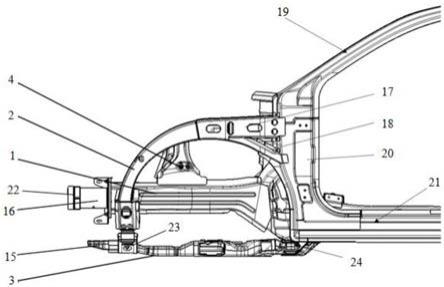
1.本实用新型属于汽车车身技术领域,特别是涉及一种车身前部结构及汽车。
背景技术:2.中国市场新增一个第三方考察体系中保研c
‑
iasi,其参照美国iihs引入了小偏置碰撞工况。小偏置碰撞工况因壁障与车体的重叠率仅25%,传统汽车中起主要吸能作用的纵梁无法参与吸能,因此对汽车结构设计带来巨大挑战。中国市场已经有若干热销车型因小偏置表现差而销量暴跌,因此开发适应小偏置的车体结构刻不容缓。
3.目前车辆舒适性和造型对消费者影响很大,宽裕的乘坐空间和短前悬的造型需求都导致机舱空间越来越小,碰撞所需的压溃吸能空间也随着减小,对碰撞优化带来较大挑战。
4.随着市场竞争的加剧,要求车型开发在更快的周期内,造出成本更低、重量更轻的车型,满足消费者需求。因此各车企纷纷提出各自的平台化方案,通过提高车型之间零件共用率,仅调整部分加强板来适应不同重量的车型。
5.现有的车身前部结构,纵梁、副车架纵梁较为平直,横向布置较为靠内,无法在小偏置碰撞中参与碰撞吸能。上短梁与纵梁通过上短梁连接板及前围板形成“口”字形结构,由于平行四边形结构的不稳定,在碰撞中刚度较低,且上短梁连接板易撕裂,进一步降低了结构强度。纵梁根部碰撞力分散结构少,容易造成局部侵入量过大。纵梁前段保留了压溃槽,导致强度匹配复杂,不利于平台化。副车架折弯点靠前,无法有效诱导底盘件向下运动。结构较为固化,对于平台化车型而言不利于灵活调整。
技术实现要素:6.本实用新型所要解决的技术问题是:针对现有的纵梁、副车架纵梁较为平直,横向布置较为靠内,无法在小偏置碰撞中参与碰撞吸能的技术问题,提供一种车身前部结构及汽车。
7.为解决上述技术问题,一方面,本实用新型实施例提供了一种车身前部结构,包括前防撞梁总成、前纵梁、上短梁、a柱总成及副车架,所述前纵梁、上短梁及a柱总成分别设置有左右相隔的两个,所述副车架包括左右相隔的两个副车架纵梁及前后相隔的两个副车架横梁,所述上短梁位于所述前纵梁的上方,所述前纵梁位于所述副车架的上方,所述副车架及两个前纵梁在左右方向上位于两个所述上短梁的内侧;所述上短梁的前端连接在同侧的所述前纵梁的前端,所述上短梁的后端连接在同侧的所述a柱总成上,所述前防撞梁总成连接在所述前纵梁的前端;
8.从俯视视角看,两个所述前纵梁呈前宽后窄的倒“八”字形,两个所述副车架纵梁呈前宽后窄的倒“八”字形。
9.可选地,所述车身前部结构还包括左右两个上短梁加强板,所述上短梁加强板的上端连接在同侧的所述上短梁上,所述上短梁加强板的下端连接在同侧的所述前纵梁上。
10.可选地,所述上短梁的前端位于所述上短梁的后端内侧,从俯视视角看,同侧的所述上短梁、上短梁加强板及前纵梁形成尖端在前的“a”字形结构。
11.可选地,所述副车架纵梁在其长度方向上呈现出两端高、中间低的形态,所述副车架纵梁最低点为副车架折弯点。
12.可选地,所述前纵梁由前至后依次设置有第一折点、第二折点及第三折点。
13.可选地,在发生正面碰撞时,所述第一折点向上弯折,所述第二折点向下弯折,所述第三折点向上弯折。
14.可选地,所述副车架还包括连接在所述副车架纵梁的前端的副车架吸能盒。
15.可选地,所述前纵梁包括前纵梁内板、前纵梁内板加强板、前纵梁后部加强板、前纵梁外板及前纵梁外板加强板,所述前纵梁内板连接在所述前纵梁外板的内侧以形成空腔,所述前纵梁内板加强板、前纵梁后部加强板及前纵梁外板加强板设置在所述空腔内,所述前纵梁内板加强板贴附在前纵梁内板的朝向前纵梁外板的一侧,所述前纵梁外板加强板贴附在前纵梁外板的朝向前纵梁内板的一侧,所述前纵梁后部加强板连接在所述前纵梁内板的后部与所述前纵梁外板的后部之间。
