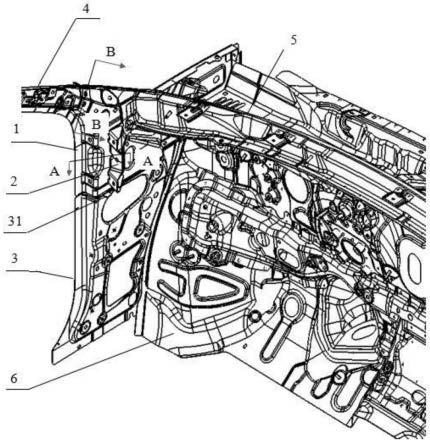
一种汽车车体a柱区域结构及车辆
技术领域
1.本发明涉及汽车车身技术领域,尤其涉及一种汽车车体a柱区域结构及车辆。
背景技术:2.随着汽车使用工况的增加以及搭载部件的增多,对白车身的性能要求越来越高。a柱下内板下部的节点位置对白车身扭转刚度贡献量很大,因此更多的车辆会将a柱下内板下部延伸至地板门槛下边缘,与侧围加强板和地板焊接,但该种方案,对一些地板平台来说,a柱下内板下部延伸到门槛下边缘会导致地板平台的某些关键焊点无法焊接。
3.为此,授权公告号为cn211252778u的专利公开了一种a柱下内板总成及汽车,a柱下内板总成包括下内板本体和刚度补偿结构,下内板本体的上端被配置为与a柱的底端连接,下内板本体的下端被配置为与地板总成的门槛上边缘连接,刚度补偿结构的上端与下内板本体的下端连接,刚度结构的下端被配置为与地板总成的门槛下边缘连接。该技术方案的a柱下内板总成采用分体结构,并将下内板本体和刚度补偿结构顺序焊装,在满足地板总成焊接工艺要求的同时,实现白车身壳体扭转刚度提升约5%,达成性能目标。
4.但由于某些车企平台化研究开发时间比较晚,工艺流程不统一,尤其a柱区域,a柱内板所属层级一般分为侧围总成和机舱总成两种情况,但随着焊接生产线体柔性化程度越来越高,平台化车型和传统车型因a柱内板流程不统一但要求共线生产情况越来越多,上述a柱总成在实际运用过程中就会不存在如下问题:1、此种结构无法适应a柱内板流程不统一车型的柔性共线生产,需新增工序,重新示教柔性上其他车型轨迹,改造代价大,调试时间周期长;2、焊接主线侧围预装后,传输过程中侧围总成上部因重力原因有一定比例会外翻掉落,造成生产线停线,影响生产线效率。3、a柱内板总成上转向支撑安装支架层级多,且y向不可调,而该支架上转向支撑定位孔直接影响转向支撑与门内饰板的间隙,该间隙敏感度高,影响精致工程感官质量。4、平台车型为适应不同轴距的变化,前壁板与前地板总成分缝更靠前,现有结构a柱内板总成会影响分缝处焊点的焊接通道。5、a柱内板上端与其他内板连接处因搭接间隙不易控制,弧焊质量难以保证,且弧焊操作人机工程差。
技术实现要素:5.有鉴于此,本发明的目的是提供一种汽车车体a柱区域结构及车辆,能够满足a柱内板流程不统一车型的柔性共线生产,规避焊接线侧围预装后传输过程掉落的问题;提升转向支撑定位安装点的尺寸精度,解决平台车型前壁板与前地板总成分缝处焊点因前移带来的焊接通道不可达的问题。
6.本发明通过以下技术手段解决上述技术问题:
7.一种汽车车体a柱区域结构,包括a柱下内板,还包括a柱上内板、a柱中内板、转向支撑安装支架、暖风机压力室板和前壁板,所述转向支撑安装支架与a柱中内板固定连接,所述a柱中内板的中部与暖风机压力室板和前壁板固定连接;所述a柱中内板与a柱上内板螺栓连接,所述a柱中内板与a柱下内板搭扣配合连接。
8.进一步,所述a柱中内板与a柱下内板的搭扣配合连接处位于汽车车体a柱区域结构的上部位置。本技术方案如此的结构设计,通过a柱中内板跟随前壁板集成在机舱总成上,a柱下内板集成在侧围分总成上,来适应a柱内板所属上下车体不同工艺流程的焊接柔性线,实现a柱中内板后工序组焊时再定位,从而提升焊接层级的需求,来满足平台车型前壁板分缝处焊点焊接时的通道需求。
9.进一步,所述a柱中内板与与暖风机压力室板和前壁板的固定连接处设置有点焊密封胶。本技术方案在a柱中内板与与暖风机压力室板和前壁板的固定连接处设置有点焊密封胶可以起到密封的作用,防止漏水。
10.进一步,所述a柱中内板上设置有三角形凸台。本技术方案,通过三角形凸台的设置,可在提高a柱中内板强度的同时,弥补暖风机压力室板缺口大带来的密封不良问题,这样的结构设计,结构简单,成型方便,实用性强。
11.进一步,所述a柱中内板包括a柱中内板片件,所述转向支撑安装支架y向安装在a柱中内板片件上,所述转向支撑安装支架包括转向支撑定位片件和转向支撑分总成,所述转向支撑定位片件与转向支撑分总成上设置有转向支撑定位孔,所述转向支撑定位片件与转向支撑分总成x向连接。本技术方案中,转向支撑安装支架与a柱中内板片件采用y向连接,利用焊接工装可实现转向支撑定位孔的x/z向可调,而转向支撑定位片件与转向支撑分总成采用x向连接,利用焊接工装可实现转向支撑定位孔的y/z向可调。
