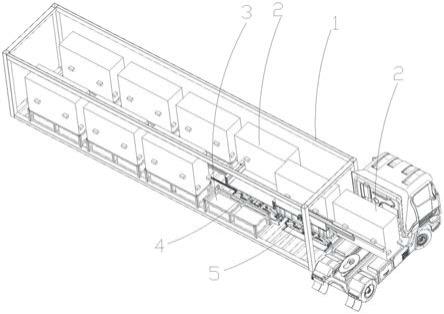
1.本发明公开了一种换电池设备,具体为一种新型卡车换电装置。
背景技术:2.电动汽车属于新能源汽车,在资源紧缺以及环境污染严重的当今社会,各国均重视新能源汽车的发展,而电动汽车技术属于较早提出的技术。但受制于当时社会的科学技术水平,电动汽车的使用成本较高,无法普及,经过了多年的发展。随着技术的成熟,电动汽车的多个难题被克服,电动汽车将逐渐替代原来的燃油动力汽车,成为发展的重点。而电动汽车的核心部件为动力电池,动力电池的容量是限制电动汽车发展的重要因素,由于充电速度慢,充电效果不佳等原因一直抑制动力电池技术的发展。基于充电技术的缺陷,提出了电动汽车的换电技术,采用直接更换电池的方式进行电力的补充,以实现快速更换达到长时间续航的能力。电动卡车属于电动汽车的一种,目前各主流商家如国外的特斯拉、国内一汽解放、重汽、陕汽等均在发展电动卡车车型。由于卡车载重大,行驶里程长,导致耗能比乘用车更大,而充电技术的缺陷导致目前电动卡车的普及性要远低于乘用车。换电技术是解决这一问题的一个途径之一,对一些通常运行在局部区域的车辆如矿卡、城市内运输卡车、物流园区卡车等来说尤为如此。
3.目前卡车的换电蓬勃发展,目前已有不少专利技术授权或申请中,但这些技术都采用顶部吊装并且在每个工位上设置移动装置(如cn 110862008a),存在的主要问题有:
4.(1)顶部吊装受力通过立柱和横梁传递到地面,造成结构复杂,设备体积庞大,尤其占用高度空间,设备难以整体运输(容易超过高速公路桥涵的限高,通常4.5m)。
5.(2)由于卡车停止的位置精度比较低,需要换电装置进行自动找正并进行姿态调整,这就需要具备多自由度的调整,顶部吊装装置会变得非常复杂并占用更多空间。目前多通过链条、钢丝绳起升系统具备的柔性进行误差补偿,这会加大对位失误,降低了可靠性。
6.(3)顶部吊装不能满足部分卡车的换电需求,部分卡车如矿卡顶部部分结构会遮挡住电池包,从而无法从顶部吊装。
7.(4)每个工位需要设置移动装置,增加了系统复杂度和成本。
8.为了适应部分卡车无法从顶部吊装,目前已有新的技术出现,比如:从侧面抓取,然后整体旋转后移动将电池包放置到工位;再如采用堆垛机(cn111717062a)抓取电池包然后配合顶部吊装放置到工位。这些装置存在的普遍缺点是:机构复杂、占用空间大、对位可靠性低。
9.本发明专利,旨在发明一种能够实现空间紧凑、便于整体公路运输(包括房屋装置)、重量轻、可靠性高的新型换电装置。
技术实现要素:10.本发明的目的是为了提供一种电动卡车换电装置及其换电方法,以解决现有技术的上述技术问题。
11.本发明的目的是通过以下技术方案来实现的:
12.一种电动卡车换电装置,在虚拟的三维坐标系下;包括电源、控制电路、各传感器和电池包;还包括:
13.一容纳各装置并可放置在平板车上的容置空间,容置空间包含一安装各设备的安装底座;若干设置于安装底座上用于放置电池包的充电机座;所述的容置空间沿x轴方向上的至少一侧设置有上下电池包的工作口;所述的充电机座整体排列有两排,分列于容置空间沿x轴向的两侧;两排充电机座之间设置有沿x轴方向上的水平轨道;水平轨道上安装有沿轨道行走的第一机器人;第一机器人与工作口之间设置有第二机器人;
