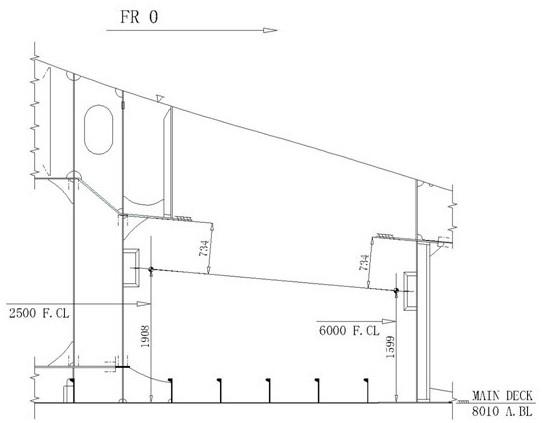
1.本发明涉及船舶制造技术领域,特别涉及一种船舶艉推设备定位与装焊方法。
背景技术:2.船舶艉推设备主要包括螺旋桨、可调螺旋桨、喷气式推进器等,是船舶的动力来源。在制造船舶时,为保证船体平台板满足设备的安装要求,一般船体会略微倾斜,艉推设备的安装平面为一个斜面,艉推设备安装时同时要调整船体筋板位置和设备筋板位置,拉线不便,造成设备定位难,不准确的问题。
技术实现要素:3.针对上述问题,本发明提供一种船舶艉推设备定位与装焊方法,旨在解决艉推设备定位难,不准确的问题。
4.本发明所提供的技术方案为:船舶艉推设备定位与装焊方法,包括以下步骤:步骤一, 根据艉推设备与船体结构对接缝的理论尺寸,制作假体;步骤二,按照艉推设备安装位置、角度要求,将钢丝线通过主甲板工艺孔、船体平台板及底板开孔进行拉线定位,根据钢丝线位置,对船体结构平台板、底板进行校对,使钢丝线垂直于船体结构平台板及底板,并以钢丝线为中心,将平台板及底板上的圆孔进行切割;步骤三,将钢丝线撤除,通过主甲板工艺孔,将假体吊运至船体结构凹槽处,使船体平台板及底板圆孔与假体上下封板相吻合,再次进行拉线,使钢丝线通过假体上下封板中心,并使上下封板面垂直于钢丝线,在此过程中,将假体以钢丝线为轴心转动,使假体侧壁上筋板与船体结构筋板相贴合;步骤四,根据假体筋板与船体结构筋板贴合情况,重新调整船体筋板位置,使船体结构各筋板与假体各筋板贴合,并对船体结构筋板与假体筋板重合处进行划线,将船体结构筋板余量沿所画对合线割除,根据定位后假体筋板位置,调整船体各筋板位置及角度,使假体各筋板与船体各筋板对合并使两者处于同一平面上,完成船体筋板与船体结构的焊接工作后将假体吊离;步骤五,以艉推设备上下法兰边缘拉线,并沿该线将设备筋板的余量进行切除,将艉推设备吊至船体结构凹槽处调整设备位置及角度,使设备筋板与船体结构筋板贴合,并参照步骤四,将设备筋板与船体结构筋板实际重合值割除,调整设备角度,使其各筋板与船体结构各筋板完全对合,同时设备上下平面板与船体平台板、底板间间隙保持一致;步骤六,将艉推设备上、下法兰分别与船体平台板、底板进行点焊固定。
5.优选的,所述主甲板工艺孔处设有用于确定上定位点的刚性梁。
6.更为优选的,所述刚性梁材料为角钢或槽钢。
7.所述钢丝线的两端设有拉线架。
8.所述假体的上下封板设有用于调节定位的顶升螺栓。
9.所述步骤四切割船体结构筋板余量时,将假体抬高或吊高,切割完成后将假体下降至船体结构凹槽处。
10.所述步骤五中,所述设备筋板加放30mm余量作为预切割线,并沿预切割线将设备筋板余量进行割除。
11.所述步骤六中,所述焊接的方式为co2多层焊,其焊接顺序为按法兰面对角线对称进行焊接。
12.本发明的有益效果为:通过制作、安装假体,并通过对假体结构的拉线定位,先利用假体与船体筋板的贴合情况调整切割船体筋板,再安装艉推设备,调整设备筋板与船体筋板的贴合情况,拉线方便,定位准确,艉推设备易安装,假体可重复使用,适合量化生产。
附图说明
13.图1为本发明实施例的船体平台板沿船宽拉线定位示意图。
14.图2为本发明实施例的船体平台板沿船长拉线定位示意图。
15.图3为本发明实施例的船体平台板安装示意图图4为本发明实施例的假体的正视图。
16.图5为本发明实施例的假体的拉线定位示意图。
17.图6为本发明实施例的艉推设备筋板预切割示意图。
18.图7为本发明实施例的艉推设备法兰面焊接顺序示意图。
19.图8为本发明实施例的艉推设备安装于船体的示意图。
20.图中,1
‑
假体,2
‑
上顶升螺栓,3
‑
下顶升螺栓,4
‑
上拉线架,5
‑
刚性梁,6
‑
主甲板工艺孔,7
‑
钢丝线,8
‑
船体平台板,9
‑
底板,10
‑
拉线架,11
‑
上法兰,12
‑
理论对合线,13
‑
预切割线,14
‑
下法兰。
具体实施方式
21.下面结合附图对本发明的实施例作进一步说明。
22.以s1049液化气船艉推设备为例,艉推设备安装前需完成平台板的拼接工作,平台板需进行校平,允许公差为
±
2mm,安装艉推设备的分段采用反造,将船体平台板吊运至该分段进行定位,为保证船体平台板满足设备安装艏艉偏5
