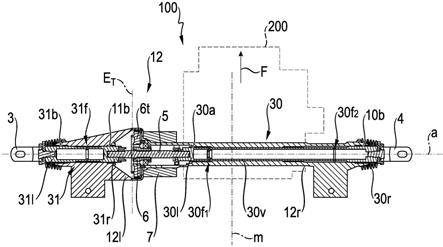
1.本实用新型涉及一种用于线控转向系统的主轴传动装置,该线控转向系统用于具有能够转向的前桥和/或后桥的机动车辆;以及一种线控转向系统。
背景技术:2.从现有技术中已知一种根据de 10 2014 206 934 a1的线控转向系统,该线控转向系统与车辆结构连接并且集中作用到车辆车桥的两个车轮或车轮支撑件上,以改变车轮的车轮转向角。de 10 2017 211 672 a1同样示出了一种所属类型的转向装置。在此,设置有延长件来延长致动器的主轴,以便在轴向方向上延长主轴。延长主轴或主轴传动装置是有利的,原因在于由此可以以较少的改变来利用用于不同车辆的致动器以及在那里现有的结构空间。延伸件由于其结构设计需要额外的滑动轴承或推力轴承,该滑动轴承或推力轴承被布置在额外的轴承座内。延伸件由轴承座支撑在车身侧。这种额外的支承或支撑虽然有效地防止了延伸件的屈曲,然而这造成了转向系统在车辆车桥上的额外重量并且在生产和装配方面是更高耗费的。
3.此外,从de 10 2016 201 699 a1中已知一种滑动销,该滑动销通过冷成型制造。与从现有技术中的两个前述文献以类似的方式同样实现的一样,滑动销与主轴的端部联接,使得主轴在转向系统的壳体中被轴向引导并且在那里被支承以便低摩擦地移位。
技术实现要素:4.通过延长主轴,线控转向系统可以与在相应的车辆的车桥的区域中现有的结构空间相适配。因此,为了解决上述问题,本实用新型的目的在于给出一种简单的方案来适配主轴传动装置以及线控转向系统,使得能够根据在车辆车桥上的可供使用的结构空间以低耗费来适配线控转向系统。在此,应找到以低耗费可以实现的成本有效的方案。此外可以以简单的方式满足线控转向系统的针对总重量轻的要求。
5.本实用新型致力于延长方面以及转向系统的低重量方面。为此,给出一种用于线控转向系统的主轴传动装置以及一种线控转向系统。
6.根据第一方面,本实用新型涉及一种用于线控转向系统的主轴传动装置,该线控转向系统用于具有能够转向的前桥和/或后桥的机动车辆,其中主轴传动装置至少由主轴、位置固定地支承的主轴螺母以及用于将主轴支承在转向系统的壳体中的至少一个支承套筒制成。主轴被设置成通过轴向位移来改变车辆车桥上的至少一个要转向的车轮的车轮转向角。借助于由主轴的外螺纹以及主轴螺母的内螺纹构成的传动螺纹,通过旋转主轴螺母,优选通过借助于电动马达间接或直接地旋转驱动来旋转主轴螺母,进行主轴的轴向位移。为此,在主轴的至少一个端部上、在可轴向位移的主轴与要转向的车轮或车轮支撑件之间设置有作为支承构件和连接构件的至少一个支承套筒。主轴被设计为实心构件,该实心构件由半成品(例如圆钢)制成。为此,圆钢借助于成型,例如通过滚轧并且/或者切削加工(例如车削并且/或者铣削)制成主轴。在此,主轴获得外螺纹,该外螺纹取决于其螺距和期望的
轴向调节行程优选通过滚轧产生。为了可以低摩擦和尽可能低噪声地实现对转向系统的操作,主轴螺母和主轴以较小的公差制造并且因此制造为精密构件。因此同样在重量方面有利的是:主轴从其轴向延伸部方面尽可能短地形成并且以尽可能小的、优选为10mm至20 mm的直径形成。主轴长度取决于使用目的。作用于每个车轮的单个执行器优选地是100mm至140mm长。作用于车桥的两个车轮的中央执行器优选是190 mm至300mm的长度。因此,转向运动到车轮支撑件的传递(必要时在中间连接有转向器的情况下)并非直接通过将连结叉联接到主轴的端部来实现。而是,为此在连结叉与主轴端部之间安装有支承套筒,以确保主轴沿其纵向轴线在转向系统的壳体中的支承和引导。
