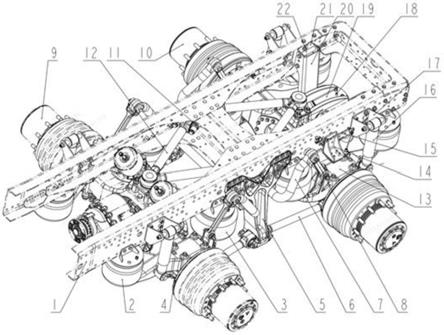
1.本实用新型涉及一种高离地底盘的后提升空气悬架,属于汽车底盘技术领域。
背景技术:2.目前国内重型车辆由于工作环境恶劣,尤其是在油田等路况较差的地区,对整车的离地间隙就有了一定的要求。因此在保证部件强度、及整车性能的同时,高通过性已经成为车辆市场需求。此外,石油资源日趋紧张,油价和天然气不断上涨,对汽车工业和汽车运输业来说,节油降成本成为关键。汽车自身质量的大小是影响燃油消耗的重要因素之一,所以将各系统进行优化布置,并进行轻量化设计也更加重要。随着法规的日趋严格,按轴收费也提上日程,为进一步降低油耗,根据市场定位再次细分到用户的空满载运输需求,且保证动力的正常输出,空车时,单轴驱动,载货时,双轴驱动,发挥燃油经济性,降低成本的同时,减少排放污染。
技术实现要素:3.本实用新型所要解决的技术问题是针对现有技术存在的缺陷,提供一种高离地底盘的后提升空气悬架。
4.为解决这一技术问题,本实用新型提供了一种高离地底盘的后提升空气悬架,包括车架、减振器支架、阻尼器、ecas阀、限位支架、上置均衡梁、吊杆、稳定杆、直推力杆、大支架、大气囊、小气囊、下推支架、中桥、后桥、上推支架、v推、套管、固定支架、下提升弯梁、气囊提升支架和提升气囊,所述上置均衡梁通过定位孔分别与中桥和后桥的上部连接,下推支架通过定位孔分别与中桥、后桥的下部连接;限位支架和减振器支架分别连接在车架外侧,阻尼器上部与减振器支架连接、下部与上置均衡梁连接;所述稳定杆上配有衬套、与大支架的配镗孔连接,所述大支架和上推支架设有共用孔位、分别设置在车架的外侧和内侧;所述吊杆与稳定杆通过台阶轴连接,吊杆与上置均衡梁的吊耳连接;所述v推双球头处与上推支架连接,单球头处通过支架与中桥、后桥连接;所述直推力杆通过一端球销与大支架下端孔位连接,另一端球销与下推支架连接;所述车架气囊支架连接在车架外侧,大气囊和小气囊上端与车架气囊支架连接,下端与上置均衡梁前后悬臂的端面连接;所述气囊提升支架为上推支架与后桥连接件,固定支架与车架连接,下提升弯梁、套管与固定支架连接;所述提升气囊上部与气囊提升支架连接、下部与下提升弯梁的中部连接。
5.所述上置均衡梁前后两端悬臂上设有孔位一和孔位二,侧面设有侧面孔位,其上表面有吊耳;所述孔位一和孔位二所在平面为机加工面;所述孔位二处上表面机加工小凸台、表面设有吊耳;所述上置均衡梁通过孔位二使用螺栓与ecas阀的连杆支架固定,ecas阀的上端与车架通过螺栓连接;所述大气囊和小气囊的底部端面与孔位一和孔位二的机加工面接触、并通过螺栓连接;所述阻尼器下端部通过台阶轴螺栓与上置均衡梁的侧面孔位连接,中间加以大垫片;所述吊杆的端部插入上置均衡梁的吊耳中间、通过台阶轴螺栓固定;所述上置均衡梁下部的三个表面为机加工面,两侧面上设有定位槽用以与中桥和后桥的凸
台预定位及限位;所述上置均衡梁以车架中心面左右对称、以后桥中心面前后对称。
6.所述中桥和后桥的桥壳截面为倒圆角矩形,为保证传动轴3
°
倾角,加工凸台均与矩形截面有3
°
夹角;所述中桥和后桥的下部设有定位销孔一用于压装定位销,该定位销与下推支架上的定位销孔二连接,直推力杆的球销孔位与下推支架上的下支腿孔螺栓连接,整体保证四连杆机构,保证高离地间隙的同时,保证传动轴倾角的运动在合理范围之内;长螺栓自下往上穿过下推支架的机加工面的孔位三、中桥及后桥的机加工孔位、上置均衡梁四个机加工大凸台孔位,在凸台通过螺母打紧。
7.所述的大气囊、小气囊均为无内置限位块的气囊,以保证上下跳动行程,基准高度250
±
20mm,金属活塞,气囊行程为135mm
‑
550mm,车桥允许上下跳动行程为
