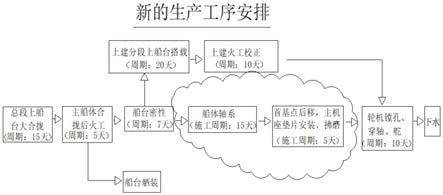
1.本发明涉及船舶建造领域,更具体地说,它涉及一种基于船体轴系施工工艺缩短船舶建造周期的方法。
背景技术:2.船体轴系施工工艺属于船舶生产技术中较为重要的一部分工艺,它的施工周期很大程度上决定着船舶的建造周期,如图1所示,船体轴系施工是在上建火工完成后进行的,船体轴系施工过程包括如下工序:
3.(1)全船压载;(2)全船测量;(3)确定基线、轴系地样线刻划、轴系首尾基准点安装报验;(4)主机座、齿轮箱座面板安装;(5)艉轴管、托架及结构安装;(6)主机座、齿轮箱基座、艉轴管、托架及结构焊接;(7)主机座、齿轮箱基座、艉轴管、托架焊后报验;(8)主机座、齿轮箱基座探伤、艉轴管、托架焊后退火及探伤试密。
4.目前某型号中小型民用船舶生产工序安排如图2所示:
5.(1)总段上船台大合拢,施工周期15天;(2)主船体合拢后火工,施工周期5天;(3)船台密性施工,周期7天;(4)上建分段上船台搭载施工,周期20天;(5)上建火工校正,施工周期10天;(6)船体轴系施工,周期15天;(7)轮机轴系施工,周期15天;(8)下水。
6.可见,现有的船体轴系施工工艺需要等到主船体上建火工校正完成后才能进行施工,在此过程中,需要等待主船体上建火工校正施工周期10天时间,延长了船舶建造周期,严重影响交船时间,进而导致生产效率下降的问题。因此,亟需研发设计一种缩短船舶建造周期的船体轴系施工方法。
技术实现要素:7.本发明要解决的技术问题是针对现有技术的上述不足,其目的是提供一种基于船体轴系施工工艺缩短船舶建造周期的方法,在保证轴系质量的前提下,缩短船舶的建造周期,提高生产效率。
8.本发明的技术方案是这样的:一种基于船体轴系施工工艺缩短船舶建造周期的方法,包括:
9.完成对主船体装焊、外板及主甲板火工矫正;
10.完成对所述主船体密性试验报验;
11.根据《设备压载布置图》对所述主船体进行压载;
12.设置所述主船体的标杆观测点,每天固定时间监控所述主船体状态并做好记录;
13.根据记录的主船体状态数进行船体轴系工序施工;
14.在船体轴系工序施工过程中,进行上建分段上船台搭载工序施工,以及进行上建火工校正工序施工;
15.在上建火工校正工序结束前完成船体轴系工序施工。
16.作为进一步地改进,进行船体轴系工序施工包括:
17.根据第一次记录的船体状态数据调整好样杆基线,以及确定船体轴系的首尾基准点,并对船体轴系进行一次拉线报验;
18.根据上建焊接、上建火工校正对主船体艏艉翘和龙骨挠度的影响,确定艉基点向下放置适当反变形量;
19.根据船体轴系拉线及船体轴系施工工艺要求,切割主机基座、齿轮箱座、制动器座腹板余量,安装定位主机座面板、齿轮箱座面板、制动器座面板,主机座面板、齿轮箱座面板、制动器座面板的安装高度偏差为0~-2mm;船体外板按开孔样开孔,吊装定位尾轴管、托架臂,尾轴管前端面零对零安装,后端面向下放置适当反变形量,做好支撑加强,安装托架臂与船体结构及覆板,安装轴出口处尾轴管覆板;
20.主机基座、齿轮箱座和制动器座装配报检,尾轴管、托架臂安装定位数据报检;
21.主机基座、齿轮箱座和制动器座焊接并报验,轮机专业测量基座数据,安装焊接主机基座、齿轮箱座、制动器座的固定垫片;
22.艉轴管后轴承座与托架臂下口焊接
23.待焊完冷却后,二次拉线重新测量艉轴管前后端面数据,复查是否符合精度要求并及时调整;
24.艉轴前轴承座与加强板、实肋板焊接,为减少焊接变形,须采用间断焊法,焊接过程中监控前后端面数据,如有偏差及时调整焊接顺序;
