,避免了气蚀、水垢、电解等腐蚀伤害等优点。冷却固体可以为干冰等。以干冰为例,干冰设置在密封结构12内,在导电端子1的外部施加制冷设备,制冷设备提供冷源来维持干冰的固体状态,用以对导电端子1进行冷却。
79.在优选的实施方式中,所述冷却介质的冷却速率大于等于0.5℃/min。冷却介质的冷却速率除了和冷却介质本身的材质有关,也和冷却介质的供给速度有关。发明人为了验证冷却介质的冷却速率对导电端子1温升的影响,选用10根相同截面积、相同材质、相同长度的导电端子1,并通相同的电流,采用不同冷却速率的冷却介质,对导电端子1进行冷却,并读取各个导电端子1的温升值,记录在表6中。
80.实验方法是在封闭的环境中,将采用不同冷却速率的冷却介质的导电端子1导通相同的电流,记录通电前的温度和通电后温度稳定时的温度,并作差取绝对值。在本实施例中,温升小于50k为合格值。
81.表6:不同冷却速率的冷却介质对导电端子1温升的影响
[0082][0083]
从上表6中可以看出,当冷却介质的冷却速率小于0.5℃/min时,导电端子1的温升值不合格,冷却介质的冷却速率越大,导电端子1的温升值越小。因此,发明人将冷却介质的冷却速率设定为大于或等于0.5℃/min。
[0084]
以上所述,仅为本发明的具体实施例,不能以其限定发明实施的范围,所以其等同组件的置换,或依本发明专利保护范围所作的等同变化与修饰,都应仍属于本专利涵盖的范畴。另外,本发明中的技术特征与技术特征之间、技术特征与技术方案、技术方案与技术方案之间均可以自由组合使用。