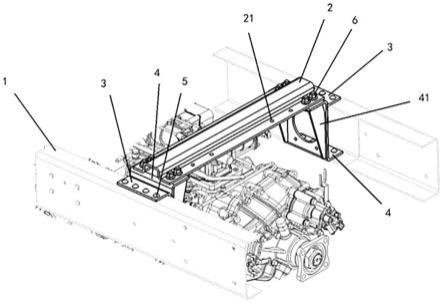
1.本实用新型涉及车架结构技术领域,具体涉及一种分装式车架横梁总成。
背景技术:2.本实用新型背景技术中公开的信息仅仅旨在增加对本实用新型的总体背景的理解,而不必然被视为承认或以任何形式暗示该信息构成已经成为本领域一般技术人员所公知的现有技术。
3.商用车上主流的混动技术路线为p2路线,即在发动机与变速箱之间增加一个电机,使整车可以实现纯电模式、混动模式、发动机模式等。发动机与变速器之间增加电机后,会造成动力总成长度增加。长度的增加导致装配落装困难,出现车架横梁与动力总成干涉的问题。现有车架上的横梁基本都是一体的,不可拆卸,影响生产节拍。因此,对于此类车型需要设计可分装拆卸式横梁,保证动力总成落装后再装配横梁,且保证相较于原结构强度不能减弱。
4.现有技术中,申请号为201921855357.2的专利文件,公开一种车架横梁总成。所述车架横梁总成包括第一连接弯板、第二连接弯板和横梁,第一连接弯板被配置为连接于车架纵梁上;第二连接弯板与第一连接弯板间隔设置,并被配置为连接于车架纵梁上;横梁的端部夹设于第一连接弯板和第二连接弯板之间,并分别与第一连接弯板和第二连接弯板可拆卸连接,横梁在第一连接弯板和第二连接弯板上的安装位置可调。
5.然而,其承载强度过于依赖螺栓连接件,连接强度可靠性和稳定性较差,安装效率较低,横梁的安装位置调节速度慢、效率低。
技术实现要素:6.针对现有技术中存在的问题,本实用新型的目的在于提供一种电动装载机先导电磁阀组控制装置。
7.为了达到以上目的,本实用新型采取以下技术方案:
8.一种分装式车架横梁总成,包括横梁和左右两个纵梁,所述横梁通过连板总成固定在纵梁上;所述连板总成包括l型支架和z型支架;其中,所述纵梁为槽钢,所述l型支架放置在纵梁顶部并与其配合可拆卸连接,所述z型支架顶端与横梁可拆卸连接,中部与所述l型支架可拆卸连接。
9.作为优选,所述z型支架两侧设置有加强筋板。
10.作为优选,所述横梁的横截面为“几”字型结构;所述纵梁为工字型或c型槽钢。
11.作为优选,所述z型支架为一体折弯件,包括上横板、下横板和竖板,所述上横板和下横板平行设置,所述竖板与上横板和下横板垂直设置;所述上横板与横梁连接,所述下横板放置在纵梁内侧底部上。
12.作为优选,所述竖板上设置有若干排呈阵列设置的连接孔,所述z型支架和l型支架通过螺栓组件配合连接孔可拆卸连接。
13.作为优选,所述z型支架和纵梁均与l型支架通过铆钉铆接连接,所述z型支架分别和横梁与纵梁均通过螺栓组件连接。
14.作为优选,所述横梁上开设有若干个用以穿过线路和管路的定位孔。
15.有益效果:所述分装式车架横梁总成可以实现动力总成装配便利性,提高装配效率;
16.该分装式车架横梁总成的通用性强,可以匹配不同宽度的车架;当车架宽度变化时,仅需要更换较长的横梁即可,连接板总成无需改动;
17.该分装式车架横梁总成的配件通过折弯或可配合焊接即可完成,加工简便,且没有模具费用,节约生产成本;
18.该分装式车架横梁总成的横梁高度可调节;当整车对于横梁高度有不同要求时,仅需要改动l型支架与z型支架的相对位置连接固定即可实现高度的变更,通用性较高。
附图说明
19.图1为本实用新型的控制原理示意图;
20.图2为本实用新型的连接关系示意图;
21.图中,纵梁1,横梁2,定位孔21,l型支架3,z型支架4,加强筋板41,上横坂42,下横板43,竖板44,铆钉5,螺栓6。