16.可选地,所述a柱总成包括a柱及a柱下立板,所述a柱的下端连接在所述a柱下立板的上端,所述a柱下立板的下端连接在同侧的门槛的前端;
17.所述上短梁包括上短梁前段、上短梁后段及上短梁后部加强板,所述上短梁前段的前端连接在同侧的所述前纵梁的前端,所述上短梁前段的后端连接所述上短梁后段的前端,所述上短梁后段的后端连接在a柱下立板的前侧;所述上短梁后部加强板的前端连接在上短梁后段上,所述上短梁后部加强板的后端连接在a柱下立板的前侧,所述上短梁后部加强板的后端位于所述上短梁后段的后端的下方。
18.根据本实用新型实施例的车身前部结构,发生正面碰撞时,具有三条纵向传力路径:一是,防撞梁总成
‑
前纵梁
‑
地板纵梁/前围板横梁等;二是,防撞梁总成
‑
上短梁
‑
a柱总成;三是,防撞梁总成
‑
副车架纵梁。并且,从俯视视角看,两个所述前纵梁呈前宽后窄的倒“八”字形,两个所述副车架纵梁呈前宽后窄的倒“八”字形。小偏置碰撞中,三条传力路径均可参与变形吸能,并产生较大的横向推力,从而降低乘员舱受到的直接冲击。从而可以在应对大重叠碰撞的基础上,应对小重叠碰撞。且相对现有技术并未增加车身重量。
19.另一方面,本实用新型实施例提供了一种汽车,其包括上述的车身前部结构。
附图说明
20.图1是本实用新型一实施例提供的车身前部结构的侧视图;
21.图2是本实用新型一实施例提供的车身前部结构的俯视图;
22.图3是本实用新型一实施例提供的车身前部结构的前纵梁与相关部件的连接示意图;
23.图4是本实用新型一实施例提供的车身前部结构的前纵梁的结构图;
24.图5是本实用新型一实施例提供的车身前部结构的前纵梁的折弯点设计及折弯效果图;
25.图6是本实用新型一实施例提供的车身前部结构的副车架纵梁的示意图;
26.图7本实用新型一实施例提供的车身前部结构的前纵梁与常规的前纵梁在正面碰
撞时压溃力对比图;
27.图8本实用新型一实施例提供的车身前部结构与常规的车身前部结构在正面碰撞时加速度波形的对比图。
28.说明书中的附图标记如下:
29.1、前纵梁;2、上短梁前段;3、副车架纵梁;4、上短梁加强板;5、前围板外侧横梁;6、扭力盒;7、地板纵梁;8、前副车架后安装板;9、前围板横梁;10、前纵梁内板;11、前纵梁内板加强板;12、前纵梁后部加强板;13、前纵梁外板;14、前纵梁外板加强板;15、副车架吸能盒;16、防撞梁吸能盒;17、上短梁后段;18、上短梁后部加强板;19、a柱;20、a柱下立柱;21、门槛;22、前防撞梁;23、副车架前安装点;24、副车架后安装点;25、副车架横梁25。
具体实施方式
30.为了使本实用新型所解决的技术问题、技术方案及有益效果更加清楚明白,以下结合附图及实施例,对本实用新型进行进一步的详细说明。应当理解,此处所描述的具体实施例仅仅用以解释本实用新型,并不用于限定本实用新型。
31.在本实用新型实施例中,左右方向为车宽方向,前后方向为车长方向,内侧表示指向车内的方向,外侧表示指向车外的方向。
32.如图1至图8所示,本实用新型实施例提供的车身前部结构,包括前防撞梁总成、前纵梁1、上短梁、a柱总成及副车架,所述前纵梁1、上短梁及a柱总成分别设置有左右相隔的两个,所述副车架包括左右相隔的两个副车架纵梁3及前后相隔的两个副车架横梁25,所述上短梁位于所述前纵梁1的上方,所述前纵梁1位于所述副车架的上方,所述副车架及两个前纵梁1在左右方向上位于两个所述上短梁的内侧;所述上短梁的前端连接在同侧的所述前纵梁1的前端,所述上短梁的后端连接在同侧的所述a柱总成上,所述前防撞梁总成连接在所述前纵梁1的前端。
