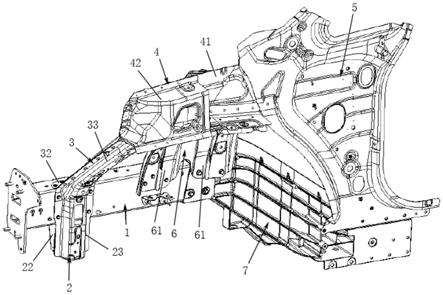
[0001]
本发明属于车辆技术领域,特别是涉及上部边梁传力结构。
背景技术:[0002]
目前铝制机舱纵梁结构车型,副车架一般直接布置于机舱纵梁上以保证刚度和强度,然而由于副车架安装点较铝挤压机舱纵梁的z向高差较大,一种方案加大机舱纵梁的z向尺寸去匹配副车架安装点,但机舱纵梁中部又需避让电机输出轴包络等布置,导致整个机舱纵梁不够流畅且重量偏大,另一种方案通过加高副车架的z向悬臂,导致副车架重量偏大;机舱纵梁与a柱的传递路径只有塔座一条通道,副车架安装点到上边梁总成无传力腔,导致碰撞传递路径以机舱纵梁为主通道,分散路径少,从而需将机舱纵梁的前端吸能空间设计得足够大以保证碰撞安全,不利于紧凑型机舱布局要求。
技术实现要素:[0003]
本发明所要解决的技术问题之一是:针对现有方案上部边梁传力结构碰撞性能不佳的问题,提供一种上部边梁传力结构。
[0004]
为解决上述技术问题,本发明实施例提供了一种上部边梁传力结构,包括机舱纵梁、塔座、副车架安装板总成、上边梁斜撑板总成、上边梁总成和a柱内板;
[0005]
所述机舱纵梁内设有前后贯通的第一传力腔;
[0006]
所述副车架安装板总成内设有上端开口的第二传力腔,所述副车架安装板总成的上端位于所述机舱纵梁的前端的底部,并与所述机舱纵梁连接;
[0007]
所述上边梁斜撑板总成内设有第三传力腔;所述上边梁斜撑板总成的下端连接所述机舱纵梁的前端和所述副车架安装板总成,上端连接所述上边梁总成;所述第三传力腔的下端连通所述第二传力腔,上端贯通至所述上边梁总成的前端;
[0008]
所述塔座的上端连接所述上边梁总成,下端连接所述机舱纵梁;
[0009]
所述上边梁总成的后端连接所述a柱内板。
[0010]
可选地,所述上边梁总成内设有第四传力腔,所述第四传力腔的前端与所述第三传力腔连通,所述塔座上设有第五传力腔,所述第五传力腔的下端贯通至所述机舱纵梁,上端贯通至所述上边梁总成。
[0011]
可选地,所述副车架安装板总成包括内侧安装板和连接于所述内侧安装板的外侧安装板,所述内侧安装板与所述外侧安装板围合形成所述第二传力腔,所述内侧安装板连接所述机舱纵梁的内侧,所述外侧安装板连接所述机舱纵梁的外侧,所述内侧安装板和所述外侧安装板中的至少一种还连接所述机舱纵梁的底侧。
[0012]
可选地,所述内侧安装板包括第一底板以及分别连接于所述第一底板上的内侧板、第一前侧板和第一后侧板;
[0013]
所述外侧安装板包括第二底板以及分别连接于所述第二底板上的外侧板、第二前侧板和第二后侧板;
[0014]
所述内侧板与所述外侧板相对,所述第一前侧板和所述第二前侧板连接,所述第一后侧板和所述第二后侧板连接,所述第一底板与所述第二底板叠设;
[0015]
所述内侧板的上端与所述机舱纵梁的内侧连接,所述第一前侧板的上端和所述第一后侧板的上端均与所述机舱纵梁的底侧连接,所述第二前侧板的上端和所述第二后侧板的上端均与所述机舱纵梁的外侧连接。
[0016]
可选地,所述第一前侧板的上端和所述第一后侧板的上端均弯折形成有第一翻边,所述第一前侧板的远离所述内侧板的一侧和所述第一后侧板的远离所述内侧板的一侧均弯折形成有第二翻边;
[0017]
所述第二前侧板的远离所述外侧板的一侧和所述第二后侧板的远离所述外侧板的一侧弯折形成第三翻边;
[0018]
所述第一前侧板的所述第二翻边和所述第二前侧板的所述第三翻边连接,所述第一后侧板的所述第二翻边和所述第二后侧板的所述第三翻边连接,所述第一底板与所述第二底板叠设;
[0019]
所述内侧板的上端与所述机舱纵梁的内侧连接,所述第一翻边与所述机舱纵梁的底侧连接,所述第三翻边的上端与所述机舱纵梁的外侧连接。
