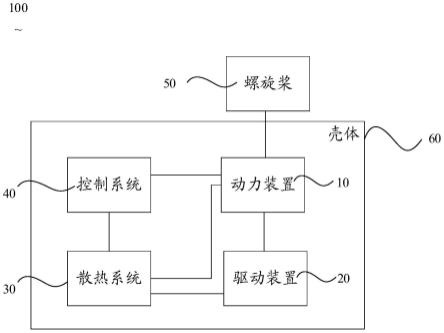
1.本技术涉及船舶技术领域,具体涉及一种推进器及船舶设备。
背景技术:2.目前的推进器主要使用的动力装置为内燃机或电动机。内燃机驱动的推进器噪声大、污染环境、能量利用率低,电动机驱动的推进器利用电动机将电能转化为动能,并将电动机的输出连接到螺旋桨,将电动机的输出动力转为竹筏的推进动力。电动机取得的推进器的优点是能量利用率高、静音、无排放等,但目前的电动机驱动的推进器暂无成熟解决方案,多为分体设计,即动力装置、驱动装置、散热系统、控制系统等分别作为独立零部件,安装于船舶设备的不同部位。这种分体式设计提高了用户安装难度,并且导致推进器各组成部件需要分别设计布置防水结构,且降低船舶设备的空间利用率,提高了推进器的成本。
技术实现要素:3.本技术提出了一种推进器及船舶设备。
4.为解决上述技术问题,本技术采用的一个技术方案是:提供一种推进器,该推进器包括壳体、动力装置、驱动装置、控制系统和散热系统及螺旋桨,动力装置、驱动装置、控制系统和散热系统设置于壳体内,螺旋桨与动力装置连接;其中,驱动装置与动力装置连接,用于驱动并控制动力装置;控制系统与驱动装置、散热系统进行电连接,用于控制驱动装置及散热系统;散热系统与动力装置及驱动装置连接,用于为动力装置与驱动装置散热。
5.其中,控制系统包括远程终端组件,远程终端组件与驱动装置及散热系统电连接,用于接收驱动装置回传的动力装置的温度信号,基于温度信号控制散热系统。
6.其中,散热系统包括泵组件、储液装置及换热器组件,泵组件与远程终端组件连接,用于基于温度信号调整散热效率;储液装置用于存储冷却液;换热器组件用于将冷却液与外界环境换热;动力装置及驱动装置均设有内部散热流道,泵组件、储液装置、换热器组件、动力装置的内部散热流道以及驱动装置的内部散热流道之间通过管道连接。
7.其中,散热系统还包括降压组件,用于将电源电压转换为泵组件的电压。
8.其中,泵组件包括泵及泵控制器,泵通过管道与储液装置、换热器组件、动力装置的内部散热流道以及驱动装置的内部散热流道连接;泵控制器与远程终端组件以及泵连接,用于基于温度信号调节泵的功率。
9.其中,动力装置包括动力装置本体及动力装置壳体,动力装置本体安装于动力装置壳体内,动力装置壳体上开设有内部散热流道,且在靠近动力装置本体一侧设置有散热齿。
10.其中,控制系统还包括通信协议转换组件,通信协议转换组件与驱动装置、远程终端组件电连接,用于转换驱动装置、远程终端组件之间的通信协议。
11.其中,推进器还包括显示组件,显示组件与控制系统和/或驱动装置电连接,显示组件设置于壳体的窗口处,用于显示航行数据。
12.其中,推进器还包括机架,壳体安装于机架上,机架设有传动轴,传动轴用于与动力装置及螺旋桨连接。
13.其中,推进器还包括操纵装置,操纵装置包括操作把手与操作杆,操作把手与操作杆连接,操作杆与机架连接。
14.其中,推进器还包括减震组件,减震组件安装与动力装置与机架之间,用于减少动力装置传导至机架的震动。
15.为解决上述技术问题,本技术采用的另一个技术方案是:提供一种船舶设备,该船舶设备包括上述的推进器。
16.本技术的有益效果是:区别于现有技术的情况,本技术推进器将推进器的动力装置、驱动装置、控制系统和散热系统装配于一体,设置于一个壳体内,有利于提高船舶设备的空间利用率,降低用户的安装难度,并且有助于减少推进器之间连接线缆的长度,减少密封件与密封结构的使用,降低整个推进器的物料成本,提高推进器的美观程度。
附图说明
17.图1是本技术推进器一实施例的结构示意框图;
18.图2是本技术推进器第一实施例的结构示意图;
19.图3是本技术推进器第二实施例一侧面的结构示意图;
20.图4是本技术推进器第二实施例另一侧面的结构示意图;
21.图5是本技术散热系统一实施例的结构示意图;
22.图6是本技术散热系统一实施例的散热流程示意图;
23.图7是本技术动力装置内部散热流道一实施例的截面示意图;
24.图8是本技术散热齿一实施例的结构示意图;
25.图9是本技术推进器一实施例的剖面示意图;
26.图10是本技术推进器第三实施例的结构示意图;
27.图11是申请船舶设备一实施例的结构示意图。
具体实施方式