具体实施方式
22.下面结合具体实施例和附图对本实用新型作进一步说明。
23.图1至图2出示了一种分装式车架横梁2总成,可以解决体积较大的动力总成落装困难的问题,包括横梁2和左右两个纵梁1,所述横梁2通过连板总成固定在纵梁1上;所述连板总成包括l型支架3和z型支架4;其中,所述纵梁1为槽钢,所述纵梁1可为工字型或c型槽钢,可为z型支架4和l型支架3提供安装空间,使得纵梁1外侧裸露的连接组件减少,均包裹在纵梁1内;所述l型支架3放置在纵梁1顶部并与其配合可拆卸连接,所述z型支架4底端与槽钢内侧可紧密配合;所述z型支架4顶端与横梁2可拆卸连接,中部与所述l型支架3可拆卸连接,在z型支架4和l型支架3连接的基础上,对z型支架4起到一定的限位作用,辅助其固定;而且,z型支架4可放置在槽钢内侧,槽钢底部可为z型支架4提供相应的支撑作用,有助于其固定的稳定性和可靠性。
24.除此之外,该所述分装式车架横梁2总成可以实现动力总成装配便利性,提高装配效率;
25.该分装式车架横梁总成的通用性强,可以匹配不同宽度的车架;当车架宽度变化时,仅需要更换较长的横梁2即可,连接板总成无需改动;
26.该分装式车架横梁总成的配件通过折弯或可配合焊接即可完成,加工简便,且没有模具费用,节约生产成本;
27.该分装式车架横梁总成的横梁2高度可调节;当整车对于横梁2高度有不同要求时,仅需要改动l型支架3与z型支架4的相对位置连接固定即可实现高度的变更,通用性较高。
28.作为优选的另一实施例中,所述z型支架4两侧焊接有加强筋板41,有利于提高z型
支架4的强度,从而提升整体车架横梁2总成的稳定性和可靠性。
29.作为优选的另一实施例中,所述横梁2的横截面为“几”字型结构,有利于提升横梁2的强度。
30.作为优选的另一实施例中,如图2所示,所述z型支架4为一体折弯钢件,包括上横板42、下横板43和竖板44,所述上横板42和下横板43平行设置,所述竖板44与上横板42和下横板43垂直设置,有利于提高竖直方向上的受力稳定性;所述上横板42与横梁2连接,所述下横板43放置在纵梁1内侧底部上,有利于提高整体分装式车架横梁2总成的载荷能力。
31.作为优选的另一实施例中,如图2所示,所述竖板44上设置有若干排呈阵列设置的连接孔,所述z型支架4和l型支架3通过螺栓6组件配合连接孔可拆卸连接;可通过不同排的连接孔固定横梁2,实现调节横梁2的高度。
32.作为优选的另一实施例中,如图2所示,所述z型支架4和纵梁1均与l型支架3通过铆钉5铆接连接,铆接连接为刚性连接,稳定性更强;所述z型支架4分别和横梁2与纵梁1均通过螺栓6组件连接,便于拆卸和安装,有利于横梁2的高度调节。
33.作为优选的另一实施例中,所述横梁2上开设有若干个用以穿过线路和管路的定位孔21;能够避免电线或管路在支架边缘上产生磨损,提高了整车可靠性与安全性。
34.综上所述,本实用新型横梁与连接板总成分开装配,落装动力总成后再将横梁装配好,便于装配线落装动力总成;结构强度更高,通用性更好,可解决较大动力总成落装问题;安装方便,可允许的装配误差范围更大。
35.最后应说明的是:以上实施例仅用以说明本实用新型的技术方案,而非对其限制;尽管参照前述实施例对本实用新型进行了详细的说明,本领域的普通技术人员应当理解:其依然可以对前述各实施例所记载的技术方案进行修改,或者对其中部分技术特征进行等同替换;而这些修改或者替换,并不使相应技术方案的本质脱离本实用新型各实施例技术方案的范围。