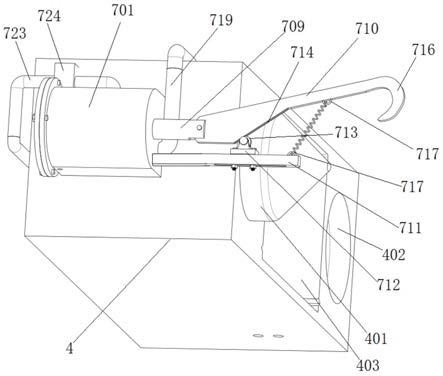
[0001]
本发明涉及铁路车辆技术领域,尤其涉及一种用于铁路车辆风电自动对接及分离的锁紧装置。
背景技术:[0002]
铁路上运行的列车是由前方的火车头以及后部连挂的车辆串接而成,当列车由静态转变成动态或由低速运行转变成高速运行是火车头通过车钩拉动实现;当列车由动态转变为静态或由高速运行转变成低速运行是各车辆通过压力空气推动基础制动装置动作,进而带动闸瓦压向转动的车轮来实现的。由于车辆自身无压力空气风源,需依靠前部的火车头向后方连挂的各车辆依次充入压力空气,后方车辆才能推动基础制动装置动作进而产生制动力。而火车头向后部车辆传输压力空气是通过车辆间连接的列车软管实现的,列车软管的连接点位于各车辆连接端部的车钩下方。
[0003]
由此,目前为了保证列车正常减速停车,在火车头与后部车辆车钩连挂后就需将各车之间的列车软管连接起来,由火车头通过连接的列车软管向各车列车软管充风,在火车头与后部车辆车钩分离前就需要先将待分离车辆之间的列车软管分离,然后再分离车钩。
[0004]
目前,列车软管的分离和连接均是通过人工进行的,而通过人工进行手动分离和连接列车软管、开闭塞门的作业方式造成调车效率低,并且存在人身及行车安全隐患;同时,因货车车辆自身不带电源也无供电装置,严重的制约了对车辆的自动检测及自动控制技术的发展,如此有必要提供一种能够实现铁路车辆风电自动对接的装置,由机车向后方连挂车辆自动供风供电,但由于列车在行驶过程中,火车头与车辆之间以及车辆与车辆之间的间距在发生变化,尽管上述两者之间通过车钩进行连挂,但车钩与车钩连挂后,车钩与车钩之间仍然存在间隙,因此可能导致机械对接体对接后会随两者之间距离的变化而产生相同的距离变化,从而导致安装在两个机械对接内的风电对接体分离,从而导致电路和风路断开并发生排风制动停车,因此有必要提供一种锁紧装置以保持两机械对接体对接后的距离不变,从而解决上述问题。
技术实现要素:[0005]
本发明提供了一种用于铁路车辆风电自动对接及分离的锁紧装置,通过锁紧装置锁紧两个相互对接的机械对接体,从而有效的避免了两个机械对接体在对接后,随机车与车辆、车辆与车辆之间间距的变化而导致两个机械对接体之间的间距发生变化,导致安装在机械对接体内部的风电对接体分离并发生排风制动停车,进而使电路和风路断开的问题。
[0006]
首先需要说明的是本发明中所提到的机车即为火车头,火车头即为机车;
[0007]
下文所述的列车软管并非是专指现有铁路列车上的列车软管,主要是指通过软管与列车管连接的管路,本发明简称为列车软管。
[0008]
为实现上述目的,本发明提供如下技术方案:
[0009]
一种用于铁路车辆风电自动对接及分离的锁紧装置,包括分别安装在两个相互对接的机械对接体两侧的锁紧风缸和锁紧销,所述锁紧风缸内安装有锁紧活塞,锁紧活塞与锁紧风缸内表面的接触面上安装有密封圈,通过锁紧活塞将锁紧风缸分为锁紧风缸前腔室和锁紧风缸后腔室,锁紧活塞上安装有锁紧活塞杆,锁紧活塞杆经过锁紧风缸前腔室活动的贯穿锁紧风缸的缸体,并且锁紧风缸缸体与锁紧活塞杆的接触面上安装有密封圈,锁紧活塞杆位于锁紧风缸外部的一端活动安装有锁紧勾,锁紧勾能够在列车直线行进方向的竖直平面上做顺时针或逆时针旋转,锁紧风缸靠近机械对接体所在平面的一端安装有滑台座,所述滑台座上安装有二号滑台,二号滑台的顶部与锁紧勾的倾斜部接触,所述锁紧勾倾斜部靠近锁紧活塞杆的一端到地面的距离小于锁紧勾远离锁紧活塞杆的一端到地面的距离,所述锁紧风缸后腔室安装有锁紧弹簧,锁紧弹簧的一端安装在锁紧活塞上,一端安装在锁紧风缸后腔室远离锁紧活塞的一端内壁上,并在锁紧风缸后腔室设置有与外界连通第五排气孔,锁紧风缸前腔室设置有贯穿锁紧风缸壁的第三通气孔,第三通气孔外接有一号风管,并在一号风管上安装有二号三通电磁阀,使得在当两个机械对接体对接后,前车后端部机械对接体上的一号风管内进入压力空气,压力空气再通过第三通气孔进入到锁紧风缸前腔室,使得锁紧活塞带动锁紧活塞杆和锁紧勾回缩,且锁紧勾在回缩的同时顺时针旋转,使得锁紧勾的勾部紧勾在锁紧销上,有效的避免了在行驶过程中,车辆与车辆之间间距的变化导致两个对接的机械对接体分离,从而导致两个对接的风电对接体分离,进而导致后部车辆电路和风路的中断并发生排风制动停车的问题。两对接车辆在分离时,只需控制二号三通电磁阀将锁紧风缸前腔室到外界的风路连通,即可将锁紧风缸前腔室的压力空气排出,使得锁紧勾做逆时针旋转的同时向前移动,进而使得锁紧勾和锁紧销分离。
[0010]
进一步的,所述锁紧活塞与锁紧风缸内壁的接触面上安装有密封圈,从而有效的防止了锁紧风缸前腔室中的压力空气进入到锁紧风缸后腔室中,从而有效的避免了锁紧风缸前腔室泄压造成的锁紧活塞无法推动锁紧弹簧压缩,进而使锁紧勾无法挂在锁紧销上的问题。
[0011]
进一步的,所述二号滑台上安装有滚轮,滚轮与所述倾斜部接触,避免了二号滑台与倾斜部之间直接接触导致的摩擦力大的问题,通过滚轮与倾斜部接触有效的降低了摩擦力。
[0012]
再进一步的,所述倾斜部上设置有沿倾斜部长度方向上的二号滑槽,所述滚轮与二号滑槽的槽底接触,并能够在二号滑槽内滚动,通过设置二号滑槽有效的避免了锁紧勾左右摆动,导致二号滑槽与滚轮脱离。
[0013]
又进一步的,所述锁紧勾的勾部到倾斜部之间安装有挂环,且滑台座远离锁紧风缸的一端也安装有挂环,两个挂环之间安装有弹簧;通过弹簧拉住锁紧勾,使锁紧勾通过二号滑槽紧贴在滚轮上,从而有效的防止车辆行进过程中,锁紧勾的跳动导致二号滑槽与滚轮脱离。
[0014]
优选的,所述滑台座上设置有沿滑台座长度方向上的条形滑槽,二号滑台通过可拆卸的固定安装方式安装在条形滑槽上,从而可在安装时调节二号滑台在条形滑槽上的安装位置来使锁紧勾的勾部能够挂在锁紧销上。
[0015]
优选的,所述锁紧风缸后腔室中设置有第四通气孔,所述第四通气孔连接有三号
风管,三号风管通过内风缸上设置的第二气压通道与内风缸后腔室相通,并且第四通气孔与第三通气孔之间的距离需按照以下状态进行设置,即当锁紧勾挂在锁紧销上,并锁紧勾紧贴锁紧销时,第三通气孔能够与第四通气孔形成通路。压力空气进入到锁紧风缸前腔室后,锁紧活塞向远离锁紧活塞杆的一端移动,当锁紧勾挂在锁紧销上后,且锁紧销和锁紧勾紧密贴合时,由于锁紧活塞向远离锁紧活塞杆的一端移动,从而使得第三通气孔和第四通气孔能够存在同一腔室之中,进而使第三通气孔和第四通气孔连通,压力空气再经过第四通气孔、三号风管和第二气压通道进入到内风缸后腔室,从而推动内活塞杆移动,进而使得风电对接体伸出,进行风电对接。从而使得当机械对接体对接完成并锁紧后再进行风电对接体的对接,从而使得风电对接体的对接更加准确可靠。
[0016]
进一步的,所述三号风管上安装有二号超压快速排风阀,从而使得当两车辆在行进过程中,两对接车辆之间发生冲击使内风缸后腔室的压力升高时,当内风缸后腔室的气压超过二号超压快速排风阀设定压力值时,能够排出内风缸后腔室中的超压空气,保持内风缸后腔室空气压力的稳定,避免了内风缸后腔室空气压力过高导致设备损坏的问题。
[0017]
优选的,所述锁紧风缸包括具备一端开口的锁紧风缸体和盖合在所述开口上的端盖,所述开口位于锁紧风缸远离锁紧活塞杆杆头的一端。从而方便加工以及装配。
[0018]
优选的,端盖位于锁紧风缸内部的一端设置有弹簧座,锁紧活塞靠近端盖的一端面上也设置有弹簧座,锁紧弹簧一端套装在端盖的弹簧座上,另一端套装在锁紧活塞的弹簧座上,所述两个弹簧座的外径略小于锁紧弹簧的内径。从而有效的避免了弹簧的径向偏移,并且也避免了锁紧弹簧固定安装导致的拆卸和安装不变的问题。