28.下面将结合本技术实施例中的附图,对本技术实施例中的技术方案进行清楚、完整地描述,显然,所描述的实施例仅是本技术的一部分实施例,而不是全部的实施例。基于本技术中的实施例,本领域普通技术人员在没有做出创造性劳动前提下所获得的所有其他实施例,都属于本技术保护的范围。
29.本技术首先提出一种推进器,如图1所示,图1是本技术推进器一实施例的结构示意框图。本实施的推进器100包括:动力装置10、驱动装置20、散热系统30、控制系统40、螺旋桨50及壳体60。
30.动力装置10、驱动装置20、散热系统30和控制系统40设置于壳体60内,螺旋桨50与动力装置10连接;其中,驱动装置20与动力装置10连接,用于驱动并控制动力装置10;控制系统40与驱动装置20、散热系统30进行电连接,用于控制驱动装置20及散热系统30;散热系统30与动力装置10及驱动装置20连接,用于为动力装置10与驱动装置20散热。
31.其中,动力装置10包括电机,动力装置10用于将输入的电能转化为动能。动力装置
10、驱动装置20、散热系统30和控制系统40设置于壳体60内,有利于减少动力装置10、驱动装置20、散热系统30和控制系统40之间的线缆连接,减少推进器100的防水结构的设置的数量。
32.散热系统30与控制系统40集成设置于一体,可以提高船舶设备的空间利用率,且降低了用户的安装难度,提高推进器100的美观程度。
33.综上所述,区别于现有技术,本技术的推进器100将推进器100的动力装置10、驱动装置20、散热系统30和控制系统40装配于一体,设置于一个壳体60内,有利于提高船舶设备的空间利用率,降低用户的安装难度,并且有助于减少推进器100之间连接线缆的长度,减少密封件与密封结构的使用,降低整个推进器100的物料成本,提高推进器100的美观程度。
34.如图2-4所示,图2是本技术推进器第一实施例的结构示意图;图3是本技术推进器第二实施例一侧面的结构示意图;图4是本技术推进器第二实施例另一侧面的结构示意图。
35.推进器100的动力装置10、驱动装置20、控制系统40和散热系统30装配于壳体60内。动力装置10设置于推进器100的整体中心位置,驱动装置20可设置于动力装置10的上侧,用于驱动并控制动力装置10,控制系统40布置于动力装置10的一侧,散热系统30布置于动力装置10的另一侧。推进器100采用如图2-4所示的布局方式的优势在于能够实现推进器100的最小体积,且布线方便,能够减少线路(无论是电缆还是水管)的长度,达到节省成本的目的。在其他实施例中,控制系统40及散热系统30也可布置于动力装置10的其他方位上,在此不作限制。
36.可选地,如图3-4所示,控制系统40包括远程终端组件41,远程终端组件41与驱动装置20及散热系统30电连接,用于接收驱动装置20回传动力装置10的温度信号,基于温度信号控制散热系统30。
37.远程终端组件41可以为远程终端单元(remote terminal unit,rtu),远程终端单元为一种针对通信距离较长和工业现场环境恶劣而设计的具有模块化结构的、特殊的计算机测控单元,远程终端单元将末端检测仪表和执行机构与远程调控中心的主计算机连接起来,具有远程数据采集、控制和通信功能,能接收主计算机的操作指令,控制末端的执行机构动作。控制系统40采用远程终端组件41可以提高推进器100的通信效率,且可使推进器100适用于其他恶劣环境。
38.远程终端组件41与驱动装置20进行电连接,并通过螺钉等方式固定于动力装置10的一侧,驱动装置20能够获取动力装置10的运行参数(如转速信号,温度信号,电流信号以及电压信号等),驱动装置20获取动力装置10的温度信号,并将温度信号回传至远程终端组件41,远程终端组件41能够基于温度信号控制散热系统30的散热效率。
39.远程终端组件41还可以实现与云端的连接,可接收云端的操作指令或数据后控制推进器对应的模块响应。
40.可选地,在其他实施例中,控制系统40还包括通信协议转换组件42,通信协议转换组件42与驱动装置20、远程终端组件41电连接,用于转换驱动装置20、远程终端组件41之间的通信协议。
41.在本实施例中,远程终端组件41的协议为控制器局域网总线(can,controller area network)协议,驱动装置20的协议为485协议,485协议可使该标准的数字通信络能在远距离条件下以及电噪声的环境下有效传输信号。通信协议转换组件42为485转can模块,
