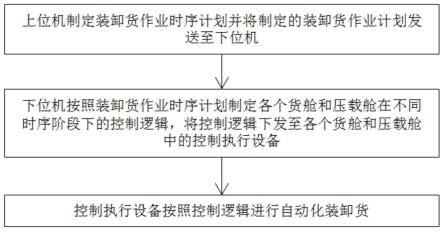
1.本发明属于油船自动化技术领域,具体涉及一种化学品船自动装卸货控制方法及系统,适用于系统高度集成,实现自动装卸货。
背景技术:2.现行化学品船液货装卸作业设备包括货泵系统设备、阀门遥控设备、液位遥测设备和惰气发生器设备,辅助作业设备包括船岸esds、压载水处理系统、蒸汽回收系统、可燃气体监测系统、洗舱机系统等设备,各个设备均由独立的供应商提供,不仅操作分散,自动化程度低,而且各个设备走协议通信存在通信延迟、通信故障和控制对象匹配性差等缺点,给船员操作带来了困难。在此情况下,迫切需要对液货装卸设备做系统集成,实现自动化装卸作业。
技术实现要素:3.本发明的目的是克服现有技术存在的上述问题,提供一种操作高度集成的化学品船自动装卸货控制方法及系统。
4.为实现以上目的,本发明提供了以下技术方案:一种化学品船自动装卸货控制方法,所述自动装卸货控制方法依次按照以下步骤进行:s1、通过上位机制定装卸货作业时序计划并将制定的装卸货作业计划发送至下位机,所述装卸货作业时序计划为各货舱的装卸货顺序及装卸货量、各压载舱的压排顺序及压排海水量;s2、所述下位机按照装卸货作业时序计划制定各个货舱和压载舱在不同时序阶段下的控制逻辑,并将控制逻辑下发至各个货舱和压载舱中的控制执行设备,由控制执行设备完成自动化装卸货。
5.步骤s1中,所述装卸货作业时序计划的制定依次按照以下步骤进行:步骤s11、由上位机中搭载的专家系统根据前三载化学品的化学性质以及人工输入的约束条件生成多个配载方案,并确定多个配载方案下的船舶姿态,其中,所述约束条件包括装货/卸货、货物种类、货量、码头允许的扬程和流量;步骤s12、通过上位机选取船舶姿态最好的配载方案作为最优配载方案,对最优配载方案进行人工校核,通过人工校核后以该最优配载方案作为装卸货作业时序计划输出至下位机。
6.步骤s11中,所述船舶姿态包括船舶纵倾、横倾、弯矩、剪力、稳性;步骤s12中,最优配载方案的选取步骤为先对船舶纵倾、横倾、弯矩、剪力、稳性进行中心化预处理,然后对中心化预处理结果进行加权处理,以权值最小的配载方案作为船舶姿态最好的配载方案。
7.步骤s2中,所述控制执行设备包括货泵系统、阀门遥控系统,在装货作业时,所述
货泵系统中的压载泵以及阀门遥控系统中的货舱进口阀门、压载舱排载阀门、压载舱压载阀门工作,在卸货作业时,所述货泵系统中的货油泵、压载泵以及阀门遥控系统中的货舱出口阀门、压载舱排载阀门、压载舱压载阀门工作。
8.在卸货作业时,所述下位机通过液位遥测系统实时监测各个货舱和压载舱的液位状态并将其反馈至上位机,当上位机检测到各个货舱中的实时液位均低于其设定液位时表示卸货完毕,卸货完毕后人工通过上位机选择需要扫舱的货舱、设定扫舱转速与惰气压力,所述下位机先根据来自上位机的扫舱转速、惰气压力制定扫舱策略,然后根据扫舱策略控制位于需要扫舱的货舱中的扫舱系统进行扫舱,当扫舱系统的惰气管路压力<0.01mpa时表示扫舱结束。
9.所述下位机与货泵系统、阀门遥控系统、液位遥测系统、扫舱系统上设置的分布式i/o模块通讯,下位机以响应时间、通信延迟时间、反馈变量精度及延迟为约束条件,通过神经网络算法生成控制执行设备的控制逻辑。