[0019]
与现有技术相比本发明的有益效果是:通过本发明的锁紧装置使得两个机械对接体在对接后进行锁紧,使得在火车头与车辆之间或者车辆与车辆之间在行进过程中间距加大时,两个对接的机械对接体之间的间距无法发生变化,进而避免了风电对接体脱离,形成风路和电路的中断并导致排风制动停车。
附图说明
[0020]
图1为本发明的风电自动对接及分离装置安装位置示意图;
[0021]
图2为本发明的风电自动对接及分离装置结构示意图;
[0022]
图3为本发明的机械对接体结构示意图;
[0023]
图4为本发明的显示检测仓内部结构的剖视图;
[0024]
图5为本发明的风电对接体结构示意图;
[0025]
图6为本发明的风电对接体安装位置示意图;
[0026]
图7为本发明的风电对接体的防尘盖开启后的结构示意图;
[0027]
图8为本发明的显示电极孔内部结构的剖视图;
[0028]
图9为本发明的显示通风管道内部结构的剖视图;
[0029]
图10为本发明的图9a部分放大示意图;
[0030]
图11为本发明的锁紧装置安装位置示意图;
[0031]
图12为本发明的锁紧装置具体结构示意图;
[0032]
图13为本发明的显示锁紧风缸内部结构的剖视图;
[0033]
图14为本发明的伸缩装置安装位置示意图;
[0034]
图15为本发明的显示内风缸和外风缸内部结构的剖视图;
[0035]
图16为本发明的支撑柱与翼柱的装配关系示意图;
[0036]
图17为本发明的支撑柱内部结构示意图;
[0037]
图18为本发明的回转中心销安装位置示意图;
[0038]
图19为本发明的外风缸与外活塞杆的装配关系示意图;
[0039]
附图标记说明:1.牵引梁;2.吊座;3.箱体;301.顶板;302.底板;303.侧板;304.条形槽;305.弹簧插板;306.板弹簧;307.支撑柱;308.安装盒;309.滚轴;310.环状凸缘;311.限位板;312.销轴;4.机械对接体;401.第一凸起部;402.第一凹陷部;403.第一通孔;404.连接孔;405.检测仓;406.检测柱塞;407.弹性部件;408.第一排气孔;409.环形槽;410.第一通气孔;411.第二通气孔;412.第二排气孔;413.第一排污孔;414.一号滑槽;5.风电对接体;501.正电极;502.负电极;503.电极引线;504.通风管道;505.标准密封圈;506.密封条;507.防尘盖;508.弹簧挂销;509.支架;510.触碰板;511.滑杆;512.翻转销;513.弧形滑槽;514.底座;515.电极杆;516.密封端板;517.电极绝缘套;518.环形仓;519.凸起环;520.电极弹簧;521.一号滑台;522.第二凸起部;523.第二凹陷部;524.阀杆;525.前部腔室;526.中部腔室;527.后部腔室;528.环形凸起部;529.延时风缸;530.活塞杆;531.活塞;532.延时风缸前腔室;533.延时风缸后腔室;534.第五通气孔;535.外风管;536.第六通气孔;537.第七通气孔;538.前腔通气孔;539.中腔通气孔;540.圆柱形安装座;6.伸缩装置;601.外风缸;602.外活塞;603.外风缸前腔室;604.外风缸后腔室;605.第一连接板;606.第三排气孔;607.第一气压通道;608.内风缸;609.内活塞;610.内风缸前腔室;611.内风缸后腔室;612.内活塞杆;613.第二连接板;614.第二气压通道;615.第四排气孔;616.芯杆;617.第三气压通道;618.四号风管;619.五号风管;620.一号超压快速排风阀;621.调压阀;622.一号三通电磁阀;623.两通电磁阀;624.压力传感器;625.三号三通电磁阀;626.销孔;627.回转中心销;628.翼柱;629.第八通气孔;630.第一花键槽;631.卡环;632.第二花键;633.第二花键槽;7.锁紧装置;701.锁紧风缸;702.锁紧销;703.锁紧活塞;704.锁紧风缸前腔室;705.锁紧风缸后腔室;706.第三通气孔;707.第五排气孔;708.锁紧弹簧;709.锁紧活塞杆;710.锁紧勾;711.滑台座;712.二号滑台;713.滚轮;714.倾斜部;715.二号滑槽;716.勾部;717.挂环;718.条形滑槽;719.一号风管;720.二号三通电磁阀;721.二号风管;722.第四通气孔;723.三号风管;724.二号超压快速排风阀。
具体实施方式
[0040]
下面将结合附图,对本发明实施例中的技术方案进行清楚、完整地描述,显然,所描述的实施例仅仅是本发明一部分实施例,而不是全部的实施例。基于本发明中的实施例,本领域普通技术人员在没有做出创造性劳动前提下所获得的所有其他实施例,都属于本发明保护的范围。
[0041]
参见附图11到附图14,一种用于铁路车辆风电自动对接及分离的锁紧装置,包括分别安装在两个相互对接的机械对接体4两侧的锁紧风缸701和锁紧销702,所述锁紧风缸701内安装有锁紧活塞703,锁紧活塞703与锁紧风缸701内表面的接触面上安装有密封圈,通过锁紧活塞703将锁紧风缸701分为锁紧风缸前腔室704和锁紧风缸后腔室705,锁紧活塞703上安装有锁紧活塞杆709,锁紧活塞杆709经过锁紧风缸前腔室704活动的贯穿锁紧风缸
701的缸体,并且锁紧风缸701的缸体与锁紧活塞杆709的接触面上安装有密封圈,锁紧活塞杆709位于锁紧风缸701外部的一端活动安装有锁紧勾710,锁紧勾710能够在列车直线行进方向的竖直平面上做顺时针或逆时针旋转,锁紧风缸701靠近机械对接体4对接面所在平面的一端安装有滑台座711,所述滑台座711上安装有二号滑台712,二号滑台712的顶部与锁紧勾710的倾斜部714接触,所述锁紧勾710倾斜部714靠近锁紧活塞杆709的一端到地面的距离小于锁紧勾710远离锁紧活塞杆709的一端到地面的距离,所述锁紧风缸后腔室705安装有锁紧弹簧708,锁紧弹簧708的一端安装在锁紧活塞703上,一端安装在锁紧风缸后腔室705远离锁紧活塞703的一端内壁上,并在锁紧风缸后腔室705设置有与外界连通第五排气孔707,锁紧风缸前腔室704设置有贯穿锁紧风缸701壁的第三通气孔706,第三通气孔706外接有一号风管719,并在一号风管719上安装有二号三通电磁阀720,使得在当两个机械对接体4对接后,前车后端部或车辆后部的机械对接体4上的一号风管719内进入压力空气,压力空气再通过第三通气孔706进入到锁紧风缸前腔室704,使得锁紧活塞703带动锁紧活塞杆709和锁紧勾710回缩,且锁紧勾710在回缩的同时顺时针旋转,使得锁紧勾710的勾部716紧勾在锁紧销702上,有效的避免了在行驶过程中,车辆与车辆之间或火车头与车辆之间间距的变化导致两个对接的机械对接体4分离,从而导致两个对接的风电对接体5分离,进而导致后部车辆电路和风路的中断并发生排风制动停车的问题。两对接车辆在分离时,只需控制二号三通电磁阀720将锁紧风缸前腔室704到外界的风路连通,即可将锁紧风缸前腔室704的压力空气排出,使得锁紧勾710做逆时针旋转的同时向前移动,进而使得锁紧勾710和锁紧销702分离。
[0042]
所述锁紧活塞703与锁紧风缸701内壁的接触面上安装有密封圈,从而有效的防止了锁紧风缸前腔室704中的压力空气进入到锁紧风缸后腔室705中,从而有效的避免了锁紧风缸前腔室704泄压造成的锁紧活塞703无法推动锁紧弹簧708压缩,进而使锁紧勾710无法挂在锁紧销702上的问题。
[0043]