7.优选地,线控转向系统具有至少两件式的壳体,该壳体具有大致与主轴的纵向轴线正交形成的分型面。壳体在传动螺纹的区域中具有最大的结构空间需求。这例如由主轴螺母的直径并且额外地由驱动装置(例如平行于纵向轴线布置的驱动马达)和传动装置(例如必要的带传动装置)决定。如果现有的结构空间有限(例如在传动装置或电动驱动装置通常靠近车桥并且居中地布置的车辆中),那么线控转向系统不可能中央地、居中地布置在车轮之间。在这种情况下,转向系统必须以其壳体在分型面的区域中非常偏心地布置,即靠近车轮布置。由此得出主轴的一个端部相对靠近车轮布置,其中相反的端部相对远地远离相反的车轮。为了这个更加远离壳体的分型面的车轮,现在必须提供主轴延长部。如果仅偏心地布置中央致动器,并且通过转向器跨接连结叉与远离的车轮或车轮支撑件之间的距离,则可能以不利的方式在要转向的车桥的左侧车轮和右侧车轮上得出不同的调节运动。这是由运动学决定的,并且车轮转向角的差别大到不能以可接受的程度实现车轮转向角的均匀改变。出于这个原因选择延长主轴,其方式为连结叉在线控转向系统的端部各自相对于相应的车轮支撑件或车轮具有相同的间隔。
8.在图2中给出了已知的主轴延长部的形式。延长部20v在此由实心圆棒形成。这个实心圆棒被布置在现有的支承套筒10与主轴5的端部之间。这些构件的联接通常通过拧接来实现。从图2中可以看到,为了引导主轴,一方面设置有第一滑动衬套20d,并且在壳体12的端部设置有端侧的滑动衬套10b。然而上述结构必须在接合位置10f、20f处由额外的滑动衬套20z支撑和引导。否则不能实现同轴度(rundlauf),原因在于这种连接不能形成足够的弯曲刚度。一方面,在壳体12中设置有针对额外的滑动衬套20z的额外的支撑方案。此外,上述结构由于延长部20v的圆棒的实心设计而高耗费地制造。通过这种实心的延长部引入的额外的重量构成了另外的缺点。该构造同样在出现的弯曲力方面由于要支撑的车轮的高的横向力和侧向力在行驶操作中是存在问题的。
9.根据本实用新型提出,支承套筒由至少两个套筒构件制成,其中这些套筒构件间接或直接地以材料配合并且/或者力配合并且/或者形状配合的方式相互接合。令人惊讶的是,已证实,当支承套筒由两个套筒构件制成时,支承套筒的总长度例如从150mm起就已经产生了重量优点。因此,整个轴向延伸部(即支承套筒的总长度)由所使用的套筒构件的长度得出。
10.本实用新型可以用于所谓的单个执行器以及中央执行器。如果线控转向系统被设计为单个执行器,那么可以以这个单个执行器在车桥上实现一个车轮上的车轮转向角的改变。因此对于车桥而言优选地使用两个单个执行器。在单个执行器的情况下,在主轴的一个端部上仅需要一个支承套筒。在此情况下,上述连结叉在主轴的该一个端部与支承套筒连
接。在同时作用于车桥的两个车轮的中央执行器的情况下,在主轴的每个端部布置有支承套筒,并且连结叉各自在端侧以支承套筒与主轴联接。
11.在直接接合的支承套筒的情况下,大体上仅两个套筒构件相互连接,因此由此得到单件式的支承套筒。为了制造直接接合的支承套筒,首先由坯料构件通过成型方法、优选冷挤压来建立至少一个套筒构件。可以与提到的方式一样建立另一个套筒构件,然而替代性地,可以由圆棒作为车削件,即借助于机械加工来制造该另一个套筒构件。在套筒构件的端部,这些套筒构件各自形成管状,使得这些套筒构件具有圆柱形的管端部。这个管端部优选具有2mm至5mm、优选3mm至4mm的壁厚度。套筒构件的与该管端部背离的端部设有与套筒构件的纵向轴线同心布置的内螺纹。在此,内螺纹可以借助于成型或在另一个步骤中以切削方式形成。优选地,通过成型方法(例如滚轧)来建立内螺纹。由此,螺纹由成型方法来压实材料而获得较高的强度。为了制造支承套筒,套筒构件以其管端部在端侧彼此接合。优选地,套筒构件相互焊接,最优选通过摩擦焊接相互焊接。为此,这些套筒构件以彼此叠置的纵向轴线在压力下相对于彼此运动,其中这些套筒构件的端面彼此接触,通过产生的摩擦导致材料的升温和塑化。摩擦焊接的优点在于:所谓的热影响区域明显比常规的焊接方法小。在接合区域中不会导致熔融物的形成。由此获得形状合适的支承套筒,其中在摩擦焊接过程后不需要其他加工。
