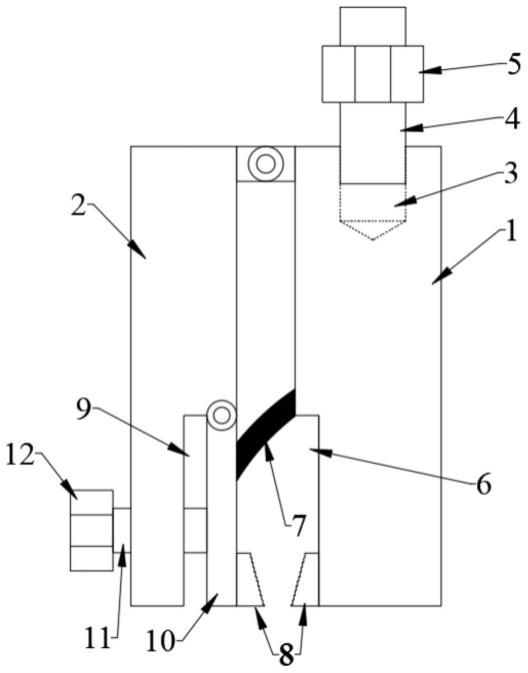
1.本发明属于电网设备技术领域,尤其涉及一种铁路接触网定位线夹装置。
背景技术:2.铁路作为一种主要的交通工具,其运输安全是首要考虑和解决的问题。接触网作为目前电气化铁路的重要组成部分,其运行安全直接影响着铁路供电和行车安全。由于铁道路线大多要穿越丘陵和高山等复杂地形,这样地形下的树木、杂草丛生,生长过于茂盛的树木就容易危及到铁路沿线接触网的安全。因此,及时检测和发现可能对接触网造成危害的树木是保证铁路运输安全的关键技术。传统的对铁路危树的检测方法大多数是通过检测车以及人的肉眼去进行观察识别,这种方法不仅耗费大量的人力和物力,而且存在效率低,不能及时发现等问题。研究对接触网危树进行自动检测的方法和装置,能够解决社会应用需求,推动铁路安全运输的发展。
技术实现要素:3.本发明提供了一种铁路接触网定位线夹装置,包括主夹具和副夹具,主夹具和副夹具的上部铰接,使得所述副夹具能够绕铰接位置转动,所述主夹具的上端设有螺纹孔,所述螺纹孔内设有连接螺柱,所述连接螺柱用于将主夹具固定在支架上,所述连接螺柱中部设有六角凸台部,所述六角凸台部用于拧动连接螺柱转动的受力部,六角凸台部的两侧为螺纹方向相反的外螺纹部,两个所述外螺纹部分别与所述主夹具和支架可拆卸地连接;所述主夹具的下部加工有第一接触线定位槽,所述第一接触线定位槽的上端设有橡胶挡片,所述橡胶挡片的一端固定在所述主夹具的侧壁上,另一端向下弯曲形成弧形;第一接触线定位槽的下端设有钩板,用于钩住接触线,防止接触线向下掉出;所述副夹具上与所述第一接触线定位槽相对的位置加工有第二接触线定位槽,所述第二接触线定位槽的上部铰接有活动夹板,第二接触线定位槽的侧壁加工有螺纹通孔,所述螺纹通孔内安装有调节螺柱,所述调节螺柱的一端穿过螺纹通孔设有调节帽,另一端抵靠在所述活动夹板上,所述活动夹板的底部也设有所述钩板;
4.其中,所述橡胶挡片的制备方法为:
5.1)配置三氯化铱、三氯化铈的水溶液,搅拌状态下向所述三氯化铱、三氯化铈的水溶液滴加氨水,直到不在产生沉淀为止,停止搅拌,固液分离,固相置于400~450℃温度范围内煅烧1h以上,获得复合氧化物;
6.2)配置n-苯基-1,4-苯二胺的乙醇溶液,将所述复合氧化物加入所述n-苯基-1,4-苯二胺的乙醇溶液中,搅拌溶液使得复合氧化物均匀分散,然后将溶液水浴恒温至65
±
5℃温度范围内,在搅拌状态下向溶液中加入甲基异丁基酮,加料完成后继续搅拌10h以上,搅拌完成后固液分离,固相烘干获得固相a;
7.3)将丁苯橡胶、炭黑、所述固相a、氧化锌粉末、硬脂酸、2-巯基苯并噻唑、二硫化四甲基秋兰姆、1,3-二苯基胍、硫磺混合均匀,在双辊开炼机上进行混炼,混炼10~15分钟,于
150℃测试硫化曲线,得到t
90
值,150℃条件下对混炼胶硫化压片,压片硫化时间为t
90
值,获得所述橡胶挡片。
8.进一步地,所述钩板的侧壁为法线斜向上的倾斜面,所述倾斜面表面加工有防滑齿。
9.进一步地,所述调节螺柱包括配合部和压紧部,所述配合部的外部加工有外螺纹,配合部与所述螺纹通孔通过螺纹配合,所述配合部的前端加工有方形截面通孔,所述方形截面通孔的内表面光滑,所述压紧部包括前端的压紧块和后端的滑动块,所述滑动块安装在所述方形截面通孔内且滑动块的侧壁与方形截面通孔的内壁贴合,滑动块能够在方形截面通孔内滑动,所述滑动块和方形截面通孔的孔底直接连接有压簧,所述压簧处于压缩状态,所述压紧块抵靠在所述活动夹板上。