所述二号滑台712上安装有滚轮713,滚轮713与所述倾斜部714接触,避免了二号滑台712与倾斜部714之间直接接触导致的摩擦力大的问题,通过滚轮713与倾斜部714接触有效的降低了摩擦力。
[0044]
所述倾斜部714上设置有沿倾斜部714长度方向上的二号滑槽715,所述滚轮713与二号滑槽715的槽底接触,并能够在二号滑槽715内滚动,通过设置二号滑槽715有效的避免了锁紧勾710左右摆动,导致二号滑槽715与滚轮713脱离。
[0045]
所述锁紧勾710的勾部716到倾斜部714之间安装有挂环717,且滑台座711远离锁紧风缸701的一端也安装有挂环717,两个挂环717之间安装有弹簧;通过弹簧拉住锁紧勾710,使锁紧勾710通过二号滑槽715紧贴在滚轮713上,从而有效的防止车辆行进过程中,锁紧勾710的跳动导致二号滑槽715与滚轮713脱离。
[0046]
所述滑台座711上设置有沿滑台座711长度方向上的条形滑槽718,二号滑台712通过可拆卸的固定安装方式安装在条形滑槽718上,从而可在安装时调节二号滑台712在条形滑槽718上的安装位置来使锁紧勾710的勾部716能够挂在锁紧销702上。
[0047]
参见附图11到附图14,再结合附图15,所述锁紧风缸后腔室705中设置有第四通气孔722,所述第四通气孔722连接有三号风管723,三号风管723通过内风缸上设置的第二气压通道614与内风缸后腔室611相通,并且第四通气孔722与第三通气孔706之间的距离需按
照以下状态进行设置,即当锁紧勾710挂在锁紧销702上,并锁紧勾710紧贴锁紧销702时,第三通气孔706能够与第四通气孔722形成通路。压力空气进入到锁紧风缸前腔室704后,锁紧活塞703向远离锁紧活塞杆709的一端移动,当锁紧勾710挂在锁紧销702上后,且锁紧销702和锁紧勾710紧密贴合时,由于锁紧活塞703向远离锁紧活塞杆709的一端移动,从而使得第三通气孔706和第四通气孔722能够存在同一腔室之中,进而使第三通气孔706和第四通气孔722连通,压力空气再经过第四通气孔722、三号风管723和第二气压通道614进入到内风缸后腔室611,从而推动内活塞杆移动,进而使得风电对接体5伸出,进行风电对接。从而使得当机械对接体4对接完成并锁紧后再进行风电对接体5的对接,从而使得风电对接体5的对接更加准确可靠。
[0048]
所述三号风管723上安装有二号超压快速排风阀724,从而使得当两车辆在行进过程中,两对接车辆之间发生冲击,使内风缸后腔室611的压力升高时,当内风缸后腔室611的气压超过二号超压快速排风阀724设定压力值时,能够排出内风缸后腔室611中的超压空气,保持内风缸后腔室611空气压力的稳定,避免了内风缸后腔室611空气压力过高导致设备损坏的问题。
[0049]
所述锁紧风缸701包括具备一端开口的锁紧风缸701体和盖合在所述开口上的端盖,所述开口位于锁紧风缸701远离锁紧活塞杆709杆头的一端。从而方便加工以及装配。
[0050]
本发明也可以运用到其他的对接装置中,只需将锁紧装置7中的锁紧风缸701和锁紧销702分别安装在两个对接装置的两侧即可,再将一号风管719接入气源即可,即可通过向锁紧风缸前腔室704中输入压力空气,使得锁紧勾710回缩的同时做顺时针旋转,即能实现锁紧工作,在脱钩时,通过二号三通电磁阀720连通锁紧风缸前腔室704到外界的气路,即可排出锁紧风缸前腔室704的空气,在锁紧弹簧708的弹簧力作用下,锁紧活塞703推动锁紧活塞杆709伸出,进而使锁紧勾710伸出的同时做逆时针旋转,从而实现了脱钩。
[0051]
因此对发明应当理解为是为实现两相互需要对接的物体而做出的锁紧装置7,而并非是专用于铁路车辆风电自动对接及分离装置中的锁紧装置7。因此只要是为了避免两个相互对接的对接体分离,均可视实际情况采用本发明,并且其具体安装方式根据实际情况进行装配即可,故应当将本发明所述的机械对接体4理解为是需要两个相互对接的物体即可,而并非专指为本发明下文所述的机械对接体4。
[0052]
下面通过对一种铁路机车车辆风电自动对接及分离装置以便本领域技术人员充分理解本发明,参见附图1到附图19,一种铁路车辆风电自动对接及分离装置,包括安装在火车头前后端部和车辆前后端部牵引梁1车钩缓冲器下方的箱体3,箱体3内部放置有风电对接体5,且箱体3靠近风电对接体5对接面的位置处设置有开口,使得风电对接体5能够从所述开口伸出;并且两对接车辆的风电对接体5处于同一水平面时,两个风电对接体5能够以两个风电对接体5几何中心连线的中点水平旋转180度对称;所述风电对接体5包括设置在对接面的多个正电极501和多个负电极502,风电对接体5远离对接面的一端连接多根电极引线503,其电极引线503分别与所述正电极501和负电极502连接;所述风电对接体5对接面的中心位置处设置有从风电对接体5对接面贯穿风电对接体5的通风管道504,其通风管道504位于风电对接体5对接面的一端安装有标准密封圈505;所述风电对接体5远离对接面的一端安装有能够带动风电对接体5向待对接车辆移动的伸缩装置6,伸缩装置6远离风电对接体5的一端安装在箱体3的顶板301和底板302上;本发明通过前车的伸缩装置6推动风
电对接体5向后车风电对接体5移动,使得两个风电对接体5的正电极501、负电极502以及通风管道504上的标准密封圈505分别相互接触,从而实现了风路和电路的导通,使得前车的压力空气和电流能够进入到后车中,在安装本装置时,只需将通风管道504远离风电对接体5对接面的一端同列车软管相连,并将电极引线503与车载电路连接,即可实现上述效果。
[0053]
所述风电对接体5的对接面上设置有第二凸起部522和第二凹陷部523,第二凸起部522包括安装在风电对接体5对接面上的定位部和安装在定位部远离风电对接体5对接面一端的导向部,导向部靠近风电对接体5对接面的一端到导向部远离风电对接体5对接面的一端直径逐渐减小,使得两对接车辆风电对接体5上的第二凸起部522能够相互插入对方车辆的第二凹陷部523中,并且能够通过导向部实现导向对位,便于第二凸起部522插入第二凹陷部523中。
[0054]
所述风电对接体5安装在机械对接体4的第一通孔403内,机械对接体4放置于箱体3内部,从而使得风电对接体5也放置于箱体3内,所述第一通孔403从机械对接体4对接面的中心位置处贯穿机械对接体4,所述机械对接体4对接面上设置有第一凸起部401和第一凹陷部402,第一凸起部401和第一凹陷部402分别位于第一通孔403两侧,当两待对接车辆的机械对接体4处于同一水平面时,两个机械对接体4能够以两个机械对接体4几何中心连线的中点水平旋转180度对称,并在所述机械对接体4远离对接面的一端安装有能够带动机械对接体4向待对接车辆移动的伸缩装置6,使得两待对接车辆上安装的机械对接体4的第一凸起部401均能够相互插入对方车辆的第一凹陷部402中,实现两对接车辆机械对接体4的对位。
[0055]
所述第一凸起部401包括安装在机械对接体4上的定位部和安装在定位部远离机械对接体4对接面一端的导向部,导向部靠近机械对接体4对接面的一端到导向部远离机械对接体4对接面的一端直径逐渐减小,从而使得第一凸起部401在插入第一凹陷部402时能够通过导向部起到导向对位的作用。
[0056]
本发明首先通过前车机械对接体4的伸缩装置6推动机械对接体4向后车移动,并使前车机械对接体4的第一凸起部401插入后车的第一凹陷部402中,同时后车机械对接体4的第一凸起部401也插入前车的第一凹陷部402中,从而完成了一次定位,再通过前车风电对接体5的伸缩装置6推动风电对接体5向后车移动,前车风电对接体5的第二凸起部522插入后车风电对接体5的第二凹陷部523中,同时后车风电对接体5的第二凸起部522插入前车风电对接体5的第二凹陷部523中,实现风电对接体5定位的同时使得两个风电对接体5上的正电极501、负电极502以及通风管道504上的标准密封圈505接触,实现了向后部车辆的通风通电。