14.所述的第一机器人具有一对可在y轴方向上伸展的第一货叉;和在z轴方向上移动的第一升降机构;所述的第一货叉之间的宽度大于电池包的长度;
15.所述的第二机器人安装于一支撑板上,支撑板下方设置有若干沿y轴方向设置的y轴向行走导向滑块,在支撑板与安装底座之间设置有y轴向行走机构,y轴向行走机构使支撑板沿y轴方向上行走;支撑板与第二机器人之间通过z轴旋转机构连接;
16.所述第二机器人还具有一对可伸缩的第二货叉和在z轴方向上移动的第二升降机构;第二货叉之间的宽度大于电池包的宽度;且第二货叉所对应的第二支撑耳的高度,高于第一货叉所对应的第一支撑耳的高度;
17.所述的第一机器人、第二机器人、传感器均与控制电路电性连接。
18.所述的z轴旋转机构包括一回转支撑和一使回转支撑绕z轴旋转的回转驱动组件;所述的回转支撑为回转轴承,回转驱动组件为液压顶杆或电动顶杆。所述的绕z轴旋转机构的旋转角度为
±
5度之间。
19.所述第一升降机构和第二升降机构包括若干组连杆机构、驱动组件和导向滑道,所述的驱动组件为电动丝杆或液压气缸。
20.更进一步地,所述的连杆机构为剪刀伸缩臂,剪刀伸缩臂中至少包括一第一叉臂,第一叉臂的一端为固定端,与第一货叉的底部转轴连接;另一端为活动端,与导向滑道匹配连接并在叉臂导向滑道中滑动;所述的驱动组件驱动活动端沿叉臂导向滑道方向滑行,从而升降支撑板。
21.第一叉臂的中间设置支撑轴,支撑轴上转动连接第二叉臂的一端,所述的第二叉臂的另一端与支撑板转动连接。
22.作为一种实施方式,所述的电动丝杆包括减速电机和丝杆装置,所述的丝杆连接一对丝杆螺母,螺母与第一叉臂的活动端连接,丝杆转动时第一叉臂的活动端沿叉臂导向滑道移动,从而实现升降机上面板的上下运动。
23.所述的第一机器人与水平导轨之间通过若干导向滚轮配合,水平导轨限制导向滚轮在y轴方向上移动。第一机器人通过x轴向行走机构驱动第一机器人沿水平导轨行走;x轴向行走机构包括x轴向行走驱动、传动组件;所述的x轴向行走驱动包括驱动电机和减速机;所述的传动组件选自齿轮和齿条传动组件、链轮和链条传动组件、滑轮和钢丝绳传动组件。
24.更进一步地,所述传动组件为齿轮和齿条时,所述齿条水平固定,减速电机的输出轴上安装有与齿条相匹配的齿轮,通过减速电机的正反旋转,控制第一机器人的x轴上的移动。
25.所述的第一货叉和第二货叉包括有下叉组件、中叉组件和上叉组件,三者之间通
过货叉减速电机、齿轮组和链轮驱动依次打开。
26.更进一步地,所述的上叉组件的上侧设置有导向定位柱,与所述电池包上对应的支撑耳下侧设置的定位孔匹配,共同限制电池包在货叉上的位置,以便于将电池包从第二机器人运转至第一机器人,进而准确放置于充电机座上。优选的是:所述上叉组件上设有两个导向定位柱,导向定位柱的头部为锥形,在
±
20mm的误差范围内可以自动将电池包导入孔内并且定位。为了补偿孔或轴之间的误差,防止过定位,所述定位孔其中一个为圆形定位孔,另一个为长腰形定位孔。
27.所述的传感器为激光距离传感器,通过传感器测量电池包的相对位置,通过控制电路(plc)计算偏离角度和距离,然后控制电路控制x轴向、y轴向和z轴向和z轴旋转向的调整,准确将电池包叉入第二货叉的指定位置。然后第二机器人复位;第二机器人在y轴向上抬升,直至电池包的底部高于第一货叉上沿高度后,第二货叉在x轴向上反向伸出。直至电池包到达第一货叉的上方指定位置后放下。电池包由第一机器人承载,由于第一支撑耳的高度低于第二支撑耳的高度,因此,当第一货叉叉取第一支撑耳时,第二支撑耳的高度高于停留在机座上电池包的第二支撑耳。接着,第一机器人在x方向上行走至空闲充电机座处,第一机器人在z轴向上降低,直至电池包停放至充电机座上后收回货叉。