±
80mm;两个气囊的顶部焊接螺柱与车架的气囊支架通过螺母打紧。
8.所述大支架包括固定支撑和轴承盖,所述固定支撑和轴承盖均为铸件、通过螺栓固定装配,并压装橡胶轴承,使稳定杆的平直段通过两侧大支架,稳定杆两侧的端部压装衬套,与吊杆一段的叉形结构通过台阶轴螺栓连接,吊杆另一端的机加工圆孔压装橡胶衬套,与上置均衡梁上表面吊耳通过台阶轴螺栓连接,前后两套稳定杆对应中桥和后桥对称;所述固定支撑叉形支腿下部机加工通孔,支腿前后侧连接前后直推的球销,通过长螺栓连接。
9.所述减振器支架本体为折弯件,其上设有焊接圆筒;所述阻尼器上部两侧有大垫圈,与减振器上部一起夹在两个圆筒中间,通过台阶轴螺栓连接,其下部也加装两个大垫圈,通过台阶轴螺栓与上置均衡梁的侧面孔位连接;所述阻尼器的行程在300mm
‑
700mm之间。
10.所述限位支架包括限位块支架本体和缓冲块,所述限位块支架本体为折弯拼焊件、其上有大圆弧,缓冲块与限位块支架本体通过螺栓连接;缓冲块与上置均衡梁的上表面设有50mm
‑
100mm的间距,确保在大气囊和小气囊内部的活塞行程极限之前将后桥的上跳限制住。
11.所述上推支架包括车架安装面和上推安装面,前后两组上推安装面通过其上孔位与v推通过螺栓连接。
12.所述气囊提升支架为v推单球头端连接支架,与提升支架集成化设计,设有气囊提升支架
‑
上推孔位、气囊提升支架下部孔位、气囊上部固定孔位和孔位四,所述气囊提升支架
‑
上推孔位与v推的单球头端通过自身的球销螺栓连接,气囊提升支架下部孔位与后桥螺栓连接;所述提升气囊上部的螺柱穿过气囊上部固定孔位,其下部端面与下提升弯梁螺栓连接;下提升弯梁为一体冲压模具件;所述固定支架为折弯件、与车架螺栓连接、中间加以套管辅助支撑,保证提升气囊的垂直;在整车高离地间隙、高通过性的同时,控制大气囊、小气囊提升60mm
‑
80mm,以此为基准,后桥提升120mm
‑
140mm。
13.有益效果:本实用新型在保证后悬架稳定性及传动性能的同时,能保证底盘布置的紧凑性,使空间利用更为合理,保证车辆横向稳定性、悬架系统的轻量化的同时,极大的保证了车辆通过性,并且可以根据路况及承载需求,调整驱动形式,路况适应性更为良好,燃油经济性更高。
附图说明
14.图1为本实用新型的装有车架的结构示意图;
15.图2为本实用新型的结构示意图;
16.图3a为本实用新型上置均衡梁的结构示意图一;
17.图3b为本实用新型上置均衡梁的结构示意图二;
18.图4所示为本发明所述的下推支架结构示意图;
19.图5为本实用新型大支架的结构示意图;;
20.图6为本实用新型稳定杆总成的结构示意图;
21.图7为本实用新型限位支架的结构示意图;
22.图8为本实用新型气囊提升支架结构示意图;
23.图9a为本实用新型上推支架的结构示意图一;
24.图9b为本实用新型上推支架的结构示意图二;
25.图10a为本实用新型桥接口的结构示意图一;
26.图10b为本实用新型桥接口的结构示意图二;
27.图11为本实用新型驱动桥后提升总成结构示意图;
28.图12为本实用新型离地间隙实测示意图。
29.图中:1车架、2小气囊、3大气囊、4下推支架、5大支架、6直推力杆、7稳定杆、8吊杆、9中桥、10后桥、11上推支架、12v推、13上置均衡梁、14限位支架、15ecas阀、16阻尼器、17减振器支架、18提升气囊、19气囊提升支架、20下提升弯梁、21固定支架、22套管、23凸台、24机加工孔位、25定位销孔一、41定位销孔二、42孔位三、43下支腿孔、51固定支撑、52轴承盖、53橡胶轴承、111车架安装面、112上推安装面、131孔位一、132孔位二、134大凸台孔位、135吊耳、136侧面孔位、137定位槽、141限位块支架本体、142缓冲块、191气囊提升支架