[0057]
所述第一凹陷部402的内部设置有用于连通检测仓405的连接孔404,使得第一凸起部401完全插入第一凹陷部402后,第一凸起部401上的导向部能够通过连接孔404伸入检测仓405中;所述检测仓405中安装有可在检测仓405中沿第一凹陷部402轴向方向上移动的检测柱塞406,检测柱塞406与远离第一凹陷部402的检测仓405内壁之间安装有能够压缩和伸张的弹性部件407,远离第一凹陷部402的检测仓405内部设置有贯穿检测仓405内壁与外界相通的第一排气孔408,并在所述检测仓405内设置有用于检测检测柱塞406位移量的检测装置。从而可通过检测装置检测检测柱塞406的位移量来判断第一凸起部401伸入检测仓405的位置是否符合要求,来判断第一凸起部401和第一凹陷部402是否完成定位,以及两个
机械对接体4的对接面是否完全贴合,避免第一凸起部401上有异物导致定位不佳、两机械对接体4对接面贴合不到位的问题,并且通过设置第一排气孔408有效的防止了检测仓405形成背压或负压。
[0058]
所述检测装置包括环绕检测柱塞406的周向开设的环形槽409,形成两端直径大于中间直径的检测柱塞406;并在所述检测仓405的内侧壁上方开设有第一通气孔410和第二通气孔411,内侧壁的下方开设有第二排气孔412和第一排污孔413,所述第一排污孔413紧邻第一凹陷部402,第一通气孔410和第二排气孔412均连通第一凸起部401未插入第一凹陷部402时检测柱塞406的环形槽409,其第二通气孔411与第一通气孔410均连通第一凸起部401插入第一凹陷部402时检测柱塞406的环形槽409,第二通气孔411外部连接有列车软管;即上述第一通气孔410、第二通气孔411和第二排气孔412设置的位置以及其位置关系参照下述状态进行设置:当第一凸起部401未插入第一凹陷部402时,第一通气孔410和第二排气孔412与所述环形槽409连通,当第一凸起部401插入第一凹陷部402后且两个机械对接体4的对接面完全贴合后,第一通气孔410和第二通气孔411与所述环形槽409连通,此时第二排气孔412位于检测柱塞406到第一凹陷部402之间。当两个机械对接体4的对接面完全贴合后,导向部推动检测柱塞406移动到极限位置,此时第一通气孔410和第二通气孔411之间形成通路,由于第二通气孔411外部接有列车软管,因此只需通过传感器检测第一通气孔410外接风管压力,即可判断出第一凸起部401伸入检测仓405中的位置是否符合标准以及两个机械对接体4的对接面是否完全贴合。上述设置排污孔的目的在于排出第一凸起部401带入第一检测仓405中的雨水或异物。
[0059]
所述检测柱塞406直径大于中间的两端均绕检测柱塞406的周向设置有多个密封圈,从而有效的防止了气压泄漏。
[0060]
所述机械对接体4远离对接面的一端面上设置有与连接孔404导通的凹孔,并在所述凹孔内插入有具备一个开口的检测仓405,检测仓405的开口靠近连接孔404,并与连接孔404形成通路,检测仓405外壁与凹孔内壁的接触面安装有多个密封圈,对应的在检测仓405的侧壁上设置有分别用于连通第一排气孔408、第二排气孔412、第一通气孔410、第二通气孔411和第一排污孔413的通孔。通过在凹孔内插入检测仓405的方式,既方便了加工又方便了零件之间的装配。
[0061]
所述检测仓405外壁的密封圈分别设置在第一排气孔408和第二通气孔411之间的检测仓405外壁上、第二通气孔411和第一通气孔410之间的检测仓405外壁上、第一通气孔410和第二排气孔412之间的检测仓405外壁上以及第二排气孔412和第一排污孔413之间的检测仓405外壁上,上述四处位置可以设置一个或多个密封圈进行密封。
[0062]
所述弹性部件407采用弹簧,弹簧的一端固定安装在检测仓405远离第一凹陷部402的一端,另一端固定安装在检测柱塞406上。
[0063]
所述检测柱塞406靠近第一凹陷部402的端面设置有密封圈,第一凸起部401未插入第一凹陷部402时,检测柱塞406靠近第一凹陷部402的端面上设置的密封圈能够与检测仓405靠近第一凹陷部402的内壁贴合,在使得机械对接体4在非对接状态下,检测柱塞406在弹性部件407的作用下紧贴在监测仓靠近第一凹陷部402的内壁上,通过密封圈进行密封,从而有效的防止了机械对接体4在非对接状态下,雨水或异物进入到检测仓405中。
[0064]
所述风电对接体5的对接面上设置有环绕对接面边缘的密封条506,使得两个风电
对接体5在对接后,两个风电对接体5上的密封条506能够相贴合,并且设置在风电对接体5对接面上的正电极501、负电极502以及通风管道504的标准密封圈505能够相贴合,从而有效的避免了在两个风电对接体5对接后雨水或异物进入风电对接体5对接面与密封条506密封所形成的腔室中。
[0065]
所述风电对接体5的对接面上设置有防尘盖507,防尘盖507的两侧可活动的安装在风电对接体5的两个侧面上,并在所述风电对接体5的任意一侧设置有驱动防尘盖507基于防尘盖507两侧安装点的连线向上翻转的驱动机构和传动机构。所述驱动机构可以采用电机,传动机构可以采用齿轮箱或其他公知的传动机构,具体的,电机连接转轴,转轴带动连接齿轮箱输入端,齿轮箱输出端连接在防尘盖507任意一侧的安装点,所述安装点可以是轴,轴与防尘盖507固定安装,与风电对接体5活动安装即可,从而实现了防尘盖507的转动,上述实现方式均是本领域技术人员的公知技术常识,因此不进行更加详细的叙说,当然上述实现方式并非是对本发明的限定,本发明也可以采用其他公知的方式驱动防尘盖507向上翻转。
[0066]
所述传动机构包括在防尘盖507两侧安装的弹簧挂销508、风电对接体5两侧安装的弹簧挂销508;位于风电对接体5和防尘盖507同一侧的弹簧挂销508之间安装有弹簧;当防尘盖507盖合在风电对接体5的对接面上时,且风电对接体5处于水平时,风电对接体5和防尘盖507同一侧的两个弹簧挂销508处于同一水平面上,并在所述风电对接体5的任意一个侧面底部上安装两个竖直向上的支架509,两个支架509沿列车直线行进方向排列,另一个侧面的底部安装有触碰板510;所述两个支架509之间安装有滑杆511,滑杆511的长度大于两个支架509之间的距离,使得滑杆511能够在两个支架509上沿滑杆511轴向运动,两个支架509之间的滑杆511杆身上固定套装有翻转销512的一端,翻转销512的另一端位于防尘盖507侧壁设置的弧形滑槽513内,从而使得两个风电对接体5在接触时,形成所述传动机构的驱动机构,其中一个风电对接体5上的滑杆511触碰到另外一个风电对接体5的触碰板510后,滑杆511向远离风电对接体5对接面的一端移动,从而带动防尘盖507向上翻转,由于在对接时两个弹簧挂销508之间的弹簧处于拉伸状态,当两车之间的风电对接体5分离时,弹簧收缩,从而带动防尘盖507向下翻转盖合在风电对接体5的对接面上,同时插入防尘盖507弧形滑槽513内的翻转销512带动滑杆511回位。通过在风电对接体5的对接面上设置防尘盖507有效的避免在非对接状态下异物与正电极501、负电极502和通风管道504接触。
[0067]
所述翻转销512上套装有滚套,滚套位于弧形滑槽513内,通过滚套将翻转销512与弧形滑槽513间的滑动摩擦变为滚动摩擦,更加利于翻转销512带动防尘盖507翻转。