10.一种化学品船自动装卸货控制系统,所述自动装卸货控制系统包括上位机、下位机、控制执行设备,所述上位机与下位机信号连接,所述下位机与控制执行设备信号连接;所述上位机用于制定装卸货作业时序计划并将制定的装卸货作业计划发送至下位机;所述下位机用于按照装卸货作业时序计划制定各个货舱和压载舱在不同时序阶段下的控制逻辑,将控制逻辑下发至各个货舱和压载舱中的控制执行设备;所述控制执行设备用于根据下位机下发的控制逻辑进行自动化装卸货。
11.所述控制执行设备包括货泵系统、阀门遥控系统、液位遥测系统、扫舱系统,所述货泵系统包括位于多个压载舱中的多个压载泵、位于多个货舱中的多个货油泵,所述阀门遥控系统包括位于多个货舱中的多个货舱进口阀门、位于多个货舱中的多个货舱出口阀门、位于多个压载舱中的多个压载舱排载阀门、位于多个压载舱中的多个压载舱压载阀门,所述扫舱系统包括位于多个货舱中的多个惰气发生器。
12.与现有技术相比,本发明的有益效果为:1、本发明一种化学品船自动装卸货控制方法,先通过上位机制定装卸货作业时序计划并将制定的装卸货作业计划发送至下位机,装卸货作业时序计划为各货舱的装卸货顺序及装卸货量、各压载舱的压排顺序及压排海水量,下位机按照装卸货作业时序计划制定各个货舱和压载舱在不同时序阶段下的控制逻辑,并将控制逻辑下发至各个货舱和压载舱中的控制执行设备,由控制执行设备完成自动化装卸货,该设计高度集成,提高了装卸货自动化程度,降低了船员操作难度。因此,本发明提高了装卸货自动化程度,降低了船员操作难度。
13.2、本发明一种化学品船自动装卸货控制方法中,装卸货作业时序计划的制定步骤为,先由上位机中搭载的专家系统根据前三载化学品的化学性质以及人工输入的约束条件生成多个配载方案,并确定多个配载方案下的船舶姿态,然后通过上位机选取船舶姿态最好的配载方案作为最优配载方案,对最优配载方案进行人工校核,通过人工校核后以该最优配载方案作为装卸货作业时序计划输出至下位机,约束条件包括装货/卸货、货物种类、货量、码头允许的扬程和流量,该设计一方面根据装卸货需求,按照先后顺序给出货舱的目标装卸量和压载舱的压载量,同时满足了船舶姿态稳定、船体结构不受伤害的要求,另一方
面,经人工确定后再将得到的装卸货作业时序计划输出至下位机,人机交互性好。因此,本发明输出的装卸货作业时序计划不仅能满足装卸货需求,而且能满足船舶姿态稳定、船体结构不受伤害的要求,输出过程的人机交互性好。
14.3、本发明一种化学品船自动装卸货控制方法中,下位机与货泵系统、阀门遥控系统、液位遥测系统、扫舱系统上设置的分布式i/o模块通讯,下位机以响应时间、通信延迟时间、反馈变量精度及延迟为约束条件,通过神经网络算法生成控制执行设备的控制逻辑,避免了走协议通信带来的通信延迟、通信故障和控制对象匹配性差等缺点,实时性好、控制对象匹配性好。因此,本发明中控制系统的实时性好、控制对象匹配性好。
附图说明
15.图1为本发明中控制方法的流程图。
16.图2为本发明中控制系统的结构图。
17.图中,上位机1、下位机2、控制执行设备3、货泵系统31、压载泵311、货油泵312、阀门遥控系统32、货舱进口阀门321、货舱出口阀门322、压载舱排载阀门323、压载舱压载阀门324、液位遥测系统33、扫舱系统34。
具体实施方式
18.下面结合说明书附图和具体实施方式对本发明作进一步的说明。