12.进一步,所述a柱中内板的上部设置有z向翻边。本技术方案的z向翻边可以采用特殊公差设计,这样的设计,能够优化a柱中内板与周边零件焊接时的z向尺寸公差累计,最终实现白车身层级转向支撑定位孔的尺寸精度。
13.进一步,所述a柱下内板的上部设置有l型缺口,位于l型缺口处的a柱下内板上设置有搭扣,所述搭扣两侧的a柱下内板上设置有工艺缺口。本技术方案在a柱下内板的上部设置l型缺口,便于a柱下内板与a柱中内板“合拢”过程的避让,如此的结构设计,能够降低a柱下内板的制造难度,规避焊接通道困难而又不必要的连接工艺设计;在a柱下内板上部位置设置搭扣,搭扣两侧设置工艺缺口,在侧围总成与下车体预装时,通过自动滚压或人工往上敲击的方式,使搭扣与a柱中内板贴合,破解侧围总成预装时中上部无约束的难题,从而规避焊接线侧围预装后传输过程掉落问题,提高生产效率。
14.进一步,所述a柱上内板上开设有第一螺纹孔和第二螺纹孔,所述a柱中内板上开设有与第一螺纹孔匹配的第一过孔,以及与第二螺纹孔匹配的第二过孔,所述第一螺纹孔与第一过孔上螺纹连接有第一螺栓,所述第二螺纹孔与第二过孔上螺纹连接有第二螺栓。本技术方案如此的结构设计,可以避免a柱中内板与a柱上内板连接的人机工程性差的问题,提升操作效率。
15.本发明还公开了一种车辆,所述车辆包括了上述的汽车车体a柱区域结构。
16.本发明的一种汽车车体a柱区域结构及车辆,具有如下优点:
17.1、本发明的a柱中内板与a柱下内板的连接处位于汽车车体a柱区域结构的上部,这样的分缝结构形式,解决了平台车型前壁板与前地板分缝太靠前带来的无焊接通道的问题,可以低成本高效的实现a柱内板流程不统一车型的柔性共线生产。
18.2、本发明在a柱下内板的上部设置有l型缺口,位于l型缺口处的a柱下内板上设置有搭扣,以新增a柱下内板上部搭扣的结构形式,可以解决侧围中上部预装不稳的问题,提
高生产效率。
19.3、本发明通过将转向支撑安装支架y向安装在a柱中内板片件上,转向支撑定位片件与转向支撑分总成上设置转向支撑定位孔,转向支撑定位片件与转向支撑分总成x向连接,实现转向支撑定位孔三个方向可调,通过a柱中内板先弱预固化再定位的方式提升焊接层级,确保白车身层级转向支撑定位孔的尺寸精度。
20.4、本发明通过第一螺栓和第二螺栓实现a柱上内板与a柱中内板的螺栓连接方式,可以避免a柱中内板与a柱上内板连接的人机工程性差的问题,提升操作效率。
附图说明
21.图1为本发明一种汽车车体a柱区域结构的结构示意图;
22.图2为本发明一种汽车车体a柱区域结构的过程结构示意图;
23.图3为本发明一种汽车车体a柱区域结构的过程结构与前地板连接示意图;
24.图4为本发明一种汽车车体a柱区域结构的过程结构与侧围分总成连接示意图;
25.图5为本发明一种汽车车体a柱下内板上部搭接区域的局部图;
26.图6为图1中a-a处的剖面图;
27.图7为图1中b-b处的剖面图。
28.主要元件符号说明如下:
29.a柱中内板1、第一螺栓11、第二螺栓12、a柱中内板片件13、三角形凸台14、z向翻边15、转向支撑安装支架2、转向支撑定位片件21、转向支撑分总成22、转向支撑定位孔211、a柱下内板3、搭扣31、l型缺口32、a柱上内板4、暖风机压力室板5、前壁板6、前地板7、侧围分总成8。
具体实施方式
30.以下将结合附图和具体实施例对本发明进行详细说明:
31.以下通过特定的具体实施例说明本发明的实施方式,本领域技术人员可由本说明书所揭露的内容了解本发明的优点和功效。需要说明的是,以下实施例中所提供的图示仅用于示例性说明,表示的仅是示意图,而非实物图,不能理解为对本发明的限制,为了更好地说明本发明的实施例,图中某些部件会有省略、放大或缩小,并不代表实际产品的尺寸;对本领域技术人员来说,图中某些公知结构及其说明可能省略是可以理解的。
32.本发明实施例的图中相同或相似的标号对应相同或相似的部件,在本发明的描述中,需要理解的是,若有术语“上”、“下”、“左”、“右”、“前”、“后”等指示的方位或位置关系为基于图所示的方位或位置关系,仅是为了便于描述本发明和简化描述,而不是指示或暗示所指的装置或元件必须具有特定的方位、以特定的方位构造和操作,因此图中描述位置关系的用语仅用于示例性说明,不能理解为对本发明的限制,对于本领域的普通技术人员而言,可以根据具体情况理解上述用语的具体含义。
