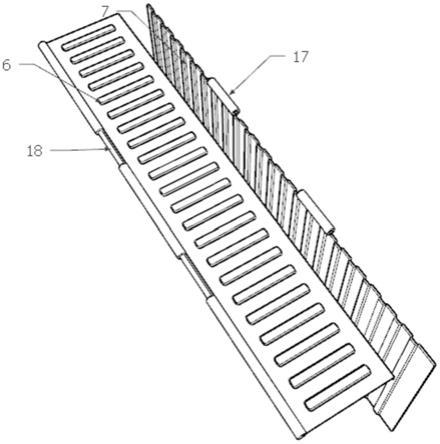
1.本实用新型涉及运输设备技术领域,尤其涉及一种用于运输沥青混合料及水泥混凝土的保温保湿自卸车。
背景技术:2.铺筑高品质的路面一直是道路工作者所追求的目标。严格控制沥青混合料的施工温度和保证水泥混凝土的湿度,是铺筑高品质的沥青路面和水泥路面的关键。自卸车运输道路建筑材料的过程中,面临着沥青混合料热量散失、水泥混凝土水分散失等问题。目前,沥青混合料保温运输技术只适用于短距离运输,现有技术在沥青混合料运输车车箱内部的四周和底部均安设保温板,同时在运输车的顶部覆盖棉絮和隔热防水的雨篷,但在实际运输中,易发生保温板折断、滑动的情况,在顶部覆盖的棉絮和隔热防水的雨篷也会因雨雪而发生破损,这种保温措施缺乏使用的耐久性和密封性,甚至直接影响沥青路面的使用性能。传统的水泥混凝土自卸车,其结构缺乏密封性,在运输水泥混凝土的过程中,上层混凝土水分不断蒸发,部分混凝土凝结成块,导致施工质量下降。此外,采用铰链连接的车门在使用的过程中,易发生铰链生锈、磨损、断裂等问题。
技术实现要素:3.针对上述现有技术中存在的不足,本实用新型提供一种用于运输沥青混合料及水泥混凝土的保温保湿自卸车。
4.本实用新型是通过如下技术方案来实现的:
5.一种用于运输沥青混合料及水泥混凝土的保温保湿自卸车,包括运输车体、自卸车车箱、液压升降机,所述自卸车车箱包括连接槽、车箱板、固定装置、车前框、车后框,所述车箱板包括可活动的车箱板和不可活动的车箱板,所述可活动的车箱板包括车箱顶板、车箱后板,车箱顶板包括车箱顶右板、车箱顶左板,所述不可活动的车箱板包括车箱左板、车箱右板、车箱底板、车箱前板。自卸车车箱为双层密闭结构,所述车箱板包括金属里板、金属外板和填充在二者之间的泡沫混凝土填充层。
6.所述可活动的车箱板与不可活动的车箱板之间通过连接金属杆、连接金属管转动密闭连接,多个连接金属杆等间距的焊接在可活动的车箱板长边边缘处,所述连接金属管包括半圆形的上半管和半圆形的下半管,所述下半管焊接在不可活动的车箱板长边边缘处,位置与连接金属杆的位置一致,所述上半管焊接在下半管上,二者相互配合形成可容纳连接金属杆转动的空间;所述连接金属管的内径与连接金属杆的直径相同,连接金属管的长度与连接金属杆的长度相同。
7.车箱顶右板和车箱右板、车箱后板和车箱底板的连接方式与车箱顶左板和车箱左板的连接方式相同。
8.优选地,在车箱顶左板和车箱左板的连接处以及车箱顶右板和车箱右板的连接处,所述连接金属杆的直径为60mm,长度为700mm,焊接在可活动的车箱板长边边缘三等分
点处,两个三等分点各焊接一个;所述连接金属管的外径为120mm,内径为60mm,长度为700mm。在车箱后板和车箱底板的连接处,所述连接金属杆的直径为52mm,长度为260mm,焊接在车箱后板短边边缘四等分点处,三个四等分点各焊接一个;所述连接金属管的外径为72mm,内径为52mm,长度为260mm。
9.优选地,所述车箱顶左板与车箱顶右板衔接面具有同方向倾斜角度,斜度均为40
°
,车箱顶左板和车箱顶右板嵌在车前框和车后框内,闭合状态下,车箱顶左板和车箱顶右板衔接面完全重合,通过相互盖合形成密闭平面。车前框和车后框上设有凸缘,闭合状态下,车箱顶右板、车箱顶左板与车箱底板平行。这些结构设计可以保证车箱顶部的密封性。
10.优选地,所述车箱后板上端与车后框通过固定装置连接,所述固定装置包括固定装置上部分和固定装置下部分,固定装置上部分焊接在车后框上,固定装置上部分内部焊接有一片弹簧片用于固定铁环,铁环在固定装置上部分内部可以上下旋转180
°
,固定装置下部分焊接在车箱后板上端。铁环统一朝上时,可以打开车箱后板;将车箱后板关闭后,拉下所有铁环,使其统一朝下,可确保车箱后部的密封性。