28.所述的容置空间优选为长方体箱体。
29.本发明所述的电动卡车换电装置的x轴向最大工作距离为:15m;y轴向最大工作距离为3.2m:z轴向最大工作距离为:3.5m;因此,可以通过平板挂车实现快速移动,快速建立电池更换站。尤其适用于矿山开采工地、港口码头、物流园区、中短途相对定点运输的重型卡车使用。
30.为了描述清楚,所建立的虚拟三维坐标系,可设沿换容置空间的长边方向为x轴,以水平面上垂直x轴的方向为y轴;以垂直于xy平面的升降方向为z轴。
31.本发明技术方案具有以下有益效果:
32.(1)通过两套机器人的配合,进行对位、移动、取放等动作功能,机器人直接将电动卡车上的电池包拆卸至充电机座上,或从充电机座上移动至电动汽车上,实现无人值守换电;
33.(2)充分利用了空间,实现了占地空间小、重量轻、对位可靠的有益效果,可实现整体公路运输、活动建站;具有良好的经济性。
附图说明
34.图1为本发明的整体结构示意图;
35.图2为图1的俯视结构示意图;
36.图3为本发明的第二机器人的结构示意图;
37.图4为第二机器人的y轴方向平移机构示意图;
38.图5为第二机器人的z方向旋转机构示意图;
39.图6为第二货叉伸出状态的结构示意图;
40.图7为第二货叉的结构示意图;
41.图8为电池包结构示意图;
42.图9为本发明第一机器人的结构示意图;
43.图10为第一机器人的升降机构示意图;
44.图11为图9的a部放大图。
45.图中,1、容置空间;2、电池包;21、第一支撑耳;22、第二支撑耳;23、长腰形定位孔、24、圆形定位孔;3、充电机座;4、第一机器人;41、x轴向行走机构;411、x轴向行走驱动;412、齿轮;413-齿条;414、导向滚轮;43、第一货叉;44、第一升降机构;5、第二机器人;51、y轴向行走机构;511、y轴向行走驱动512、y轴向行走导向滑块;52、z轴旋转机构;53、第二货叉;531、下叉组件;532、中叉组件;533、上叉组件;534、导向定位柱;535、货叉减速电机、54、第二升降机构;541、第一叉臂;542、第二叉臂;543、叉臂导向滑道;55、回转驱动组件。
具体实施方式
46.下面结合附图与具体实施方式进一步阐述本发明的技术特点。
47.实施例以容置空间为长方体箱体为例。为了描述清楚,所建立的虚拟三维坐标系,可设沿换容置空间的长边方向为x轴,以水平面上垂直x轴的方向为y轴;以垂直于xy平面的升降方向为z轴。
48.如图1-11所示,一种电动卡车换电装置,在虚拟的三维坐标系下;包括电源、控制电路、各传感器和电池包;还包括:一容纳各装置并可放置在平板车上的容置空间,容置空间包含一安装各设备的安装底座;若干设置于安装底座上用于放置电池包的充电机座;所述的容置空间沿x轴方向上的至少一侧设置有上下电池包的工作口;所述的充电机座整体排列有两排,分列于容置空间沿x轴向的两侧;两排充电机座之间设置有沿x轴方向上的水平轨道;水平轨道上安装有沿轨道行走的第一机器人;第一机器人