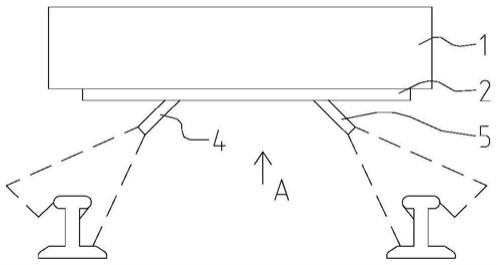
1.本发明属于轨道测距领域,具体的是轨距检测装置及检测方法。
背景技术:2.随着我国轨道交通产业的迅猛发展,国铁、地铁以及城铁等轨道交通系统运营速度提高、建设里程的增加以及线路日趋繁忙,轨道的路线更加复杂。若轨道检测数据不准确,会导致无法预估轨道质量的问题,严重影响轨道交通,因此,对于轨道的检测显的尤为重要,特别是对轨距的准确测量。
3.轨距检测基于轨距的定义,是对轨道的统一横截面,钢轨面以下16mm处两根钢轨之间的最小内侧距离相对于规定的轨距值1435mm的偏差。
4.目前,轨距检测的方法为:在车底安装轨检梁,轨检梁上的两个2d激光传感器会采用激光三角测距原理,利用2d激光轮廓传感器对轨面和内轨腰、轨底进行扫描,测得铁轨到轨检梁下方得距离,运用高速图像处理技术对轮廓曲线进行提取和分析,确定轨距的变化,加上两个2d激光轮廓传感器安装的距离,计算合成的轨距值,进而得到轨距变化率。该检测方法,要求检测梁应该与轨道垂直,当检测小车进入曲线轨道时,检测梁也应该与轨道切面垂直,才能实现准确测量。故,该检测方法,在轨道的路况比较平直的情况下,测得的数据较为准确。一旦轨道呈弯曲复杂变化,当检测车辆进入弯曲线路时,轮轴横向力过大导致轮对发生一定程度的偏移,进而导致轨检梁偏移,此时测得的轨距与准确的轨距出现偏差,导致检测系统无法得到准确的数据,也无法对铁轨的状况进行良好的评估。
技术实现要素:5.本发明的目的是解决现有轨距检测在弯曲线路检测时存在偏差的问题,提供一种轨距检测装置及检测方法,修正偏差,提高测量的准确性。
6.本发明采用的技术方案是:轨距检测装置,包括检测小车和设置于检测小车的车体底部的检测梁,在检测梁上设置有2d激光轮廓传感器一和2d激光轮廓传感器二,在检测小车的车体底部还设置有补偿梁,所述补偿梁与检测梁的夹角为γ,1
°
≤γ≤8
°
;在补偿梁上安装有用于扫描两条铁轨中的其中一条铁轨的2d激光轮廓传感器三和扫描另一条铁轨的2d激光轮廓传感器四。
7.进一步的,补偿梁到检测小车的车体底部的距离与检测梁到检测小车的车体底部的距离相等。
8.进一步的,在补偿梁与检测小车的车体底部之间设置有两幅关于补偿梁中心对称的吊装座,所述吊装座顶部与检测小车的车体底部固定连接,底部与补偿梁的顶部固定连接。
9.进一步的,在补偿梁的两端设置有防脱拉杆,所述防脱拉杆一端与检测小车的车体底部铰接,另一端与补偿梁的顶端铰接,且补偿梁的两端防脱拉杆关于补偿梁的两端中心对称设置。
10.轨距检测的方法,步骤一,在检测小车的车体底部加装一道补偿梁,所述补偿梁与检测梁的夹角为γ,1
°
≤γ≤8
°
,并在补偿梁上安装一个2d激光轮廓传感器三和一个2d激光轮廓传感器四;
11.步骤二,加装补偿梁的检测小车驶入轨道,利用检测梁上的2d激光轮廓传感器一和2d激光轮廓传感器二扫描测出测量轨距一,所述测量轨距一为b;利用补偿梁上的2d激光轮廓传感器三和2d激光轮廓传感器四扫描测出测量轨距二,所述测量轨距二为a;
12.步骤三,构建检测三角形abc,
△
abc中,cb=a、ca=b、∠bca=γ、∠cba=β;
13.步骤四,在
△
abc上,以c为顶点,向边ab做垂线,垂足为d;
14.步骤五,计算出cd,cd为实际轨距。
15.进一步的,5
°
≤γ≤8
°
。
16.本发明的有益效果是:本发明,通过补偿梁对检测误差进行纠正,大大降低了在弯曲线路上由于轮轴横向力导致的轨距检测误差,提高了轨距检测的准确性。补偿梁与检测梁结构相同,无需重新设计补偿梁,节约了设计成本。并且只需要在原来的结构上加装一根补偿梁即可,无需拆解原来的结构,保护了检测系统的完整性,降低了制作成本。补偿梁轻便,对车底空间影响小,对车体压力小。
附图说明
17.图1为轨距检测装置示意图;
18.图2为图1的a向视图;
19.图3为检测三角形原理图一;
20.图4为检测三角形原理图二;
21.图5为补偿梁安装结构示意图。
22.图中,检测小车1、检测梁2、补偿梁3、2d激光轮廓传感器一4、2d激光轮廓传感器二5、2d激光轮廓传感器三6、2d激光轮廓传感器四7、吊装座8、防脱拉杆9。