11.优选地,所述金属里板的厚度为0.5cm,所述泡沫混凝土填充层的厚度为3cm,所述金属外板的厚度为0.5cm。按照混合料的表观密度为3000kg/m3计算,所制备的泡沫混凝土强度应不小于1mpa,且所制得的强度等级应符合jgt 266
‑
2011《泡沫混凝土标准》规范。
12.优选地,所述运输车体包括连接板,连接板包括上板、连接轴、下板,上板与车箱底板连接,连接轴将上板和下板连接在一起,下板连接在运输车体车盘二分之一处。在卸料的过程中,液压升降机顶起自卸车车箱,连接板连接车箱底板和运输车体车盘,减小自卸车车箱的抖动,使自卸车车箱受力更加均匀。
13.与现有技术相比,本实用新型具有如下有益效果:
14.1.本实用新型自卸车车箱采用双层密闭结构,层间填充泡沫混凝土材料,泡沫混凝土热传导系数小,且具有一定的承载能力,能起到很好的保温和保湿作用,适用于运输沥青混合料和水泥混凝土。
15.2.自卸车在运输道路建筑材料的过程中,层间填充泡沫混凝土,可以减缓运输材料对自卸车车箱的冲击力,延长整个自卸车车箱的使用寿命。
16.3.升降技术方面,在卸料的过程中,本实用新型的连接板,连接车箱底板和运输车体车盘,减小自卸车车箱的抖动,使自卸车车箱受力更加均匀。
17.4.在车箱顶左板与车箱左板、车箱顶右板与车箱右板、车箱后板与车箱底板的连接处,连接金属管的外径、内径、长度,连接金属杆的直径、长度,焊接方式以及开关方式提高了整个自卸车车箱的密封性和保温保湿性能。
附图说明
18.图1是本实用新型运输车体示意图;
19.图2是本实用新型自卸车车箱整体示意图;
20.图3是本实用新型自卸车车箱后部示意图;
21.图4是本实用新型自卸车车箱底部示意图;
22.图5是本实用新型自卸车车箱侧面示意图;
23.图6是本实用新型车箱左板内部结构示意图;
24.图7是本实用新型卸料示意图;
25.图8是本实用新型填料示意图;
26.图9是本实用新型车箱顶左板焊接方式及工作原理示意图;
27.图10是本实用新型车箱左板焊接方式及工作原理示意图;
28.图11是本实用新型焊接好的车箱顶左板开关方式示意图;
29.图12是本实用新型车箱顶左板与车箱顶右板衔接闭合示意图;
30.图13是本实用新型车箱顶右板与车前框、车后框接触示意图;
31.图14是本实用新型车箱后板的闭合状态示意图;
32.图15是本实用新型车箱后板的打开状态示意图;
33.图16是本实用新型车箱后板焊接方式及工作原理示意图;
34.图17是本实用新型的等轴视图;
35.图18是本实用新型的俯视图;
36.图19是本实用新型的前视图;
37.图20是本实用新型的右视图;
38.图21是本实用新型的后视图;
39.图22是本实用新型的左视图;
40.图23是本实用新型中固定装置上部分示意图;
41.图24是本实用新型中铁环朝上时固定装置示意图。
42.图中,1液压升降机、2前轴、3后轴、4连接槽、5车箱顶右板、6车箱顶左板、7车箱左板、8车箱右板、9固定装置、10车箱后板、11车箱底板、12车箱前板、13金属里板、14泡沫混凝土填充层、15金属外板、16连接板、17连接金属管、18连接金属杆、19弹簧片、20铁环、21固定装置上部分、22固定装置下部分、23车前框、24车后框、25上板、26连接轴、27下板。
具体实施方式
43.下面结合实施例及附图详细叙述本实用新型的技术方案,并不用于限定本技术的保护范围。
44.运输车体采用编号为4类,3轴整体式货车(非双前轴),类型为15型,其前轴2采用单轴形式(每侧单轮胎),后轴3采用双联轴形式(每侧双轮胎)。运输车体的轴载及质量限值应满足gb 1589
‑
2016《汽车、挂车及汽车列车外廓尺寸、轴载及质量限值》的要求,如表1所示:
45.表1汽车及挂车单轴、二轴组及三轴组的最大允许轴荷限制单位为千克
[0046][0047]