[0020]
可选地,所述副车架安装板总成还包括中间立板和用于连接副车架的螺纹管;
[0021]
所述中间立板连接于所述内侧安装板与所述外侧安装板之间,所述螺纹管设于所述第二传力腔内,并连接于所述中间立板。
[0022]
可选地,所述副车架安装板总成还包括中间立板和用于连接副车架的螺纹管,所述中间立板包括第三底板和立板;
[0023]
所述第三底板叠设于所述第一底板和所述第二底板中的位于上侧的一种上;
[0024]
所述立板的内侧连接所述第一前侧板和所述第一后侧板上的第二翻边,所述立板的外侧连接所述第二前侧板和所述第二后侧板上的第三翻边;
[0025]
所述螺纹管的侧部连接于所述中间立板,所述螺纹管的底部连接于所述第一底板和所述第二底板中的位于上侧的一种上。
[0026]
可选地,所述上边梁斜撑板总成包括斜撑内板和连接于所述斜撑内板的斜撑外板,所述斜撑内板与所述斜撑外板围合形成所述第三传力腔;
[0027]
所述斜撑内板的上端连接所述上边梁总成的内侧,下端连接所述机舱纵梁的顶部;
[0028]
所述斜撑外板的上端连接所述上边梁总成的底侧,下端连接所述机舱纵梁的外侧和所述副车架安装板总成的外侧。
[0029]
可选地,所述斜撑内板包括斜撑上内板和斜撑下内板,所述斜撑上内板和所述斜撑下内板分别与所述斜撑外板连接,所述斜撑上内板的下端与所述斜撑下内板的下端搭接。
[0030]
可选地,所述上边梁总成包括上边梁内侧板和连接于所述上边梁内侧板的上边梁外侧板,所述上边梁内侧板与所述上边梁外侧板围合形成第四传力腔;
[0031]
所述上边梁内侧板的前端的内侧连接所述斜撑内板,所述上边梁内侧板的前端的底侧连接所述斜撑外板,所述上边梁内侧板的后端连接所述a柱内板。
[0032]
可选地,所述塔座的上端连接所述上边梁内侧板的内侧,下端连接所述机舱纵梁
的外侧,所述塔座上设有第五传力腔,所述第五传力腔自所述机舱纵梁延伸至所述上边梁内侧板;
[0033]
所述机舱纵梁、所述上边梁斜撑板总成和所述塔座为铝制结构,所述副车架安装板总成、所述上边梁总成和所述a柱内板为钢制结构。
[0034]
本发明实施例提供的前纵梁结构,通过副车架安装板总成连接副车架,无需增大机舱纵梁的z向尺寸或增大副车架的悬臂高度以匹配机舱纵梁与副车架之间的安装点,有利于缩减机舱纵梁的z向尺寸,使机舱纵梁能避开电机输出轴包络等布置,避免因机舱纵梁不够流畅而影响传力,有利于碰撞吸能,提升碰撞安全,有利于轻量化;
[0035]
除机舱纵梁和塔座传力外,还增加了副车架安装点到上边梁总成的传力路径,机舱纵梁与副车架安装板总成和上边梁斜撑板总成交叉,第一传力腔前后贯通机舱纵梁,第三传力腔向下贯通至机舱纵梁同时连通第二传力腔,向上贯通至上边梁总成,从而形成交叉的传力路径,有效将机舱纵梁受到的正碰力向上传递至上a柱区域,再分散到上a柱、侧门和门槛,向下传递至副车架,有效将副车架受力分散至机舱纵梁和a柱区域,提升副车架安装点的刚度和强度,提升碰撞安全性能,缩减前端碰撞吸能空间,有利于紧凑型机舱布置,适用于机舱布置紧凑的车型,特别是短前悬的电动车。
附图说明
[0036]
图1是本发明提供的一种上部边梁传力结构的结构示意图;
[0037]
图2是图1所示的上部边梁传力结构在正碰时的外侧传力路径图;
[0038]
图3是图1所示的上部边梁传力结构在正碰时的内侧传力路径图;
[0039]
图4是图1所示的上部边梁传力结构在副车架受碰时的传力路径图;
[0040]
图5是图1所示的上部边梁传力结构的局部结构图一;
[0041]
图6是图1所示的上部边梁传力结构的局部结构图二;
[0042]
图7是图1所示的上部边梁传力结构的局部结构分解图;