通信协议转换组件42与驱动装置20、远程终端组件41连接,能够转换驱动装置20与远程终端组件41之间的通信协议,除了转换驱动装置20与远程终端组件41的协议外,还可以实现推进器的各个模块(若协议不同)的协议转换。经过协议转换后,远程终端组件41就能从驱动装置20接收动力装置10的温度信号,从而获取动力装置10的具体温度,进而控制散热系统30的散热功率,具体地,在本实施例中,当动力装置10的温度为40℃以下时,可设置散热系统30的功率为10%;当动力装置10的温度为70℃以上时,可设置散热系统30的功率为100%,当动力装置10温度为40-70℃时,可设置散热系统30的功率为10%-100%之间,且可设置动力装置10与散热系统30的功率之间存在线性关系。在其他实施例中,动力装置10的温度与散热系统30的功率的关系并不局限于上述的线性关系,也可设置为其他关系,在此不作限定。在其他实施例中,当远程终端组件41与驱动装置20之间的协议相同时,可不使用通信协议转换组件42进行协议转换,直接将远程终端组件41与驱动装置20连接后进行信息交互。
42.通信协议转换组件42除了进行协议转换外,还可以提供更多的接口,当驱动装置20上设置的接口不足以满足需求,又需要额外增加连接模块或部件时,可通过通信协议转换组件42提供接口用于连接其他的部件,提高推进器100的拓展性,以实现更多的功能。
43.可选地,如图4所示,散热系统30包括:泵组件31、储液装置32及换热器组件33。
44.泵组件31与远程终端组件41连接,用于基于温度信号调整散热效率。储液装置32用于存储冷却液;换热器组件33用于将冷却液与外界环境换热。
45.动力装置10及驱动装置20均设有内部散热流道,泵组件31、储液装置32、换热器组件33、动力装置10的内部散热流道以及驱动装置20的内部散热流道之间通过管道连接。
46.如图2及图4所示,泵组件31及储液装置32设置于壳体60的内部,且设置于动力装置10的一侧,换热器组件33通过管道延伸设置于壳体60外,与泵组件31及储液装置32连接,用于将冷却液与外界环境换热。
47.具体地,泵组件31包括泵311及泵控制器312。
48.泵311通过管道与储液装置32、换热器组件33、动力装置10的内部散热流道以及驱动装置20的内部散热流道连接。泵控制器312与远程终端组件41以及泵311连接,用于基于温度信号调节泵311的功率。
49.其中,泵组件31中的泵311的作用是强制散热系统30中的冷却液流动,加速散热循环的进行,提高散热系统30的散热效率。泵控制器312用于控制泵311的效率。本技术中的泵311不限于机械泵或电机泵,能够强制液体流动的装置即可;且泵311不限动力源,使用外界电源或电机出轴驱动泵等方式均可。
50.储液装置32用于储存冷却液,并提供冷却液加注口(冷却液加注口是指加注冷却液进储液装置32内的入口)。其中,冷却液包括但不限于水、专用冷却液、冷却油等。本实施例中,冷却液使用乙二醇溶液,优点在于价格低,冷却效果好。储液装置32可以是储水装置(如水箱等),其他形式的储液装置32如储液罐、油箱等也可作为本技术的储液装置32,本技术中的储液装置32可独立设置也可以集成在泵311、驱动装置20、动力装置10以及换热器组件33等任一结构中。
51.换热器组件33与储液装置32连接,用于散发热量至外界环境中,如图3-4所示,换热器组件33设置于机架80上,可与空气、推进器100周围水等进行热交换。
52.如图5-6所示,图5是本技术散热系统一实施例的结构示意图;图6是本技术散热系统一实施例的散热流程示意图。如图5所示,储液装置32、泵311及驱动装置20的内部散热流道及动力装置10的内部散热流道通过管道互相连接。
53.图5的示意图不代表此散热系统30中的部件空间位置关系,本实施例中不限制散热系统30的部件空间位置布置方式;散热系统30的内循环散热利用自带的冷却液,避免了外部水体的影响。冷却液可以不仅限于水、油、特质冷却液等,还可以选用防腐、防冻冷却液等提高散热系统30的鲁棒性。
54.且本实施例中散热系统30的冷却液流向由泵311决定,如图6所示流向为储液装置32、泵311、驱动装置20的内部散热流道、动力装置10的内部散热流道及换热器组件33。
