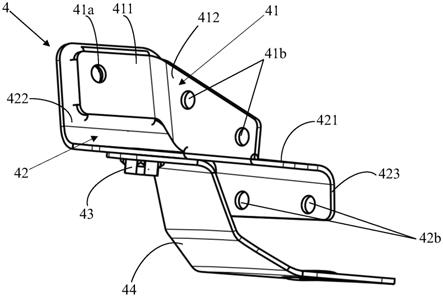
[0001]
本实用新型涉及汽车技术领域,特别是涉及一种前副车架碰撞导向支架总成及前副车架碰撞导向机构。
背景技术:[0002]
随着乘用车整车重量的增加与碰撞安全要求的不断提升,对底盘部件参与碰撞吸能的要求也愈来愈高。为了满足新版标准,整车设计阶段通常会匹配底盘部件与车身结构,将其组成吸能的“双通道”来应对汽车碰撞。其中,底盘部件中吸能的主要部件是前副车架,它承受正碰与偏置碰工况下较多的载荷,但在偏置碰工况中的25%小面积偏置碰撞工况中,因车辆与壁障重叠面积较小,前副车架的纵梁结构无法完全参与到上述碰撞工况中。
[0003]
专利cn106143612b公开了一种副车架安装点结构,主要针对安装点处结构进行设计优化,能够在车辆碰撞过程中脱落,降低对乘员舱乘客的伤害。
[0004]
专利cn109808771a公开了一种车辆、副车架安装结构及其设计方法,该结构可在前悬尺寸一定的条件下,通过控制副车架与车身安装支架的变形以及螺栓失效增加整车动态碰撞空间,提高动态碰撞空间的承载能力,从而提高汽车整体的吸能效率,降低汽车动力总成对前围的侵入,减小对乘员舱的直接冲击。
[0005]
上述两项专利,在设计初衷、实现方法及用途上与本专利都不尽相同。
[0006]
专利cn203854596u公开了一种汽车前防撞梁,联接于汽车前副车架/纵梁前端,通过前防撞梁的设计优化提升缓冲吸能效果。但此专利提供的结构中,保护标为冲压成型,它的制作周期长、费用较高,且在车辆短前悬的趋势下,布置局限性较大。
[0007]
综合上述专利的技术方案,现有技术方案的缺点主要在于工艺复杂、重量重、成本高。为保证碰撞强度和耐久性能,防撞结构多采用高强度的钢材冲压、焊接获得,受限于车辆前机舱布置空间和承载特点,此种防撞结构容易具有结构笨重并且平台拓展性差的缺点,且防撞结构与车身机舱纵梁一般采用四点或以上的螺接方式,占用了大量前轮前端的布置空间,产品的性价比、工艺性、结构通用性与拓展性较差。
技术实现要素:[0008]
本实用新型的目的是提供一种前副车架碰撞导向支架总成,旨在解决上述背景技术存在的不足,使结构紧凑且可显著提升碰撞性能。
[0009]
本实用新型提供一种前副车架碰撞导向支架总成,包括碰撞导向上板和碰撞导向下板,所述碰撞导向上板包括横向设置的第一受力板以及竖向设置的第二受力板和第三受力板,所述第二受力板的下端与所述第一受力板的前端一体连接,所述第三受力板的上端与所述第一受力板的右端一体连接,所述碰撞导向下板为“z”形结构,所述碰撞导向下板的顶端通过螺栓连接于所述第一受力板的下表面。
[0010]
进一步地,所述第一受力板为直角三角形结构,所述第二受力板的下端与所述第一受力板的第一直角边一体连接,所述第二受力板垂直于所述第一受力板向上延伸,所述
第三受力板的上端与所述第一受力板的第二直角边一体连接,所述第三受力板垂直于所述第一受力板向下延伸。
[0011]
进一步地,还包括碰撞导向上撑板,所述碰撞导向上撑板为“l”形结构,所述碰撞导向上撑板包括平行于所述第二受力板设置的第一撑板和平行于所述第三受力板设置的第二撑板,所述第一撑板和所述第二撑板一体连接。
[0012]
进一步地,所述碰撞导向上板、所述碰撞导向下板和所述碰撞导向上撑板均为钣金弯折一体成型。
[0013]
进一步地,所述第一撑板与所述第二受力板的内侧面贴合并焊接固定,所述第二撑板的下端与所述第一受力板的上表面焊接固定。
[0014]
