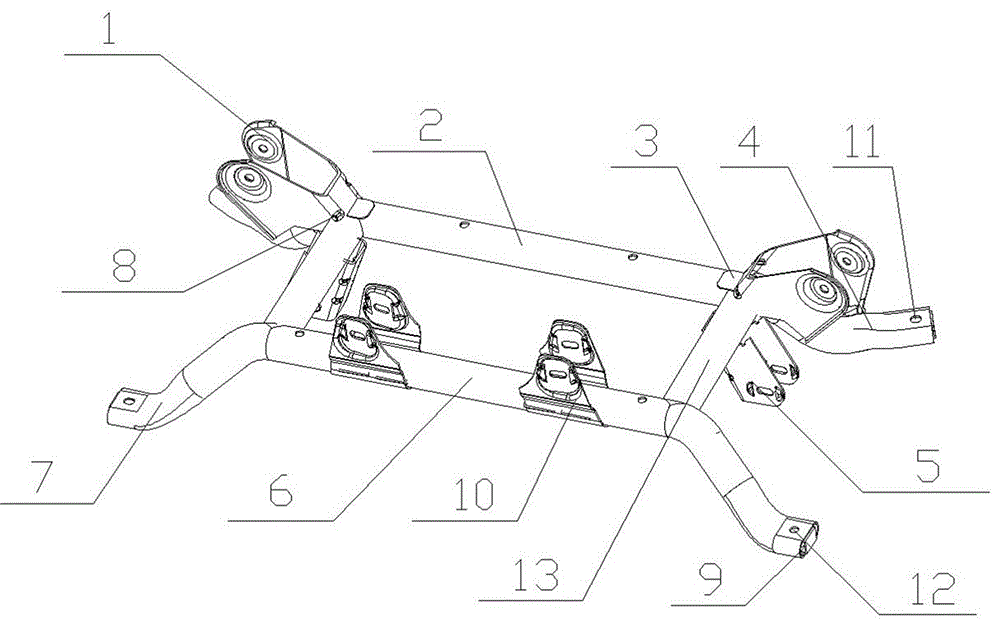
本发明涉及车辆工程领域,尤其涉及一种后副车架总成。
背景技术:
:随着生活水平的提高,人们越来越多的购买了汽车作为代步工具,而汽车上都安装了悬挂,保证车辆行驶在凹凸不平路面上不产生侧倾。汽车悬挂有独立悬挂和非独立悬,独立悬挂需要通过副车架将悬挂与车桥和车身连接,具有阻隔振动和噪声的作用。现有技术中,后副车架总成各梁之间通过焊接方式连接,所以梁之间的强度需要靠焊接强度来保证,同时在车辆颠簸过程中,后副车架与车身和车桥连接的部位变形量较大,容易造成下拉杆变形。技术实现要素:本发明针对上述
背景技术:
中的情况,提供了一种后副车架总成,通过局部优化大大降低了后副车架焊接部位的应力集中,同时通过增加加强板提高了下拉杆的刚度。为了解决上述技术问题,本发明通过下述技术方案得以解决:一种后副车架总成,包括第一横梁、第二横梁、两个纵梁以及若干支架,所述第一横梁与所述第二横梁两端侧边通过所述纵梁固定连接,所述第一横梁两端固定连接有第一摆臂,所述第二横梁两端固定连接有第二摆臂,所述第一摆臂另一端上设有第二螺纹孔,所述第一摆臂内固定连接有加强板,所述第二摆臂另一端上设有第一螺纹孔,所述第二摆臂内也固定连接有加强板,所述第一横梁上还固定有第三支架,所述纵梁上固定连接有第二支架,所述第二横梁上固定有第一支架,所述第一支架还与所述纵梁固定连接,所述第二横梁与所述第一支架间还固定有翻边板,所述第一支架与所述纵梁连接部位上设有凹坑。优选的,所述第一横梁、第二横梁和2个纵梁都为圆柱形。优选的,所述第一摆臂和第二摆臂都为2个,所述第一摆臂和第二摆臂一端为圆形分别与所述第一横梁和第二横梁固定连接,所述第一摆臂和第二摆臂另一端上下边水平,左右边为圆弧形。优选的,所述加强板为口字型,所述加强板有4个。优选的,所述第三支架有2个,对称固定在第一横梁上。优选的,所述翻边板长度为30mm。优选的,所述凹坑深度大于3mm,且小于5mm。优选的,上述固定连接都为焊接。当车辆行驶在颠簸路面时,汽车的车轮会随着地面的凹凸起伏一起运动,进而对整个车体产生振动,当车轮受到向上的力的作用时,进而与车轮悬挂铰接的副车架也受到向上的力的作用,由于车辆为独立悬挂,其副车架两端受力相互影响不大,即一边受力时另一边受力不明显,此时副车架上第一支架受到向上的倾覆力矩,此时第一支架与第二横梁和纵梁焊接部位应力集中较大,同时第二摆臂与车身连接,在第一支架倾覆力矩的作用下,第二摆臂会产生形变,进而影响了车身整体的隔振效果,所以在第二横梁与第一支架的连接位置固定连接翻边板,当第一支架受到倾覆力矩时,翻边板增加了第二横梁与第一支架之间焊接强度,进而将应力集中转移到翻边板前端,同时在纵梁与横梁焊接部位开设凹坑,可通过当倾覆力矩产生时,增加焊接部位的局部形变来进一步的降低应力集中,但凹坑的尺寸不能过大,过大会降低焊接部位的焊接强度。本发明的有益效果:通过增加翻边板和凹坑,将焊接部分的应力集中进行偏移的同时再进行降低,通过摆臂内增加加强板,降低了摆臂受力的变形量,大大提高了摆臂的下拉刚度。附图说明图1是本发明的示意图。图2是本发明的正视图。图3是本发明加强板示意图。图4是现有技术仿真结果示意图。图5是本发明的仿真结果示意图。图中:第一支架1、第二横梁2、翻边板3、第二摆臂4、第二支架5、第一横梁6、第一摆臂7、凹坑8、加强板9、第三支架10、第一螺纹孔11、第二螺纹孔12、纵梁13。具体实施方式以下将结合附图对本发明各实施例的技术方案进行清楚、完整的描述,显然,所描述的实施例仅仅是本发明的一部分实施例,而不是全部实施例。