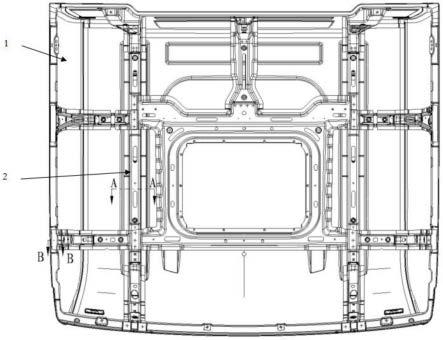
1.本实用新型涉及一种商用车驾驶室顶盖总成,属于车辆驾驶室技术领域。
背景技术:2.汽车驾驶室顶盖是汽车驾驶室的一个重要组成部分,其盖装于汽车驾驶室的上端,用于增大驾驶室头部空间。传统的商用车驾驶室顶盖通常采用金属或者非金属材料制成,金属材料的顶盖总成重量较大,成本较高,模夹检工装投资费用较高,需要较大产线资源支撑;非金属材料的顶盖总成由顶盖本体及安装支架组成,这种非金属顶盖刚强度性能较低,安全性低,破损后维修困难。
技术实现要素:3.本实用新型所要解决的技术问题是针对现有技术存在的缺陷,提供一种新型商用车驾驶室顶盖总成,全新开发的金属顶盖具备更低的成本,更高的结构性能、安全性及便捷的维修性。
4.为解决这一技术问题,本实用新型提供了一种商用车驾驶室顶盖总成,包括顶盖外板总成和顶盖内板总成,所述顶盖外板总成由顶盖左外板、顶盖后外板、顶盖右外板和顶盖前外板拼焊而成,整体呈长方凹型;所述顶盖内板总成为由顶盖前支撑梁上段、顶盖前支撑梁下段总成、顶盖后支撑梁上段、顶盖后支撑梁下段总成、两个顶盖纵梁、以及顶盖前横梁总成、顶盖中后梁和顶盖窗口加强板总成搭接焊接而成的框架形结构,顶盖前支撑梁上段、顶盖前支撑梁下段总成、顶盖后支撑梁上段、顶盖后支撑梁下段总成和两个顶盖纵梁呈井字形设置,顶盖前横梁总成设置在两个顶盖纵梁的前端部,顶盖中后梁设置在顶盖后支撑梁总成中部,顶盖内板总成整体与顶盖外板总成内侧适配、布置在顶盖外板总成的内部,所述顶盖外板总成和顶盖内板总成所有贴合面通过点焊连接。
5.所述顶盖左外板、顶盖后外板、顶盖右外板和顶盖前外板通过焊接搭接边进行点焊连接,其顶部设有天窗开口;所述顶盖左外板、顶盖后外板、顶盖右外板和顶盖前外板上均设置有加强筋。
6.所述顶盖纵梁包括顶盖纵梁前段总成、顶盖纵梁中段总成和顶盖纵梁后段,顶盖纵梁前段总成与顶盖纵梁中段总成搭接边使用四个两层焊焊点连接;顶盖纵梁中段总成和顶盖纵梁后段连接处搭接边使用四个两层焊焊点连接;顶盖前支撑梁上段、顶盖纵梁中段总成、顶盖窗口加强板总成三者搭接处使用三个三层焊焊点连接;顶盖后支撑梁上段、顶盖纵梁中段总成、顶盖窗口加强板总成三者搭接处使用三个三层焊焊点连接;顶盖纵梁中段总成、顶盖窗口加强板总成搭接边处使用两个两层焊焊点连接。
7.所述顶盖前支撑梁上段和顶盖前支撑梁下段总成搭接边使用四个两层焊焊点连接;顶盖后支撑梁下段总成与顶盖后支撑梁上段搭接边使用四个两层焊焊点连接;顶盖中后梁和顶盖窗口加强板总成搭接边使用四个两层焊焊点连接;顶盖后支撑梁总成和顶盖中后梁搭接边使用两个两层焊焊点连接。
8.所述顶盖内板总成的各梁的横向截面形状为长方形结构,纵向截面形状为倒“几”字形结构。
9.所述顶盖前支撑梁下段总成、顶盖后支撑梁下段总成、顶盖纵梁后段均为上窄下宽式结构。
10.所述顶盖纵梁前段总成、顶盖纵梁中段总成、顶盖纵梁后段均使用高强钢材质。
11.所述驾驶室顶盖总成通过顶盖内板总成的各梁的末端与车身本体总成通过螺栓连接,周圈通过聚氨酯密封胶进行密封。
