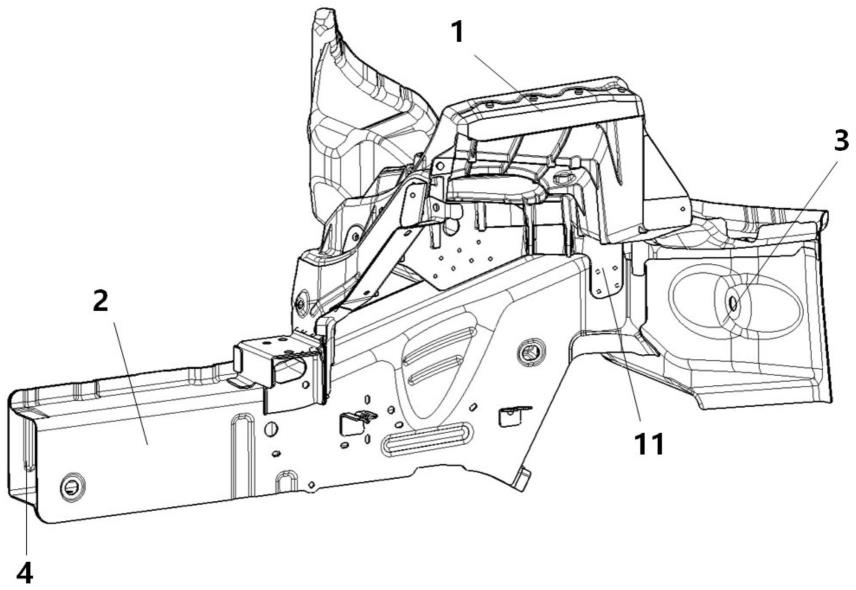
1.本实用新型涉及汽车技术领域,尤其是涉及一种减震器座与纵梁横梁耦合形成的减震结构及车辆。
背景技术:2.目前全球安全性评价全面、客观,偏置碰撞评价是整个体系的较新项目,也越来越重要。如iihs和中保研安全指数的25%的重叠刚性墙碰撞实验即小偏置碰撞实验,因前纵梁与刚性壁障无或者极小重叠梁,基本不参与碰撞变形吸能,导致shotgun(前轮罩上部和a柱竖板中间区域)和a柱变形较大,影响驾乘人员安全。c-ncap和e-ncap的mpdb(50km/h的50%重叠对碰)工况,对碰能量较大,同时考察碰撞车和壁障的变形情况,除了考虑碰撞车辆伤害,还要考虑壁障变形均匀,防止过大侵入量,这要求碰撞车吸能盒、前纵梁和shotgun尽可能吸收能量,减少侵入量。
3.汽车前纵梁结构对于汽车的碰撞安全,整车nvh、车身模态、车身刚度等都具有重要影响,特别是在汽车行驶过程中发生正面的碰撞时,汽车的前纵梁结构对于传递和吸收撞击力和撞击能量,降低驾驶员和乘员的伤害起到了至关重要的作用。目前的前纵梁结构设计存在无法有效传递碰撞力和碰撞能量等问题,影响车身整体的安全性能。
技术实现要素:4.本实用新型的目的就是为了克服上述现有技术存在的缺陷而提供一种能够有效传递碰撞力和碰撞能量,提升车身整体安全性能的减震器座与纵梁横梁耦合形成的减震结构。
5.本实用新型的目的可以通过以下技术方案来实现:
6.第一方面,本实用新型提供一种减震器座与纵梁横梁耦合形成的减震结构,包括减震器座,前纵梁,前围横梁,所述前纵梁包括前纵梁外板和前纵梁内板,所述前纵梁外板和前纵梁内板连接形成空腔,所述的减震器座与前纵梁和前围横梁相连接构成传递载荷的减震结构总成。
7.进一步地,所述前纵梁外板包括上前纵梁外板和后前纵梁外板,减震器座一侧设有向外延伸的凸起。
8.进一步地,所述上前纵梁外板靠近前纵梁内板焊接边,后前纵梁外板靠近前围横梁焊接边。
9.进一步地,所述凸起与减震器座本体之间形成30-150度夹角。
10.进一步地,所述凸起呈l型、c型、弧形,或多折边状。
11.进一步地,所述后前纵梁外板与减震器座,凸起,前纵梁内板和前围横梁连接形成一个空腔。
12.进一步地,所述上前纵梁外板和前纵梁内板与减震器座固定连接。
13.进一步地,所述减震器座材料为铸铝。
14.进一步地,所述前纵梁,前围横梁为钢板冲压件。
15.第二方面,提供了一种汽车,包括前述的减震器座与纵梁横梁耦合形成的减震结构。
16.与现有技术相比,本实用新型具有以下优点:
17.(1)通过减震器座将前纵梁与前围横梁固定连接形成一个总成,拓展了车辆受到碰撞时的传力路径,提高了车身的抗疲劳强度。
18.(2)减震器座采用铸铝材质,在承受同等载荷的情况下,整体结构更具轻量化的优势。
附图说明
19.图1为本实用新型的一种结构示意图;
20.图2为本实用新型的另一种结构示意图;
21.图3为本实用新型中减震器座与后前纵梁外板和前围横梁装配结构的截面图;
22.图4为本实用新型中减震器座与上前纵梁外板和前纵梁内板装配结构的截面图;
23.图5为本实用新型中凸起的局部放大图。
24.图中:1、减震器座;11、凸起;2、前纵梁外板;21、上前纵梁外板;22、后前纵梁外板;3、前围横梁;4、前纵梁内板。
具体实施方式
25.下面结合附图和具体实施例对本实用新型进行详细说明。
26.实施例
27.本实用新型提供了一种减震器座与纵梁横梁耦合形成的减震结构,如图1和图2所示,包括减震器座1,前纵梁,前围横梁3,减震器座1材料为铸铝,在保证总成结构刚度的情况下达到了轻量化的目的,前纵梁,前围横梁3为钢板冲压件,前纵梁包括前纵梁外板2和前纵梁内板4,前纵梁外板2和前纵梁内板4固定连接形成空腔的前纵梁结构,前纵梁外板2包括上前纵梁外板21和后前纵梁外板22,所述上前纵梁外板21靠近前纵梁内板焊接边,后前纵梁外板22靠近前围横梁焊接边。