55.散热系统30的工作方式为:泵311开始工作,使散热系统30中的冷却液开始流动。低温冷却液从储液装置32经过管道流入驱动装置20的内部散热流道,与驱动装置20进行热交换后,再流入动力装置10的内部散热流道中,与动力装置10进行热交换,流出高温冷却液。高温冷却液流入换热器组件33,并通过换热器组件33令高温冷却液与外界环境(可以是与外界水体也可以是周围空气)进行热交换,将高温冷却液中的热量散发到外界环境中,流出低温冷却液。低温冷却液流回储液装置32中,并重复上述过程,进行散热循环。在其他实施例中,冷却液流向不仅限图5及图6中所示流向,相反流向也可以,反向流动可以是冷却液流经储液装置32、换热器组件33、动力装置10的内部散热流道、驱动装置20的内部散热流道、泵311,最后冷却液流回储液装置32,冷却液反向流动同样也可以实现散热。在其他实施例中,还可以设置冷却液的其他流动方向以及流经的装置的顺序,在此不再赘述。
56.为了提高散热效率,本实施例中还对动力装置10的内部散热流道进行了设计。
57.可选地,如图7所示,图7是本技术动力装置内部散热流道一实施例的截面示意图。动力装置10包括动力装置本体11及动力装置壳体12,动力装置本体11安装于动力装置壳体12内,动力装置10的内部散热流道13设置于动力装置壳体12上,且在靠近动力装置本体11一侧设置散热齿131。
58.本实施例在动力装置10的内部散热流道13及驱动装置20的内部散热流道13中可设置散热齿131。以动力装置10的内部散热流道13为例,可在靠近动力装置本体11的一侧添加了散热齿131,每个内部散热流道13可设置5个散热齿131,共可设置12个内部散热流道13,散热齿131共可设置60个,其中,每个内部散热流道13的散热齿131的个数,内部散热流道13的个数等可以根据需要进行调整,并不局限于本实施中的数量。本实施中在内部散热流道13中添加了散热齿131的目的是增大冷却液与动力装置本体11发热面的接触面积。如图7所示的动力装置壳体12可通过挤出的方式进行制造。也可以采用机加工等的方式制造出来。通过挤出的方式进行制造的优点在于,成型简单,且效率较高,且物料损耗小。
59.如图8所示,图8是本技术散热齿一实施例的结构示意图;在光滑的内部流道设置如图8所示的散热齿131的形状,相较于光滑的内部流道,在相同的流道长度下,设置散热齿131可使与冷却液动力装置本体11的接触面积增加。
60.与光滑内部散热流道相比,增加散热齿131可使散热齿131的内部散热流道13靠近动力装置本体11一侧的接触长度增加。添加散热齿131的内部散热流道13与光滑内部散热流道相比,在相同的流道长度下,其内部散热流道13的截面周长也增加,接触面积增加,而相较于光滑的内部散热流道,设置散热齿131的内部散热流道13的降低的容积并不多。
61.有上述可知,通过设置散热齿131,能够增加动力装置10的散热面积,虽然内部散热流道13的腔体的截面面积降低了,但是在相同的流道长度下,流道容积与原来光滑壁面相比降低得并不多,整体来看,增加散热齿131后,能够使动力装置10的散热效果更佳,散热效率高。
62.散热齿131的形状不仅限于图8中所示形状,在其他实施例中,散热齿131也可以为其他形状,在此不作限制。
63.动力装置10的内部散热流道13的截面不仅限于图中所示形式,圆形、方形或以及其他形状的截面均可。目前的形状为类似于梯形的形状,在其他实施例中,可以将内部散热流道13设置成圆形或方形等的不同的形状,再在对应形状的内部散热流道13中设置散热齿131即可,在此不作限制。
64.本技术的散热系统30通过设置散热齿131,能够有效增加冷却液与动力装置10与驱动装置20的接触的面积,能够有效带走动力装置10与驱动装置20内部的结构所产生的热量,并进行热交换。并且增大了动力装置10与驱动装置20散热面积增大,使散热效果更佳,提高了热交换效率,能够避免动力装置10与驱动装置20的结构由于散热不佳而损坏,保证了动力装置10与驱动装置20的使用寿命。
65.可选地,散热系统30还包括降压组件34,降压组件34与泵组件31及电源连接,用于将电源电压转换为泵组件31的电压。在其他实施中,若电源电压即为泵组件31的工作电压,则无需设置降压组件34,降压组件34可进行省略设置。
66.可选地,如图2所示,本实施例中推进器100还包括显示组件70,显示组件70与控制系统40和/或驱动装置20电连接,显示组件70设置于壳体60的窗口处,用于显示航行数据。