33.前侧的副车架横梁23的左端连接左侧的副车架纵梁3的前端,前侧的副车架横梁23的右端连接右侧的副车架纵梁3的前端。后侧的副车架横梁23的左端连接左侧的副车架纵梁3的后端,后侧的副车架横梁23的右端连接右侧的副车架纵梁3的后端。副车架纵梁3通过副车架前安装点23和副车架后安装点24与车身相连。
34.从俯视视角看(图2),两个所述前纵梁1呈前宽后窄的倒“八”字形,两个所述副车架纵梁3呈前宽后窄的倒“八”字形。
35.在一实施例中,所述车身前部结构还包括左右两个上短梁加强板4,所述上短梁加强板4的上端连接在同侧的所述上短梁上,所述上短梁加强板4的下端连接在同侧的所述前纵梁1上。所述上短梁的前端位于所述上短梁的后端内侧,从俯视视角看(图2),同侧的所述上短梁、上短梁加强板4及前纵梁1形成尖端在前的“a”字形结构。“a”字形结构结构稳固。
36.在一实施例中,如图6所示,所述副车架纵梁3在其长度方向上呈现出两端高、中间低的形态,所述副车架纵梁3最低点为副车架折弯点(图6中的a点)。在碰撞中可实现副车架的v形折弯模式,带动安装在副车架上的底盘件向下运动,从而提高碰撞吸能效率。
37.在一实施例中,如图5所示,所述前纵梁3由前至后依次设置有第一折点、第二折点及第三折点,所述前纵梁3上不设压溃段。即与现有技术相比,取消了前纵梁前段的压溃段。通过型面变化、加强板和诱导槽设置,使得第一折点、第二折点及第三折点在碰撞中发生变
形,其变形模式呈标准的三点式折弯。即,在发生正面碰撞时,所述第一折点向上弯折,所述第二折点向下弯折,所述第三折点向上弯折。
38.在一实施例中,如图1及图2所示,所述副车架还包括通过螺栓连接在所述副车架纵梁3的前端的副车架吸能盒15。
39.在一实施例中,如图1所示,所述前防撞梁总成包括前防撞梁22及防撞梁吸能盒16,所述前防撞梁22的两端后侧各设置在所述防撞梁吸能盒16,所述前纵梁1的前端通过螺栓连接在同侧的所述防撞梁吸能盒16上。
40.在一实施例中,如图4所示,所述前纵梁1包括前纵梁内板10、前纵梁内板加强板11、前纵梁后部加强板12、前纵梁外板13及前纵梁外板加强板14,所述前纵梁内板10连接在所述前纵梁外板13的内侧以形成空腔,所述前纵梁内板加强板11、前纵梁后部加强板12及前纵梁外板加强板14设置在所述空腔内,所述前纵梁内板加强板11贴附在前纵梁内板10的朝向前纵梁外板13的一侧,所述前纵梁外板加强板14贴附在前纵梁外板13的朝向前纵梁内板10的一侧,所述前纵梁后部加强板13连接在所述前纵梁内板10的后部与所述前纵梁外板13的后部之间。优选地,前纵梁内板10、前纵梁内板加强板11、前纵梁后部加强板12、前纵梁外板13及前纵梁外板加强板14通过焊接形成前纵梁1。
41.小偏置碰撞中还要求乘员舱保持稳定,其中a柱19最容易发生折弯,为此可以通过调节上短梁后段17和上短梁加强板18的强度,实现a柱19和a柱下立柱20的碰撞力合理分配,避免a柱19承受过大碰撞力而发生折弯。
42.在一实施例中,如图1所示,所述a柱总成包括a柱19及a柱下立板20,所述a柱19的下端连接在所述a柱下立板20的上端,所述a柱下立板20的下端连接在同侧的门槛21的前端。所述上短梁包括上短梁前段2、上短梁后段17及上短梁后部加强板18,所述上短梁前段2的前端连接在同侧的所述前纵梁1的前端,所述上短梁前段2的后端连接所述上短梁后段17的前端,所述上短梁后段17的后端连接在a柱下立板20的前侧;所述上短梁后部加强板18的前端连接在上短梁后段17上,所述上短梁后部加强板18的后端连接在a柱下立板20的前侧,所述上短梁后部加强板18的后端位于所述上短梁后段17的后端的下方。
