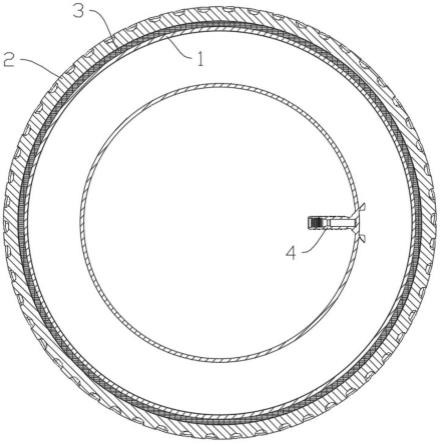
1.本实用新型涉及交通工具技术领域,具体涉及一种轮胎及具有其的滑板车。
背景技术:2.近年来,代步装置例如电动滑板车,因其外观时尚性、携带便捷性、控制简单、低碳出行等优点逐渐走近人们的视野,且越来越受到人们的关注和青睐。
3.电动滑板车行业的兴起及蓬勃发展,同时也带动了滑板车细分轮胎市场的发展。滑板车轮胎主要分为实心胎和充气胎。早期滑板车轮胎以带内胎的充气胎为主。由于一般入门级滑板车没有减震设计,充气胎与实心胎相比,充气胎能够通过内部空腔气体来缓冲达到减震效果。另外,在雨天湿滑路面,充气胎的抗湿滑性能明显优于实心胎。
4.然而,现有的带内胎的充气胎最大的短板在于爆胎问题,这也是针对滑板车投诉率反馈最高的问题。原因主要有以下几点:一、滑板车尤其是无减震设计的滑板车,轮胎会存在低气压骑行的情况。二、滑板车轮胎的内腔小,单位体积气压损失率高。三、滑板车用户目前还没有良好的胎压保养习惯。所以,轮胎在这样欠压行驶的条件下,轮胎外胎与内胎间的摩擦系数会增加,疲劳生热也会增加,内胎被外胎磨破的风险也相应增加。因此,针对目前滑板车有内轮胎普遍存在的爆胎问题开发一种能够提高滑板车轮胎耐久尤其是欠压行驶条件下的耐久走行里程的方法迫在眉睫。
技术实现要素:5.因此,本实用新型所要解决的技术问题是提供一种轮胎及具有其的滑板车,以保证轮胎减震效果的同时,提高耐久度。
6.为解决上述技术问题,本实用新型提供了一种轮胎,应用于滑板车,包括:内胎;外胎,包裹在所述内胎外;其中,所述内胎与所述外胎之间设有润滑部。
7.进一步地,所述内胎形成有与所述外胎相接触的接触部分,所述润滑部至少覆盖了所述接触部分。
8.进一步地,所述润滑部均匀覆盖在所述内胎的所述接触部分上。
9.进一步地,所述内胎的外周表面形成为所述接触部分。
10.进一步地,所述润滑部为添加在所述内胎配方中的润滑剂,所述润滑剂被配置为在所述内胎成型过程中不会析出,且在所述内胎硫化完成后的预设时间,所述润滑部析出至所述内胎的外表面。
11.进一步地,所述润滑部为二甲基硅油。
12.进一步地,所述润滑部为润滑油,所述润滑部的涂抹厚度为50~300μm。
13.进一步地,所述内胎为充气式的胎体。
14.进一步地,所述外胎包括内里部,所述内胎可拆卸地安装于所述内里部,所述内里部的表面凸设有排气纹路,所述排气纹路为曲面结构且沿着所述外胎的周向间隔设置。
15.此外,本实用新型还提供一种滑板车,包括前述所述的轮胎。
16.本实用新型提供的技术方案,具有以下优点:本实用新型通过设置润滑部,改善了内胎表面的润滑特性,降低了轮胎内胎与外胎间的摩擦系数,降低了内外胎间的疲劳生热和内胎被外胎磨破的风险,从而提高了内胎的耐久性能,保证了轮胎的使用寿命,降低了轮胎在欠压行驶条件下的爆胎风险,提升了产品品质和客户满意度。
附图说明
17.为了更清楚地说明本实用新型具体实施方式或现有技术中的技术方案,下面将对具体实施方式或现有技术描述中所需要使用的附图作简单地介绍,显而易见,下面描述中的附图是本实用新型的一些实施方式,对于本领域普通技术人员来讲,在不付出创造性劳动的前提下,还可以根据这些附图获得其他的附图。
18.图1是本实用新型轮胎的结构示意图。
19.图2是本实用新型轮胎的分解结构示意图。
20.图3是本实用新型轮胎的剖面示意图。