12.根据另一个优选的实施方式,由两个套筒构件以及处于其间的管体间接地制成支承套筒。在此,与在上述实施方式一样的方式制造套筒构件。然而套筒构件现在并非直接地在其端面相互接合。根据需要的主轴延长部,根据需要的延长部的长度由管半成品切割出管体。将管体在其端部的区域中、在套筒构件之间与这些套筒构件的管端部接合成支承套筒。在此,管体的端面以优选的方式与各自背离套筒构件的螺纹的端面接合。这优选通过焊接、最优选通过摩擦焊接实现,正如已经关于间接接合的支承套筒所指出的那样具有在那里提及的优点。
13.例如选择优选热轧的无缝钢管作为管半成品。这种例如以“e355”命名的管半成品作为有利的半成品批量货物可获得。显而易见,管(即圆柱形的管体) 具有比相同长度的圆棒显著更轻的重量。如果对于主轴而言提供大约10mm至 20mm的直径,那么对于支承套筒而言假定25mm至35mm的外直径。因此显而易见,在这种直径的情况下,使用无缝钢管作为管体来延长主轴传动装置或主轴为整个主轴传动装置带来明显的重量优点。此外,管体的突出之处在于较高的抗弯阻力矩。因此,即使使用非常长的延长部的情况下,也可以以比针对延长部使用实心圆棒时更小的总重量来制造线控转向系统。
14.为了简化支承套筒的制造,制成套筒构件的管端部,其方式为使这些管端部与管半成品的内直径和/或外直径近似对应,优选具有相同的内直径以及外直径。由此确保通过一致的环形面来获得用于摩擦焊接的尽可能最大的接触。
15.根据一个替代性的实施方式,同样可以设计套筒构件的管端部的直径和管体的直径,其方式为这些直径彼此具有至少游隙配合或甚至过盈配合。因此,例如可能将管端部压入管体的端侧的端部中。替代性地,可以推入这些管端部,以便随后将这些管端部相互焊接。在此,例如同样需要非常低的热量输入的激光焊接是合适的。替代性地,管体的端部可以具有较小的直径,使得可以将这些端部压入或推入相应的套筒构件的管端部,以便接合这些端部。在此可能获得如下优点:支承套筒的总长度可以被设计成可变的,尤其还根据对
管体的切割是可变的。
16.如已经在上文提到的,通过支承套筒确保沿主轴的纵向轴线相对于壳体支承并且因此还引导主轴。由进入、优选压入线控转向系统的壳体中的滑动衬套来支承和引导支承套筒。为此,在壳体中为滑动衬套提供对应的支承座,并且在压入后获得永久的形状配合并且力配合的连接。在一个优选的实施方式中,在制造套筒构件之后,在远离接合位置或背离接合位置的端部的区域中各自建立滑动支承面。优选地,这个滑动支承面被设计成圆柱形,并且借助于切削加工以及随后的研磨过程建立。替代性地,还可以在制造支承套筒之后建立滑动支承面。
17.根据另一个方面,本实用新型涉及一种线控转向系统,该线控转向系统用于具有前桥转向系统和/或后桥转向系统的机动车辆,该线控转向系统具有壳体以及接纳在其中的主轴传动装置,该主轴传动装置具有相对于壳体固定的主轴螺母和能够相对于壳体轴向移位的主轴。至少一个端部与支承套筒联接,并且以借助于支承套筒相对于壳体可移位的方式支承。如果位置固定地支承的主轴螺母以其内螺纹例如由电动马达旋转驱动,则以其外螺纹与主轴螺母处于啮合的主轴沿其纵向轴线位移。在此,支承套筒被设计成多件式的,并且根据上述方法在单独的步骤或多个步骤中制造。
附图说明
18.对于本实用新型,下面参照附图描述优选的实施方式。在附图中:
19.图1示出了设计有主轴驱动装置的线控转向系统,
20.图2示出根据图1的主轴驱动装置的细节视图,
21.图3示出了根据本实用新型的设计有主轴驱动装置的线控转向系统。
具体实施方式