[0068]
所述防尘盖507盖合在风电对接体5对接面上时,与风电对接体5相靠近的一面上设置有密封条506,其防尘盖507上的密封条506能够与风电对接体5对接面上的密封条506相接触,从而保证了防尘盖507在盖合后,雨水或异物不能进入其内,并在所述防尘盖507的靠近地面的一端设置有一通孔,使得当风电对接体5分离后,防尘盖507盖合上后,两分离车辆列车管的空气压力能够从该通孔内排至外界。
[0069]
所述风电对接体5包括固定在风电对接体5底部的底座514,底座514两侧之间的距离大于风电对接体5两侧之间的距离,并且底座514的两侧分别伸出风电对接体5的两侧,并分别在其伸出的两侧分别安装所述支架509和所述触碰板510。
[0070]
所述正电极501和负电极502均是通过电极杆515插入贯穿风电对接体5的电极孔,
所述电极孔靠近风电对接体5对接面的一端安装有密封端板516,电极杆515活动的穿过密封端板516伸入电极孔内部,电极杆515位于电极孔中的杆身上套装有电极绝缘套517,所述电极绝缘套517靠近密封端板516的一端设置有环绕电极杆515圆周的环形仓518,电极杆515位于环形仓518内的杆身上且紧靠密封端板516的位置处设置有绕电极杆515圆周的凸起环519;凸起环519到环形仓518远离密封端板516的内端壁之间安装有电极弹簧520,电极弹簧520套装在电极杆515上;从而在两个对接车辆的正电极501互相接触、负电极502互相接触时,电极杆515上的凸起环519挤压弹簧,从而有效的增强了对接电极的接触压力,缓和了电极杆515对接冲击,防止了电极杆515冲撞损坏。所述密封端板516采用绝缘材料制成,与电极绝缘套517共同作用,避免在风电对接体5通电情况下,电极发生漏电现象。
[0071]
推动所述机械对接体4移动的伸缩装置6包括安装在机械对接体4远离对接面一端面上的外风缸601,所述外风缸601包括安装在外风缸601内部的外活塞602,外活塞602与外风缸601内壁的接触面上安装有密封圈,通过外活塞602将外风缸601分为靠近机械对接体4的外风缸前腔室603和远离机械对接体4的外风缸后腔室604,在所述外活塞602上安装有外活塞杆,外活塞杆从外风缸前腔室603伸出外风缸601,并在外活塞杆的杆头形成与机械对接体4远离对接面的一端相装配的第一连接板605,并在所述外活塞杆上套装有弹簧,弹簧一端安装在外活塞602上,另一端安装在外风缸前腔室603靠近机械对接体4的内壁上,并在所述外风缸前腔室603内侧壁且靠近机械对接体4的位置处设置有与外界连通的第三排气孔606,所述外风缸601远离机械对接体4的一端设置与外风缸后腔室604相通的第一气压通道607,第一气压通道607连接有列车软管。从而可通过向第一气压通道607中注入压力空气,带动外活塞602压缩弹簧,使外活塞杆伸出,进而带动机械对接体4向前移动,使得两对接车辆的机械对接体4对接。
[0072]
所述外活塞杆远离外活塞602的一端外表面设置有第二花键632,外风缸601远离外活塞602且与外活塞杆配合的内表面设置有第二花键槽633,外活塞杆上的第二花键632与外风缸601上的第二花键槽633配合,以防止外活塞杆相对外风缸601体转动。
[0073]
所述外活塞602与外风缸601的接触面之间安装有密封圈。有效的避免了外风缸后腔室604中的气体流向外风缸前腔室603中,从而造成泄压。
[0074]
推动所述风电对接体5移动的伸缩装置6包括被所述外风缸601套装在内的内风缸608上,内风缸608的风缸体形成外风缸601的外活塞杆,并在所述内风缸608内安装有内活塞609,内活塞609与内风缸608内壁的接触面上设置有密封圈,将内风缸608分为靠近风电对接体5的内风缸前腔室610和远离风电对接体5的内风缸后腔室611,内活塞609上安装有内活塞杆612,内活塞杆612经过内风缸前腔室610伸出内风缸608,内活塞杆612位于内风缸前腔室610的杆身套装有弹簧,弹簧一端固定在内活塞609上,一端固定在内风缸前腔室610靠近风电对接体5的内端面,所述内活塞杆612活动的贯穿第一连接板605,并在内活塞杆612远离内活塞609的一端形成与风电对接体5连接的第二连接板613,并在内风缸608的缸体壁内设置有与内风缸后腔室611连通的第二气压通道614,第二气压通道614经过第一连接板605、内风缸608缸体壁到外活塞602与内风缸后腔室611连通,内风缸前腔室610内侧壁且靠近风电对接体5的位置处设置有与外界相通的第四排气孔615,并且所述风电对接体5活动安装在机械对接体4上设置的第一通孔403中。从而在两个机械对接体4对接完成后,再向第二气压通道614中输送压力空气,将所述风电对接体5推出对接,如此保证了两个风电
对接体5上的正负电极502和标准密封圈505能够完全贴合在一起,有效的避免了由于加工时尺寸误差造成两个风电对接体5的正负电极502和标准密封圈505无法完全贴合,从而无法形成通路;所述内活塞杆612为中空杆,并在内活塞杆612的内部插入有一根中空的芯杆616,芯杆616与内活塞杆612采用间隙配合,并且芯杆616的外壁上设置有多个与内活塞杆612内壁接触的密封圈,芯杆616远离风电对接体5的一端可活动的穿过内活塞609、内风缸后腔室611、外活塞602以及外风缸后腔室604并与外风缸601上设置的第三气压通道617相接固定,芯杆616与内活塞609和外活塞602的接触面上设置有密封圈,所述内活塞杆612靠近机械对接体4的一端穿过第二连接板613,并与风电对接体5的通风管道504相接通;第三气压通道617外接有管道,从而使得在风电对接体5完成对接后前部车辆的压力空气能够通过通风管道504,再经过内活塞杆612、芯杆616、第三气压通道617和第三气压通道617的外界管道进入到后部车辆的列车软管中。
[0075]
所述风电对接体5的两侧分别设置有一号滑台521,对应的所述机械对接体4的第一通孔403中设置有一号滑槽414,风电对接体5通过一号滑台521和所述一号滑槽414配合装配在机械对接体4的第一通孔403中,使得内风缸608能够推动风电对接体5在机械对接体4的一号滑槽414上移动,并完成风电对接体5的对接;非对接时,风电对接体5回缩在机械对接体4的后端部,只有在机械对接体4完成对接后,风电对接体5才会从机械对接体4的后端部前伸,与对方风电对接体5对接。
[0076]
所述外活塞602靠近机械对接体4的一端为筒状结构,内风缸608插入并固定在该筒状结构内部,内风缸608与筒状结构侧壁相接触的面上设置有密封圈,从而有效的避免了内风缸后腔室611中的压力空气进入到外风缸前腔室603中,从而造成泄压。
[0077]