具体实施方式
23.下面结合附图对本发明做进一步的说明如下:
24.轨距检测时,检测梁2应该与轨道垂直,当检测小车1进入曲线轨道时,检测梁2也应该与轨道切面垂直,才能实现准确测量。但是,当检测小车1车轮与轨道发生偏移时,带动检测梁2跟随偏移,导致测量的轨距不准确。为了克服该问题,本发明公开了轨距检测装置,如图1和图2所示,包括检测小车1和设置于检测小车1的车体底部的检测梁2,在检测梁2上设置有2d激光轮廓传感器一4和2d激光轮廓传感器二5,在检测小车1的车体底部还设置有补偿梁3,所述补偿梁3与检测梁2的夹角为γ,1
°
≤γ≤8
°
;在补偿梁3上安装有用于扫描两条铁轨中的其中一条铁轨的2d激光轮廓传感器三6和扫描另一条铁轨的2d激光轮廓传感器四7。
25.与检测梁2相同,如图5所示,补偿梁3通过两幅吊装座8吊装于检测小车1的车体底部,且两幅吊装座8关于补偿梁3中心对称布置。所述吊装座8顶部与检测小车1的车体底部固定连接,底部与补偿梁3的顶部固定连接。为了起到二次防脱作用,保证补偿梁3安装的牢固可靠性,提高安全性能,在补偿梁3的两端设置有防脱拉杆9,所述防脱拉杆9一端与检测
小车1的车体底部铰接,另一端与补偿梁3的顶端铰接,且补偿梁3的两端防脱拉杆9关于补偿梁3的两端中心对称设置。
26.通过检测梁2上的2d激光轮廓传感器一4扫描轨道上的其中一条铁轨的轮廓,2d激光轮廓传感器二5扫描另一条铁轨的轮廓,获取通过检测梁2测量的测量轨距一。通过加装一根补偿梁3,通过该补偿梁3上的2d激光轮廓传感器三6扫描轨道上的其中一条铁轨的轮廓,2d激光轮廓传感器四7扫描另一条铁轨的轮廓,获取通过补偿梁3测量的测量轨距二。然后,通过测量轨距一和测量轨距二,构建检测三角形,计算出实际轨距。从而起到修正检测梁2检测误差的作用。由于该装置,仅需要在原有的轨距检测小车1上加转一根与检测梁2结构相同的补偿梁3即可,其结构简单、制作容易,并且对原有检测小车1及检测系统结构的影响较小。
27.采用上述轨距检测装置进行轨距检测的方法,具体操作为:首先,利用检测梁2上的2d激光轮廓传感器一4和2d激光轮廓传感器二5扫描测出测量轨距一,所述测量轨距一为b;利用补偿梁3上的2d激光轮廓传感器三6和2d激光轮廓传感器四7扫描测出测量轨距二,所述测量轨距二为a;接着,构建检测三角形abc,且三角形的边长cb=a、ca=b、∠bca=γ、∠cba=β、∠cab=а;然后,在
△
abc上,以c为顶点,向边ab做垂线,垂足为d;最后,计算出cd,cd为实际轨距。构建出的
△
abc可以为如图3所示的钝角三角形,也可以为如图4所示的锐角三角形。
28.计算时,首先计算出
△
abc的∠cba:
[0029][0030]
然后,根据正弦定理计算出cd。
[0031]
该检测方法,通过补偿梁3对检测误差进行纠正,大大降低了在弯曲线路上由于轮轴横向力导致的轨距检测误差,提高了轨距检测的准确性。补偿梁3与检测梁2结构相同,无需重新设计补偿梁3,节约了设计成本。并且只需要在原来的结构上加装一根补偿梁3即可,无需拆解原来的结构,保护了检测系统的完整性,降低了制作成本。补偿梁3轻便,对车底空间影响小,对车体压力小。通过实际应用发现,1
°
≤γ≤8
°
时,弯轨触轨距检测的误差得到有效纠正。其中,当5
°
≤γ≤8
°
时,弯轨触轨距检测的误差最小,精度更高。
[0032]
利用该轨距检测装置及检测方法对某一轨道进行测量的结果如下:
[0033]
公里标(公里)γ(
°
)实测轨距b(mm)实测轨距a(mm)矫正轨距(mm)164.65651436.1861438.1861435.634164.8951436.0751438.0751435.523165.12361436.0481438.0481434.951165.35761436.0751438.0751434.978165.5971436.0481438.0481434.275165.82471436.0271438.0271434.254166.05781435.8561438.8561433.694166.29181435.5681438.5681433.406