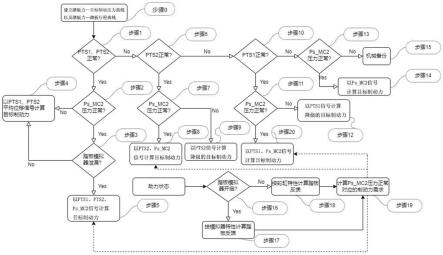
1.本发明涉及线控制动系统的领域,具体涉及一种基于行程与压力信号的多轴商用车线控制动系统驾驶员制动意图判断方法。
背景技术:2.线控制动系统是指可以电控阀组控制实现制动的制动系统,因其可电控制动的特性,线控制动系统通常用于aeb、acc、自动驾驶等需要主动制动代替或帮助驾驶员制动的场景。
3.现有的线控制动系统基于行程传感器信号,作为驾驶员制动踏板后的制动目标输入。其助力目标计算依赖位移信号,当位移信号异常后,导致计算的集成式线控制动系统(qebs,qianchao electric brake system)目标压力不合理,位移信号不可用时,无法根据驾驶员踩踏踏板程度调整qebs压力。
技术实现要素:4.本发明的目的在于克服现有技术存在的不足,而提供一种基于行程与压力信号的多轴商用车线控制动系统驾驶员制动意图判断方法,根据不同传感器信号情况,采用不同的qebs目标压力计算策略,提高可靠性和各种工况下的踏板感。
5.本发明的目的是通过如下技术方案来完成的:一种基于行程与压力信号的多轴商用车线控制动系统驾驶员制动意图判断方法,所述线控制动系统包括由制动踏板带动的主缸,主缸通过助力模块连接至轮端;所述制动踏板与主缸连接处设置有第一行程传感器pts1和第二行程传感器pts1,第一行程传感器pts1以pwm输出测得的制动踏板行程信号,第二行程传感器pts1以sent协议输出测得的制动踏板行程信号;所述助力模块内设置压力传感器ps_mc2用于测量主缸第二腔体的压力值,所述助力模块中集成有踏板模拟器;所述判断方法包括以下步骤:
6.步骤0:建立踏板力—目标制动压力曲线以及踏板力—踏板行程曲线;
7.步骤1:判断pts1和pts2的行程信号是否正常,若行程信号正常则进入步骤2,若行程信号不正常则进入步骤6;
8.步骤2:判断ps_mc2的压力信号是否正常,若压力信号正常则进入步骤3,若压力信号不正常则进入步骤4;
9.步骤3:判断踏板模拟器是否发生泄漏,若发生泄漏则进入步骤5,若未发生泄漏则进入步骤4;
10.步骤4:以pts1、pts2的平均行程信号计算目标制动压力;
11.步骤5:以pts1的行程信号、pts2的行程信号及步骤19中得到的基于ps_mc2压力信号的目标制动压力,加权计算目标制动压力;
12.步骤6:判断pts2的行程信号是否正常,若信号正常则进入步骤7,若信号不正常则
进入步骤10;
13.步骤7:判断ps_mc2的压力信号是否正常,若信号正常则进入步骤8,若信号不正常则进入步骤9;
14.步骤8:以pts2的行程信号及步骤19中得到的基于ps_mc2压力信号的目标制动压力,加权计算目标制动压力;
15.步骤9:以pts2的行程信号计算降级的目标制动压力;
16.步骤10:判断pts1的行程信号是否正常,若信号正常则进入步骤11,若信号不正常则进入步骤13;
17.步骤11:判断ps_mc2的压力信号是否正常,若信号正常则进入步骤20,若信号不正常则进入步骤12;
18.步骤12:以pts1的行程信号计算降级的目标制动压力;
19.步骤13:判断ps_mc2信号是否正常,若信号正常则进入步骤14,若信号不正常则进入步骤15;
20.步骤14:以ps_mc2的压力信号计算目标制动压力;
21.步骤15:关闭线控制动系统的助力功能,使系统进入机械备份制动状态;
22.步骤16:判断踏板模拟器是否开启,若开启则进入步骤17,若未开启则进入步骤18;
23.步骤17:按照踏板模拟器特性计算踏板反馈,进入步骤19;
24.步骤18:按照轮缸特性计算踏板反馈,进入步骤19;
25.步骤19:按照步骤17或18得到的踏板反馈计算ps_mc2压力正常对应的制动力需求,得到基于ps_mc2压力信号的目标制动压力,并输出至步骤5、步骤8、步骤20;
26.步骤20:以pts1的行程信号及步骤19中得到的基于ps_mc2压力信号的目标制动压力,加权计算目标制动压力。