所述风电对接体5的通风管道504内插入有具备一端开口的圆桶状阀杆524,阀杆524的开口端安装有标准密封圈505,所述阀杆524的开口端位于通风管道504外部,并在所述通风管道504内部设置前部腔室525、中部腔室526和后部腔室527,前部腔室525、中部腔室526和后部腔室527的直径均大于通风管道504的直径,其阀杆524插入通风管道504后使得前部腔室525和中部腔室526形成环形腔室,并且前部腔室525和中部腔室526之间通过通风管道504的管壁间隔开;所述后部腔室527的内径大于中部腔室526的内径,并在阀杆524远离风电对接体5对接面的一端设置有绕阀杆524圆周的环形凸起部528,其环形凸起部528与后部腔室527靠近中部腔室526的端壁接触,从而通过该环形凸起部528将中部腔室526和后部腔室527隔开,并在所述后部腔室527中安装有延时风缸529,所述延时风缸529内可活动的插入有活塞杆530,活塞杆530插入延时风缸529的一端安装有活塞631,活塞631的圆周面上设置有延时风缸529内壁接触的密封圈,活塞杆530的另一端与阀杆524连接,通过活塞631将延时风缸529分为延时风缸前腔室532和延时风缸后腔室533,活塞杆530位于延时风缸529外部的一段上套装有弹簧,所述弹簧的一端固定安装在延时风缸529上,另一端固定安装在阀杆524上,所述延时风缸前腔室532设置有与后部腔室527连通的第五通气孔534,延时风缸后腔室533设置有与外风管535连接的第六通气孔536,且所述第五通气孔534的孔径远小于第六通气孔536,所述外风管535与前部腔室525和后部腔室527之间开设的第七通气孔537相连,使得延时风缸后腔室533与前部腔室525相通,所述阀杆524上开设有分别与前部腔室525和中部腔室526连通的前腔通气孔538和中腔通气孔539,并且所述中腔通气孔539的个数多于前腔通气孔538,中腔通气孔539的直径大于前腔通气孔538,并且前腔通气
孔538时刻与前部腔室525连通,中腔通气孔539时刻与中部腔室526连通,后部腔室527远离风电对接体5对接面的一端通过第二连接板613密封,内活塞杆612穿过第二连接板613伸入后部腔室527中,从而使得后部腔室527中的压力空气能够进入到内活塞杆612中,其延时风缸529的安装方式有多种,例如通过支撑杆固定安装在后部腔室527中,或固定安装在第二连接板613上均可,只需保留能够使内活塞杆612和后部腔室527相通的孔即可。两车辆分离时因第五通气孔534的孔径远小于第六通气孔536,故延时风缸前腔室532压力空气的排放速度远小于延时风缸后腔室533压力空气的排放速度,从而使得延时风缸前腔室532中的空气压力大于延时风缸后腔室533的空气压力,从而达到阻碍阀杆524环形凸起部528与后部腔室527靠近中部腔室526的端壁接触,为列车管压力空气的排放预留了足够时间,从而使分离车辆原地制动,有效的避免了后部车辆的溜车。
[0078]
如图10所示,活塞杆530杆头穿过环形凸起部528再安装在阀杆524底部的通孔中,采用上述安装方式时,就需要在活塞杆530与所述阀杆524底部通孔的接触面上安装密封圈;除上述方式以外,也可将环形凸起部528设置成与阀杆524一体成型,活塞杆530杆头直接安装在阀杆524远离开口的一端,如此不需要设置通孔,也不需设置密封圈,就能后部腔室527中的压力空气进入阀杆。
[0079]
所述外风管535与第七通气孔537之间设置有密封圈。上述管道与通孔之间的安装方式属于本领域人员公知的技术常识,即管道与通孔之间如何安装能够保证密封性,均是本领域技术人员公知的技术常识,例如在加工时,将第七通气孔537与外风管535的连接端设置成圆管状,并在第七通气孔537与外风管535的接触端设置密封圈,安装时通过卡箍就能实现外风管535与第七通气孔537的连接并保证其密封性。
[0080]
所述延时风缸529靠近内活塞杆612的一端设置有圆柱形安装座540,内活塞杆612套装在圆柱形安装座540上,并且所述内活塞杆612固定套装在所述圆柱形安装座540上,并在所述内活塞杆612上设置有与后部腔室527连通的第八通气孔629,从而使得后部腔室527中的压力空气能够经过第八通气孔629进入到内活塞杆612中,由于内活塞杆612和圆柱形安装座540采用固定安装的方式,从而避免了延时风缸529的周向转动。
[0081]
所述内活塞杆612靠圆柱形安装座540方向设置有多个第一花键槽630,圆柱形安装座540上设置有多个第一花键,圆柱形安装座540上的第一花键插入内活塞杆612上的第一花键槽630中相互配合定位。
[0082]
所述阀杆524开口端到前部腔室525之间的阀杆524与通风管道504的接触面上安装有密封圈,后部腔室527靠近中部腔室526的端面与环形凸起部528之间安装有密封圈。
[0083]
所述风电自动对接及分离装置还包括锁紧装置7,所述锁紧装置7包括安装在机械对接体4一侧的锁紧风缸701和安装在机械对接体4另一侧的锁紧销702,所述锁紧风缸701内部可活动的安装有锁紧活塞703,锁紧活塞703与锁紧风缸701内壁的接触面上安装有密封圈,通过锁紧活塞703将锁紧风缸701分为靠近机械对接体4对接面所在平面的锁紧风缸前腔室704和远离机械对接体4对接面所在平面的锁紧风缸后腔室705,所述锁紧风缸前腔室704设置有与列车软管连通的第三通气孔706,锁紧风缸后腔室705设置有第五排气孔707,并在锁紧风缸后腔室705安装有锁紧弹簧708,锁紧弹簧708一端安装在锁紧活塞703上,另一端安装在锁紧风缸后腔室705远离锁紧风缸前腔室704的内部端壁上;所述锁紧活塞703上安装有锁紧活塞杆709,锁紧活塞杆709经过锁紧风缸前腔室704伸出锁紧风缸701,
并在锁紧活塞杆709的杆头安装有锁紧勾710,锁紧勾710能够在车辆直线行径方向的竖直平面上以安装点为圆心做逆时针或顺时针旋转;锁紧风缸701靠近机械对接体4对接面所在平面的一端安装有滑台座711,所述滑台座711上固定安装有二号滑台712,二号滑台712上安装有滚轮713,滚轮713与锁紧勾710靠近地面一端的倾斜部714接触;所述倾斜部714靠近锁紧风缸701的一端到地面的距离小于倾斜部714远离锁紧风缸701的一端到地面的距离;本装置在初始状态时,由于锁紧弹簧708弹簧力的作用使得锁紧勾710处于伸出的极限状态,当需要将锁紧勾710挂于锁紧销702上时,通过第三通气孔706向锁紧风缸前腔室704中注入压力空气,从而锁紧活塞703压缩锁紧弹簧708并带动锁紧活塞杆709回缩,进而使得锁紧勾710在回缩的同时做顺时针旋转,从而挂于对接车辆机械对接体4的锁紧销702上;当需要将锁紧勾710从锁紧销702上取下时,通过第三通气孔706排气,从而锁紧活塞703由于锁紧弹簧708弹簧力的作用带动锁紧活塞杆709伸出,进而带动锁紧勾710向前移动的同时做逆时针旋转,从而实现了脱钩。
[0084]
所述倾斜部714上设置有沿倾斜部714长度方向的二号滑槽715,所述滚轮713在所述二号滑槽715内部滚动,从而有效避免了滚轮713脱离倾斜部714。
[0085]
所述锁紧勾710的勾部716到倾斜部714之间安装有挂环717,滑台座711远离锁紧风缸701的一端也安装有挂环717,两个挂环717之间安装有弹簧,通过弹簧力的作用使得滚轮713紧贴在二号滑槽715内,进一步的避免了滚轮713脱离倾斜部714。
[0086]
所述滑台座711上设置有条形滑槽718,二号滑台712固定安装在条形滑槽718上,在安装时可通过调节二号滑台712在条形滑槽718上的安装位置,来达到使锁紧勾710的勾部716内表面能够与锁紧销702配合的目的。
[0087]