10.进一步地,所述三氯化铱、三氯化铈的水溶液中,三氯化铱的质量百分含量为1%~2%,所述三氯化铈的质量百分含量为1%~4%;所述氨水中溶质的质量百分含量为25%。
11.进一步地,所述n-苯基-1,4-苯二胺的乙醇溶液中,n-苯基-1,4-苯二胺的浓度为2~5mg/ml,溶剂为乙醇,所述复合氧化物加入所述n-苯基-1,4-苯二胺的乙醇溶液中的固液质量比固/液=1:6~8;所述甲基异丁基酮加入质量为溶液中n-苯基-1,4-苯二胺质量的2~3倍。
12.进一步地,所述丁苯橡胶、炭黑、所述固相a、氧化锌粉末、硬脂酸、2-巯基苯并噻唑、二硫化四甲基秋兰姆、1,3-二苯基胍、硫磺按重量份数计为:丁苯橡胶100份,炭黑15~20份,所述固相a8~10份,氧化锌粉末3~5份,硬脂酸1~1.5份,2-巯基苯并噻唑0.4~0.5份,二硫化四甲基秋兰姆0.1~0.2份,1,3-二苯基胍0.4~0.5份,硫磺2~3份。
13.本发明的有益效果在于:
14.1、本发明便于安装和拆卸,显著降低了施工人员的劳动强度,且方便检修,使用效果好;
15.2、本发明用橡胶固定接触线,减少了对接触线的损伤,接触线不容易磨损,但是鉴于与接触线靠近的橡胶材质容易发生老化的现象,本技术优化橡胶的制备工艺,提高了橡胶的耐老化性,进而提高了装置的使用寿命。
16.说明书附图
17.图1为本技术所述装置的结构示意图;
18.图2为所述调节螺柱优化方案的结构示意图;
19.图3为各实施例和对比例制备的橡胶挡片拉伸强度和耐老化性能对比图。
具体实施方式
20.下面结合实施例进行详细的说明:
21.如图1所示,一种铁路接触网定位线夹装置,包括主夹具1和副夹具2,主夹具1和副夹具2的上部铰接,使得所述副夹具2能够绕铰接位置转动。所述主夹具1的上端设有螺纹孔3,所述螺纹孔3内设有连接螺柱4,所述连接螺柱4用于将主夹具1固定在支架上。所述连接螺柱4中部设有六角凸台部5,所述六角凸台部5用于拧动连接螺柱转动的受力部,六角凸台部的两侧为螺纹方向相反的外螺纹部,两个所述外螺纹部分别与所述主夹具和支架可拆卸
地连接;这样在安装时,拧动六角凸台部可同时实现连接螺柱4和主夹具1、连接螺柱4和支架的安装连接,安装方便。所述主夹具1的下部加工有第一接触线定位槽6,所述第一接触线定位槽6的上端设有橡胶挡片7,所述橡胶挡片7的一端固定在所述主夹具1的侧壁上,另一端向下弯曲形成弧形,包绕保护接触线,减少接触线因轴向拉力发生错动磨损,也可减少夹具本身对接触线的压伤,防止接触线磨损。第一接触线定位槽6的下端设有钩板8,用于钩住接触线,防止接触线向下掉出,钩板8的侧壁为法线斜向上的倾斜面,所述倾斜面表面可加工有防滑齿。所述副夹具2上与所述第一接触线定位槽6相对的位置加工有第二接触线定位槽9,所述第二接触线定位槽9的上部铰接有活动夹板10,第二接触线定位槽9的侧壁加工有螺纹通孔,所述螺纹通孔内安装有调节螺柱11,所述调节螺柱11的一端穿过螺纹通孔设有调节帽12,另一端抵靠在所述活动夹板10上,所述活动夹板10的底部也设有所述钩板8。为了防止长时间使用时调节螺柱11松动造成活动夹板10对接触线的加紧失效,作为可供优选的一种方案,对调节螺柱的结构进行优化,如图2所示,所述调节螺柱11包括配合部13和压紧部14,所述配合部13的外部加工有外螺纹,配合部13与所述螺纹通孔通过螺纹配合。