进一步地,所述第一受力板设有第一螺栓安装孔,所述碰撞导向下板的顶端对应于所述第一螺栓安装孔的位置设有第二螺栓安装孔,所述第二螺栓安装孔的下方焊接固定有螺母,所述第一受力板与所述碰撞导向下板通过螺接固定。
[0015]
本实用新型还提供一种前副车架碰撞导向机构,包括前副车架焊接总成,所述前副车架碰撞导向机构还包括以上任一项所述的前副车架碰撞导向支架总成,所述前副车架碰撞导向支架总成螺接固定至所述前副车架焊接总成上。
[0016]
进一步地,所述前副车架碰撞导向支架总成的数量为两个,包含前副车架碰撞导向左支架总成和前副车架碰撞导向右支架总成,所述前副车架碰撞导向左支架总成和所述前副车架碰撞导向右支架总成分别螺接固定至所述前副车架焊接总成上,所述前副车架碰撞导向左支架总成和所述前副车架碰撞导向右支架总成在所述前副车架焊接总成上呈左右对称分布设置。
[0017]
进一步地,所述第一撑板设有第三螺栓安装孔,所述第二受力板对应于所述第三螺栓安装孔的位置设有第四螺栓安装孔,所述第三受力板设有两个第五螺栓安装孔,所述碰撞导向下板的底端设有第六螺栓安装孔,所述第一撑板、所述第二受力板、所述第三受力板和所述碰撞导向下板均螺接固定至所述前副车架焊接总成上。
[0018]
进一步地,所述前副车架碰撞导向机构还包括前橡胶衬套总成和后橡胶衬套总成,所述前橡胶衬套总成和所述后橡胶衬套总成均通过工装压入至所述前副车架焊接总成上。
[0019]
本实用新型的前副车架碰撞导向支架总成,通过折弯钣金与安装紧固件的合理配置,在保证碰撞需求与提升强度耐久的基础上有效减少零件重量,实现结构的轻量化设计,该导向机构工艺可行性高,结构适应性强,有利于降低生产成本。
[0020]
同时,该导向支架总成固连在前副车架的前安装塔座与前副车架纵梁之间,在保证前悬架空间布置和性能的前提下,无需重新布置开发现有常规车型的前悬。特别的,该导向机构可根据整车重量与周边布置适应变更,不仅利于车辆的开发验证与减重降本,而且对车辆主体的结构部件的平台化制造意义重大。
附图说明
[0021]
图1为本实用新型实施例中前副车架碰撞导向左支架总成的主视图;
[0022]
图2为本实用新型实施例中前副车架碰撞导向左支架总成的俯视图;
[0023]
图3为本实用新型实施例中前副车架碰撞导向左支架的焊接示意图;
[0024]
图4为本实用新型实施例中前副车架碰撞导向机构的仰视图;
[0025]
图5为本实用新型实施例中前副车架碰撞导向机构的侧视图。
具体实施方式
[0026]
下面结合附图和实施例,对本实用新型的具体实施方式作进一步详细描述。以下实施例用于说明本实用新型,但不用来限制本实用新型的范围。
[0027]
本实用新型的说明书和权利要求书中的术语“第一”、“第二”、“第三”、“第四”、“第五”等(如果存在)是用于区别类似的对象,而不必用于描述特定的顺序或先后次序。
[0028]
如图4至图5所示,本实施例提供的前副车架碰撞导向机构,包括前橡胶衬套总成1、前副车架碰撞导向支架总成、前副车架焊接总成6和后橡胶衬套总成7,其中,前副车架碰撞导向支架总成的数量为两个,包含前副车架碰撞导向左支架总成4和前副车架碰撞导向右支架总成5。
[0029]
下面以前副车架碰撞导向左支架总成4为例说明前副车架碰撞导向支架总成的结构。
[0030]
如图1至图3所示,前副车架碰撞导向左支架总成4包括碰撞导向上板42和碰撞导向下板44,碰撞导向上板42包括横向设置的第一受力板421以及竖向设置的第二受力板422和第三受力板423,第二受力板422的下端与第一受力板421的前端一体连接,第三受力板 423的上端与第一受力板421的右端一体连接,碰撞导向下板44为“z”形结构,碰撞导向下板44的顶端通过螺栓连接于第一受力板 421的下表面。