运输车体包括连接板16,连接板16包括上板25、连接轴26、下板27,上板25与车箱底板11连接,连接轴26将上板25和下板27连接在一起,下板27连接在运输车体车盘二分之一处。在卸料的过程中,液压升降机1顶起自卸车车箱,连接板16连接车箱底板11和运输车体车盘,减小自卸车车箱的抖动,使自卸车车箱受力更加均匀。
[0048]
自卸车车箱根据20英尺集装箱改装,它的尺寸参考20英寸集装箱的长度、宽度、高度进行设计,20英尺集装箱外尺寸为6.1m*2.44m*2.59m,本实施例中自卸车车箱外尺寸为:7m*2.5m*3m。
[0049]
自卸车车箱包括连接槽4、固定装置9、车箱顶右板5、车箱顶左板6、车箱后板10、车箱左板7、车箱右板8、车箱底板11、车箱前板12、车前框23、车后框24。
[0050]
车箱顶左板6与车箱左板7之间通过连接金属管17和连接金属杆18转动密闭连接,连接金属管17包括半圆形的上半管和半圆形的下半管。在车箱顶左板6边缘三等分点处,切割下长度为700mm的一段,用于焊接直径为60mm、长度为700mm的连接金属杆18,两个三等分点各焊接一个。连接金属管17外径为120mm、内径为60mm、长度为700mm。连接金属管17的内径与连接金属杆18的直径相同,连接金属管17的长度与连接金属杆18的长度相同。在焊接时,先将下半管,焊接到车箱左板7顶部三等分点处,两个三等分点各焊接一个。然后,将连接金属杆18表面和连接金属管17内侧打磨光滑,将车箱顶左板6所焊接的连接金属杆18,放
置在车箱左板7所焊接下半管内侧,最后把上半管和下半管焊接到一起。
[0051]
车箱顶右板5和车箱右板8的连接方式与车箱顶左板6和车箱左板7的连接方式相同。
[0052]
车箱后板10和车箱底板11的连接处,连接金属杆18焊接在车箱后板10短边边缘四等分点处,三个四等分点各焊接一个,连接金属杆18的直径为52mm、长度为260mm。连接金属管17焊接在车箱底板11短边边缘四等分点处,三个四等分点各焊接一个,连接金属管17的外径为72mm、内径为52mm、长度为260mm。其他与车箱顶左板6和车箱左板7的连接方式相同。
[0053]
车箱顶左板6与车箱顶右板5衔接面具有同方向倾斜角度,斜度均为40
°
,闭合车箱顶板时,先闭合车箱顶右板5,再闭合车箱顶左板6,保证车箱顶左板6和车箱顶右板5衔接面完全重合。车前框23和车后框24上设有凸缘,车箱顶右板5闭合后,可以使车箱顶右板5与车箱底板11平行。同样,闭合车箱顶左板6时,车箱顶右板5、车前框23、车后框24可以使车箱顶左板6与车箱底板11平行。这些结构设计可以保证车箱顶部的密封性。
[0054]
车箱后板10上端与车后框24通过固定装置9连接,固定装置9包括固定装置上部分21和固定装置下部分22,固定装置上部分21焊接在车后框24上,固定装置上部分21内部焊接有一片弹簧片19用于固定铁环20,铁环20在固定装置上部分21内部可以上下旋转180
°
,固定装置下部分22焊接在车箱后板10上端。铁环20统一朝上时,可以打开车箱后板10;将车箱后板10关闭后,拉下所有铁环20,使其统一朝下,可确保车箱后部的密封性。
[0055]
车箱顶右板5、车箱顶左板6、车箱左板7、车箱右板8、车箱后板10、车箱底板11、车箱前板12的结构相同,均包括金属里板13、金属外板15和填充在二者之间的泡沫混凝土填充层14,自卸车车箱为双层密闭结构。金属里板13的厚度为0.5cm,泡沫混凝土填充层14的厚度为3cm,金属外板15的厚度为0.5cm。按照混合料的表观密度为3000kg/m3计算,所制备的泡沫混凝土强度应不小于1mpa。
[0056]
