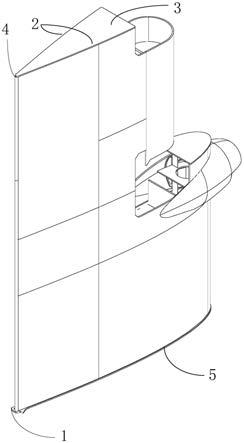
[0001]
本发明涉及船舶领域,尤其是涉及一种船舶舵叶及其摆动测试方法。
背景技术:[0002]
船舶工具通常使用舵叶改变行进方向,舵叶借助舵杆安装在船尾上,在船舶建造过程中需要对舵叶进行摆动测试,现阶段货船船型的舵叶设计为在舵叶艉向外板设置穿绳孔,舵叶制作过程中该位置封板阶段空间狭小,该穿绳孔的设计位置不利于施工,且难以确保舵叶外板的焊接质量,由于舵叶穿绳孔的位置不便摆舵,船坞坞内摆舵测试施工作业中仍采取叉车等“机械冲撞”形式,采取叉车等“机械冲撞”形式作业不但破坏船舶舵叶油漆质量,而且存在着一定的安全隐患,且人员劳动强度大,成本花费高。
技术实现要素:[0003]
针对现有技术的不足,本发明提供一种加工便捷且可牵引舵叶进行摆动测试的一种船舶舵叶及其摆动测试方法。
[0004]
本发明提供一种船舶舵叶,包括舵叶主体和开孔板,所述舵叶主体包括两侧侧板、顶板和底板,所述顶板设置于所述两侧侧板顶部,所述底板设置于所述两侧侧板底部,所述两侧侧板、顶板和底板组成空心结构,所述开孔板设置于所述两侧侧板尾部,并与所述底板连接,所述开孔板相对于所述两侧侧板向外突出设置,所述开孔板上设置有贯穿其的工作孔。
[0005]
优选地,所述开孔板上设置有相互对应的第一工作孔和第二工作孔。
[0006]
优选地,所述两侧侧板尾部设置有尾部加强结构,所述第一工作孔和第二工作孔分别设置于所述尾部加强结构两侧。
[0007]
优选地,所述开孔板包括第一部分和第二部分,所述第一部分向外突出具有第一突出弧边,所述第二部分向外突出具有第二突出弧边,所述第一工作孔设置于第一部分,且所述第一工作孔的半径与所述第一突出弧边的半径比值为1:(1-5);所述第二工作孔设置于第二部分,且所述第二工作孔的半径与所述第二突出弧边的半径比值为1:(1-5)。
[0008]
优选地,所述开孔板还包括连接边、第一内弧边和第二内弧边,所述第一内弧边和第二内弧边均朝内弯曲,所述第一内弧边、第一突出弧边、连接边、第二突出弧边和第二内弧边依次连接。
[0009]
优选地,所述开孔板与所述底板一体成型。
[0010]
优选地,所述两侧侧板上开设有穿绳孔。
[0011]
优选地,所述两侧侧板上设置有多个吊码。
[0012]
优选地,所述两侧侧板上还设置有横向加强结构和竖向加强结构。
[0013]
优选地,先用钢丝绳穿过船舶舵叶的工作孔,然后使用外力拉动钢丝绳进行摆舵测试。
[0014]
本发明提供的一种船舶舵叶设置有开孔板,开孔板上设置有相互对应的第一工作
孔和第二工作孔,开孔板加工便捷,降低舵叶制作的难度,且满足技术要求,可以牵引舵叶进行摆动测试,提高舵叶安装、调试效率,降低作业人员的劳动强度,降低成本。
附图说明
[0015]
通过附图中所示的本发明优选实施例更具体说明,本发明上述及其它目的、特征和优势将变得更加清晰。在全部附图中相同的附图标记指示相同的部分,且并未刻意按实际尺寸等比例缩放绘制附图,重点在于示出本发明的主旨。
[0016]
图1为本发明实施例提供的船舶舵叶结构立体示意图;
[0017]
图2为本发明实施例提供的船舶舵叶俯视结构示意图;
[0018]
图3为图2提供的船舶舵叶a环内放大结构示意图。
[0019]
图中:1、开孔板;2、两侧侧板;3、顶板;4、尾部加强结构;5、底板:11、第一部分;111、第一突出弧边;112、第一内弧边;12、第二部分;121、第二突出弧边;122、第二内弧边;13、第一工作孔;14、第二工作孔;15、连接边。
具体实施方式
[0020]
为了便于理解本发明,下面将参照相关附图对本发明进行更全面的描述。
[0021]
需要说明的是,当一个元件被认为是“连接”另一个元件,它可以是直接连接到另一个元件并与之结合为一体,或者可能同时存在居中元件。本文所使用的术语“安装”、“一端”、“另一端”以及类似的表述只是为了说明的目的。
[0022]
除非另有定义,本文所使用的所有的技术和科学术语与属于本技术领域的技术人员通常理解的含义相同。本文中说明书中所使用的术语只是为了描述具体的实施例的目的,不是旨在于限制本发明。本文所使用的术语“及/或”包括一个或多个相关的所列项目的任意的和所有的组合。
[0023]
参考图1-2,本发明实施例提供一种船舶舵叶,包括舵叶主体和开孔板1,舵叶主体包括两侧侧板2、顶板3和底板5,顶板3设置于两侧侧板2顶部,底板5设置于两侧侧板2底部,两侧侧板2、顶板3和底板5组成空心结构,开孔板1设置于两侧侧板2尾部,并与底板5连接,开孔板1相对于两侧侧板2向外突出设置,开孔板1上设置有贯穿其的工作孔。
[0024]