43.在一实施例中,如图3所示,所述前纵梁1分别连接前围板外侧横梁5、扭力盒6、地板纵梁7、前副车架后安装板8及前围板横梁9,以形成多叉型结构,可以很好地分散前纵梁1所受的碰撞力,防止车厢局部侵入过大。
44.上述实施例的车身前部结构其工作原理如下:
45.正面碰撞过程具有不同重叠率的壁障,常规技术中,由于前纵梁和副车架纵梁较为平直,与25%重叠刚性壁障重叠量小,无法有效吸收能量。本实施例的中车身前部结构发生正面碰撞时,具有三条纵向传力路径:一是,前防撞梁22
‑
防撞梁吸能盒16
‑
前纵梁1
‑
地板纵梁7/前围板横梁9等;二是,前防撞梁22
‑
防撞梁吸能盒16
‑
前纵梁1
‑
上短梁前段2
‑
上短梁后段17/上短梁后部加强板18
‑
a柱19/a柱下立柱20。由于两个前纵梁1和两个副车架纵梁3外撇,形成的倒“八”字形结构,同时上短梁呈向内环抱布置,并与前纵梁1及上短梁加强板连接形成稳固的“a”字形结构,因此小偏置碰撞中,三条传力路径均可参与变形吸能,并产生较大的横向推力,从而降低乘员舱收到的直接冲击。
46.平台化要求同一套前纵梁1结构应对不同重量的车型,同一个车型需要应对正面碰撞不同重叠率的多个工况,为此,需要提高前纵梁1的变形模式的稳健性。如图7所示,常
规技术中,变形模式为防撞梁吸能盒压溃a1
‑
前纵梁前段压溃a2
‑
前纵梁三段折弯a3(参见图7的实线),因而需要匹配三级递增的压溃力强度。本申请的变形模式为防撞梁吸能盒16压溃b1
‑
前纵梁1三点折弯b2(参见图7中虚线),只需匹配两级压溃力强度,对于多车型、多工况发动机舱强度匹配带了了极大的便利,同时提高了变形模式的稳健性。
47.如图8所示,在正面碰撞过程中,相对于常规技术,加速度波形得到优化(虚线为本申请的加速度波形,实线为现有技术的加速度波形),在短前悬等更严苛的工程条件下,更好的满足正面碰撞对加速度波形的要求,降低碰撞性能对吸能空间的需求。这样,发动机舱尽可能的多吸收能量,减少对乘员的冲击。为此通过三个方式提升机舱吸能:一是,将前纵梁1的三级压溃力强度匹配降低为两级压溃强度匹配,提升防撞梁吸能盒16强度;二是,缩短前纵梁1,拉大防撞梁吸能盒16;增加副车架吸能盒15。通过将前纵梁1三段折弯改为三点折弯模式,将副车架设计成v形折弯模式,增大整车压溃量,降低乘员舱冲击。
48.在正面碰撞中还需控制前纵梁1根部(后部)侵入量,避免乘员脚部受到挤压而伤害,为此,前纵梁1通过前围板外侧横梁5、扭力盒6、地板纵梁7、前副车架后安装板8、前围板横梁9组成的多叉型结构分散碰撞力。
49.为适应不同车型重量的强度需求,发动机舱设计强化了平台化设计的概念,不需要调整大板结构,仅可通过调整局部部件,如防撞梁吸能盒16、副车架吸能盒15、前纵梁内板加强板11、上短梁加强板4,即可满足平台不同车型重量对结构强度的需求,从而降低平台车型研发成本。
50.根据本实用新型实施例的车身前部结构,发生正面碰撞时,具有三条纵向传力路径:一是,防撞梁总成
‑
前纵梁
‑
地板纵梁/前围板横梁等;二是,防撞梁总成
‑
上短梁
‑
a柱总成;三是,防撞梁总成
‑
副车架纵梁。并且,从俯视视角看,两个所述前纵梁呈前宽后窄的倒“八”字形,两个所述副车架纵梁呈前宽后窄的倒“八”字形。小偏置碰撞中,三条传力路径均可参与变形吸能,并产生较大的横向推力,从而降低乘员舱受到的直接冲击。从而可以在应对大重叠碰撞的基础上,应对小重叠碰撞。且相对现有技术并未增加车身重量。
51.另外,本实用新型实施例还提供一种汽车,包括上述实施例的车身前部结构。
52.以上所述仅为本实用新型的较佳实施例而已,并不用以限制本实用新型,凡在本实用新型的精神和原则之内所作的任何修改、等同替换和改进等,均应包含在本实用新型的保护范围之内。