67.显示组件70设置于壳体60的窗口处,与控制系统40和/或驱动装置20电连接。在本实施例中,显示组件70分别与控制系统40以及驱动装置20电连接,可在推进器100在工作过程中显示航行数据。航行数据包括但不限于电源剩余电量、散热系统30的散热效率、动力装置10的工作效率、云端的指令以及数据。
68.显示组件70还用于显示动力装置10的温度信号、转速信号、电流信号及电压信号,及显示推进器100各个模块的运行状态,用户可通过显示组件70实现可以对推进器100的实时监控。
69.可选地,如图9所示,图9是本技术推进器一实施例的剖面示意图,本实施例的推进器100还包括机架80,壳体60安装于机架80上,机架80设有传动轴81,传动轴81用于与动力装置10及螺旋桨50连接。
70.传动轴81与动力装置10的输出轴转动连接,并与螺旋桨50连接,用于传输动力装置10的输出转动扭矩至螺旋桨50。传动轴81可套设一套筒,用于保护传动轴81与动力装置10的输出轴转动连接。
71.动力装置10的输出轴的端面设有螺纹孔,传动轴81与动力装置10端面螺纹孔对应的位置同样设有螺钉孔,通过螺钉穿过螺钉孔可固定动力装置10以及传动轴81。
72.可选地,如图2-4所示,本实施例的推进器100还包括操纵装置90,操纵装置90包括操作把手91与操作杆92,操作把手91与操作杆92连接,操作杆92与机架80连接。
73.操纵装置90包括操作把手91与操作杆92,操作把手91用于为操作者提供功率控制的功能,并提供一个方便人手握持的部位,提高操作的舒适性,操作杆92与操作把手91及机
架80连接,用于加长操作把手91与机架80之间的距离。操作把手91上可设置对应的旋钮或者按钮,以操作把手91上设置按钮为例,按钮包括但不限于前进按钮、后退按钮等,按钮与控制系统40电连接,按钮经控制系统40发送至驱动装置20,驱动装置根据信号对动力装置10进行控制。
74.可选地,如图2-4所示,本实施例的推进器100还包括底座101,底座101设置有转轴组件102,转轴组件102与机架80连接,转轴组件102用于调整螺旋桨50的方向。
75.底座101用于将推进器100与船舶本体连接,底座设有转轴组件102,具体地,转轴组件102包括横轴和纵轴,操作把手91与机架80连接,机架80另一端与传动轴81连接,转轴组件102的横轴的两端设有连接部,连接部与横轴转动连接,连接部与机架80固定连接,使得机架80可绕横轴转动,传动轴81可上下运动,从而调整螺旋桨50的升降位置,纵轴上套设一个纵杆,纵杆与横轴连接,纵杆可绕纵轴转动,纵轴安装在底座101上,使得机架80可绕纵轴左右摆动,从而调整螺旋桨50的偏航角度,以调整船舶设备的航向方向。转轴组件102的结构简单、且易于制造。
76.可选地,如图10所示,图10是本技术推进器第三实施例的结构示意图,本实施例的推进器100还包括减震组件103,减震组件103安装与动力装置10与机架80之间,用于减少动力装置10传导至机架80的震动。
77.动力装置10的底部可设置减震组件103,减震组件103的一面与动力装置10相连,减震组件103的另一面与机架80相连,从而减少从动力装置10传递到机架80的振动,进而提高人员操作的舒适性并降低噪音。减震组件103可以为减震胶,在其他实施例中,减震组件103也可以为其他减震结构,在此不作限定。
78.如图10所示,本实施中推进器100还包括电源线104,电源线104用于与电源连接,为整体推进器100进行供电。
79.本技术进一步提出一种船舶设备,如图11所示,图11是本技术船舶设备一实施例的结构示意图。本实施例的船舶设备200包括上述任一实施例的推进器100及船舶本体210。
80.在船舶设备200行驶的状态下,螺旋桨50下沉于水面下,螺旋桨50推动水流,水流反作用力经机架本体80传递至船舶本体210,使得船舶本体210前进。当船舶设备200需要转向时,通过控制操纵装置90控制机架本体80上下摆动或者左右摆动,从而调整螺旋桨50的升降位置及偏转方向,从而实现船舶设备200的偏航转向。
81.以上所述仅为本技术的实施例,并非因此限制本技术的专利范围,凡是利用本技术说明书及附图内容所作的等效结构或等效流程变换,或直接或间接运用在其他相关的技术领域,均同理包括在本技术的专利保护范围内。