所述配合部13的前端加工有方形截面通孔15,所述方形截面通孔15的内表面光滑,所述压紧部14包括前端的压紧块16和后端的滑动块17,所述滑动块17安装在所述方形截面通孔15内且滑动块的侧壁与方形截面通孔的内壁贴合,滑动块17能够在方形截面通孔15内滑动,所述滑动块和方形截面通孔的孔底直接连接有压簧18,所述压簧18处于压缩状态,所述压紧块16抵靠在所述活动夹板上。压簧18的弹力不但给了活动夹板的推力,使得调节螺柱11略有松动时活动夹板依然能够保持对接触线一定的夹持;且压簧18对配合部13有一个轴向推力,该推力对调节螺柱11和螺纹通孔之间的螺纹配合有一个自锁效应,防止调节螺柱11的松动。
22.橡胶挡片7的设计固然能够减少装置对接触线的损伤,但是鉴于与接触线靠近的橡胶材质容易发生老化的现象,本技术优化橡胶的制备工艺。为了验证本技术橡胶制备工艺的优势,设计如下实施例和对比例:
23.实施例1
24.一种橡胶挡片7的制备方法,包括如下步骤:
25.1)配置三氯化铱、三氯化铈的水溶液,所述三氯化铱、三氯化铈的水溶液中,三氯化铱的质量百分含量为1%,所述三氯化铈的质量百分含量为1%;50r/min搅拌状态下向所述三氯化铱、三氯化铈的水溶液滴加氨水,直到不在产生沉淀为止,所述氨水中溶质的质量百分含量为25%;停止搅拌,固液分离,固相置于400℃温度范围内煅烧1h,获得复合氧化物;
26.2)配置n-苯基-1,4-苯二胺的乙醇溶液,所述n-苯基-1,4-苯二胺的乙醇溶液中,n-苯基-1,4-苯二胺的浓度为2mg/ml,溶剂为乙醇;按固液质量比固/液=1:6的比例将所述复合氧化物加入所述n-苯基-1,4-苯二胺的乙醇溶液中,60r/min搅拌溶液使得复合氧化物均匀分散,然后将溶液水浴恒温至65
±
5℃温度范围内,在60r/min搅拌状态下向溶液中加入甲基异丁基酮,所述甲基异丁基酮加入质量为溶液中n-苯基-1,4-苯二胺质量的2倍;加料完成后继续搅拌10h,搅拌完成后固液分离,固相烘干获得固相a;
27.3)将丁苯橡胶、炭黑、所述固相a、氧化锌粉末、硬脂酸、2-巯基苯并噻唑、二硫化四甲基秋兰姆、1,3-二苯基胍、硫磺混合均匀,上述组分按重量份数计为:丁苯橡胶100份,炭
黑15份,所述固相a8份,氧化锌粉末3份,硬脂酸1份,2-巯基苯并噻唑0.4份,二硫化四甲基秋兰姆0.1份,1,3-二苯基胍0.4份,硫磺2份。在双辊开炼机上进行混炼,混炼15分钟,于150℃测试硫化曲线,得到t
90
值,150℃条件下对混炼胶硫化压片,压片硫化时间为t
90
值,获得所述橡胶挡片。
28.实施例2
29.一种橡胶挡片7的制备方法,包括如下步骤:
30.1)配置三氯化铱、三氯化铈的水溶液,所述三氯化铱、三氯化铈的水溶液中,三氯化铱的质量百分含量为1%,所述三氯化铈的质量百分含量为2%;50r/min搅拌状态下向所述三氯化铱、三氯化铈的水溶液滴加氨水,直到不在产生沉淀为止,所述氨水中溶质的质量百分含量为25%;停止搅拌,固液分离,固相置于400℃温度范围内煅烧1h,获得复合氧化物;
31.2)配置n-苯基-1,4-苯二胺的乙醇溶液,所述n-苯基-1,4-苯二胺的乙醇溶液中,n-苯基-1,4-苯二胺的浓度为3mg/ml,溶剂为乙醇;按固液质量比固/液=1:6的比例将所述复合氧化物加入所述n-苯基-1,4-苯二胺的乙醇溶液中,60r/min搅拌溶液使得复合氧化物均匀分散,然后将溶液水浴恒温至65