与工作口之间设置有第二机器人;所述的第一机器人具有一对可在y轴方向上伸展的第一货叉;和在z轴方向上移动的第一升降机构;所述的第一货叉之间的宽度大于电池包的长度;所述的第二机器人安装于一支撑板上,支撑板下方设置有若干沿y轴方向设置的y轴向行走导向滑块,在支撑板与安装底座之间设置有y轴向行走机构,y轴向行走机构使支撑板沿y轴方向上行走;支撑板与第二机器人之间通过z轴旋转机构连接;所述第二机器人还具有一对可伸缩的第二货叉和在z轴方向上移动的第二升降机构;第二货叉之间的宽度大于电池包的宽度;且第二货叉所对应的第二支撑耳的高度,高于第一货叉所对应的第一支撑耳的高度;所述的第一机器人、第二机器人、传感器均与控制电路电性连接。
49.如图5所示,所述的z轴旋转机构包括一回转支撑和一使回转支撑绕z轴旋转的回转驱动组件;所述的回转支撑为回转轴承,回转驱动组件为液压顶杆或电动顶杆。所述的绕z轴旋转机构的旋转角度为
±
5度之间。
50.如图3所示,所述第一升降机构和第二升降机构包括若干组连杆机构、驱动组件和导向滑道,所述的驱动组件为电动丝杆或液压气缸。
51.如图9和图10所示,所述的连杆机构为剪刀伸缩臂,剪刀伸缩臂中至少包括一第一叉臂,第一叉臂的一端为固定端,与第一货叉的底部转轴连接;另一端为活动端,与导向滑道匹配连接并在叉臂导向滑道中滑动;所述的驱动组件驱动活动端沿叉臂导向滑道方向滑行,从而升降支撑板。
52.为了增加稳定性和减少驱动力,可自第一叉臂的中间设置支撑轴,支撑轴上转动连接第二叉臂的一端,所述的第二叉臂的另一端与支撑板转动连接。
53.作为一种实施方式,所述的电动丝杆包括减速电机和丝杆装置,所述的丝杆连接一对丝杆螺母,螺母与第一叉臂的活动端连接,丝杆转动时第一叉臂的活动端沿叉臂导向滑道移动,从而实现升降机上面板的上下运动。
54.如图11所示,所述的第一机器人与水平导轨之间通过若干导向滚轮配合,水平导轨限制导向滚轮在y轴方向上移动。第一机器人通过x轴向行走机构驱动第一机器人沿水平导轨行走;x轴向行走机构包括x轴向行走驱动、传动组件;所述的x轴向行走驱动包括驱动电机和减速机;所述的传动组件选自齿轮和齿条传动组件、链轮和链条传动组件、滑轮和钢丝绳传动组件。
55.更进一步地,所述传动组件为齿轮和齿条时,所述齿条水平固定,减速电机的输出轴上安装有与齿条相匹配的齿轮,通过减速电机的正反旋转,控制第一机器人的x轴上的移动。
56.如图7所示,所述的第二货叉包括有下叉组件、中叉组件和上叉组件,三者之间通过货叉减速电机、齿轮组和链轮驱动依次打开。所述的上叉组件的上侧设置有导向定位柱,与所述电池包上对应的支撑耳下侧设置的定位孔匹配,共同限制电池包在货叉上的位置,以便于将电池包从第二机器人运转至第一机器人,进而准确放置于充电机座上。优选的是:所述上叉组件上设有两个导向定位柱,导向定位柱的头部为锥形,在
±
20mm的误差范围内可以自动将电池包导入孔内并且定位。为了补偿孔或轴之间的误差,防止过定位,所述定位孔其中一个为圆形定位孔,另一个为长腰形定位孔。本发明中的第一货叉和第二货叉具有相同的构件和传动结构。