[0043]
图8是图7所示副车架安装板总成在另一视角的结构示意图;
[0044]
图9是图7所示副车架安装板总成的分解图;
[0045]
图10是图7所示上边梁斜撑板总成的分解图;
[0046]
图11是图7所示上边梁总成的分解图。
[0047]
说明书中的附图标记如下:
[0048]
1、机舱纵梁;11、第一传力腔;
[0049]
2、副车架安装板总成;21、第二传力腔;
[0050]
22、内侧安装板;221、第一底板;222、内侧板;223、第一前侧板;224、第一后侧板;225、第一翻边;226、第二翻边;
[0051]
23、外侧安装板;231、第二底板;232、外侧板;233、第二前侧板;234、第二后侧板;235、第三翻边;
[0052]
24、中间立板;241、第三底板;242、立板;
[0053]
25、螺纹管;
[0054]
3、上边梁斜撑板总成;31、第三传力腔;32、斜撑内板;321、斜撑上内板;3211、第四翻边;322、斜撑下内板;3221、第五翻边;33、斜撑外板;331、第六翻边;
[0055]
4、上边梁总成;41、上边梁内侧板;42、上边梁外侧板;
[0056]
5、a柱内板;
[0057]
6、塔座;61、第五传力腔;
[0058]
7、机舱纵梁后部接头。
具体实施方式
[0059]
为了使本发明所解决的技术问题、技术方案及有益效果更加清楚明白,以下结合附图及实施例,对本发明进行进一步的详细说明。应当理解,此处所描述的具体实施例仅用以解释本发明,并不用于限定本发明。
[0060]
如图1、图5、图6和图7所示,本发明实施例提供的一种上部边梁传力结构,包括机舱纵梁1、副车架安装板总成2、上边梁斜撑板总成3、上边梁总成4和a柱内板5;
[0061]
机舱纵梁1内设有前后贯通的第一传力腔11;
[0062]
副车架安装板总成2内设有上端开口的第二传力腔21,副车架安装板总成2的上端位于机舱纵梁1的前端的底部,并与机舱纵梁1连接;
[0063]
上边梁斜撑板总成3内设有第三传力腔31;上边梁斜撑板总成3的下端连接机舱纵梁1的前端和副车架安装板总成2,上端连接上边梁总成4;第三传力腔31的下端连通第二传力腔21,上端贯通至上边梁总成4的前端;
[0064]
上边梁总成4的后端连接a柱内板5。
[0065]
使用时,副车架连接于副车架安装板总成2的底部,机舱纵梁1的后端通过机舱纵梁后部接头7连接门槛。
[0066]
如图2和图3所示,机舱纵梁1受正碰时,机舱纵梁1受到的碰撞力一部分沿机舱纵梁1向后传递,一部分沿副车架安装板总成2向下传递至副车架,一部分向上传递至上边梁斜撑板总成3;传递到上边梁斜撑板总成3上的碰撞力斜向上传递至上边梁总成4,沿机舱纵梁1向后传递的碰撞力一部分向后传递至门槛,另一部分经塔座6向上传递至上边梁总成4;传递到上边梁总成4上的碰撞力再传至a柱内板5,并经a柱内板5分散向上a立柱、侧门系统和门槛。
[0067]
如图4所示,副车架受碰时,副车架受到的碰撞力通过副车架安装板总成2传递到机舱纵梁1和上边梁斜撑板总成3;传递到上边梁斜撑板总成3上的碰撞力斜向上传递至上边梁总成4,传递到机舱纵梁1上的碰撞力向前和向后分散,向后分散的碰撞力一部分向后传递至门槛,另一部分经塔座6向上传递至上边梁总成4;传递到上边梁总成4上的碰撞力再传至a柱内板5,并经a柱内板5分散向上a柱、侧门系统和门槛。
[0068]
本发明实施例提供的上部边梁传力结构,通过副车架安装板总成2连接副车架,无需增大机舱纵梁1的z向尺寸或增大副车架的悬臂高度以匹配机舱纵梁1与副车架之间的安装点,有利于缩减机舱纵梁1的z向尺寸,使机舱纵梁1能避开电机输出轴包络等布置,避免因机舱纵梁1不够流畅而影响传力,有利于碰撞吸能,提升碰撞安全,有利于轻量化;