±
5℃温度范围内,在60r/min搅拌状态下向溶液中加入甲基异丁基酮,所述甲基异丁基酮加入质量为溶液中n-苯基-1,4-苯二胺质量的2倍;加料完成后继续搅拌10h,搅拌完成后固液分离,固相烘干获得固相a;
32.3)将丁苯橡胶、炭黑、所述固相a、氧化锌粉末、硬脂酸、2-巯基苯并噻唑、二硫化四甲基秋兰姆、1,3-二苯基胍、硫磺混合均匀,上述组分按重量份数计为:丁苯橡胶100份,炭黑18份,所述固相a9份,氧化锌粉末4份,硬脂酸1.2份,2-巯基苯并噻唑0.4份,二硫化四甲基秋兰姆0.1份,1,3-二苯基胍0.4份,硫磺2份。在双辊开炼机上进行混炼,混炼15分钟,于150℃测试硫化曲线,得到t
90
值,150℃条件下对混炼胶硫化压片,压片硫化时间为t
90
值,获得所述橡胶挡片。
33.实施例3
34.一种橡胶挡片7的制备方法,包括如下步骤:
35.1)配置三氯化铱、三氯化铈的水溶液,所述三氯化铱、三氯化铈的水溶液中,三氯化铱的质量百分含量为2%,所述三氯化铈的质量百分含量为3%;50r/min搅拌状态下向所述三氯化铱、三氯化铈的水溶液滴加氨水,直到不在产生沉淀为止,所述氨水中溶质的质量百分含量为25%;停止搅拌,固液分离,固相置于400℃温度范围内煅烧1h,获得复合氧化物;
36.2)配置n-苯基-1,4-苯二胺的乙醇溶液,所述n-苯基-1,4-苯二胺的乙醇溶液中,n-苯基-1,4-苯二胺的浓度为4mg/ml,溶剂为乙醇;按固液质量比固/液=1:6的比例将所述复合氧化物加入所述n-苯基-1,4-苯二胺的乙醇溶液中,60r/min搅拌溶液使得复合氧化物均匀分散,然后将溶液水浴恒温至65
±
5℃温度范围内,在60r/min搅拌状态下向溶液中加入甲基异丁基酮,所述甲基异丁基酮加入质量为溶液中n-苯基-1,4-苯二胺质量的2倍;加料完成后继续搅拌10h,搅拌完成后固液分离,固相烘干获得固相a;
37.3)将丁苯橡胶、炭黑、所述固相a、氧化锌粉末、硬脂酸、2-巯基苯并噻唑、二硫化四甲基秋兰姆、1,3-二苯基胍、硫磺混合均匀,上述组分按重量份数计为:丁苯橡胶100份,炭黑18份,所述固相a9份,氧化锌粉末4份,硬脂酸1.4份,2-巯基苯并噻唑0.5份,二硫化四甲
基秋兰姆0.2份,1,3-二苯基胍0.5份,硫磺3份。在双辊开炼机上进行混炼,混炼15分钟,于150℃测试硫化曲线,得到t
90
值,150℃条件下对混炼胶硫化压片,压片硫化时间为t
90
值,获得所述橡胶挡片。
38.实施例4
39.一种橡胶挡片7的制备方法,包括如下步骤:
40.1)配置三氯化铱、三氯化铈的水溶液,所述三氯化铱、三氯化铈的水溶液中,三氯化铱的质量百分含量为2%,所述三氯化铈的质量百分含量为4%;50r/min搅拌状态下向所述三氯化铱、三氯化铈的水溶液滴加氨水,直到不在产生沉淀为止,所述氨水中溶质的质量百分含量为25%;停止搅拌,固液分离,固相置于400℃温度范围内煅烧1h,获得复合氧化物;
41.2)配置n-苯基-1,4-苯二胺的乙醇溶液,所述n-苯基-1,4-苯二胺的乙醇溶液中,n-苯基-1,4-苯二胺的浓度为5mg/ml,溶剂为乙醇;按固液质量比固/液=1:6的比例将所述复合氧化物加入所述n-苯基-1,4-苯二胺的乙醇溶液中,60r/min搅拌溶液使得复合氧化物均匀分散,然后将溶液水浴恒温至65