‑
上推孔位、192气囊提升支架下部孔位、193气囊上部固定孔位、194孔位四。
具体实施方式
30.下面结合附图及实施例对本实用新型做具体描述。
31.如图1
‑
图12所示,本实用新型提供了一种高离地底盘的后提升空气悬架,包括车架1、减振器支架17、阻尼器16、ecas 15、限位支架14、上置均衡梁13、吊杆8、稳定杆7、直推力杆6、大支架5、大气囊3、小气囊2、下推支架4、中桥9、后桥10、上推支架11、v推12、套管22、固定支架21、下提升弯梁20、气囊提升支架19和提升气囊18,所述上置均衡梁13通过定位孔分别与中桥9和后桥10的上部连接,下推支架4通过定位孔分别与中桥9、后桥10的下部连接;所述限位支架14和减振器支架17分别连接在车架1外侧,阻尼器16上部与减振器支架17连接、下部与上置均衡梁13连接;所述稳定杆7上配有衬套、与大支架5的配镗孔连接,所述大支架5和上推支架11设有共用孔位、分别设置在车架1的外侧和内侧;所述吊杆8与稳定杆7通过台阶轴连接,吊杆8与上置均衡梁13的吊耳连接;所述v推12双球头处与上推支架11连接,单球头处通过支架与中桥9、后桥10连接;所述直推力杆6通过一端球销与大支架5下端孔位连接,另一端球销与下推支架4连接;所述车架气囊支架连接在车架1外侧,大气囊3和小气囊2上端与车架气囊支架连接,下端与上置均衡梁13前后悬臂的端面连接;所述气囊提升支架19为上推支架11与后桥10连接件,固定支架21与车架1连接,下提升弯梁20、套管22与固定支架21连接;所述提升气囊18上部与气囊提升支架19连接、下部与下提升弯梁20的中部连接。
32.如图2、图3、图4、图6、图10所示,所述上置均衡梁13前后两端悬臂上设有孔位一131和孔位二132,侧面设有侧面孔位136,其上表面有吊耳135;所述孔位一131和孔位二132所在平面为机加工面;所述孔位二132处上表面机加工小凸台、表面设有吊耳135;所述上置均衡梁13通过孔位二132使用螺栓与ecas阀15的连杆支架固定,ecas阀15的上端与车架1通过螺栓连接;所述大气囊3和小气囊2的底部端面与孔位一131和孔位二132的机加工面接触、并通过螺栓连接;所述阻尼器16下端部通过台阶轴螺栓与上置均衡梁13的侧面孔位136连接,中间加以大垫片,防止磨碰;所述吊杆8的端部插入上置均衡梁13的吊耳135中间、通过台阶轴螺栓固定;所述上置均衡梁13下部的三个表面为机加工面,两侧面上设有定位槽137用以与中桥9和后桥10的凸台23预定位及限位,限制上置均横梁在桥上面的前后及左右位移;所述上置均衡梁13以车架中心面左右对称、以后桥中心面前后对称。
33.所述中桥9和后桥10的桥壳截面为倒圆角矩形,为保证传动轴3
°
倾角,加工凸台均与矩形截面有3
°
夹角,以确保上置均衡梁13为对称件;所述中桥9和后桥10的下部设有定位销孔一25用于压装定位销,该定位销与下推支架4上的定位销孔二41连接,直推力杆6的球销孔位与下推支架4上的下支腿孔43螺栓连接;长螺栓自下往上穿过下推支架4的机加工面的孔位三42、中桥9及后桥10的机加工孔位24、上置均衡梁13四个机加工大凸台孔位134,在凸台通过螺母打紧。
34.所述的大气囊3、小气囊2均为无内置限位块的气囊,以保证上下跳动行程,基准高度250
±
20mm,金属活塞,气囊行程为135mm
‑
550mm,车桥允许上下跳动行程为
±
80mm;两个气囊的顶部焊接螺柱与车架1的气囊支架通过螺母打紧,打紧的时候需要制作角钢工装,以确保车桥两侧均横梁打紧之后的齐平、对称。