27.作为进一步的技术方案,在使用pts1或pts2或二者的平均行程信号计算目标制动压力时,先通过踏板力—踏板行程曲线得到对应的踏板力,再根据踏板力—目标制动压力曲线得到对应的目标制动压力。
28.作为进一步的技术方案,在使用ps_mc2的压力信号计算目标制动压力时,先通过下式计算踏板力,再根据踏板力—目标制动压力曲线得到对应的目标制动压力:
29.f
pdl
=ps_mc2
·amc
30.ꢀꢀꢀꢀꢀꢀꢀꢀꢀꢀꢀꢀꢀꢀꢀꢀꢀꢀꢀꢀꢀꢀꢀꢀꢀꢀꢀꢀꢀꢀꢀꢀꢀꢀꢀꢀꢀꢀꢀꢀꢀꢀꢀꢀꢀꢀꢀꢀꢀꢀꢀꢀꢀꢀꢀꢀꢀ
(1)
31.式中,f
pdl
为踏板力,a
mc
为主缸(1)的面积。
32.作为进一步的技术方案,加权计算目标制动压力时,采用下式:
33.p
aim
=p
aim19
·
λ+p
aimpts
·
(1-λ)
34.ꢀꢀꢀꢀꢀꢀꢀꢀꢀꢀꢀꢀꢀꢀꢀꢀꢀꢀꢀꢀꢀꢀꢀꢀꢀꢀꢀꢀꢀꢀꢀꢀꢀꢀꢀꢀꢀꢀꢀꢀꢀꢀꢀꢀꢀꢀꢀꢀꢀꢀꢀꢀꢀꢀꢀꢀꢀꢀ
(2)
35.式中,p
aim
为目标制动压力,p
aim19
为步骤19中得到的基于ps_mc2压力信号的目标制动压力,p
aimpts
为使用pts1或pts2或二者的平均行程信号计算目标制动压力,λ为加权系数。
36.作为进一步的技术方案,所述步骤5中采用式(2)计算目标制动压力,其中p
aimpts
为以pts1、pts2的平均行程信号计算得到的目标制动压力,λ取0.2。
37.作为进一步的技术方案,所述步骤8中采用式(2)计算目标制动压力,其中p
aimpts
为
以pts2的行程信号计算得到的目标制动压力,λ取0.35。
38.作为进一步的技术方案,所述步骤20中采用式(2)计算目标制动压力,其中p
aimpts
为以pts1的行程信号计算得到的目标制动压力,λ取0.5。
39.作为进一步的技术方案,所述步骤9、步骤12中,先对踏板力—目标制动压力曲线进行降级,再计算目标制动压力。
40.作为进一步的技术方案,判断pts1、pts2及ps_mc2信号是否正常时包括以下步骤:
41.步骤a,进行pts1自身信号判断,计算pwm信号的周期、占空比是否正常,若正常则进入步骤d,若不正常则判断pts1故障;
42.步骤b,进行pts2自身信号判断,计算sent数据中的传感器状态是否正常、crc校验是否正常、互补信号的和是否正常,若正常则进入步骤d,若不正常则判断pts2故障;
43.步骤c,进行ps_mc2自身信号的判断,读取自检状态、判断ad值范围,若正常则进入步骤d,若不正常则判断ps_mc2故障;
44.步骤d:计算各正常信号显示的制动踏板是否踩下,进入步骤e;
45.步骤e:选择识别制动踏板状态相同数量占优的状态,若数量相同,则判断当前状态为制动踏板踩下;进入步骤f;
46.步骤f:判断与识别的制动踏板状态相一致的信号为正常信号。
47.作为优选的技术方案,所述步骤d中,若车辆上有单独制动灯开关,则增加该制动灯开关状态信号。
48.本发明的有益效果为:
49.1、自动判断pts1、pts2、ps_mc2信号是否正常;
50.2、基于各信号是否正常,提出了驾驶员制动意图识别方法和制动压力目标计算方法,根据不同传感器信号情况,采用不同的qebs目标压力计算策略,提高可靠性和各种工况下的踏板感。
附图说明
51.图1为线控制动系统的结构示意图。
52.图2为踏板力—目标制动压力曲线以及踏板力—踏板行程曲线。
53.图3为本发明中制动意图判断流程图。
54.图4为本发明中故障状态识别流程图。
55.附图标记说明:主缸1、助力模块2、轮端3、制动踏板4、第二腔体5、踏板模拟器6。
具体实施方式
56.下面将结合附图对本发明做详细的介绍:
57.实施例:如附图1~4所示,一种基于行程与压力信号的多轴商用车线控制动系统驾驶员制动意图判断方法,参考附图1,所述线控制动系统包括由制动踏板4带动的主缸1,主缸1通过助力模块2连接至轮端3。所述制动踏板4与主缸1连接处设置有第一行程传感器pts1和第二行程传感器pts1(如图1中pts1/2所示),第一行程传感器pts1以pwm输出测得的制动踏板4行程信号,第二行程传感器pts1以sent协议输出测得的制动踏板4行程信号。所述助力模块2内设置压力传感器ps_mc2用于测量主缸1第二腔体5的压力值,所述助力模块2
中集成有踏板模拟器6。参考附图2、3、4,所述判断方法包括以下步骤:
58.步骤0:建立踏板力—目标制动压力曲线以及踏板力—踏板行程曲线,如附图2所示。踏板力—目标制动压力曲线(图2中实线所示)一般根据客户(主机厂)提供的踏板力—车辆减速度曲线计算确定,踏板力—踏板行程曲线(图2中虚线所示)则根据踏板模拟器6确定;
59.步骤1:判断pts1和pts2的行程信号是否正常,若行程信号正常则进入步骤2,若行程信号不正常则进入步骤6;
60.步骤2:判断ps_mc2的压力信号是否正常,若压力信号正常则进入步骤3,若压力信号不正常则进入步骤4;
61.步骤3:判断踏板模拟器是否发生泄漏,若发生泄漏则进入步骤5,若未发生泄漏则进入步骤4;踏板模拟器在设计完成后,其踏板行程和踏板主缸压力(即ps_mc2处测得的压力)之间的关系是确定的,泄漏时对应关系会发生变化。
62.步骤4:以pts1、pts2的平均行程信号计算目标制动压力;
63.步骤5:以pts1的行程信号、pts2的行程信号及步骤19中得到的基于ps_mc2压力信号的目标制动压力,加权计算目标制动压力;
64.步骤6:判断pts2的行程信号是否正常,若信号正常则进入步骤7,若信号不正常则进入步骤10;
65.步骤7:判断ps_mc2的压力信号是否正常,若信号正常则进入步骤8,若信号不正常则进入步骤9;
66.步骤8:以pts2的行程信号及步骤19中得到的基于ps_mc2压力信号的目标制动压力,加权计算目标制动压力;
67.步骤9:以pts2的行程信号计算降级的目标制动压力;
68.步骤10:判断pts1的行程信号是否正常,若信号正常则进入步骤11,若信号不正常则进入步骤13;
69.步骤11:判断ps_mc2的压力信号是否正常,若信号正常则进入步骤20,若信号不正常则进入步骤12;
70.步骤12:以pts1的行程信号计算降级的目标制动压力;
71.步骤13:判断ps_mc2信号是否正常,若信号正常则进入步骤14,若信号不正常则进入步骤15;
72.步骤14:以ps_mc2的压力信号计算目标制动压力;
73.步骤15:关闭线控制动系统的助力功能,使系统进入机械备份制动状态;
74.步骤16:判断踏板模拟器是否开启,若开启则进入步骤17,若未开启则进入步骤18;
75.步骤17:按照踏板模拟器特性计算踏板反馈,进入步骤19;按照踏板模拟器的pv特性曲线计算当前踏板主缸压力值(即ps_mc2处测得的压力)对应的踏板力和踏板行程;
76.步骤18:按照轮缸特性计算踏板反馈,进入步骤19;按照轮缸的pv特性曲线计算当前踏板主缸压力值(即ps_mc2处测得的压力)对应的踏板力和踏板行程;
77.步骤19:按照步骤17或18计算得到的踏板力和踏板行程,代入踏板力—目标制动压力曲线得到基于ps_mc2压力信号的目标制动压力,并输出至步骤5、步骤8、步骤20;
78.步骤20:以pts1的行程信号及步骤19中得到的基于ps_mc2压力信号的目标制动压力,加权计算目标制动压力。
79.进一步的,参考附图2,在使用pts1或pts2或二者的平均行程信号计算目标制动压力时(如步骤4中),先通过踏板力—踏板行程曲线(图2中虚线)得到对应的踏板力,再根据踏板力—目标制动压力曲线(图2中实线)得到对应的目标制动压力。
80.进一步的,在使用ps_mc2的压力信号计算目标制动压力时(如步骤14中),先通过下式计算踏板力,再根据踏板力—目标制动压力曲线得到对应的目标制动压力:
81.f
pdl