21.图4是本实用新型轮胎在另一方向上的剖面示意图。
22.附图标记说明:
23.1、内胎;11、防滑圈;2、外胎;21、内里部;22、胎面;23、防滑纹;3、润滑部;4、气门嘴。
具体实施方式
24.下面将结合附图对本实用新型的技术方案进行清楚、完整地描述,显然,所描述的实施例是本实用新型一部分实施例,而不是全部的实施例。下文中将参考附图并结合实施例来详细说明本实用新型。需要说明的是,在不冲突的情况下,本实用新型中的实施例及实施例中的特征可以相互组合。
25.需要说明的是,本实用新型的说明书和权利要求书及上述附图中的术语“第一”、“第二”等是用于区别类似的对象,而不必用于描述特定的顺序或先后次序。
26.在本实用新型中,在未作相反说明的情况下,使用的方位词如“上、下、顶、底”通常是针对附图所示的方向而言的,或者是针对部件本身在竖直、垂直或重力方向上而言的;同样地,为便于理解和描述,“内、外”是指相对于各部件本身的轮廓的内、外,但上述方位词并不用于限制本实用新型。
27.请参阅图1至图4所示,对应于本实用新型一种较佳实施例的轮胎,在一种示意性的场景中,该轮胎可以应用于滑板车。值得注意的是,上述举例中的轮胎被应用于滑板车,仅是一种可行的适用场景,在其他可行且不可被明确排除的场景中,该轮胎也可应用于其他类型的代步装置。
28.进一步地,轮胎包括内胎1、外胎2以及润滑部3,外胎2包裹在内胎1外,以保护内胎1,润滑部3设置在内胎1和外胎2之间,以降低内胎1与外胎2间的摩擦系数。
29.进一步地,外胎2主要由天然橡胶、合成橡胶、炭黑、尼龙、钢丝等材质制成。外胎2整体呈圆环形结构,外胎2的内周表面向内凹设有内里部21,内里部21为沿着外胎2的周向延伸而成的环形槽,内胎1自内里部21的槽口可拆卸地安装于内里部21中,使得外胎2对内胎1进行包裹,从而保护内胎1。优选地,内里部21在其槽口至槽底的方向上槽宽逐渐增大,
从而提高对内胎1的包裹性,避免内胎1在安装到位后脱离外胎2。
30.由于外胎2在硫化过程中,需要将其置于硫化设备(图未示)的模具中,并将硫化设备的胶囊装入内里部21中,利用胶囊的膨胀压力使外胎2充满模具,确保外胎2充分硫化。然而胶囊与内里部21贴合接触,在硫化过程中,不易排出气体,从而降低外胎2的合格率。为了避免上述情况发生,内里部21的表面凸设有排气纹路(图未示),排气纹路为曲面结构且沿着外胎2的周向间隔设置。排气纹路可以在外胎2生产过程中挤压而成。通过将排气纹路的表面设计成曲面结构,从而避免产生棱角,当将内胎1装入内里部21后,有效减缓内胎1的磨损,提高内胎1的使用寿命。此外,排气纹路的设置,也能够使得内胎1与外胎2在行驶过程中不易相对转动,进而减小了因转动而造成内胎1磨损的几率。
31.外胎2包括环绕轮胎的旋转轴线设置的胎面22,胎面22上设有用于增加与路面摩擦的防滑纹23。优选地,防滑纹23自胎面22向内凹陷而成,相较于自胎面22凸出的防滑纹23,凹设的防滑纹23行驶过程中滚动阻力小,噪音低,舒适性佳。在本实施例中,防滑纹23具体为人字纹,以便于切割加工,防滑纹23沿着胎面22的周向连续或者断续分布。
32.进一步地,内胎1由丁基橡胶材质制成。内胎1整体呈圆环形结构,内胎1具有与内里部21的内壁相接触的接触部分,润滑部3至少覆盖了接触部分,从而降低内胎1与外胎2间的摩擦系数,进而降低内外胎间的疲劳生热和内胎1被外胎2磨破的风险。在本实施例中,内胎1的外周表面形成接触部分,润滑部3均匀涂覆在接触部分上。