所述第三通气孔706与所述机械对接体4检测仓405中设置的第一通气孔410通过一号风管719连接,并在所述一号风管719上安装一个出气口与外界连通的二号三通电磁阀720,检测仓405第二通气孔411通过二号风管721与列车软管连接,二号风管721为软管;所述锁紧风缸701中设置有第四通气孔722,且所述第四通气孔722在锁紧风缸701中的设置位置参照锁紧勾710挂在锁紧销702上后,第四通气孔722能够和第三通气孔706相通进行设定,所述第四通气孔722与内风缸608的第二气压通道614通过三号风管723相连通,从而列车软管中的压力空气先经过检测仓405,再经过锁紧风缸701,最后到达伸缩装置6的内风缸608中;由上可知,两个车辆风电自动对接的过程是,首先机械对接体4对接,且第一凸起部401插入检测仓405中的位置符合要求后,前车及后车的第一通气孔410和第二通气孔411分别连通,前车列车管中的压力空气经过列车软管、二号风管721、第二通气孔411、第一通气孔410、一号风管719和第三通气孔706进入到锁紧风缸前腔室704中,通过空气压力推动锁紧活塞703压缩弹簧,从而前车的锁紧勾710勾在后车锁紧销702上,同时锁紧风缸701中的第三通气孔706和第四通气孔722实现导通,压力空气经过第四通气孔722、三号风管723和第二气压通道614进入内风缸后腔室611中,通过压力空气推动内活塞609挤压弹簧,并将与内活塞杆612第二连接板613连接的风电对接体5推出,与后车的风电对接体5对接,从而实现了与后车的通电和通风,压力空气就进入了后车列车管中,后车的锁紧勾710再与前车锁紧销702配合。其后部连挂车辆参照上述过程依次连接即可,并且本发明在分离风电自动对接装置时,先控制二号三通电磁阀720切断第三通气孔706与所述机械对接体4检测仓405的风路通道,并且将第三通气孔706与外界形成连通,从而先排出锁紧风缸前腔室704中的压
力空气,通过弹簧力的作用使锁紧勾710向前伸出的同时向上旋转,从而实现脱钩。
[0088]
所述第一气压通道607通过四号风管618连接列车软管,第三气压通道617通过五号风管619连接列车软管,四号风管618在靠近第一气压通道607的一端安装有一号超压快速排风阀620,从而使得列车行驶过程中,车辆之间发生纵向冲击导致外风缸后腔室604压力瞬时增大时,通过一号超压快速排风阀620快速排出超压空气避免外风缸后腔室604压力增大造成装置损坏。
[0089]
所述三号风管723上安装有二号超压快速排风阀724,使得在车辆行驶过程中,车辆间发生纵向冲击导致内风缸后腔室611压力瞬间增大时,通过二号超压快速排风阀724将内风缸后腔室611中的超压空气快速排出,避免内部压力过大造成装置损坏。
[0090]
所述四号风管618从一号超压快速排风阀620到与列车软管的连接处依次安装有一个开口与外界相通的一号三通电磁阀622和调节风路压力的调压阀621,所述二号风管721连接在四号风管618上从而与列车软管相连,且二号风管721连接于一号三通电磁阀622和一号超压快速排风阀620之间,从而可通过调压阀621调节二号风管721和四号风管618内部的空气压力,进而达到调节外风缸后腔室604的压力和锁紧风缸前腔室704的空气压力。
[0091]
所述五号风管619上安装有两通电磁阀623、压力传感器624和一个开口与外界相通的三号三通电磁阀625。从而使得车辆在驼峰溜放作业时,通过两通电磁阀623事先切断列车管与五号风管619的风路,使得列车管内的压力空气在风电对接体5分离时无法排出,确保车辆顺利进行驼峰溜放作业;在列车行驶过程中,火车头司机发现无法排除后部车辆列车管压力空气,车辆刹车速度慢或无法刹车时,可通过控制端控制三号三通电磁阀625使列车管与外界连通,从而快速排放后部车辆列车管内部的压力空气,进而使闸瓦迅速压上车轮进行紧急停车;火车头司机或地面控制中心可通过压力传感器624经信号发送装置发出的电信号,随时监测所连挂车辆列车管压力状况,以便判断各车辆风电自动对接及分离装置的工作状态、所连挂车辆列车管的充风状态、减压状态及整个列车车辆的列车管贯通状态;并且可通过该压力传感器624的压力变化判断两个机械对接体4的对接面是否完全贴合。
[0092]
所述伸缩装置6远离机械对接体4的一端设置有销孔626,回转中心销627穿过该销孔626并将回转中心销627的两端安装在箱体3底板302和顶板301的条形槽304中,并在回转中心销627与销孔626的接触面上安装有球面关节轴承或橡胶轴承,所述条形槽304贯穿箱体3底板302和顶板301,回转中心销627的两端分别穿过底板302和顶板301上的条形槽304伸出箱体3外部,所述回转中心销627伸出顶板301的一端设置有环状凸缘310,防止了回转中心销627从条形槽304内掉落至地面,并且在箱体3顶板301外部且沿条形槽304的长度方向上并排设置有多组限位板311,属于同一组的两个限位板311分别位于条形槽304的两侧,并在属于同一组的两个限位板311之间安装销轴312,从而有效的防止了回转中心销627向远离地面的一端移动,在所述底板302和顶板301的内壁上均分别设置有两组弹簧插板305,顶板301和底板302上的两组弹簧插板305之间均安装有板弹簧306,底板302和顶板301上的两组板弹簧306的中部均固定在所述回转中心销627上,使得在行车过程中两个车辆发生冲击时,外风缸601带动回转中心销627后移或前移,翼柱628在支撑柱307顶部上前后滑动,同时带动回转中心销627再带动上下板弹簧306移动,使板弹簧306发生形变,将冲击动能变成弹性势能,在此过程中板弹簧306起到缓冲作用。并且在车辆过弯时,伸缩装置6、机械对接
体4以及风电对接体5能够围绕回转中心销627左右摇摆。在车辆通过竖曲线时,伸缩装置6、机械对接体4以及风电对接体5能够围绕回转中心销627上下摇摆。
[0093]
所述回转中心销627上安装有两个卡环631,两个卡环631分别位于伸缩装置6销孔626的上下方,并且两个卡环631与销孔626的开口均保留有间距,从而通过卡环631限制了伸缩装置6在回转中心销627轴向上的位移量。
[0094]
所述箱体3的底板302上安装有两个支撑柱307,两个支撑柱307分别位于外风缸601的两侧,并且支撑柱307远离底板302的一端与外风缸601两侧设置的翼柱628接触,所述翼柱628分别向箱体3的两个侧板303延伸并且向远离地面的一端倾斜,所述支撑柱307为伸缩杆,并在两个杆身之间安装弹簧,且支撑柱307靠近翼柱628的一端设置有安装盒308,安装盒308内安装有滚轴309,使得整个装置在发生左右偏转时,翼柱628能够在滚轴309上滑动,在非对接状态下由于外风缸601自身重量的作用能够使伸缩装置6自动对中,进而带动前部的机械对接体4和风电对接体5自动对中。
[0095]
当然本发明也可以采用弹簧吊装的方式替代上述支撑柱307,只需将弹簧一端安装在翼柱628远离外风缸601的一端,弹簧另一端安装在顶板301上。
[0096]
所述支撑柱307和安装盒308之间设置有调整垫,在安装时,通过加减调整垫可以方便的调整机械对接体4的水平度,防止其倾斜、低头或仰头。在对接车辆通过竖曲线时,伸缩装置6前端带动翼柱628通过滚轴309下压或释放弹簧,后端绕回转中心销627上下摇摆,实现机械对接体4及风电对接体5的上下摇摆。在对接车辆通过水平曲线时,伸缩装置6前端带动翼柱628在滚轴309上左右摇摆,后端绕回转中心销627同步左右摇摆,实现机械对接体4及风电对接体5的左右摇摆;非对接状况下,依靠伸缩装置6、机械对接体4及风电对接体5自重,翼柱628自动沿滚轴309下滑,带动伸缩装置6滑落并保持在距地面最低点,实现伸缩装置6、机械对接体4及风电对接体5纵向中心线与箱体3纵向中心线重合,自动对中,奠定了与对方车辆对接基础。
[0097]
所述箱体3的两个侧板303上分别开设有通孔,五号风管619和四号风管618分别穿过所属侧的通孔与列车软管连接后与列车管连接,五号风管619所属侧的通孔内壁到五号风管619外壁之间的距离大于五号风管619的位移距离,四号风管618所属侧的通孔内壁到四号风管618外壁之间的距离大于四号风管618的位移距离,从而使得车辆在行驶过程中,机械对接体4和风电对接体5带动伸缩装置6前后移动和左右偏摆时,能够为五号风管619和四号风管618保留足够的位移距离。