12.有益效果:本实用新型通过对顶盖总成加强梁总成布置优化,改善接头性能,部分加强梁使用高强钢代替原有普通材质,实现驾驶室顶盖总成的降本减重并加强车身的弯扭结构性能、安全性及nvh性能,提升了产品品质,降低了生产成本,降低用户的用车成本。本实用新型刚强度较高,生产成本较低,重量较轻,安全性较高,能够实现轻量化的需求。
附图说明
13.图1为本实用新型的结构示意图;
14.图2为本实用新型顶盖外板的结构示意图;
15.图3为本实用新型顶盖内板的结构示意主视图;
16.图4为本实用新型车身本体的结构示意图;
17.图5为本实用新型图1中顶盖纵梁中段的a-a断面示意图;
18.图6为本实用新型图1中与车身本体螺接及胶粘b-b断面断面示意图。
19.图7为本实用新型顶盖前支撑梁处的结构连接示意图。
20.图8为本实用新型顶盖后支撑梁处的结构连接示意图。
21.图9为本实用新型顶盖中后梁处的结构连接示意图。
22.图中:1、顶盖外板总成;2、顶盖内板总成;3、车身本体总成;11、顶盖左外板;12、顶盖后外板;13、顶盖右外板;14、顶盖前外板;21、顶盖前横梁总成;22、顶盖纵梁前段总成;23、顶盖前支撑梁下段总成;24、顶盖前支撑梁上段;25、顶盖纵梁中段总成;26、顶盖后支撑梁下段总成;27、顶盖后支撑梁上段;28、顶盖纵梁后段;29、顶盖后支撑梁总成;210、顶盖中后梁;211、顶盖窗口加强板总成;31、聚氨酯密封胶。
具体实施方式
23.下面结合附图及实施例对本实用新型做具体描述。
24.如图1-图9所示,本实用新型提供了一种商用车驾驶室顶盖总成,包括顶盖外板总成1和顶盖内板总成2,所述顶盖外板总成1由顶盖左外板11、顶盖后外板12、顶盖右外板13和顶盖前外板14拼焊而成,整体呈长方凹型;所述顶盖内板总成2为由顶盖前支撑梁上段24、顶盖前支撑梁下段总成23、顶盖后支撑梁上段27、顶盖后支撑梁下段总成26、两个顶盖纵梁、以及顶盖前横梁总成21、顶盖中后梁210和顶盖窗口加强板总成211搭接焊接而成的框架形结构,顶盖前支撑梁上段24、顶盖前支撑梁下段总成23、顶盖后支撑梁上段27、顶盖后支撑梁下段总成26和两个顶盖纵梁呈井字形结构,顶盖前横梁总成21设置在两个顶盖纵梁的前端部,顶盖中后梁210设置在顶盖后支撑梁总成29中部,顶盖内板总成2整体与顶盖外板总成1内侧适配、布置在顶盖外板总成1的内部,所述顶盖外板总成1和顶盖内板总成2
所有贴合面通过点焊连接。
25.所述顶盖左外板11、顶盖后外板12、顶盖右外板13和顶盖前外板14通过焊接搭接边进行点焊连接,其顶部设有天窗开口;所述顶盖左外板11、顶盖后外板12、顶盖右外板13和顶盖前外板14上均设置有加强筋,提升其结构刚度,防止振动异响及风噪,提升用户驾乘舒适性。