泡沫混凝土填充层14的主要组成为无机胶凝材料。在无机胶凝材料中,掺入泡沫,均匀搅拌混合料,冷凝后形成气孔结构的轻质材料就是泡沫混凝土。泡沫混凝土隔热保温性能好,自卸车在运输沥青混合料或水泥混凝土的过程中,可以很好的保证自卸车车箱内部沥青混合料或水泥混凝土的温度和湿度。泡沫混凝土的密度、延性在冲击荷载方面也有很大优势,是很好的减震材料。同时,泡沫混凝土填充层14还是自卸车车箱的承重结构。
[0057]
石锦炎等(《不同温度下泡沫混凝土热物理性能的研究》,工程热物理学报:第41卷第7期)所提出泡沫混凝土的制作原料与方案,为本实施例泡沫混凝土填充层14制作方法的依据。
[0058]
本实施例泡沫混凝土填充层14所采用的水泥原料为42.5级普通硅酸盐水泥,其比表面积为345.00m2/kg,28d抗压强度为46.2mpa。粉煤灰:河南荣昌盛净水材料厂提供的ⅰ级粉煤灰,密度为2.1g/cm3.eps颗粒:粒径为2~4mm,密度为18.8kg/m3,常温导热系数为0.0313w/(m
·
k)。发泡剂为:浓度30%的过氧化氢溶液,使用硬脂酸钙作为稳定泡剂、亚硝酸钠作为早强剂、丙烯酸酯共聚乳液作为增稠剂粘结剂,水为自来水。在确定基准配比之后,加入体积分数为25%的eps颗粒。本专利中涉及泡沫混凝土的制作原料以及方法应符合jgt266
‑
2011《泡沫混凝土标准》。
[0059]
本实施例泡沫混凝土填充层14制备工艺如下:
[0060]
1.将水泥、粉煤灰和其它固体材料搅拌均匀。
[0061]
2.向搅拌好的固体材料中,倒入2/3的水和增稠剂,并将表面润湿的eps颗粒倒入其中(eps颗粒体积分数为25%)。
[0062]
3.使用水泥净浆搅拌机,搅拌1min,控制浆料的温度为25℃。
[0063]
4.搅拌完成后,加入早强剂,低速搅拌30s,高速搅拌10s,最后倒入发泡剂搅拌10s。
[0064]
5.搅拌完成后,将浆体迅速倒入车箱顶右板5、车箱顶左板6、车箱左板7、车箱右板8、车箱后板10、车箱底板11、车箱前板12的金属里板13和金属外板15之间,在20℃下静止24h,待其内的泡沫混凝土具有一定强度后,再进行标准养护。
[0065]
此外,在制作自卸车车箱的过程中,为了满足更轻质、更高的比热容、更低的热扩散系数等要求,可以在泡沫混凝土填充层14制作的原料中,掺入体积百分数为25%到30%eps高分子有机材料,以此来代替其它掺合料。
[0066]
石锦炎等研究得出,当eps体积分数为25%~35%时,制备的泡沫混凝土性能相对兼备轻质、低导热、高比热和低热扩散系数的特性。随着eps颗粒加入量增大,泡沫混凝土内部的孔隙率会增大,力学性能会随之降低。因为泡沫混凝土填充层14起到承重作用,所以在本实施例中,选择加入体积分数为25%的eps。
[0067]
下面结合附图对自卸车做详细的工作描述:
[0068]
(1)自卸车到达指定的加料点,驾驶员打开车箱顶右板5和车箱顶左板6,使自卸车呈现图8状态,方便加料。
[0069]
(2)加料完成之后,驾驶员关闭车箱顶右板5和车箱顶左板6,将拌合好的混合料运输至施工现场。在运输的过程中,整个自卸车车箱呈封闭状态,以减少混合料在运输过程中的热量和水分散失。在车箱顶右板5、车箱顶左板6、车箱左板7、车箱右板8、车箱后板10、车箱底板11、车箱前板12内部填灌的泡沫混凝土14对混合料起到保温作用。
[0070]
(3)在自卸车到达施工现场之后,打开车箱后板10,驾驶员通过控制液压升降机1顶起自卸车车箱,使自卸车呈现图7状态,将自卸车车箱中的混合料卸至规定的摊铺机或搅拌机前。
[0071]
(4)经过以上三个步骤,自卸车完成混合料的整个运输过程。驾驶员通过控制液压升降机1和连接板16,使自卸车车箱下降,缓慢的恢复至原位,使自卸车呈现图15状态。关闭车箱后板10,驾驶员驾驶自卸车至混合料生产现场,重复上述操作。
[0072]
本实用新型未述及之处适用于现有技术。