35.如图3、图5、图6所示,所述大支架5包括固定支撑51和轴承盖52,所述固定支撑51和轴承盖52均为铸件、通过螺栓固定装配,并制作工装、配镗(配镗孔位前后对称),压装橡胶轴承53,使稳定杆7的平直段通过两侧大支架5,稳定杆7两侧的端部压装衬套,与吊杆8一段的叉形结构通过台阶轴螺栓连接,吊杆8另一端的机加工圆孔压装橡胶衬套,与上置均衡梁13上表面吊耳135通过台阶轴螺栓连接,前后两套稳定杆7对应中桥9和后桥10对称;所述固定支撑51叉形支腿下部机加工通孔,支腿前后侧连接前后直推的球销,通过长螺栓连接。
36.如图1和图2所示,所述减振器支架17本体为折弯件,其上设有焊接圆筒;所述阻尼器16上部两侧有大垫圈,与减振器上部一起夹在两个圆筒中间,通过台阶轴螺栓连接,其下部也加装两个大垫圈,通过台阶轴螺栓与上置均衡梁13的侧面孔位136连接;所述阻尼器16的行程在300mm
‑
700mm之间。
37.如图1和图7所示,所述限位支架14包括限位块支架本体141和缓冲块142,所述限位块支架本体141为折弯拼焊件、其上有大圆弧,以确保中桥9、后桥10上下以及扭曲路况时,避免限位支架14与ecas阀15的连杆运动干涉,缓冲块142与限位块支架本体141通过螺栓连接;缓冲块142与上置均衡梁13的上表面设有50mm
‑
100mm的间距,确保在大气囊3和小气囊2内部的活塞行程极限之前将后桥的上跳限制住,确保气囊的使用寿命及整体后悬架系统的运作安全;缓冲块142可根据需要进行更换,高度可根据需求调整压缩程度,以确保缓冲效果。
38.所述上推支架11包括车架安装面111和上推安装面112,前后两组上推安装面112通过其上孔位与v推12通过螺栓连接。
39.如图1和图8所示,所述气囊提升支架19为v推单球头端连接支架,与提升支架集成化设计,设有气囊提升支架
‑
上推孔位191、气囊提升支架下部孔位192、气囊上部固定孔位193和孔位四194,所述气囊提升支架
‑
上推孔位191与v推12的单球头端通过自身的球销螺栓连接,气囊提升支架下部孔位192与后桥10螺栓连接;所述提升气囊18上部的螺柱穿过气囊上部固定孔位193,其下部端面与下提升弯梁20螺栓连接;下提升弯梁20为一体冲压模具件,薄壁板件通过几字形截面保证自身刚度强度,确保自身轻量化;所述固定支架21为折弯件、与车架1螺栓连接,为防止下提升弯梁20、固定支架21打紧时,出现过度的变形,中间加以套管22辅助支撑,保证提升气囊18的垂直,套管22的壁厚根据拧紧力矩大小而定,单侧两个,起到支撑作用;在整车高离地间隙、高通过性的同时,控制大气囊3、小气囊2提升60mm
‑
80mm,以此为基准,后桥提升120mm
‑
140mm。
40.工作中,可根据ecas调整两个悬架高度:双桥驱动时,低悬架高度,确保承载及降低重心;当需要单桥驱动时,车辆静止,8个承载气囊充气,提升悬架基准高度60mm,与此同时,提升气囊被压缩60mm,到达第二个基准高度,再次提升后驱动桥,根据需求,后驱动桥可提升120mm
‑
140mm。
41.所述的大气囊3、小气囊2均为无内置限位块的气囊,以保证上下跳动行程,基准高度250
±
20mm,金属活塞,气囊行程为135mm
‑
550mm,车桥允许上下跳动行程为
±
80mm;两个气囊的顶部焊接螺柱与车架1的气囊支架通过螺母打紧。
42.本实用新型保证底盘布置的紧凑性,使空间利用更为合理,保证车辆横向稳定性、悬架系统的轻量化的同时,极大的保证了车辆通过性,路况适应性更为良好。
43.本实用新型上述实施方案,只是举例说明,不是仅有的,所有在本实用新型范围内或等同本实用新型的范围内的改变均被本实用新型包围。