19.参见图1、图2,一种化学品船自动装卸货控制方法,所述自动装卸货控制方法依次按照以下步骤进行:s1、通过上位机1制定装卸货作业时序计划并将制定的装卸货作业计划发送至下位机2,所述装卸货作业时序计划为各货舱的装卸货顺序及装卸货量、各压载舱的压排顺序及压排海水量;s2、所述下位机2按照装卸货作业时序计划制定各个货舱和压载舱在不同时序阶段下的控制逻辑,并将控制逻辑下发至各个货舱和压载舱中的控制执行设备3,由控制执行设备3完成自动化装卸货。
20.步骤s1中,所述装卸货作业时序计划的制定依次按照以下步骤进行:步骤s11、由上位机1中搭载的专家系统根据前三载化学品的化学性质以及人工输入的约束条件生成多个配载方案,并确定多个配载方案下的船舶姿态,其中,所述约束条件包括装货/卸货、货物种类、货量、码头允许的扬程和流量;步骤s12、通过上位机1选取船舶姿态最好的配载方案作为最优配载方案,对最优配载方案进行人工校核,通过人工校核后以该最优配载方案作为装卸货作业时序计划输出至下位机。
21.步骤s11中,所述船舶姿态包括船舶纵倾、横倾、弯矩、剪力、稳性;步骤s12中,最优配载方案的选取步骤为先对船舶纵倾、横倾、弯矩、剪力、稳性进行中心化预处理,然后对中心化预处理结果进行加权处理,以权值最小的配载方案作为船舶姿态最好的配载方案。
22.步骤s2中,所述控制执行设备3包括货泵系统31、阀门遥控系统32,在装货作业时,所述货泵系统31中的压载泵311以及阀门遥控系统32中的货舱进口阀门321、压载舱排载阀
门323、压载舱压载阀门324工作,在卸货作业时,所述货泵系统31中的货油泵312、压载泵311以及阀门遥控系统32中的货舱出口阀门322、压载舱排载阀门323、压载舱压载阀门324工作。
23.在卸货作业时,所述下位机2通过液位遥测系统33实时监测各个货舱和压载舱的液位状态并将其反馈至上位机1,当上位机1检测到各个货舱中的实时液位均低于其设定液位时表示卸货完毕,卸货完毕后人工通过上位机1选择需要扫舱的货舱、设定扫舱转速与惰气压力,所述下位机2先根据来自上位机1的扫舱转速、惰气压力制定扫舱策略,然后根据扫舱策略控制位于需要扫舱的货舱中的扫舱系统34进行扫舱,当扫舱系统34的惰气管路压力<0.01mpa时表示扫舱结束。
24.所述下位机2与货泵系统31、阀门遥控系统32、液位遥测系统33、扫舱系统34上设置的分布式i/o模块通讯,下位机2以响应时间、通信延迟时间、反馈变量精度及延迟为约束条件,通过神经网络算法生成控制执行设备3的控制逻辑。
25.一种化学品船自动装卸货控制系统,所述自动装卸货控制系统包括上位机1、下位机2、控制执行设备3,所述上位机1与下位机2信号连接,所述下位机2与控制执行设备3信号连接;所述上位机1用于制定装卸货作业时序计划并将制定的装卸货作业计划发送至下位机2;所述下位机2用于按照装卸货作业时序计划制定各个货舱和压载舱在不同时序阶段下的控制逻辑,将控制逻辑下发至各个货舱和压载舱中的控制执行设备3;所述控制执行设备3用于根据下位机2下发的控制逻辑进行自动化装卸货。
26.所述控制执行设备3包括货泵系统31、阀门遥控系统32、液位遥测系统33、扫舱系统34,所述货泵系统31包括位于多个压载舱中的多个压载泵311、位于多个货舱中的多个货油泵312,所述阀门遥控系统32包括位于多个货舱中的多个货舱进口阀门321、位于多个货舱中的多个货舱出口阀门322、位于多个压载舱中的多个压载舱排载阀门323、位于多个压载舱中的多个压载舱压载阀门324,所述扫舱系统34包括位于多个货舱中的多个惰气发生器。
