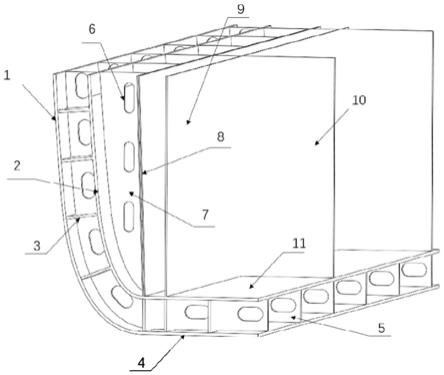
1.本发明属于舰船防护领域,特别是涉及一种大型船舶舷侧吸收液舱泄爆装置。
背景技术:2.大型船舶在现代海战中主要受到鱼雷、水雷等水中兵器的毁伤,其中鱼雷接触爆炸毁伤对水面舰船的威胁最为严峻,因此大型船舶在舷侧采用多舱结构以增强结构防护能力。随着我国重心不断从陆地走向海洋,而大型船舶对于这一战略的实施有着不可忽略的作用,其抗冲击能力的进一步提升有着重要的战略需求。
3.针对大型船舶的水下爆炸试验,其试验成本高,积累的相关实验数据较少,当前典型大型船舶舷侧防护结构为“空—液—空”结构,第一层空舱结构承受最初的爆炸载荷和爆轰产物的冲击,第二层液舱进一步减缓高速弹片的冲击并且减缓弹片的冲击速度,最后的空舱减缓液舱内板损坏后形成的冲击压力,避免水密舱壁破坏。现阶段典型液舱防护结构在爆炸冲击载荷作用下均出现了严重的损毁,危及内部水密舱壁,其防护性能有进一步提升的需求。
技术实现要素:4.本发明为了解决现有技术中的问题,提出一种大型船舶舷侧吸收液舱泄爆装置。
5.为实现上述目的,本发明采用以下技术方案:一种大型船舶舷侧吸收液舱泄爆装置,它包括液舱外板、吸收液舱内弧形板支撑、复合液舱内板结构、水密舱壁、横舱壁结构和船体内底板,所述吸收液舱内弧形板支撑焊接在布线好的液舱外板与复合液舱内板结构之间,所述吸收液舱内弧形板支撑上开设有多个吸收液舱内泄爆孔,所述水密舱壁与船体内底板相连,所述船体内底板与液舱外板相连,所述横舱壁结构依次贯穿连接液舱外板、复合液舱内板结构和水密舱壁。
6.更进一步的,所述液舱外板和船体内底板外侧与船体肋板相连。
7.更进一步的,所述液舱外板和船体内底板通过船体肋板分别与船体舷侧外板和船底外板相连。
8.更进一步的,所述液舱外板和船体舷侧外板之间设置有多个空舱弧形板支撑。
9.更进一步的,所述船体肋板上开设有泄爆孔。
10.更进一步的,所述吸收液舱内弧形板支撑和复合液舱内板结构舷侧舱室内设置有t型材。
11.更进一步的,所述多个吸收液舱内泄爆孔等距设置。
12.本发明解决了现有大型船舶舷侧舱壁防护结构优化不足,冗杂的问题,节省了大量的财力和物力和人力的同时又减轻了船舶的重量且满足大型船舶抗冲击性能的要求。对于船厂施工可操作性较高。
13.本发明在舷侧防护方面可获得较好效果,其中:在舱壁处设置泄爆孔能够弥散冲击波,削弱液舱内板结构受到的液舱冲击作用,同时在用相同质量钢板的情况下吸收液舱
泄爆装置的抗冲击性能更好,减轻了液舱内板的破坏程度,通过复合舱壁结构的介质阻抗强弱变化可以减弱冲击波的透射作用,使得冲击波载荷更多的由液舱内板吸收,进而起到对水密舱壁的防护作用。从水密舱壁的防护效果上看,复合液舱内板结构要优于同厚度下的传统板架结构。
14.本发明所搭载舷侧结构受到爆炸载荷冲击时,外板最先受到冲击;然后,冲击波通过外板传递到船体肋板上,船体肋板上的泄爆孔进一步抵抗冲击;之后冲击波传到吸收液舱内,吸收液舱内液体减缓爆炸破片的冲击;最后复合液舱内板结构将冲击的影响减到最小。与现有舷侧防护结构相比,该发明将进一步增强大型舰船的防护性能。
附图说明
15.图1为本发明所述的一种大型船舶舷侧吸收液舱泄爆装置结构示意图;
16.图2为本发明所述的吸收液舱整体结构示意图;
17.图3为本发明所述的吸收液舱侧视结构示意图;
18.图4为本发明所述的吸收液舱后壁复合液舱内板结构示意图;
19.图5为本发明所述的吸收舱后壁双层板内部加强结构示意图
[0020]1‑
船体舷侧外板,2
‑
液舱外板,3
‑
空舱弧形板支撑,4
‑
船底外板,5
‑
船体肋板,6
‑
吸收液舱内泄爆孔,7
‑
吸收液舱内弧形板支撑,8
‑
复合液舱内板结构,9
‑ꢀ
水密舱壁,10