25.复查艉轴管后端面数据,尾轴架与周边船体结构、外板覆板加强定位焊,然后按焊接顺序施焊;
26.轴出口处尾轴管与外板覆板焊接;
27.艉轴管和托架臂焊接报验,消除应力冷却48小时后拆除支撑加强,批磨码脚,艉轴管和托架臂进行无损检测、试密,艉轴管前后端面数据报验;
28.上建火工校正报验后,复查艉轴管前后端面数据,满足精度要求后转交轮机专业施工;
29.把整个船体轴系施工过程的监控数据整理成册,作为后续船的指导依据。
30.进一步地,密性试验时应从船中逐步向首尾两端压载,以此控制密性试验对船体龙骨挠度的影响。
31.进一步地,对所述主船体进行压载时,根据上建焊接、上建火工对主船体艏艉翘和龙骨挠度的影响适当增加部分压载。
32.进一步地,每天上午9:00、下午15:00监控主船体状态并做好记录,主船体状态包括中心状态、左右水平状态、龙骨挠度状态、首尾翘状态。
33.进一步地,艉轴管后轴承座与托架臂下口的焊接要求:
34.正式焊接前须由焊工进行加强定位焊,托架焊接前采用割炬对焊接部位及其两侧100mm范围内进行预热,预热温度为120~200℃;
35.焊接时由2名焊工分别在尾轴架下口对称进行施焊,打底焊及盖面焊均采用co2气体保护焊;
36.尾轴架上口周边船体结构焊接,注意尾轴架上口与结构暂不焊,严格按焊接工艺要求施焊,焊接过程中应监控变形与数据变化。
37.进一步地,按焊接顺序施焊具体为:
38.正式焊接前须由焊工在舱内、舱外进行加强定位焊;
39.焊接程序为先进行舱内结构焊接,后进行舱外焊接;
40.焊接时由1名焊工分别在尾轴架支臂上对称进行施焊;
41.舱外首先进行覆板对接缝焊接,打底焊及盖面焊均采用co2气体保护焊,搭接对接缝从两侧向中间逐层堆焊,保证根部熔合良好;
42.焊接覆板与尾轴架支臂的仰角焊缝,尾轴架焊接前采用割炬对焊接部位及其两侧100mm范围内进行预热,预热温度为120~200℃;
43.焊接覆板塞焊孔,必须从孔的四周向中间逐层堆焊,保证根部熔合良好,焊接时应分散均匀地进行;
44.最后焊接覆板与船体外板的平角焊缝;
45.每焊完一道焊需等焊缝冷却后再施下一道焊,过程中加强监控后端面数据,如发现数据偏差,则应及时调整焊接时机和顺序。
46.进一步地,轴出口处尾轴管与外板覆板的焊接顺序为:
47.首先进行覆板对接缝焊接,打底焊及盖面焊均采用co2气体保护焊,搭接对接缝从两侧向中间逐层堆焊,保证根部熔合良好;
48.焊接覆板与艉轴管的仰角焊缝,焊接前采用割炬对焊接部位及其两侧100mm范围内进行预热,预热温度为120~200℃;
49.焊接覆板塞焊孔,必须从孔的四周向中间逐层堆焊,保证根部熔合良好,焊接时应分散均匀地进行;
50.最后焊接覆板与船体外板的平角焊缝。
51.进一步地,对焊接材料的要求:
52.e5015焊条φ3.2mm,焊条使用前须经300~350℃烘干1~2小时,并存放在焊条保温筒内,焊接过程中保温筒须通电保温,焊条随用随取,为了加强焊接变形的控制,须经严格执行焊材选用原则,禁止采用φ4.0mm焊条进行施工:
53.co2气体保护焊焊丝采用supercored-71焊丝,φ1.2mm。
54.进一步地,手工焊的工艺参数为:焊条直径φ3.2mm,平焊电流110~150a,立焊电流100~130a,横焊电流100~140a,仰焊电流90~130a;
55.co2气体保护焊的工艺参数为:焊丝直径φ1.2mm,焊接电流110~160a,焊接电压20~24v,焊接速度22~24m/h,干伸长8~15mm,气流量10~15l/min。
56.有益效果
57.本发明与现有技术相比,具有以下优点:
58.本发明通过在上建上船台搭载工序的同时进行船体轴系工序施工,船体轴系工序和上建焊接、上建火工校正工序并行施工,与传统工艺过程相比,本发明的整个轴系施工周期可以提前15~20天,为油漆施工、管子安装、电缆拉放提供充裕施工时间,保证了下水项目的完整性,同时可以使整个船舶建造的施工周期可以缩短15~20天,在公司总体资源紧张的大环境下,工序的前移和周期的缩短,能有效释放劳力、设备、场地,为公司节省各方面的资源成本,对公司的统筹生产意义十分重大。
附图说明
59.图1为常规的船体轴系施工程序图;
60.图2为常规的生产工序安排图;
61.图3为发明的船体轴系施工程序图;
62.图4为发明的生产工序安排图;
63.图5为艉轴前轴承座与加强板、实肋板的焊接顺序图;
64.图6为轴出口处尾轴管、外板覆板的焊接顺序图。
具体实施方式
65.下面结合附图中的具体实施例对本发明做进一步的说明。
66.参阅图3~6,一种基于船体轴系施工工艺缩短船舶建造周期的方法,包括:
67.(1)完成对主船体装焊、外板及主甲板火工矫正。
68.(2)完成对主船体密性试验报验,密性试验时应从船中逐步向首尾两端压载,以此控制密性试验对船体龙骨挠度的影响。
69.(3)根据《设备压载布置图》对主船体进行压载,对主船体进行压载时,根据上建焊接、上建火工对主船体艏艉翘和龙骨挠度的影响适当增加部分压载。
70.(4)设置主船体的标杆观测点,每天固定时间监控主船体状态并做好记录;每天上午9:00、下午15:00监控主船体状态并做好记录,直到整个船体轴系工序施工完成,主船体状态包括中心状态、左右水平状态、龙骨挠度状态、首尾翘状态。如下表1所示为记录的表格。
[0071][0072]
表1
[0073]
(5)根据记录的主船体状态数进行船体轴系工序施工。
[0074]
(6)在船体轴系工序施工过程中,进行上建分段上船台搭载工序施工,以及进行上建火工校正工序施工。
[0075]
(7)在上建火工校正工序结束前完成船体轴系工序施工。
[0076]
进行船体轴系工序施工包括:
[0077]
(1)根据第一次记录的船体状态数据调整好样杆基线,以及确定船体轴系的首尾基准点,并对船体轴系进行一次拉线报验。
[0078]
根据上建焊接、上建火工校正对主船体艏艉翘和龙骨挠度的影响,确定艉基点向下放置适当反变形量。
[0079]
(2)根据船体轴系拉线及船体轴系施工工艺要求,切割主机基座、齿轮箱座、制动
器座腹板余量,安装定位主机座面板、齿轮箱座面板、制动器座面板,主机座面板、齿轮箱座面板、制动器座面板的安装高度偏差为0~-2mm;船体外板按开孔样开孔,吊装定位尾轴管、托架臂,尾轴管前端面零对零安装,后端面向下放置适当反变形量,做好支撑加强,安装托架臂与船体结构及覆板,安装轴出口处尾轴管覆板。
[0080]
(3)主机基座、齿轮箱座和制动器座装配报检,尾轴管、托架臂安装定位数据报检。
[0081]
(4)主机基座、齿轮箱座和制动器座焊接并报验,轮机专业测量基座数据,安装焊接主机基座、齿轮箱座、制动器座的固定垫片。
[0082]
(5)艉轴管后轴承座与托架臂下口焊接。
[0083]
焊接要求:
[0084]
①
正式焊接前须由焊工进行加强定位焊,托架焊接前采用割炬对焊接部位及其两侧100mm范围内进行预热,预热温度为120~200℃;
[0085]
②
焊接时由2名焊工分别在尾轴架下口对称进行施焊,打底焊及盖面焊均采用co2气体保护焊。
[0086]
尾轴架上口周边船体结构焊接,注意尾轴架上口与结构暂不焊,严格按焊接工艺要求施焊,焊接过程中应监控变形与数据变化。
[0087]
(6)待焊完冷却后,二次拉线重新测量艉轴管前后端面数据,复查是否符合精度要求并及时调整。
[0088]