[0031]
具体地,第一受力板421为直角三角形结构,第二受力板422的下端与第一受力板421的第一直角边一体连接,第二受力板422垂直于第一受力板421向上延伸,第三受力板423的上端与第一受力板 421的第二直角边一体连接,第三受力板423垂直于第一受力板421 向下延伸。
[0032]
进一步地,前副车架碰撞导向左支架总成4还包括碰撞导向上撑板41,碰撞导向上撑板41为“l”形结构,碰撞导向上撑板41包括平行于第二受力板422设置的第一撑板411和平行于第三受力板423 设置的第二撑板412,第一撑板411和第二撑板412一体连接。
[0033]
具体地,碰撞导向上撑板41为起一定导向作用的加强件,在前碰工况(包括25%小面积偏置碰撞工况)中,与碰撞导向上板42和碰撞导向下板44一同起到了将碰撞载荷有效传递到前副纵梁的作用。本实用新型采用的碰撞导向上板42、碰撞导向下板44与加强导向件碰撞导向上撑板41简单结构,可在有限的布置空间下调整材料与料厚以及折弯件的型面与修边,以达到不同车型均可应用的目的。同时,在整车“v”型开发验证过程中能快速、及时匹配整车方案进行验证,节约了开发周期与成本。
[0034]
进一步地,如图3所示,第一撑板411与第二受力板422的内侧面贴合并焊接固定,第二撑板412的下端与第一受力板421的上表面焊接固定。
[0035]
优选地,第一撑板411的上端、下端和左端均与第二受力板422 的内侧面定位焊接固定。
[0036]
优选地,碰撞导向上板42、碰撞导向下板44和碰撞导向上撑板 41均为钣金弯折一体成型,采用钣金弯折结构不仅工艺简易,成型简单,制造周期短,而且在紧固件与加强钣金件的共同作用下,能有效改善特定碰撞工况下的变形情况。
[0037]
进一步地,第一受力板421设有第一螺栓安装孔42a,碰撞导向下板44的顶端对应于第一螺栓安装孔42a的位置设有第二螺栓安装孔(图未示),第二螺栓安装孔的下方固定有螺母43,第一受力板421与碰撞导向下板44通过螺接固定。
[0038]
优选地,第一螺栓安装孔42a的尺寸为直径φ12mm,第二螺栓安装孔的尺寸为直径φ10.5mm,螺母43的尺寸为m8
×
1.0,第一受力板421与碰撞导向下板44通过尺寸为m8
×
1.0的螺栓(图未示) 穿过第一螺栓安装孔42a和第二螺栓安装孔与螺母43配合螺接固定。
[0039]
如图4及图5所示,前副车架碰撞导向支架总成螺接固定至前副车架焊接总成6上。
[0040]
进一步地,前副车架碰撞导向左支架总成4和前副车架碰撞导向右支架总成5分别螺接固定至前副车架焊接总成6上,前副车架碰撞导向左支架总成4和前副车架碰撞导向右支架总成5在前副车架焊接总成6上呈左右对称分布设置。
[0041]
进一步地,第一撑板411设有第三螺栓安装孔41a,第二受力板 422对应于第三螺栓安装孔41a的位置设有第四螺栓安装孔(图未示),第三受力板423设有两个第五螺栓安装孔42b,碰撞导向下板44的底端设有第六螺栓安装孔44b,第一撑板411、第二受力板422、第三受力板423和碰撞导向下板44均螺接固定至前副车架焊接总成6 上。
[0042]
具体地,以前副车架碰撞导向左支架总成4为例说明前副车架碰撞导向支架总成与前副车架焊接总成6的螺接关系:如图3至图5所示,第一撑板411设有尺寸为直径φ10mm的第三螺栓安装孔41a,第二受力板422对应于第三螺栓安装孔41a的位置设有尺寸为直径φ 12mm的第四螺栓安装孔,第三螺栓安装孔41a和第四螺栓安装孔装配尺寸为m8
