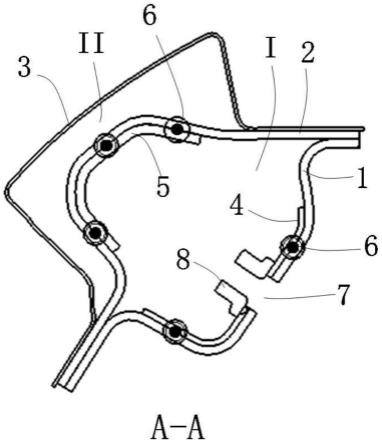
一种a柱总成及具有其的车辆
技术领域
1.本实用新型具体涉及一种a柱总成及具有其的车辆。
背景技术:2.a柱总成通常包括自车内向车外依次设置的a柱内板、a柱加强板和部分的侧围外板;在相关技术中,a柱总成位于驾驶员的左前方,会在车辆行驶过程中遮蔽驾驶员的部分视线(也称形成a柱障碍角),从而增加行车事故的发生率;基于此,在确保a柱总成具有合规的碰撞性能的前提下,尽可能地减小a柱总成的截面尺寸以减小a柱障碍角,能够显著提高行车的安全性,降低事故发生风险,并提升驾驶员的整体视觉体验。
技术实现要素:3.有鉴于此,本实用新型的目的在于提供一种a柱总成及具有其的车辆,此a柱总成在确保a柱碰撞性能的前提下,能拥有较小的截面结构尺寸。
4.本实用新型提供的a柱总成包括a柱内板、a柱加强板、第一补强板和第二补强板,所述a柱内板位于所述a柱加强板的内侧,所述第一补强板和所述第二补强板位于所述a柱内板和所述a柱加强板之间,所述第一补强板与所述a柱内板固定连接,所述第二补强板与所述a柱加强板固定连接。
5.可选地,所述第一补强板和所述第二补强板相互间隔地设置在所述a柱内板和所述a柱加强板之间,所述第一补强板和所述第二补强板分别与所述a柱内板和所述a柱加强板相贴合。
6.可选地,所述a柱内板上设有第一形态区和第二形态区,所述第一形态区用于在车辆上位于所述第二形态区之前,所述a柱内板在所述第一形态区中的横截面宽度大于其在所述第二形态区中的横截面宽度,所述第一形态区与所述第二形态区的交界处用于与车辆的一横梁相接;
7.所述第二补强板具有u型横截面;所述第一补强板具有分别与所述第一形态区和所述第二形态区配合的部分,且其在所述第一形态区内具有一字型横截面,在所述第二形态区内具有u型横截面;在所述第一形态区与所述第一补强板和所述第二补强板相对应的位置中,所述第一补强板和所述第二补强板的开口相对。
8.可选地,所述第一补强板和所述第二补强板分别与所述所述a柱内板和所述a柱加强板焊连;在所述第一补强板的具有u型横截面的部位和所述第二补强板的具有u型横截面的部位上,所述第一补强板和所述第二补强板的底壁和两侧壁上分别存在焊点。
9.可选地,在所述第一补强板的具有u型横截面的部位和/或所述第二补强板的具有u型横截面的部位上,u型横截面的侧壁的高度至少为8mm。
10.可选地,所述a柱总成上设有安装孔,所述安装孔贯穿所述a柱内板和所述第一补强板并用于为车辆附件提供安装点。
11.可选地,所述第一补强板的对应所述安装孔的开设处焊接有固定件,所述固定件
用于与安装车辆附件时需使用的紧固件配合。
12.本实用新型还提供一种车辆,包括如上任一项所述的a柱总成。
13.可选地,包括位于所述a柱加强板外侧的侧围外板,所述侧围外板上设有前车门安装区,所述侧围外板于所述前车门安装区的上方与所述a柱加强板固定连接。
14.可选地,所述侧围外板、所述a柱加强板、所述a柱内板、所述第一补强板和所述第二补强板的前边沿于车辆前部错落布置,所述侧围外板、所述a柱加强板、所述a柱内板、所述第一补强板和所述第二补强板的后边沿在车辆上错落布置。
15.综上所述,通过在a柱总成内设置第一补强板和第二补强板,本实用新型能够提升a柱总成的强度;由于a柱总成的强度得到提升,工程师在a柱总成的强度足以通过相关测试的前提下,能够尽量减小a柱总成的截面尺寸,从而达到减小a柱障碍角,增强行车安全性的目的。经验证,相较于未设置第一补强板和第二补强板的方案,本实用新型结构中的a柱总成的外表面宽度至少能减少5mm。进一步地,由于减小了a柱障碍角,本实用新型还能够提升驾驶员的整体视觉体验。
16.上述说明仅是本实用新型技术方案的概述,为了能够更清楚了解本实用新型的技术手段,而可依照说明书的内容予以实施,并且为了让本实用新型的上述和其他目的、特征和优点能够更明显易懂,以下特举较佳实施例,并配合附图,详细说明如下。
附图说明
17.图1为本实用新型实施例中车辆的部分结构示意图(第一角度)