33.为了提高轮胎整体的减震性能,在一实施例中,内胎1为充气式的内胎,内胎1上设有用于向内胎1内进行供气的气门嘴4。优选地,气门嘴4设置在内胎1位于内里部21槽口处的内周表面上,且朝向内胎1的中心延伸,从而避免气门嘴4受到外胎2的限位,提高内胎1安装的便捷性。优选地,气门嘴4在朝向内胎1的中心延伸后向外弯折,从而便于供气装置(图未示)与气门嘴4相接。诚然,在其他实施例中,内胎1也可采用非充气式的发泡体(图未示),发泡体内可具有若干用于减震的减震孔(图未示)。
34.优选地,内胎1的至少部分外周表面凸设有与内里部21的内壁相接触的防滑部,该防滑部可以形成为防滑圈11,防滑圈11的数量有多个,且沿着内胎1的周向间隔排布。当将内胎1安装至外胎2内后,防滑圈11能够限制外胎2,使得内胎1与外胎2在行驶过程中不易相对转动,进而减小了因转动而造成内胎1磨损的几率。
35.进一步地,润滑部3为涂覆在内胎1上的润滑油,润滑部3可采用人工或者涂抹工装进行涂抹。润滑部3的涂抹厚度为50~300μm,以节省润滑部3的同时,达到最佳的润滑效果。优选地,润滑部3具体可选用二甲基硅油,由于二甲基硅油分子结构式中只有甲基基团,性状稳定佳,并且二甲基硅油具有无毒、无腐蚀、热稳定、安全等特点,从而不会存在影响内胎1物性的风险。
36.诚然,在另一实施例中,润滑部3还可以是添加在内胎1配方中的润滑剂,且该润滑剂不会在成型过程中析出。当内胎1硫化完成并停放一定时间后,该润滑剂会自然析出至内胎1的外表面,以形成润滑层。采用上述方式,能够避免对内胎1进行润滑部3的涂抹工作,有效提高了轮胎的生产效率。
37.进一步地,以230
×
50规格的轮胎为例,在室内进行转鼓耐久走行试验,其中,标准胎压为50psi,试验载荷为75kg,试验速度为25km/h,障碍块数1个,轮胎可靠性验证通过标准为:轮胎耐久走行里程达到3500km且无损坏,在该实验条件下,本实用新型轮胎和现有轮
胎均能满足内外胎无损坏。
38.当将标准胎压改变至37psi,此时轮胎处于欠压状态,为了提高实验的准确度,本实验采用不少于3组本实用新型轮胎和现有轮胎进行对比,以损坏形式为内胎1磨破为标准,通过实验可知,在该状态下,本实用新型轮胎的欠压耐久里程分别为1820km、1940km以及1760km,平均走行里程达到1840km,而对比案例的欠压耐久里程分别为760km、820km以及996km,平均走行里程为859km。因此,本新型轮胎在欠压状态下耐久水平整体提高114%。
39.此外,本实用新型还提供一种滑板车,包括前述的轮胎、用于安装轮胎的轮毂(图未示)以及用于安装轮毂的车架(图未示)。
40.综上所述,本实用新型通过设置润滑部,改善了内胎表面的润滑特性,降低了轮胎的内胎与外胎间的摩擦系数,降低了内外胎间的疲劳生热和内胎被外胎磨破的风险,从而提高了内胎的耐久性能,显著提升了轮胎的使用寿命,降低了轮胎在欠压行驶条件下的爆胎风险,提高了产品品质和客户满意度。
41.显然,上述所描述的实施例仅仅是本实用新型一部分的实施例,而不是全部的实施例。基于本实用新型中的实施例,本领域普通技术人员在没有做出创造性劳动前提下,可以做出其它不同形式的变化或变动,都应当属于本实用新型保护的范围。