[0098]
所述箱体3通过工字钢状的吊座2安装在牵引梁1车钩缓冲器下方。
[0099]
所述第一凸起部401包括圆柱体定位部和圆锥体导向部,圆锥体最大圆平面与圆柱体的圆平面全等,从而使得在第一凸起部401插入第一凹陷部402时,圆锥体的斜面能够提供导向作用,使第一凸起部401能够顺利的插入到第一凹陷部402中。
[0100]
所述第一凹陷部402包括一圆柱状的凹陷区和一圆台状的凹陷区,圆台状凹陷区最大的一个圆周平面与圆柱状凹陷区的圆周平面紧邻并全等,且所述圆柱状凹陷区位于第一凹陷部402的开口处,圆台状凹陷区位于第一凹陷部402的内部,且所述圆柱状凹陷区的内径略大于第一凸起部401的圆柱体定位部的外径,其第一凸起部401的圆锥体导向部的锥度略小于圆台状凹陷区倾斜面延伸所形成的圆锥体锥度,所述连接孔404的直径等于第一凹陷区圆台状凹陷区的最小直径;从而使得第一凸起部401能够插入第一凹陷部402中,且
圆锥体导向部能够插入所述连接孔404内。从而使得当第一凸起部401相对于第一凹陷402部错位时,可通过导向部斜面起到导向对位作用,进而使第一凸起部401能够顺利地插入第一凹陷部402内。插入后可通过圆柱体第一凸起部401与圆柱状凹陷区的配合实现对第一凸起部401与第一凹陷部402的相互径向定位,防止第一凸起部401相对第一凹陷部402径向滑移。
[0101]
所述第二凸起部522包括圆柱体定位部和圆锥体导向部,第二凹陷部523包括设置在第二凹陷部523靠近开口端的圆柱状凹陷区和远离开口端的圆锥状凹陷区,所述第二凸起部522的圆柱体定位部直径略小于圆柱状凹陷区的直径,圆锥体导向部的最大圆平面直径略小于圆锥状凹陷区的最大圆平面直径,且圆锥体导向部的锥度略小于圆锥状凹陷区的锥度。使得第二凸起部522能够顺利插入到第二凹陷部523中,并且能够通过导向部进行导向对位,再通过第二凹陷部523的圆柱形凹陷区实现定位。
[0102]
通过本发明风电自动对接的对接步骤做详细说明,以便本领域技术人员能够充分理解本发明的技术方案,具体步骤如下:
[0103]
步骤1.首先火车头与火车头后方的车辆进行对接,与火车头列车软管连接的四号风管618上的一号三通电磁阀622得电,导通列车软管到外风缸后腔室604的风路,压力空气经过四号风管618进入到外风缸后腔室604,从而使得作为外活塞杆的内风缸608体伸出,推动机械对接体4向火车头后部车辆的方向移动,直至火车头后部的机械对接体4与车辆前部的机械对接体4相对接,火车头后部的第一凸起部401完全插入车辆前部的第一凹陷部402,车辆前部的第一凸起部401完全插入火车头后部的第一凹陷部402,完成定位。
[0104]
步骤2.定位完成后,火车头上的机械对接体4检测仓405的第一通气孔410和第二通气孔411导通,处于失电状态的二号三通电磁阀720接通第一通气孔410到第三通气孔706的风路,连通检测仓405到锁紧风缸701的风路,火车头列车管的压力空气经过列车软管、四号风管618、二号风管721、检测仓405、第二通气孔411、第一通气孔410、一号风管719、第三通气孔706、再进入锁紧风缸前腔室704中,从而通过压力空气推动锁紧活塞703压缩锁紧弹簧708,使得锁紧勾710向下转动的同时回缩,并挂在锁紧销702上,完成对后部车辆机械对接体4的锁紧工作。
[0105]
步骤3.当火车头机械对接体4完成对后部车辆机械对接体4锁紧工作后,火车头机械对接体4上安装的锁紧风缸701上设置的第三通气孔706和第四通气孔722导通,进入锁紧风缸701中的压力空气经过第四通气孔722进入到三号风管723中,并从三号风管723中进入到第二气压通道614,再从第二气压通道614经外活塞602进入到内风缸后腔室611中,从而通过压力空气推动内活塞609压缩弹簧,使得内活塞杆612伸出推动风电对接体5向后部车辆的方向移动,并且通过两个风电对接体5上的触碰板510和滑杆511接触,从而使得防尘盖507开启,防尘盖507开启后,火车头上的风电对接体5继续移动,直至火车头上的风电对接体5的正电极501、负电极502、标准密封圈505及密封条506与后部车辆相互接触,并抵压正电极501、负电极502、阀杆524向后移动,密封条506压缩。阀杆524向各自的后部腔室527方向上移动后,使得环形凸起部528及密封圈与后部腔室527端壁分离,实现了火车头和后部车辆各自风电对接体5的后部腔室527和中部腔室526的导通。
[0106]
步骤4.火车头和后部车辆各自风电对接体5的后部腔室527和中部腔室526导通后,火车头列车管中的压力空气首先依次经过火车头的列车管和列车软管进入到五号风管
619、第三气压通道617、芯杆616、内活塞杆612中空部、第八通气孔629、后部腔室527、中部腔室526、中腔通气孔539、阀杆524进入到后部车辆的阀杆524、中腔通风孔539、中部腔室526、后部腔室527、第八通气孔629、内活塞杆612中空部、芯杆616、第三气压通道617、五号风管619后进入后部车辆的列车软管中,再进入到后部车辆的列车管中,同时,一部分压力空气经前腔通气孔538、前部腔室525、第七通气孔537、外风管535、第六通气孔536进入延时风缸后腔室533;另一部分经后部腔室527、第五通气孔534进入延时风缸前腔室532。直到延时风缸活塞533前后压力与列车管压力相等。
[0107]
步骤5.当后部车辆列车管进风后,与步骤2风路走向相同,区别在于将步骤2中的火车头更换为车辆即可,使得后部车辆的锁紧勾710与火车头锁紧销702配合并锁紧。
[0108]
步骤6.其他后续车辆按照上述步骤中的风路顺序依次进行对接即可。
[0109]
两车辆风电自动对接和分离装置的分离步骤如下:
[0110]
步骤1:控制二号三通电磁阀720得电切断第一通气孔410到锁紧风缸701的通路,同时连通锁紧风缸前腔室704到外界的风路,使得锁紧风缸前腔室704的压力空气排向大气,锁紧活塞703被弹簧推动,使锁紧活塞杆709伸出,锁紧勾710向上旋转的同时向前移动,完成脱钩,并且由于锁紧活塞杆709伸出,开通了第四通气孔722到第五排气孔707的通路,排出内风缸后腔室611的压力空气,弹簧推动内活塞609移动,带动内活塞杆612回缩,从而使得两个相互对接的风电对接体5分别实现回缩分离。
[0111]
步骤2.两风电对接体5分离完成后,再控制一号三通电磁阀622失电,切断调压阀621至四号风管618及二号风管721的供风通路,同时连通四号风管618及二号风管721到外界的风路,使外风缸后腔室604的压力空气排出,弹簧推动外活塞602移动,带动作为外活塞杆的内风缸608回缩,从而带动对接的机械对接体4分离,由于延时风缸529的作用,使得列车管中的压力空气通过阀杆524排出,使分离的后部车辆实施原地制动,避免溜车。而与火车头连接的前部分离车辆列车管因有火车头不断向其补风,待阀杆524关闭排风口停止排风后,列车管空气压力及时恢复定压,前部车辆基础制动装置自然缓解一段时间后,二号三通电磁阀720失电连通检测仓405至锁紧风缸701的供风通路,同时切断第三通气孔706经二号三通电磁阀720到外界的风路,为下次对接做好准备。同时,伸缩装置6的翼柱628沿支撑柱滚轴309下滑,使前车、后车机械对接体4和风电对接体5及伸缩装置6中心线与箱体3中心线重合,实现自动对中,也为下次对接做好准备。风电自动对接及分离装置恢复初始状态。
[0112]
由于每个车辆上都安装有蓄电池因此在风电自动对接及分离装置分离的一段时间内,仍然可以通过控制器控制所有的三通电磁阀和两通电磁阀。