57.所述的传感器为激光距离传感器,通过传感器测量电池包的相对位置,通过控制电路(plc)计算偏离角度和距离,然后控制电路控制x轴向、y轴向和z轴向和z轴旋转向的调整,准确将电池包叉入第二货叉的指定位置。然后第二机器人复位;第二机器人在y轴向上抬升,直至电池包的底部高于第一货叉上沿高度后,第二货叉在x轴向上反向伸出。直至电池包到达第一货叉的上方指定位置后放下。电池包由第一机器人承载,由于第一支撑耳的高度低于第二支撑耳的高度,因此,当第一货叉叉取第一支撑耳时,第二支撑耳的高度高于停留在机座上电池包的第二支撑耳。接着,第一机器人在x方向上行走至空闲充电机座处,第一机器人在z轴向上降低,直至电池包停放至充电机座上后收回货叉。
58.本发明所述的电动卡车换电装置的x轴向最大工作距离为:15m;y轴向最大工作距离为3.2m:z轴向最大工作距离为:0.6m;因此,可以通过平板挂车实现快速移动,快速建立电池更换站。尤其适用于矿山开采工地、港口码头、物流园区、中短途相对定点运输的重型卡车使用。
59.取放电池包时,卡车按要求停止到指定位置;按“启动”按钮;卡车顶部z方向测距激光传感器测量电池包高度方向尺寸;第二机器人升降机构根据测得的电池包高度,升降机构调整高度,使得机器人上的光电穿管器高度与电池包上的反射板中心高度一致(此时机器人货叉高度方向已低于电池包,高度方向具备伸出条件);第二机器人沿y方向左右移动,当光电传感器检测到电池包上的反光板后停止,此时机器人y方向已对准电池包;第二机器人上的两侧两个激光测距传感器测量与电池包的距离,由此得到电池包与理论位置的偏转角度。
60.根据测得的偏角,第二机器人z轴旋转机构旋转同时y方向平移机构微动,直到两
个测距传感器测得的距离相等并且光电传感器对准电池包反射板。此时第二机器人与电池包在z方向、y方向对准,x方向与电池包平行,并已经测得与电池包x方向的距离。
61.第二机器人的第二货叉向卡车方向伸出,到达所需值(根据以上测距传感器测得的距离确定)停止;第二机器人的第二货叉上升,到达设定值停止;第二机器人的第二货叉收回到中位位置停止,此时需存储第二机器人y方向、z方向、z轴转动方向位置状态。
62.第二机器人的z轴旋转机构与y轴向行走机构同时动作,回归原点位置,第二机器人的第二货叉向第一货叉伸出,使得电池包到达第一货叉正上方,第二机器人的第二升降机构下降,直到电池包落到第一货叉上,并且第二货叉完全脱离电池包,第二机器人的第二货叉缩回到中位。
63.第一机器人根据管理系统指令确定目标电池包工位,沿x方向行驶到相应位置;第一机器人的第一货叉向指定工位伸出,到达设定位置停下;第一机器人的第一货叉下降,直到货叉完全脱离电池包;第一机器人的第一货叉缩回到中位。
64.装载电池包至电动汽车上时,第一机器人根据管理系统的指令确定目标充电池包工位(已经充满电),然后沿着x方向移动到相应位置;第一机器人的第一货叉向指定工位伸缩,到达电池包下方;
65.第一机器人的第一货叉上升,上升到设定高度时停止;第一机器人的第一货叉缩回到中位;第一机器人带着电池包,向第二机器人方向移动,直到终点位置;第二机器人的第二货叉向第一货叉方向伸出。
66.第二机器人的升降机构上升,直到电池包完全脱离第一货叉;第二机器人的第二货叉缩回到中位;第二机器人y方向平移、z方向升降、z轴方向转动同时动作,恢复存储的记忆姿态;第二货叉向卡车方向伸出。
67.第二机器人的升降机构下降直到电池包就位,第二货叉完全脱离电池包;第二货叉回到中位位置;第二机器人y方向平移、z轴旋转、z方向升降同时动作归零位。