×
1.0的内六角花形盘头螺钉3;第三受力板423设有两个尺寸为直径φ10mm的第五螺栓安装孔42b,第五螺栓安装孔42b 同样装配尺寸为m8
×
1.0的内六角花形盘头螺钉3;碰撞导向下板44 的底端设有尺寸为直径φ12mm的第六螺栓安装孔44b,第六螺栓安装孔44b装配尺寸为m10
×
1.25的内六角花形盘头螺钉2。前副车架碰撞导向左支架总成4通过以上所述的三处尺寸为m8
×
1.0的内六角花形盘头螺钉3和一处尺寸为m10
×
1.25的内六角花形盘头螺钉2 螺接固定至前副车架焊接总成6的左侧。
[0043]
进一步地,前副车架碰撞导向右支架总成5以同样的方式螺接固定至前副车架焊接总成6的右侧。
[0044]
进一步地,第二撑板412设有两个尺寸为直径φ10mm的第一焊接定位孔41b,碰撞导向下板44的底端靠近第六螺栓安装孔44b设有尺寸为直径φ12mm第二焊接定位孔44a。
[0045]
组装前副车架碰撞导向左支架总成4时,可先将碰撞导向上撑板 41焊接至第二受力板422,组合后再与碰撞导向下板44螺接固定。
[0046]
进一步地,前橡胶衬套总成1和后橡胶衬套总成7均通过特定工装压入至前副车架焊接总成6上。
[0047]
当进行25%小面积偏置碰撞工况时,刚性壁障与整车的重叠区间大致在前橡胶衬套总成1和其以外的区域,此时,不论车身纵梁还是前副车架纵梁均不在碰撞重叠区域中,无法起到溃缩/折弯吸能的功能。增加前副车架碰撞导向支架总成后,特定碰撞工况下的载荷可通过前副车架碰撞导向左支架总成4和前副车架碰撞导向右支架总成5 传递至前副车架焊接总成6本体,使前副车架焊接总成6参与到吸能保护作用中,提升整车的碰撞性能。在整车cae(computer aidedengineering)分析与碰撞下,试验假人关键位置侵入量减少约53.6%,主副驾驶侧加速度峰值分别减小约3.7g与7.6g,速度归零时刻减少约0.5ms。
[0048]
具体地,以前副车架碰撞导向左支架总成4为例,在进行25%小面积偏置碰撞工况时,靠近前橡胶衬套总成1的前副车架焊接总成 6(如图4中前副车架焊接总成6的左上角和右上角位置)参与碰撞,而前副车架碰撞导向左支架总成4的前端通过第一撑板411和第二受力板422螺接固定至前副车架焊接总成6的左上角位置,前副车架碰撞导向左支架总成4的右端和下端分别通过第三受力板423和碰撞导向下板44螺接固定至前副车架焊接总成6的纵梁上,使得前副车架焊接总成6的纵梁可以参与到吸能保护作用中。
[0049]
本实用新型的效果在于:
[0050]
1、该前副车架碰撞导向支架总成,已验证在25%小面积偏置碰撞工况下,对整车碰撞性能有利,而且在保证前机舱的空间布置和性能的前提下,无需重新开发现有常规车型前悬。特别的,该前副车架碰撞导向机构结构简易,通过折弯件和连接紧固件的合理配置,可实现不同车辆的快速开发验证,不仅利于车辆开发周期与成本的管控,而且对主体结构的平台化制造意义重大;
[0051]
2、该前副车架碰撞导向支架总成虽结构简易但对碰撞性能有较好的改善,结构可适应性强,有利于降低开发与生产成本,同时性能方面的改善有利于提升品牌形象。
[0052]
以上所述仅是本实用新型的优选实施方式,应当指出,对于本技术领域的普通技术人员来说,在不脱离本实用新型技术原理的前提下,还可以做出若干改进和替换,这些改进和替换也应视为本实用新型的保护范围。