22.图1示出了已知的并且本技术开篇所提到的线控转向系统1,该线控转向系统还被称为致动器或简称为执行器,该致动器或执行器被紧固在车辆结构2 上,例如居中地紧固在机动车辆的车桥支撑件上。由于存在的结构空间,因此在此可以居中地布置。示出的中央执行器1能够使车桥的两个车轮17r、18r同时转向,并且具有彼此相反布置的两个铰接点,即第一连结叉3、第二连结叉 4,这些连结叉在中间连接有横向转向器(spurlenker)14、15的情况下与车轮支撑件17、18联接。执行器1设计有主轴驱动装置并且具有可轴向移位的主轴5,该主轴可以由主轴螺母6而由电动马达7轴向位移或调节。主轴5在主轴螺母6的区域中具有设计为外螺纹的自锁式螺纹5a,该自锁式螺纹与主轴螺母6的对应的内螺纹6a啮合并且因此构成传动螺纹。在主轴螺母6转动时,(以未展示的方式)被防止旋转的主轴5(在附图中)沿其纵向轴线s向右或向左执行轴向运动。主轴5具有两个相反的主轴端部或紧固端部8、9,这些端部本身与支承套筒10、11固定地连接。支承套筒10、11在壳体侧借助于滑动衬套 10b、11b在滑动轴承中受到径向地引导并且与第一连结叉3、第二连结叉4构成两个铰接点3、4。支承套筒10、11由铸造坯料构件或圆棒以切削的方式制造,并且在长度给定的情况下由于壁厚度而具有较大的重量。
23.图2示出了由实心圆棒制成的主轴延长部20v。关于图2的详细细节可以在上文得出并且在此不再说明。
24.图3示出了中央执行器100,该中央执行器具有两件式的壳体12,该壳体具有左侧壳体部分12l和右侧壳体部分12r。壳体部分12l、12r沿与主轴5的纵向轴线正交形成的分型面e
t
相互连接。考虑到用于这种执行器或线控转向系统100所需要的结构空间,在此也得出与在图1中示出的执行器1相同的结构空间需求。如果在车桥转向的情况下在车辆中心(由纵向轴线m指出)的区域中不存在结构空间,则设备(例如线控转向系统100)必须被布置或构造成使得可以安装到现有的车桥设计或现有的结构空间中,而无需在车桥的区域中的安装位置处对车辆做出昂贵的改变。由于具有被压在主轴螺母6上的传动轮6t 的主轴传动装置的直径,因此壳体12在分型面e
t
的区域中具有整个执行器100 的最大直径。同样,在此考虑用于凸缘安装的电动马达7所需要的结构空间,该电动马达在图3中、在示出的图示中被布置在右侧壳体部分12r的后方。在图3中示意性地用虚线展示了车桥的驱动单元200,该驱动单元围绕(未展示的)车辆的纵向轴线m在车辆的后方部分的区域中延伸。在当前的结构空间条件下不可能插入或安装根据图1的执行器。出于这个原因,中央执行器100如在图3中展示的那样形成。相对于主轴5的纵向轴线s,主轴传动装置以及因此的分型面e
t
非常偏心地布置。在此示出的执行器100的布置或设计以为了延长主轴而使用第二支承套筒30为前提,该支承套筒具有以下第二套筒构件:左侧套筒端部30l和右侧套筒端部30r以及位于其间的延长部30v。在主轴的另一侧实施有由第一套筒构件构成的第一支承套筒31,第一套筒构件包括左侧套筒端部31l和右侧套筒端部31r。在此,第一支承套筒31然而由于靠近车轮而仅被实施为没有延长部的短的支承套筒。这两个支承套筒30、31具有所谓的接合位置31f、30f1、30f2。左侧展示的第一支承套筒31以如下方式制造:首先制造左侧套筒端部31l和右侧套筒端部31r。左侧套筒端部31l通过冷成型被制造为挤压件。右侧套筒端部31r是由高强度钢制造而成的车削件。这两个套筒端部在接合位置31f的区域中借助于摩擦焊接彼此永久地制成单件式的第一支承套筒31。第一支承套筒31在其外端部的区域中(即背离接合位置)借助于滑动衬套11b、31b径向引导并且支承在壳体部分12l中。相比之下,在另一侧被插入在主轴5的端部与叉4之间的第二支承套筒30由三个部分制成。