(7)艉轴前轴承座与加强板、实肋板焊接,为减少焊接变形,须采用间断焊法,焊接过程中监控前后端面数据,如有偏差及时调整焊接顺序,如图5所示。
[0089]
(8)复查艉轴管后端面数据,尾轴架与周边船体结构、外板覆板加强定位焊,然后按焊接顺序施焊。
[0090]
焊接顺序:
[0091]
①
正式焊接前须由焊工在舱内、舱外进行加强定位焊;
[0092]
②
焊接程序为先进行舱内结构焊接,后进行舱外焊接;
[0093]
③
焊接时由1名焊工分别在尾轴架支臂上对称进行施焊;
[0094]
④
舱外首先进行覆板对接缝焊接,打底焊及盖面焊均采用co2气体保护焊,搭接对接缝从两侧向中间逐层堆焊,保证根部熔合良好;
[0095]
⑤
焊接覆板与尾轴架支臂的仰角焊缝,尾轴架焊接前采用割炬对焊接部位及其两侧100mm范围内进行预热,预热温度为120~200℃;
[0096]
⑥
焊接覆板塞焊孔,必须从孔的四周向中间逐层堆焊,保证根部熔合良好,焊接时应分散均匀地进行;
[0097]
⑦
最后焊接覆板与船体外板的平角焊缝。
[0098]
每焊完一道焊需等焊缝冷却后再施下一道焊,过程中加强监控后端面数据,如发现数据偏差,则应及时调整焊接时机和顺序。
[0099]
(9)轴出口处尾轴管与外板覆板焊接。
[0100]
焊接顺序为:
[0101]
①
首先进行覆板对接缝焊接,打底焊及盖面焊均采用co2气体保护焊,搭接对接缝从两侧向中间逐层堆焊,保证根部熔合良好;
[0102]
②
焊接覆板与艉轴管的仰角焊缝,焊接前采用割炬对焊接部位及其两侧100mm范
围内进行预热,预热温度为120~200℃;
[0103]
③
焊接覆板塞焊孔,必须从孔的四周向中间逐层堆焊,保证根部熔合良好,焊接时应分散均匀地进行;
[0104]
④
最后焊接覆板与船体外板的平角焊缝,如图6所示。
[0105]
(10)艉轴管和托架臂焊接报验,消除应力冷却48小时后拆除支撑加强,批磨码脚,艉轴管和托架臂进行无损检测、试密,艉轴管前后端面数据报验。
[0106]
(11)上建火工校正报验后,复查艉轴管前后端面数据,满足精度要求后转交轮机专业施工。
[0107]
(12)把整个船体轴系施工过程的监控数据整理成册,作为后续船的指导依据。
[0108]
在本发明的工序过程中,
[0109]
对焊接材料的要求:
[0110]
e5015焊条φ3.2mm,焊条使用前须经300~350℃烘干1~2小时,并存放在焊条保温筒内,焊接过程中保温筒须通电保温,焊条随用随取,为了加强焊接变形的控制,须经严格执行焊材选用原则,禁止采用φ4.0mm焊条进行施工:
[0111]
co2气体保护焊焊丝采用supercored-71焊丝,φ1.2mm。
[0112]
对焊接工艺参数的要求,
[0113]
手工焊的工艺参数为:焊条直径φ3.2mm,平焊电流110~150a,立焊电流100~130a,横焊电流100~140a,仰焊电流90~130a;
[0114]
co2气体保护焊的工艺参数为:焊丝直径φ1.2mm,焊接电流110~160a,焊接电压20~24v,焊接速度22~24m/h,干伸长8~15mm,气流量10~15l/min。
[0115]
手工焊
[0116]
焊条直径(mm)平焊电流(a)立焊电流(a)横焊电流(a)仰焊电流(a)φ3.2110~150100~130100~14090~130
[0117]
co2气体保护焊
[0118][0119]
以上所述的仅是本发明的优选实施方式,应当指出对于本领域的技术人员来说,在不脱离本发明结构的前提下,还可以作出若干变形和改进,这些都不会影响本发明实施的效果和专利的实用性。