26.所述顶盖纵梁包括顶盖纵梁前段总成22、顶盖纵梁中段总成25和顶盖纵梁后段28,顶盖纵梁前段总成22与顶盖纵梁中段总成25搭接边使用四个两层焊焊点连接;顶盖纵梁中段总成25和顶盖纵梁后段28连接处搭接边使用四个两层焊焊点连接;顶盖前支撑梁上段24、顶盖纵梁中段总成25、顶盖窗口加强板总成211三者搭接处使用三个三层焊焊点连接;顶盖后支撑梁上段27、顶盖纵梁中段总成25、顶盖窗口加强板总成211三者搭接处使用三个三层焊焊点连接;顶盖纵梁中段总成25、顶盖窗口加强板总成211搭接边处使用两个两层焊焊点连接。
27.顶盖前支撑梁上段24和顶盖前支撑梁下段总成23搭接边使用四个两层焊焊点连接;顶盖后支撑梁下段总成26与顶盖后支撑梁上段27搭接边使用四个两层焊焊点连接;顶盖中后梁210和顶盖窗口加强板总成211搭接边使用四个两层焊焊点连接;顶盖后支撑梁总成29和顶盖中后梁210搭接边使用两个两层焊焊点连接。
28.所述顶盖内板总成2的各梁的横向截面形状为长方形结构,纵向截面形状为倒“几”字形结构,内板骨架的末端均与车身本体进行螺栓连接。
29.所述顶盖前支撑梁下段总成23、顶盖后支撑梁下段总成26、顶盖纵梁后段28均为上窄下宽式结构。
30.所述顶盖纵梁前段总成22、顶盖纵梁中段总成25、顶盖纵梁后段28均使用高强钢材质。
31.所述驾驶室顶盖总成通过顶盖内板总成2的各梁的末端与车身本体总成3通过螺栓连接,周圈通过聚氨酯密封胶31进行密封,满足了顶盖总成及附件的模块化装配,提升生产线装配效率。
32.通过cae性能分析,对顶盖纵梁前段总成22、顶盖纵梁中段总成25、顶盖纵梁后段28在y向位置调整优化,提升了顶盖顶压的性能,使顶压力能够均布迅速传递,提升整体的顶压刚度性能;对顶盖前支撑梁上段24、顶盖纵梁中段总成25、顶盖窗口加强板总成211三个零部件的接头及顶盖后支撑梁上段27、顶盖纵梁中段总成25、顶盖窗口加强板总成211三个零部件的接头进行截面腔体性能优化,接头处均使用三层焊焊点连接,并使关键接头分布于与车身本体连接点x向的对应位置,保证顶盖在顶压过程中顶压力有效传递,不发生溃折变形,保证顶压变形的稳定性;对顶盖前支撑梁下段总成23、顶盖后支撑梁下段总成26、顶盖纵梁后段28均使用上窄下宽式结构设计,保证顶盖总成下部与本体连接点处的结构刚度,从而提升顶盖整体的稳定性;对顶盖纵梁前段总成22、顶盖纵梁中段总成25、顶盖纵梁后段28均使用高强钢材质,提升纵梁整体的强度,并根据cae仿真结果进行减重优化,布置减重加强特征。
33.本实用新型在原有基础上进行轻量化优化设计,实现驾驶室顶盖总成的降本减重,并加强车身的弯扭结构性能及nvh性能,提升了产品品质,降低了生产成本,降低用户的用车成本。本实用新型是全新开发的高顶金属顶盖总成,一是重新优化顶盖外板造型,补充
加强特征,提升顶盖外板的刚度,降低行驶风阻;二是全新开发设计顶盖内板总成,重新布置骨架分布方案,改善顶压、侧碰等外力传递路径,并对安装硬点进行局部加强,对顶盖内板总成实施精细化减重。顶盖内板总成的纵梁骨架使用高强钢材质,增强了顶盖内板总成整体的刚强度性能。
34.本实用新型上述实施方案,只是举例说明,不是仅有的,所有在本实用新型范围内或等同本实用新型的范围内的改变均被本实用新型包围。