与之前解释的第一支承套筒31类似地,在此也制成与主轴5连接的左侧套筒端部 30l,该左侧套筒端部被制造成车削件。在相反侧示出了套筒端部30r,该套筒端部被制造成挤压件,即借助于成型来制造。然而,现在在这些套筒端部30l、 30r之间布置有呈管体形式的延长部30v。管体具有与套筒端部30l、30r的朝向管体的端部相同的外直径和内直径。与第一支承套筒31类似,套筒端部30l、 30r与管体30v之间的连接同样借助于摩擦焊接实施。摩擦焊接在以30f1、30f2示出的接合位置处进行。第二支承套筒30在其外端部的区域中(即背离接合位置)借助于滑动衬套11b、31b径向引导并且支承在壳体部分12r中。尽管有延长部30v,但不需要其他支承,原因在于管体30v具有高的并且因此足够的弯曲刚度,并且在外部区域中的支承是足够的。
25.借助在图3中示出的执行器100,即使在困难的结构空间状况下也可以将线控转向系统集成到车辆车桥中。通过管体30v来延长第二支承套筒30或主轴5可以形成成本有效的并且与实心圆棒相比重量轻或重量优化的延长部。因此还可以跨接更大的距离,当车辆车桥中现有的结构空间较小时这是必要的。即使延长部较大,制造本身也是可以容易地实现的,其中尤其延长的管体30v 的圆柱形形状已经由坯料构件给出。因此使现有的线控转向系统可以容易地与现有的结构空间状况相适配。不必适配示出的主轴传动装置的左侧。仅对应地容易地延长右侧。
26.然而,即使主轴传动装置以常规方式居中布置(例如在图1中由现有技术示出的),也可以借助于所提到的方法实现优点,即节省重量。通过使用套筒端部或套筒构件来制造支承套筒可以以简单的方式实现这种重量节省。因此,即使在线控转向系统中,通过根据本实用新型的由套筒构件构成的支承套筒的设计也可以实现在现代车辆中所要求的重量优化。
27.附图标记清单
[0028]1ꢀꢀꢀ
线控转向系统
[0029]2ꢀꢀꢀ
车辆结构
[0030]3ꢀꢀꢀ
第一连结叉
[0031]4ꢀꢀꢀ
第二连结叉
[0032]5ꢀꢀꢀ
主轴
[0033]
5a
ꢀꢀ
主轴螺纹
[0034]6ꢀꢀꢀ
主轴螺母
[0035]
6a
ꢀꢀ
主轴螺母螺纹
[0036]
6t
ꢀꢀ
传动轮
[0037]7ꢀꢀꢀ
电动马达
[0038]8ꢀꢀꢀ
主轴端部(右侧)
[0039]9ꢀꢀꢀ
主轴端部(左侧)
[0040]
10
ꢀꢀ
支承套筒(右侧)
[0041]
10b 滑动衬套
[0042]
10f 接合位置
[0043]
11
ꢀꢀ
支承套筒(左侧)
[0044]
11b 滑动衬套
[0045]
12
ꢀꢀ
壳体
[0046]
12l 左侧壳体部分
[0047]
12r 右侧壳体部分
[0048]
13
ꢀꢀ
带传动装置
[0049]
14
ꢀꢀ
转向器
[0050]
15
ꢀꢀ
转向器
[0051]
17
ꢀꢀ
车轮支撑件
[0052]
18
ꢀꢀ
车轮支撑件
[0053]
20v 延长部
[0054]
20f 接合位置
[0055]
20b 滑动衬套
[0056]
20z 滑动衬套
[0057]
100 中央执行器
[0058]
30 第二支承套筒
[0059]
30l 套筒端部左侧
[0060]
30r 套筒端部右侧
[0061]
30v 延长部,管体
[0062]
30f
1 接合位置
[0063]
30f
2 接合位置
[0064]
30a 滑动衬套
[0065]
31
ꢀꢀ
第一支承套筒
[0066]
31l 套筒端部左侧
[0067]
31r 套筒端部右侧
[0068]
31f 接合位置
[0069]
31b 滑动衬套
[0070]
a
ꢀꢀꢀ
车桥的纵向轴线
[0071]
a
ꢀꢀꢀ
后桥
[0072]
s
ꢀꢀꢀ
主轴的纵向轴线
[0073]
f
ꢀꢀꢀ
行驶方向
[0074]
e
t
ꢀꢀ
壳体的分型面
[0075]
m
ꢀꢀꢀ
纵向轴线(车辆中心)