=ps_mc2
·amc
82.ꢀꢀꢀꢀꢀꢀꢀꢀꢀꢀꢀꢀꢀꢀꢀꢀꢀꢀꢀꢀꢀꢀꢀꢀꢀꢀꢀꢀꢀꢀꢀꢀꢀꢀꢀꢀꢀꢀꢀꢀꢀꢀꢀꢀꢀꢀꢀꢀꢀꢀꢀꢀꢀꢀꢀꢀꢀꢀꢀꢀꢀꢀ
(1)
83.式中,f
pdl
为踏板力,a
mc
为主缸1的面积。
84.进一步的,加权计算目标制动压力时,采用下式:
85.p
aim
=p
aim19
·
λ+p
aimpts
·
(1-λ)
86.ꢀꢀꢀꢀꢀꢀꢀꢀꢀꢀꢀꢀꢀꢀꢀꢀꢀꢀꢀꢀꢀꢀꢀꢀꢀꢀꢀꢀꢀꢀꢀꢀꢀꢀꢀꢀꢀꢀꢀꢀꢀꢀꢀꢀꢀꢀꢀꢀꢀꢀꢀꢀꢀꢀꢀꢀꢀꢀꢀꢀꢀꢀ
(2)
87.式中,p
aim
为目标制动压力,p
aim19
为步骤19中得到的基于ps_mc2压力信号的目标制动压力,p
aimpts
为使用pts1或pts2或二者的平均行程信号计算目标制动压力,λ为加权系数。例如在所述步骤5中采用式(2)加权计算目标制动压力,其中p
aimpts
为以pts1、pts2的平均行程信号计算得到的目标制动压力,优选地,此处加权系数λ取0.2。又如,在所述步骤8中也采用式(2)加权计算目标制动压力,其中p
aimpts
为以pts2的行程信号计算得到的目标制动压力,由于此处仅使用pts2的行程信号,故加权系数λ取0.35。再如,所述步骤20中仍采用式(2)计算目标制动压力,其中p
aimpts
为以pts1的行程信号计算得到的目标制动压力,由于此处仅使用pts1的行程信号,pts1为pwm输出信号,与pts2的sent信号相比,缺少信号状态识别,因此对应的加权系数λ取0.5。
88.进一步的,步骤9中,仅以pts2的行程信号计算的目标制动压力,为了防止单一信号源引起的非预期制动,对踏板力—目标制动压力曲线进行降级(即提高图2中2a处的横坐标值、减小图2中2b线段的斜率、减小图2中2c拐点处的纵坐标值),再计算目标制动压力。优选地,调整时,将2a处的横坐标值提高25%、2b线段的斜率减小25%、2c拐点处的纵坐标值也减小25%。
89.同样的,在步骤12中,仅以pts1的行程信号计算的目标制动压力,为了防止单一信号源引起的非预期制动,对踏板力—目标制动压力曲线进行降级,再计算目标制动压力,即提高图2-2a处的横坐标值,减小图2-2b线段的斜率,减小图2-2c拐点处的纵坐标值。
90.进一步的,判断pts1、pts2及ps_mc2信号是否正常时(如步骤1、2中)包括以下步骤:
91.步骤a,进行pts1自身信号判断,计算pwm信号的周期、占空比是否正常,若正常则进入步骤d,若不正常则判断pts1故障;
92.步骤b,进行pts2自身信号判断,计算sent数据中的传感器状态是否正常、crc校验是否正常、互补信号的和是否正常,若正常则进入步骤d,若不正常则判断pts2故障;
93.步骤c,进行ps_mc2自身信号的判断,读取自检状态、判断ad值范围,若正常则进入步骤d,若不正常则判断ps_mc2故障;
94.步骤d:计算各正常信号显示的制动踏板是否踩下,进入步骤e;优选地,若车辆上
有单独制动灯开关,则增加该制动灯开关状态信号
95.步骤e:选择识别制动踏板状态相同数量占优的状态,若数量相同,则判断当前状态为制动踏板踩下;进入步骤f;
96.步骤f:判断与识别的制动踏板状态相一致的信号为正常信号。
97.在步骤a、b、c中对pts1、pts2及ps_mc2三者的信号进行独立判断,步骤e、f中对三者的信号进行一致性判断。
98.本发明基于线控制动系统,在该系统内部集成2个行程传感器(pts1/2)和1个压力传感器(ps_mc2)工作状态不确定的情况下,先进行故障状态识别;然后,根据不同传感器的信号情况(正常或故障状态),采用不同的qebs目标压力计算策略,将驾驶员的制动意图数值化为可供计算的目标制动压力,进而提高车辆行驶时的可靠性和各种工况下的踏板感。
99.可以理解的是,对本领域技术人员来说,对本发明的技术方案及发明构思加以等同替换或改变都应属于本发明所附的权利要求的保护范围。