±
5℃温度范围内,在60r/min搅拌状态下向溶液中加入甲基异丁基酮,所述甲基异丁基酮加入质量为溶液中n-苯基-1,4-苯二胺质量的2倍;加料完成后继续搅拌10h,搅拌完成后固液分离,固相烘干获得固相a;
42.3)将丁苯橡胶、炭黑、所述固相a、氧化锌粉末、硬脂酸、2-巯基苯并噻唑、二硫化四甲基秋兰姆、1,3-二苯基胍、硫磺混合均匀,上述组分按重量份数计为:丁苯橡胶100份,炭黑20份,所述固相a10份,氧化锌粉末5份,硬脂酸1.5份,2-巯基苯并噻唑0.5份,二硫化四甲基秋兰姆0.2份,1,3-二苯基胍0.5份,硫磺3份。在双辊开炼机上进行混炼,混炼15分钟,于150℃测试硫化曲线,得到t
90
值,150℃条件下对混炼胶硫化压片,压片硫化时间为t
90
值,获得所述橡胶挡片。
43.对比例1
44.一种橡胶挡片7的制备方法,包括如下步骤:将丁苯橡胶、炭黑、氧化锌粉末、硬脂酸、2-巯基苯并噻唑、二硫化四甲基秋兰姆、1,3-二苯基胍、硫磺混合均匀,上述组分按重量份数计为:丁苯橡胶100份,炭黑18份,氧化锌粉末4份,硬脂酸1.4份,2-巯基苯并噻唑0.5份,二硫化四甲基秋兰姆0.2份,1,3-二苯基胍0.5份,硫磺3份。在双辊开炼机上进行混炼,混炼15分钟,于150℃测试硫化曲线,得到t
90
值,150℃条件下对混炼胶硫化压片,压片硫化时间为t
90
值,获得本对比例所述橡胶挡片。
45.对比例2
46.一种橡胶挡片7的制备方法,包括如下步骤:
47.1)配置三氯化铱、三氯化铈的水溶液,所述三氯化铱、三氯化铈的水溶液中,三氯化铱的质量百分含量为2%,所述三氯化铈的质量百分含量为3%;50r/min搅拌状态下向所述三氯化铱、三氯化铈的水溶液滴加氨水,直到不在产生沉淀为止,所述氨水中溶质的质量百分含量为25%;停止搅拌,固液分离,固相置于400℃温度范围内煅烧1h,获得复合氧化物;
48.2)将丁苯橡胶、炭黑、所述复合氧化物、氧化锌粉末、硬脂酸、2-巯基苯并噻唑、二硫化四甲基秋兰姆、1,3-二苯基胍、硫磺混合均匀,上述组分按重量份数计为:丁苯橡胶100份,炭黑18份,所述复合氧化物9份,氧化锌粉末4份,硬脂酸1.4份,2-巯基苯并噻唑0.5份,
二硫化四甲基秋兰姆0.2份,1,3-二苯基胍0.5份,硫磺3份。在双辊开炼机上进行混炼,混炼15分钟,于150℃测试硫化曲线,得到t
90
值,150℃条件下对混炼胶硫化压片,压片硫化时间为t
90
值,获得本对比例所述橡胶挡片。
49.对比例3
50.一种橡胶挡片7的制备方法,包括如下步骤:
51.1)配置三氯化铱的水溶液,所述三氯化铱的水溶液中,三氯化铱的质量百分含量为2%;50r/min搅拌状态下向所述三氯化铱的水溶液滴加氨水,直到不在产生沉淀为止,所述氨水中溶质的质量百分含量为25%;停止搅拌,固液分离,固相置于400℃温度范围内煅烧1h,获得ir氧化物粉末;
52.2)配置n-苯基-1,4-苯二胺的乙醇溶液,所述n-苯基-1,4-苯二胺的乙醇溶液中,n-苯基-1,4-苯二胺的浓度为4mg/ml,溶剂为乙醇;按固液质量比固/液=1:6的比例将所述ir氧化物粉末加入所述n-苯基-1,4-苯二胺的乙醇溶液中,60r/min搅拌溶液使得ir氧化物粉末均匀分散,然后将溶液水浴恒温至65