28.如图5所示,减震器座1一侧设有凸起11,凸起11与减震器座1本体之间形成30-150度夹角,凸起11有多种形状,例如:l型、c型、弧形或多折边状等,在本实施例中,凸起11为l形凸起,如图3所示,后前纵梁外板22与减震器座1,凸起11,前纵梁内板4和前围横梁3连接形成一个空腔,实现减震器座1与前纵梁之间的连接,上前纵梁外板21和前纵梁内板4与减震器座1固定连接,实现减震器座1与前纵梁和前围横梁3之间的连接,上述两处的连接构成了传递载荷的减震结构总成。
29.本实用新型中的各部件连接方式为汽车制造工艺中常用的连接方法,例如:spr连接、fds连接或点焊连接,其中,spr采用的是自冲铆连接,主要是经过夹紧、冲裁、扩张、冲铆等步骤进行加工连接,fds采用的是现有技术中的流钻螺钉进行连接,通过旋转加热、穿透、通孔、攻螺纹、拧螺纹、紧固进行加固。具体地,在本实施例中,如图3所示,后前纵梁外板22与减震器座1,凸起11的连接方式为spr连接,后前纵梁外板22与前围横梁3通过点焊的方式连接。如图4所示,所述上前纵梁外板21和前纵梁内板4与减震器座1通过spr相连接,减震器
座1以上述方式将前纵梁与前围横梁3通过不同平面上的装配关系固定连接,形成了减震器座1与前纵梁和前围横梁3构成的传递载荷的减震结构总成,拓展了车辆受到碰撞时的传力路径,提高了车身的抗疲劳强度。
30.本实用新型实施例提供了一种汽车,包括前述的减震器座与纵梁横梁耦合形成的减震结构。所述减震结构包括:减震器座1,前纵梁,前围横梁3。
31.所述减震器座1材料为铸铝,在保证总成结构刚度的情况下达到了轻量化的目的,前纵梁,前围横梁3为钢板冲压件,前纵梁包括前纵梁外板2和前纵梁内板4,前纵梁外板2和前纵梁内板4固定连接形成空腔的前纵梁结构,前纵梁外板2包括上前纵梁外板21和后前纵梁外板22,所述上前纵梁外板21靠近前纵梁内板焊接边,后前纵梁外板22靠近前围横梁焊接边。
32.如图5所示,减震器座1一侧设有l形凸起11,凸起11与减震器座1本体之间形成30-150度夹角,凸起11有多种形状,例如:l型、c型、弧形或多折边状等。如图3所示,后前纵梁外板22与减震器座1,凸起11,前纵梁内板4和前围横梁3连接形成一个空腔,实现减震器座1与前纵梁之间的连接,上前纵梁外板21和前纵梁内板4与减震器座1固定连接,实现减震器座1与前纵梁和前围横梁3之间的连接,上述两处的连接构成了传递载荷的减震结构总成。
33.本实用新型中的各部件连接方式为汽车制造工艺中常用的连接方法,例如:spr连接、fds连接或点焊连接,其中,spr采用的是自冲铆连接,主要是经过夹紧、冲裁、扩张、冲铆等步骤进行加工连接,fds采用的是现有技术中的流钻螺钉进行连接,通过旋转加热、穿透、通孔、攻螺纹、拧螺纹、紧固进行加固。具体地,在本实施例中,如图3所示,后前纵梁外板22与减震器座1,l形凸起11的连接方式为spr连接,后前纵梁外板22与前围横梁3通过点焊的方式连接。如图4所示,所述上前纵梁外板21和前纵梁内板4与减震器座1通过spr相连接,减震器座1以上述方式将前纵梁与前围横梁3通过不同平面上的装配关系固定连接,形成了减震器座1与前纵梁和前围横梁3构成的传递载荷的减震结构总成,拓展了车辆受到碰撞时的传力路径,提高了车身的抗疲劳强度。
34.综上所述,本实用新型通过减震器座将前纵梁与前围横梁相连接,加强了连接强度,拓展了车辆受到碰撞时的传力路径,提高了车身的抗疲劳强度,是对现有技术的一种补充。