‑
横舱壁结构,11
‑
船体内底板,12
‑
t型材,13
‑
内部加强结构。
具体实施方式
[0021]
下面将结合本发明实施例中的附图,对本发明实施例中的技术方案进行清楚、完整地阐述。
[0022]
参见图1
‑
5说明本实施方式,一种大型船舶舷侧吸收液舱泄爆装置,它包括液舱外板2、吸收液舱内弧形板支撑7、复合液舱内板结构8、水密舱壁9、横舱壁结构10和船体内底板11,吸收液舱内弧形板支撑7焊接在布线好的液舱外板2与复合液舱内板结构8之间,吸收液舱内弧形板支撑7上开设有多个吸收液舱内泄爆孔6,水密舱壁9与船体内底板11相连,船体内底板11与液舱外板2相连,横舱壁结构10依次贯穿连接液舱外板2、复合液舱内板结构8 和水密舱壁9。
[0023]
本实施例液舱外板2和船体内底板11外侧与船体肋板5相连,液舱外板2 和船体内底板11通过船体肋板5分别与船体舷侧外板1和船底外板4相连,液舱外板2和船体舷侧外板1之间设置有多个空舱弧形板支撑3,船体肋板5上开设有泄爆孔,吸收液舱内弧形板支撑7和复合液舱内板结构8舷侧舱室内设置有t型材12,多个吸收液舱内泄爆孔6等距设置,复合液舱内板结构8。
[0024]
本实施例所述泄爆装置可代替目前的舷侧吸收液舱结构,即重新设计了一种船舱防护设计方式,试验样件为具体大型船舶具体分析,可随着不同的船舶尺寸进行调整。可实现高速弹片冲击防护,且吸收液舱内弧形板支撑7设有泄爆孔,能够卸载冲击波,吸收液舱后舱壁为复合液舱内板结构8,进一步提高舷侧强力防护舱壁结构在受到典型水下接触爆炸作用时的防护性能。实施例中复合液舱内板结构8即为液舱内板。
[0025]
如图1所示,可以看到在吸收液舱上等距离布置泄爆孔,在舭部泄爆孔可适当减小
直径以保证结构强度,同时泄爆孔的另一作用就是保证液舱内部流体流动,更好的抵御冲击载荷。如图2所示,在吸收液舱内部设置了板架支撑,板架为液舱外板2与复合液舱内板结构8,且焊接于液舱外板2和复合液舱内板结构8之间,且开孔为平滑过渡减小了应力集中现象的发生,开孔跨度较大时会严重影响板架的整体强度,使其不能有效地起到支撑作用,以板架跨度1/5 开孔跨度为宜。如图3所示,为吸收液舱侧视结构示意图,与船厂现有的布置升级,便于工人施工,操作简单方便,可替代性高。如图4所示,具体为将原单层板替换为厚度与之前一致的复合液舱内板结构8,经试验证明可知,复合液舱内板结构8间隔布置虽然会略比单层板所占空间更多,但对于舷侧抗冲击的能力会有大幅度提高,有利于维持大型舰艇生命力,保证大型船舶自持力。
[0026]
实施例中所述各部件均为焊接,焊接的原则即先焊接吸收液舱刚性最大的吸收液舱内弧形板支撑7,然后由中央向边缘焊接每一个部件,首先吸收液舱内弧形板支撑7焊接在事先布线好的液舱外板2和复合液舱内板结构8中,横舱壁结构10为连续板架应贯穿整个大型船舶舷侧部分,所以应将液舱外板2、复合液舱内板结构8和水密舱壁9事先切割好相应尺寸,留好焊后进行焊接,之后将吸收液舱与吸收液舱之后的空舱整体焊接于船体内底板11与船体肋板5 上,之后进行空舱弧形板支撑3以及船体舷侧外板1的焊接。
[0027]
吸收液舱内弧形支撑板7的位置和数量由大型船舶主尺度及舱室尺寸进行确定,应采用合理间距布置以避免出现应力集中的现象,另外在易受冲击位置进行结构补强进一步加强结构抗冲击性能,复合液舱内板结构8应采用比强度大、比模量大的复合材料,与单层板相比,结构质量的降低以及能量吸收和变形的高效模式的出现,可以吸收更多的能量,进一步弥补因占用空间而带来的负面影响。由于吸收液舱采用了强度较大的支撑板结构,是整个吸收液舱形成一个整体,在抵抗冲击载荷是更加均匀的传递到全舱各个部位,从而降低了局部外载荷的冲击强度,达到提高整个船体生命力的目的。