[0069]
除机舱纵梁1和塔座6传力外,还增加了副车架安装点到上边梁总成4的传力路径,机舱纵梁1与副车架安装板总成2和上边梁斜撑板总成3交叉,第一传力腔11前后贯通机舱纵梁1,第三传力腔31向下贯通至机舱纵梁1同时连通第二传力腔21,向上贯通至上边梁总成4,从而形成交叉的传力路径,有效将机舱纵梁1受到的正碰力向上传递至上a柱区域,再
分散到上a柱、侧门和门槛,向下传递至副车架,有效将副车架受力分散至机舱纵梁1和a柱区域,提升副车架安装点的刚度和强度,提升碰撞安全性能,缩减前端碰撞吸能空间,有利于紧凑型机舱布置,适用于机舱布置紧凑的车型,特别是短前悬的电动车。
[0070]
优选地,机舱纵梁1的横截面呈日字形或目字形(如图7所示),以增加机舱纵梁1的承载性能,具体可根据相应车型对机舱纵梁1的性能要求进行选择。
[0071]
在一实施例中,如图1、图3、图6、图7和图11所示,上边梁总成4内设有第四传力腔,第四传力腔的前端与第三传力腔31连通,塔座6上设有第五传力腔61,第五传力腔61的下端贯通至机舱纵梁1,上端贯通至上边梁总成4,增加传力路径,有效将机舱纵梁1和副车架受碰时的力经塔座6和上边梁斜撑板总成3分散传递到上边梁总成4,再经上边梁总成4传递至a柱内板5,有利于碰撞吸能,提升碰撞安全性能。
[0072]
在一实施例中,如图5、图7、图8和图9所示,副车架安装板总成2包括内侧安装板22和连接于内侧安装板22的外侧安装板23,内侧安装板22与外侧安装板23围合形成第二传力腔21,内侧安装板22连接机舱纵梁1的内侧,外侧安装板23连接机舱纵梁1的外侧,内侧安装板22和外侧安装板23中的至少一种还连接机舱纵梁1的底侧。
[0073]
对副车架安装板总成2进行分块,便于加工,内侧安装板22与外侧安装板23连接为一体,并分别与机舱纵梁1的内外两侧连接,且还连接机舱纵梁1的底侧,保证了副车架安装板总成2自身的结构稳定性以及与机舱纵梁1连接的可靠性。
[0074]
在一实施例中,如图8和图9所示,副车架安装板总成2还包括中间立板24和用于连接副车架的螺纹管25;
[0075]
中间立板24连接于内侧安装板22与外侧安装板23之间,螺纹管25设于第二传力腔21内,并连接于中间立板24。
[0076]
设置中间立板24和螺纹管25能够匹配副车架的安装需求,保证副车架与副车架安装板总成2之间的连接可靠性。
[0077]
在一实施例中,如图5、图7、图8和图9所示,内侧安装板22包括第一底板221以及分别连接于第一底板221上的内侧板222、第一前侧板223和第一后侧板224;
[0078]
外侧安装板23包括第二底板231以及分别连接于第二底板231上的外侧板232、第二前侧板233和第二后侧板234;
[0079]
内侧板222与外侧板232相对,第一前侧板223和第二前侧板233连接,第一后侧板224和第二后侧板234连接,第一底板221与第二底板231叠设;
[0080]
内侧板222的上端与机舱纵梁1的内侧连接,第一前侧板223的上端和第一后侧板224的上端均与机舱纵梁1的底侧连接,第二前侧板233的上端和第二后侧板234的上端均与机舱纵梁1的外侧连接。
[0081]
结构简单,便于加工和装配,增加内侧安装板22与外侧安装板23之间的连接可靠性,以及内侧安装板22和外侧安装板23与机舱纵梁1连接的可靠性,内侧安装板22的内腔与外侧安装板23的内腔组合形成第二传力腔21,机舱纵梁1盖合内侧安装板22的内腔的上端,外侧安装板23的内腔能够向上导通第三传力腔31,有利于提高碰撞性能,提升副车架刚度和强度。