°
、左右偏3
°
的安装要求,需对船体平台板沿船宽、船长方向各拉钢丝线进行定位,如图1
‑
2所示,具体定位数据如下:沿船宽:靠船舯定位点:x=fr0,y=
±
2500,z= 6092(距基线)、1908(距主甲板,不包括板厚);靠舷侧定位点:x=fr0,y=
±
6000,z= 6399(距基线)、1599(距主甲板,不包括板厚);并保证平台板距钢丝线的直线距离为:734
±
2mm,沿船长:靠艏定位点:x=fr8
‑
300
,y=
±
4336,z= 5974(距基线)、2026(距主甲板,不包括板厚);靠艉定位点:x=fr
‑
2,y=
±
4336,z= 6327(距基线)、1673(距主甲板,不包括板厚);
并保证平台板距钢丝线的直线距离为:735
±
2mm。
23.如图3所示,按照上述拉线要求,定位、装焊船体平台板后,将分段进行翻身,翻身后将分段置平,以满足设备安装要求,下一步进行艉推设备的定位及装焊。
24.如图4
‑
8所示,船舶艉推设备定位与装焊方法,包括以下步骤:步骤一,根据艉推设备与船体结构对接缝的理论尺寸,制作假体,该假体为圆台结构,靠近船体平台板的部分为圆台结构的宽部,靠近船体底板的部分为圆台结构的窄部,假体的上下封板设有顶升螺栓,用于假体的调节定位。
25.步骤二,按照艉推设备安装位置、角度要求,将钢丝线通过主甲板工艺孔、船体平台板及底板开孔进行拉线定位,此时主甲板已被割孔,可在主甲板工艺孔处装焊刚性梁,以确定上定位点,为防止扭曲、下垂,刚性梁采用角钢、槽钢等材料,并上下各设一拉线架,钢丝线上下定位点三向定位数据为:上定位点:x=fr0
+131
,y=
±
4183,z=8010(距基线);下定位点:x=fr0
‑
158
,y=
±
4665,z=2500(距基线)。
26.根据钢丝线位置,对船体结构平台板、底板进行校对,平面度允许公差为:
±
3mm,使钢丝线垂直于船体结构平台板及底板,并以钢丝线为中心,将平台板及底板上的圆孔进行切割,完成切割后平台板开孔尺寸为:
ø
2650
‑
3mm;底板开孔尺寸为:
ø
1490
‑
3 mm。
27.步骤三,将钢丝线撤除,通过主甲板工艺孔,将假体吊运至船体结构凹槽处,进行初步定位,即使船体平台板及底板圆孔与假体上下封板相吻合,再次进行拉线,使钢丝线通过假体上下封板中心,并使上下封板面垂直于钢丝线,在此过程中,将假体以钢丝线为轴心转动,通过调整上下封板的顶升螺栓,使假体侧壁上筋板与船体结构筋板相贴合。
28.步骤四,根据假体筋板与船体结构筋板贴合情况,重新调整船体筋板位置,使船体结构各筋板与假体各筋板贴合,并对船体结构筋板与假体筋板重合处进行划线,划线前,确保船体各筋板远离设备一端定位准确,并将船体各筋板点焊固定,将船体结构筋板余量沿所画对合线割除,为保证切割时不对假体筋板造成破坏,及保证足够的施工空间,可在切割船体结构筋板时将假体抬高或吊离,切割完成后假体再次就位,根据定位后假体筋板位置,调整船体各筋板位置及角度,使假体各筋板与船体各筋板对合并使两者处于同一平面上,完成船体筋板与船体结构的焊接工作后将假体吊离;步骤五,以艉推设备上下法兰边缘拉线,此线即为设备与船体结构筋板的理论对合线,为确保对合准确,设备筋板可加放30mm余量作为预切割线,并沿预切割线将设备筋板余量进行割除,将艉推设备吊至船体结构凹槽处调整设备位置及角度,使设备筋板与船体结构筋板贴合,并参照步骤四,将设备筋板与船体结构筋板实际重合值割除,调整设备角度,使其各筋板与船体结构各筋板完全对合,同时设备上下平面板与船体平台板、底板间间隙保持一致。
29.步骤六,将设备上、下法兰分别与船体平台板、底板进行焊接固定,焊接采用co2多层焊,其包括打底焊和盖面焊,打底焊电流不能超过220a,盖面焊电流不要超过250a,焊缝焊长约300mm,焊缝高度约3mm,完成第一道焊缝后,按法兰面对角线对称进行焊接,其多道焊的焊道接头进行错开,如此重复,完成设备上、下法兰分别与船体平台板、底板的打底焊缝施焊工作,并作好盖面焊,使上、下法兰分别与船体平台板、底板对接光顺。
30.实施例不应作为本发明的限制,任何基于本发明的精神所作的非创造性改进都应
视为本发明的保护范围。