本实施例通过设置开孔板1及其上设置的贯穿的工作孔实现穿绳牵引的功能,既满足舵叶的技术要求,而且摆动测试时起到穿绳牵引的作用,加工方便且使用便捷,可提高舵叶安装、调试效率,降低作业人员的劳动强度,且将开孔板1设置于舵叶底部尾端,可以更好的实现牵引效果,本实施例中提供的船舶舵叶在安装与摆动测试时,一些大型尺寸的舵叶工期可由原来的4天缩短到现在的4小时,单船工时减少1300小时,船坞周期缩短3天,具有极高的经济价值。
[0025]
参考图2,在优选实施例中,开孔板1上设置有相互对应的第一工作孔13和第二工作孔14,舵叶摆动测试需要左右牵引,设置第一开孔板1和第二开孔板1可以更好的实现牵引效果,进一步提高测试效率。
[0026]
参考图1-2,在优选实施例中,两侧侧板2尾部设置有尾部加强结构4,第一工作孔13和第二工作孔14分别设置于尾部加强结构4两侧,舵叶的两侧侧板2尾部连接需要高强度连接,连接处的尾部加强结构4通常使用扁钢,第一工作孔13和第二工作孔14设置于尾部加
强结构4两侧可以实现舵叶的左右牵引,提高安全性,且可更好的牵引舵叶进行摆动测试。
[0027]
参考图2,在优选实施例中,开孔板1包括第一部分11和第二部分12,第一部分11向外突出具有第一突出弧边111,第二部分12向外突出具有第二突出弧边121,第一工作孔13设置于第一部分11,且第一工作孔13的半径与第一突出弧边111的半径比值为1:(1-5),比值可以为1:1,1:2,1:3,1:4,1:5;第二工作孔14设置于第二部分12,且第二工作孔14的半径与第二突出弧边121的半径比值为1:(1-5),比值可以为1:1,1:2,1:3,1:4,1:5,在本实施例中,舵叶的本体质量较大,工作孔作为牵引舵叶进行摆动测试的受拉力的眼板开孔,开孔位置及尺寸经受力分析,将开孔板1及其上的第一工作孔13和第二工作孔14如此设置可以更好的牵引舵叶进行摆动测试,不会断裂损毁,且降低成本,提高安全性。
[0028]
参考图2,在优选实施例中,开孔板1还包括连接边15、第一内弧边112和第二内弧边122,第一内弧边112和第二内弧边122均朝内弯曲,第一内弧边112、第一突出弧边111、连接边15、第二突出弧边121和第二内弧边122依次连接,在本实施例中,开孔板1如此设置更符合舵叶的技术要求以及实用性,且能提升开孔板1的强度,安全性更好。
[0029]
参考图1-2,在优选实施例中,开孔板1与底板5一体成型,防止断裂,提高安全性,且制作效率更高。
[0030]
参考图1-2,在优选实施例中,两侧侧板2上开设有穿绳孔,在大型舵叶吊装时通过穿绳孔吊装的安全性更高,也可配合第一工作孔13和第二工作孔14,可实现更高的舵叶安装效率,但穿绳孔一般为贯穿舵叶两侧侧板2设置,且可多个设置,穿绳孔的加工位置狭窄,施工困难,且难以保证舵叶两侧侧板2的焊接质量,所以在其他实施例中,两侧侧板2上也可不设穿绳孔,采用其他方式吊装。
[0031]
参考图1-2,在优选实施例中,两侧侧板2上设置有多个吊码,在大型舵叶吊装时通过吊码吊装的安全性更高,也可配合第一工作孔13和第二工作孔14,可实现更高的舵叶安装及测试效率,在其他实施例中,两侧侧板2上也可不设吊码,采用其他方式吊装。
[0032]
参考图1-2,在优选实施例中,两侧侧板2上还设置有横向加强结构和竖向加强结构,提升舵叶的强度。
[0033]
参考图1-2,本发明实施例还提供一种船舶舵叶摆动测试方法,其特征在于,先用钢丝绳穿过船舶舵叶的工作孔,然后使用外力拉动钢丝绳进行摆舵测试。
[0034]
在本申请中,除非另有明确的规定和限定,第一特征在第二特征“上”或“下”可以是第一和第二特征直接接触,或第一和第二特征通过中间媒介间接接触。而且,第一特征在第二特征“之上”、“上方”和“上面”可是第一特征在第二特征正上方或斜上方,或仅仅表示第一特征水平高度高于第二特征。第一特征在第二特征“之下”、“下方”和“下面”可以是第一特征在第二特征正下方或斜下方,或仅仅表示第一特征水平高度小于第二特征。
[0035]
在本说明书的描述中,参考术语“优选实施例”、“再一实施例”、“其他实施例”或“具体示例”等的描述意指结合该实施例或示例描述的具体特征、结构、材料或者特点包含于本申请的至少一个实施例或示例中。在本说明书中,对上述术语的示意性表述不必须针对的是相同的实施例或示例。而且,描述的具体特征、结构、材料或者特点可以在任一个或多个实施例或示例中以合适的方式结合。此外,在不相互矛盾的情况下,本领域的技术人员可以将本说明书中描述的不同实施例或示例以及不同实施例或示例的特征进行结合和组合。
[0036]
尽管上面已经示出和描述了本申请的实施例,可以理解的是,上述实施例是示例性的,不能理解为对本申请的限制,本领域的普通技术人员在本申请的范围内可以对上述实施例进行变化、修改、替换和变型。