[0082]
优选地,如图5、图7、图8和图9所示,第一前侧板223的上端和第一后侧板224的上端均弯折形成有第一翻边225,第一前侧板223的远离内侧板222的一侧和第一后侧板224的
远离内侧板222的一侧均弯折形成有第二翻边226;
[0083]
第二前侧板233的远离外侧板232的一侧和第二后侧板234的远离外侧板232的一侧弯折形成第三翻边235;
[0084]
第一前侧板223的第二翻边226和第二前侧板233的第三翻边235连接,第一后侧板224的第二翻边226和第二后侧板234的第三翻边235连接,第一底板221与第二底板231叠设;
[0085]
内侧板222的上端与机舱纵梁1的内侧连接,第一翻边225与机舱纵梁1的底侧连接,第三翻边235的上端与机舱纵梁1的外侧连接。设置第一翻边225、第二翻边226和第三翻边235,更于相应结构的连接,同时增大连接面积,有利于增加连接可靠性,可适当降低相应板材的厚度,有利于减重降本。
[0086]
在一实施例中,如图8和图9所示,中间立板24包括第三底板241和立板242;第三底板241叠设于第一底板221和第二底板231中的位于上侧的一种上,即第一底板221在上时,第三底板241叠设于第一底板221,第二底板231在上时,第三底板241叠设于第二底板231;
[0087]
立板242的内侧连接第一前侧板223和第一后侧板224上的第二翻边226,立板242的外侧连接第二前侧板233和第二后侧板234上的第三翻边235,螺纹管25的侧部连接于中间立板24,螺纹管25的底部连接于第一底板221和第二底板231中的位于上侧的一种上。
[0088]
如此,能够增加中间立板24与内侧安装板22和外侧安装板23的连接可靠性,同时增加螺纹管25与第一底板221或第二底板231的连接可靠性,从而保证副车架安装板总成2连接副连架的可靠性。
[0089]
优选地,如图8和图9所示,第二底板231、第一底板221和第三底板241依次叠设、贴合且连接,有利于增加副车架安装板总成2的底部的强度。
[0090]
在一实施例中,如图1、图5、图6和图7所示,上边梁斜撑板总成3包括斜撑内板32和连接于斜撑内板32的斜撑外板33,斜撑内板32与斜撑外板33围合形成第三传力腔31;
[0091]
斜撑内板32的上端连接上边梁总成4的内侧,下端连接机舱纵梁1的顶部;
[0092]
斜撑外板33的上端连接上边梁总成4的底侧,下端连接机舱纵梁1的外侧和副车架安装板总成2的外侧。
[0093]
结构简单,连接可靠,使得上边梁总成4封闭第三传力腔31的上端,机舱纵梁1和副车架安装板总成2封闭第三传力腔31的下端,第二传力腔21和第三传力腔31连接成封闭的腔体,有利于碰撞吸能,提升碰撞安全性。
[0094]
具体地,设有外侧安装板23时,斜撑外板33的下端连接机舱纵梁1的外侧和外侧安装板23。
[0095]
在一实施例中,如图7所示,斜撑内板32包括斜撑上内板321和斜撑下内板322,斜撑上内板321和斜撑下内板322分别与斜撑外板33连接,斜撑上内板321的下端与斜撑下内板322的下端搭接。斜撑内板32分成两块,便于加工和装配,装配时,斜撑上内板321先与斜撑外板33连接,斜撑下内板322再连接于斜撑上内板321和斜撑外板33。
[0096]
优选地,如图1、图5、图6、图7和图10所示,斜撑上内板321的两侧设有第四翻边3211,斜撑下内板322的两端设有第五翻边3221,斜撑外板33的两侧设有第六翻边331,第四翻边3211和第五翻边3221连接第六翻边331,在斜撑上内板321与斜撑下内板322的搭接处,第四翻边3211、第五翻边3221和第六翻边331连接,有利于增加上边梁斜撑板总成3的结构