27.实施例1:参见图1、图2,一种化学品船自动装卸货控制方法,具体按照以下步骤进行:s1、通过上位机1制定装卸货作业时序计划并将制定的装卸货作业计划发送至下位机2,所述装卸货作业时序计划为各货舱的装卸货顺序及装卸货量、各压载舱的压排顺序及压排海水量;s2、所述下位机2按照装卸货作业时序计划制定各个货舱和压载舱在不同时序阶段下的控制逻辑,并将控制逻辑下发至各个货舱和压载舱中的控制执行设备3,由控制执行设备3完成自动化装卸货;上述化学品船自动装卸货控制方法的控制系统,包括上位机1、下位机2、控制执行设备3,所述上位机1与下位机2信号连接,所述下位机2与控制执行设备3信号连接。
28.实施例2:与实施例1的不同之处在于:步骤s1中,所述装卸货作业时序计划的制定依次按照以下步骤进行:
步骤s11、由上位机1中搭载的专家系统根据前三载化学品的化学性质以及人工输入的约束条件生成多个配载方案,并确定多个配载方案下的船舶姿态,其中,所述约束条件包括装货/卸货、货物种类、货量、码头允许的扬程和流量,所述船舶姿态包括船舶纵倾、横倾、弯矩、剪力、稳性;步骤s12、通过上位机1选取船舶姿态最好的配载方案作为最优配载方案,对最优配载方案进行人工校核,通过人工校核后以该最优配载方案作为装卸货作业时序计划输出至下位机,其中,所述最优配载方案的选取步骤为先对船舶纵倾、横倾、弯矩、剪力、稳性进行中心化预处理,然后对中心化预处理结果进行加权处理,以权值最小的配载方案作为船舶姿态最好的配载方案。
29.实施例3:与实施例2的不同之处在于:所述控制执行设备3包括货泵系统31、阀门遥控系统32、液位遥测系统33、扫舱系统34,所述货泵系统31包括位于多个压载舱中的多个压载泵311、位于多个货舱中的多个货油泵312,所述阀门遥控系统32包括位于多个货舱中的多个货舱进口阀门321、位于多个货舱中的多个货舱出口阀门322、位于多个压载舱中的多个压载舱排载阀门323、位于多个压载舱中的多个压载舱压载阀门324,所述扫舱系统34包括位于多个货舱中的多个惰气发生器;步骤s2中,在装货作业时,所述货泵系统31中的压载泵311以及阀门遥控系统32中的货舱进口阀门321、压载舱排载阀门323、压载舱压载阀门324工作,在卸货作业时,所述货泵系统31中的货油泵312、压载泵311以及阀门遥控系统32中的货舱出口阀门322、压载舱排载阀门323、压载舱压载阀门324工作。
30.实施例4:与实施例3的不同之处在于:在卸货作业时,所述下位机2通过液位遥测系统33实时监测各个货舱和压载舱的液位状态并将其反馈至上位机1,当上位机1检测到各个货舱中的实时液位均低于其设定液位时表示卸货完毕,卸货完毕后人工通过上位机1选择需要扫舱的货舱、设定扫舱转速与惰气压力,所述下位机2先根据来自上位机1的扫舱转速、惰气压力制定扫舱策略,然后根据扫舱策略控制位于需要扫舱的货舱中的扫舱系统34进行扫舱,当扫舱系统34的惰气管路压力<0.01mpa时表示扫舱结束。
31.实施例5:与实施例4的不同之处在于:所述下位机2与货泵系统31、阀门遥控系统32、液位遥测系统33、扫舱系统34上设置的分布式i/o模块通讯,下位机2以响应时间、通信延迟时间、反馈变量精度及延迟为约束条件,通过神经网络算法生成控制执行设备3的控制逻辑。