基于本发明中所述的实施例,本领域普通技术人员在不需要创造性劳动的前提下所得到的所有其它实施例,都在本发明所保护的范围内。实施例如图1至图5所示,一种后副车架总成,包括第一横梁6、第二横梁2、两个纵梁13以及若干支架,所述第一横梁6与所述第二横梁2两端侧边通过所述纵梁13固定连接,所述第一横梁6两端固定连接有第一摆臂7,所述第二横梁2两端固定连接有第二摆臂4,所述第一摆臂7另一端上设有第二螺纹孔12,所述第一摆臂7内固定连接有加强板9,所述第二摆臂4另一端上设有第一螺纹孔11,所述第二摆臂4内也固定连接有加强板9,所述第一横梁6上还固定有第三支架10,所述纵梁13上固定连接有第二支架5,所述第二横梁2上固定有第一支架1,所述第一支架1还与所述纵梁13固定连接,所述第二横梁2与所述第一支架1间还固定有翻边板3,所述第一支架1与所述纵梁13连接部位上设有凹坑8。优选的,所述第一横梁6、第二横梁2和2个纵梁13都为圆柱形。优选的,所述第一摆臂7和第二摆臂4都为2个,所述第一摆臂7和第二摆臂4一端为圆形分别与所述第一横梁6和第二横梁2固定连接,所述第一摆臂7和第二摆臂4另一端上下边水平,左右边为圆弧形。所述加强板9为口字型,所述加强板9有4个。所述第三支架10有2个,对称固定在第一横梁6上。所述翻边板3长度为30mm。所述凹坑8深度大于所述纵梁13和所述第一支架1厚度。上述固定连接都为焊接。具体的仿真过程:模拟汽车行驶在凸起公路上的情况,通过ansys有限元软件来分析后副车架总成的静力学特性。先建立后副车架总成的模型如图4所示,图4为未优化的后副车架总成模型,图5为本发明的后副车架总成简化模型。定义材料属性:后副车架总成整体常用材料高强钢,杨氏模量e=2.1×105n/mm2,泊松比ε=0.3,密度ρ=7.89×10-3g/mm3。划分网格:对后副车架总成中结构较为平整的区域使用六面体网格,对各连接部分使用四面体网格。施加约束:模拟汽车行驶过程的颠簸情况,当车轮与障碍物接触时,障碍物对车轮施加一个反作用力,即对模型中f面施加向上的力f=2400n的力,在4个摆臂的端面a、b、c和d都施加固定约束,以模拟后副车架与车身的固定,限制后副车架总成的平动和转动。运算求解:通过有限元计算结果显示,未优化前最危险部位出现在h部位,其最大应力为169.91mpa,最大形变部位出现在e部位,其最大变形量为4.256mm;然后针对上述分析结果进行优化,多次优化的部分结果如下表:表1加强板对摆臂变形量的影响是否增加加强板最大应力/mpa扭力梁变形量/mm否169.914.256是167.423.618表2翻边板对应力集中的影响翻边板长度/mm最大应力/mpa扭力梁变形量/mm20149.624.13230148.754.11340148.424.095表3凹坑深度对应力集中的影响凹坑深度/mm最大应力/mpa扭力梁变形量/mm2158.424.1893153.674.1754152.554.1715153.484.1746157.824.185通过上述的优化数据可知,是否增加加强板对摆臂的变形量有显著影响,对应力集中影响不大;翻边板的长度和凹坑的深度都对焊接部位的应力集中有显著影响,对摆臂的变形量影响不大;将上述最优参数共同带入有限元软件,计算得到最危险部位出现在k部位,其最大应力为138.64mpa,此时e部位最大应力132.15mpa,摆臂的最大变形量为3.576mm。相比较未优化前,优化后最危险位置出现了偏移,将最危险位置从第二横梁与纵梁焊接位置向第二横梁中间靠近,位于翻边板前端,同时在凹坑的共同作用下,h部位的应力降低了22.22%,大大的提高了焊接部位的安全性;同时加强板的增加,将摆臂的变形量降低了16%,大大提高了摆臂的下拉刚度。当前第1页12