±
5℃温度范围内,在60r/min搅拌状态下向溶液中加入甲基异丁基酮,所述甲基异丁基酮加入质量为溶液中n-苯基-1,4-苯二胺质量的2倍;加料完成后继续搅拌10h,搅拌完成后固液分离,固相烘干获得固相a;
53.3)将丁苯橡胶、炭黑、所述固相a、氧化锌粉末、硬脂酸、2-巯基苯并噻唑、二硫化四甲基秋兰姆、1,3-二苯基胍、硫磺混合均匀,上述组分按重量份数计为:丁苯橡胶100份,炭黑18份,所述固相a9份,氧化锌粉末4份,硬脂酸1.4份,2-巯基苯并噻唑0.5份,二硫化四甲基秋兰姆0.2份,1,3-二苯基胍0.5份,硫磺3份。在双辊开炼机上进行混炼,混炼15分钟,于150℃测试硫化曲线,得到t
90
值,150℃条件下对混炼胶硫化压片,压片硫化时间为t
90
值,获得本对比例所述橡胶挡片。
54.对比例4
55.一种橡胶挡片7的制备方法,包括如下步骤:
56.1)配置三氯化铈的水溶液,所述三氯化铈的水溶液中,三氯化铈的质量百分含量为3%;50r/min搅拌状态下向所述三氯化铈的水溶液滴加氨水,直到不在产生沉淀为止,所述氨水中溶质的质量百分含量为25%;停止搅拌,固液分离,固相置于400℃温度范围内煅烧1h,获得ce氧化物粉末;
57.2)配置n-苯基-1,4-苯二胺的乙醇溶液,所述n-苯基-1,4-苯二胺的乙醇溶液中,n-苯基-1,4-苯二胺的浓度为4mg/ml,溶剂为乙醇;按固液质量比固/液=1:6的比例将所述ce氧化物粉末加入所述n-苯基-1,4-苯二胺的乙醇溶液中,60r/min搅拌溶液使得ce氧化物粉末均匀分散,然后将溶液水浴恒温至65
±
5℃温度范围内,在60r/min搅拌状态下向溶液中加入甲基异丁基酮,所述甲基异丁基酮加入质量为溶液中n-苯基-1,4-苯二胺质量的2倍;加料完成后继续搅拌10h,搅拌完成后固液分离,固相烘干获得固相a;
58.3)将丁苯橡胶、炭黑、所述固相a、氧化锌粉末、硬脂酸、2-巯基苯并噻唑、二硫化四甲基秋兰姆、1,3-二苯基胍、硫磺混合均匀,上述组分按重量份数计为:丁苯橡胶100份,炭黑18份,所述固相a9份,氧化锌粉末4份,硬脂酸1.4份,2-巯基苯并噻唑0.5份,二硫化四甲基秋兰姆0.2份,1,3-二苯基胍0.5份,硫磺3份。在双辊开炼机上进行混炼,混炼15分钟,于150℃测试硫化曲线,得到t
90
值,150℃条件下对混炼胶硫化压片,压片硫化时间为t
90
值,获得本对比例所述橡胶挡片。
59.实施例5
60.对上述实施例和对比例制备的橡胶挡片分别进行老化测试,测试方法为:老化前测试橡胶的拉伸强度,然后置于100℃环境下老化48h,再测试老化后的橡胶拉伸强度,以两次拉伸强度的差值来表征橡胶的耐老化性能。结果如图3所示。由图可知,本技术制备的橡胶具有优良的耐老化性能,100℃老化48小时后橡胶的拉伸强度变化较小。对比实施例3和各对比例可知,加入处理后的ir-ce复合氧化物能够进一步提高橡胶的拉伸强度和耐老化性,这可能是由于ir-ce复合氧化物促进橡胶内部交联而产生的增强作用所致。
61.此外,应当理解,虽然本说明书按照实施方式加以描述,但并非每个实施方式仅包含一个独立的技术方案,说明书的这种叙述方式仅仅是为清楚起见,本领域技术人员应当将说明书作为一个整体,各实施例中的技术方案也可以经适当组合,形成本领域技术人员可以理解的其他实施方式。