18.图2为本实用新型实施例中车辆的部分结构示意图(第二角度)
19.图3为本实用新型实施例中车辆的部分结构示意图(第三角度)
20.图4为本实用新型实施例中a柱总成的剖视图
21.图5为本实用新型实施例中a柱内板、第一补强板和横梁处于装配状态的示意图
22.图6为本实用新型实施例中第一补强板和a柱内板在第一形态区中的横截面示意图
23.图7本实用新型实施例中第一补强板和a柱内板在第二形态区中的横截面示意图。
24.附图标记说明
25.1-a柱内板,11-第一形态区,12-第二形态区,2-a柱加强板,3-侧围外板,31-前车门安装区,4-第一补强板,5-第二补强板,6-焊点,7-安装孔,8-固定件,9-横梁;
26.i-第一腔体,ii-第二腔体。
具体实施方式
27.下面结合附图和实施例,对本实用新型的具体实施方式作进一步详细描述。以下实施例用于说明本实用新型,但不用来限制本实用新型的范围。
28.本实用新型的说明书和权利要求书中的术语“第一”、“第二”等是用于区别类似的对象,而不必用于描述特定的顺序或先后次序。
29.如图1到图2所示,本实施例提供一种车辆,该车辆的左前部设有a柱总成,a柱总成包括自车内到车外依次设置的a柱内板1、a柱加强板2以及部分的侧围外板3,其中a柱内板1与a柱加强板2主要通过焊接固定连接,a柱加强板2与侧围外板3主要通过焊接固定连接;特
别地,在a柱内板1和a柱加强板2之间互为相对侧地设有第一补强板4和第二补强板5,如图3和图4所示,a柱内板1与a柱加强板2合围构建出一第一腔体i,a柱加强板2与侧围外板3合围构建出一第二腔体ii,第一补强板4和第二补强板5分别和a柱内板1与a柱加强板2通过焊接固定连接,该第一补强板4和该第二补强板5能够增加a柱总成的整体强度,以确保工程师能在a柱总成的强度足以通过相关测试(例如中保研c-iasi侧正面25%偏置测试)的前提下,尽可能地缩减a柱总成的截面尺寸,从而达到减小a柱障碍角的目的。
30.具体地,侧围外板3上设有用于安装车辆左前门的前车门安装区31,侧围外板3于其位于前车门安装区31上方的框架部分与a柱加强板2相连;在前车门安装区31的上方,a柱加强板2于其前部和中部与侧围外板3固定连接;在a柱加强板2的前部和中部,a柱内板1与a柱加强板2固定连接;在a柱内板1的后部,a柱内板1与车辆的一横梁9固定连接。本实施例中,第一补强板4的截面尺寸和整体体积均小于a柱内板1,第二补强板5的截面尺寸和整体体积均小于a柱加强板2,第一补强板4和第二补强板5分别具有与a柱内板1和a柱加强板2相似的截面形态和相同走向,并能分别与a柱内板1和a柱加强板2紧密贴合,以便分别对a柱内板1和a柱加强板2起补强作用。优选地,第一补强板4和第二补强板5始终相互间隔地位于第一腔体i内,为各自独立互不接触的两个零件,以便能在制备过程中分别成型并与对应的a柱总成的部位相连,同时避免增加a柱总成的制备工艺的复杂性。
31.更优选地,如图5所示,a柱内板1上设有第一形态区11和第二形态区12,其中a柱内板1在第一形态区11内的横截面宽度大于其在第二形态区12内的横截面宽度,第二形态区12位于第一形态区11的前方并为a柱内板1的形成a柱障碍角的区域,同时第一形态区11和第二形态区12的交界之处大致为a柱内板1的与横梁9相连的位置,横梁9在第一形态区11内与a柱内板1相连,以确保a柱内板1的截面尺寸的变化不会在其上形成过于薄弱的区域;如图6和图7所示,由于相对于第二形态区12,a柱内板1在第一形态区11内(因截面尺寸较大而)具有较高的强度,因此第一补强板4与第一形态区11相贴合的部分的横截面大致为一字型,以节省其成型所需材料,同时第一补强板4与第二形态区12相贴合的部分的横截面呈u型,以进一步确保a柱总成在对应第二形态区12的位置的强度和抗扭转性。
32.此外,本实施例中的第二补强板5于长度方向上的任何位置均具有u型的横截面,以确保其自身也具有较高的抗扭转性。需要说明的是,前述设计将使得第一补强板4和第二补强板5在第二形态区12内呈开口相对的形态(见图4),如此,第一补强板4与第二补强板5之间的第一腔体i相当于形成了一个供a柱总成受撞击后溃缩的余量空间,能进一步加强a柱总成受到撞击时的抗扭转性能。