稳定性。
[0097]
在一实施例中,如图1、图6、图7和图11所示,上边梁总成4包括上边梁内侧板41和连接于上边梁内侧板41的上边梁外侧板42;上边梁内侧板41与上边梁外侧板42围合形成第四传力腔。便于加工,有利于碰撞吸能。
[0098]
优选地,如图3、图6、图7和图11所示,上边梁内侧板41的前端的内侧连接斜撑内板32,上边梁内侧板41的前端的底侧连接斜撑外板33,上边梁内侧板41的后端连接a柱内板5;如此,上边梁内侧板41作为上边梁总成4的主受力件,上边梁外侧板42作为上边梁总成4的辅受力件,将上边梁内侧板41的强度设计得高于上边梁外侧板42的强度,有利于简化结构,保证传力性能的前提下,实现减重降本。
[0099]
在一实施例中,如图1、图3和图6所示,塔座6的上端连接上边梁内侧板41的内侧,下端连接机舱纵梁1的外侧,有利于传力。优选塔座6上设有第五传力腔61,第五传力腔61自机舱纵梁1延伸至上边梁内侧板41,能进一步提高碰撞安全性,具体地,第五传力腔61可设有多个,以增加传力路径。
[0100]
在一实施例中,机舱纵梁1为铝制结构,优选为“目”字形挤压铝结构(如图7所示),有利于轻量化,满足碰撞需求。
[0101]
在一实施例中,副车架安装板总成2为钢制结构,强度更高。具体地,内侧安装板22、外侧安装板23和中间立板24为冲压钢板。
[0102]
优选地,内侧安装板22、外侧安装板23、中间立板24和螺纹管25(具有相应结构)点焊连接形成副车架安装板总成2。
[0103]
在一实施例中,上边梁斜撑板总成3为铝制结构,整体形成矩形梁结构。具体地,斜撑上内板321、斜撑下内板322和斜撑外板33为冲压铝板结构。
[0104]
优选地,斜撑上内板321、斜撑下内板322和斜撑外板33通过spr(自冲铆)连接形成上边梁斜撑板总成3。
[0105]
在一实施例中,上边梁总成4为钢制结构,强度更高,优选上边梁内侧板41和上边梁外侧板42呈l形(如图11所示),整体形成矩形梁结构。
[0106]
优选地,上边梁内侧板41和上边梁外侧板42通过点焊连接形成上边梁总成4。
[0107]
在一实施例中,塔座6为铝制结构,具体为铸造铝合金结构,优选为半封闭盒形结构(如图7所示),用于安装前悬挂,且避让前悬包络。
[0108]
具体地,塔座6的顶部和侧部具有加强筋,保证塔座6具有足够强度。
[0109]
在一实施例中,a柱内板5采用钢制结构,具体为冲压钢板,相对于现有a柱内板5的纵向尺寸增大。
[0110]
在一实施例中,副车架安装板总成2和上边梁斜撑板总成3分别通过fds(热熔自攻丝)连接机舱纵梁1,塔座6通过spr连接上边梁总成4,通过fds机舱纵梁1,通过螺栓连接机舱纵梁1后部接头。
[0111]
优选地,装配时,先将副车架安装板总成2、斜撑下内板322和机舱纵梁1连接成机舱纵梁内侧总成(如图5所示),将上边梁总成4、塔座6、斜撑上内板321和斜撑外板33连接成机舱纵梁外侧总成(如图6所示),再连接机舱纵梁1内侧总成和机舱纵梁1外侧总成(如图1所示)。
[0112]
本申请优选实施例,在满足副车架刚度和强度,碰撞安全c-ncap五星要求下,有效
减少前端吸能空间约85~295mm,能更好地匹配紧凑型机舱布置需求,实现短前悬纯电动车造型风格;机舱纵梁1的z向尺寸缩减约76~95mm,左、右机舱纵梁重量共降低约1.876~4.664kg,成本降低约56.28~139.92元,有利于轻量化提升和成本控制。
[0113]
以上仅为本发明的较佳实施例而已,并不用以限制本发明,凡在本发明的精神和原则之内所作的任何修改、等同替换和改进等,均应包含在本发明的保护范围之内。