33.实施例1、
34.本实施例为一种汽车车体a柱区域结构,如图1和图2所示,包括a柱中内板1、转向支撑安装支架2、暖风机压力室板5和前壁板6,a柱中内板1与暖风机压力室板5和前壁板6先采用点焊预固定进行弱连接,并用点焊密封胶实现a柱中内板1与暖风机压力室板5、前壁板
6之间的密封,防止漏水,a柱中内板1设置有三角形凸台14,可提高a柱中内板的强度的同时,弥补暖风机压力室板缺口大带来的密封不良问题。a柱中内板1包括a柱中内板片件13,转向支撑安装支架2与a柱中内板片件13采用y向点焊连接,利用焊接工装可实现转向支撑定位孔211的x/z向可调,转向支撑安装支架2包括转向支撑定位片件21和转向支撑分总成22,如图6所示,转向支撑定位片件21和转向支撑分总成22采用纯x向连接,利用焊接工装可实现转向支撑定位孔211的y/z向可调,a柱中内板1上部一体成型有z向翻边15,本实施例的z向翻边15采用特殊公差设计,这样能够优化a柱中内板与周边零件焊接时的z向尺寸公差累计,最终实现白车身层级转向支撑定位孔211的尺寸精度。
35.如图1所示,a柱中内板1与a柱下内板3的分缝布置在该区域的上部位置,a柱中内板1如图2所示,其先与暖风机压力室板5和前壁板6采用点焊连接,a柱下内板3如图4所示,先与侧围分总成8采用点焊连接,此种结构和工艺流程的设计,能够适应a柱内板所属上下车体不同工艺流程的焊接柔性线,同时也能够解决因平台车型为尽量提高零件的平台通用性,选择如图3所示将前壁板6与前地板7的分缝靠前设计时而大部分焊点通道被遮挡的问题。
36.如图5所示,a柱下内板3左上部设计有l型缺口32,便于a柱下内板3与a柱中内板1“合拢”过程的避让。这样的结构设置,能够降低a柱下内板3的制造难度,规避焊接通道困难而又不必要的连接工艺设计。a柱下内板3上部中间一体成型有搭扣31,搭扣31两侧设置有工艺缺口,在侧围总成与下车体预装时,通过自动滚压或人工往上敲击的方式,使搭扣31与a柱中内板1贴合,破解侧围总成预装时中上部无约束的难题,从而规避焊接线侧围预装后传输过程掉落问题,提高生产效率。
37.如图7所示a柱上内板4上开设有第一螺纹孔和第二螺纹孔,a柱中内板1上开设有与第一螺纹孔匹配的第一过孔,以及与第二螺纹孔匹配的第二过孔,第一螺纹孔与第一过孔上螺纹连接有第一螺栓11,第二螺纹孔与第二过孔上螺纹连接有第二螺栓12。通过如此的结构设计,可以避免a柱中内板1与a柱上内板4连接的人机工程性差的问题,提升操作效率。
38.实施例2、
39.本实施例为一种车辆,该车辆包括了实施例1中的汽车车体a柱区域结构。该车辆的a柱中内板1与a柱下内板3的连接处位于汽车车体a柱区域结构的上部,有效的解决了平台车型前壁板6与前地板7分缝太靠前带来的无焊接通道的问题,可以低成本高效的实现a柱内板流程不统一车型的柔性共线生产。另外,该车辆的a柱下内板3的上部设置有l型缺口32,位于l型缺口32处的a柱下内板3上设置有搭扣31,以新增a柱下内板3上部搭扣31的结构形式,可以解决侧围中上部预装不稳的问题,提高该车辆生产效率。再者,该车辆通过将转向支撑安装支架2y向安装在a柱中内板1片件上,转向支撑定位片件21与转向支撑分总成22上设置转向支撑定位孔211,转向支撑定位片件21与转向支撑分总成22x向连接,实现转向支撑定位孔211三个方向可调,通过a柱中内板1先弱预固化再定位的方式提升焊接层级,确保白车身层级转向支撑定位孔211的尺寸精度。最后,本实施例的车辆通过第一螺栓11和第二螺栓12实现a柱上内板4与a柱中内板1的螺栓连接方式,可以避免a柱中内板1与a柱上内板4连接的人机工程性差的问题,提升了操作效率。
40.以上实施例仅用以说明本发明的技术方案而非限制,尽管参照较佳实施例对本发
明进行了详细说明,本领域的普通技术人员应当理解,可以对本发明的技术方案进行修改或者等同替换,而不脱离本发明技术方案的宗旨和范围,其均应涵盖在本发明的权利要求范围当中。本发明未详细描述的技术、形状、构造部分均为公知技术。