33.更优选地,为了进一步地确保a柱总成在a柱内板1的第一形态区11和第二形态区12的交界之处不会形成过于薄弱的区域,自该交界之处往后,a柱加强板2的截面尺寸大于其与a柱内板1的第二形态区12相对应的部分。
34.请转回参阅图1和图2,本实施例中,第一补强板4的长度约为第二补强板5的二分之一,侧围外板3的前边沿位于a柱加强板2的前边沿之后,a柱内板1的前边沿位于侧围外板3的前边沿之后,第一补强板4的前边沿位于a柱内板1之内,第二补强板5的前边沿位于侧围外板3的前边沿之后、a柱内板1的前边沿之前以及位于a柱加强板2之内,同时a柱内板1的后边沿位于车门安装前31的后边沿之前,a柱加强板2的后边沿位于前车门安装区31之后,第一补强板4的后边沿位于前车门安装区31的上方并位于a柱内板1之内,第二补强板5的后边
沿位于前车门安装区31之后并位于a柱加强板2之内。如此将a柱内板1、a柱加强板2、侧围外板3、第一补强板4和第二补强板5各自的前后边沿错落布置的目的在于,避免车身上出现过于集中的部件分缝区域(也可称拼接区域),从而在a柱总成上形成过分薄弱区域,影响到a柱总成的抗撞击性能和总体强度。
35.进一步地,如图4所示,本实施例中第一补强板4和第二补强板5通过焊接分别与a柱内板1和a柱加强板2相连的具体方案包括:在第一形态区11焊接第一补强板4和a柱内板1时,令具有u型横截面的第一补强板4的底壁和两侧壁上分别存在焊点6,以确保第一补强板4和a柱内板1之间焊连的稳固性;同理,在焊接具有u型横截面的第二补强板5和a柱加强板2时,令具有u型横截面的第二补强板5的底壁和两侧壁上分别存在焊点6,以确保第二补强板5和a柱加强板2之间焊连的稳固性。优选地,为了确保第一补强板4和a柱内板1之间或第二补强板5和a柱加强板2之间的焊连的稳固性,当第一补强板4具有一字型横截面时,其上的焊点6的直径至少为4-6mm;在具有u型横截面的第一补强板4或第二补强板5的底壁或两侧壁上,焊点6直径为至少4-6mm;与之相对地,此时第一补强板4和第二补强板5的侧壁的高度至少为8mm,以提供足够形成焊点6的平台。
36.更进一步地,在a柱总成上还设有数个安装孔7,该安装孔7贯穿a柱内板1和第一补强板4,用于为车辆的附件(例如安全气囊总成,图未示)提供安装点;此外,本实施例于第一补强板4对应安装孔7的开设处还焊连有对应的固定件8(例如螺母),以便使固定件8与车辆对应附件安装时需要用到的紧固件(例如螺栓,图未示)形成配合,从而在车辆附件与a柱总成之间构建出具有高可靠性的紧固结构。
37.此外,在某些可能的实施例中,前述侧围外板3的设计参数包括:厚度为0.65mm,由深冲镀锌钢板dc56d+z制成。前述a柱加强板2的设计参数包括:厚度为1.8mm,由cr950/1300hs as75/75制成。前述第一补强板4的设计参数包括:厚度为1.2mm,由cr950/1300hs as75/75制成。前述第二补强板5的设计参数包括,厚度为1.8mm,由cr950/1300hs as75/75制成。在某些可能的实施例中,第一补强板4和第二补强板5由热成型加工得到。
38.综上所述,通过在a柱总成内设置第一补强板4和第二补强板5,本实用新型能够提升a柱总成的强度;由于a柱总成的强度得到提升,工程师在a柱总成的强度足以通过相关测试的前提下,能够尽量减小a柱总成的截面尺寸,从而达到减小a柱障碍角,增强行车安全性的目的。经验证,相较于未设置第一补强板4和第二补强板5的方案,本实用新型结构中的a柱总成的外表面宽度至少能减少5mm。进一步地,由于减小了a柱障碍角,本实用新型还能够提升驾驶员的整体视觉体验。
39.以上所述,仅为本实用新型的具体实施方式,但本实用新型的保护范围并不局限于此,任何熟悉本技术领域的技术人员在本实用新型揭露的技术范围内,可轻易想到变化或替换,都应涵盖在本实用新型的保护范围之内。因此,本实用新型的保护范围应以所述权利要求的保护范围为准。