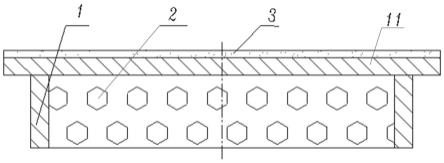
1.本实用新型属于通用非金属复合材料技术领域,尤其涉及一种低密度、高强度的非金属复合材料板,主要用于船舶重载场合甲板铺装,实现低密度高负载通用化地板工程应用。
背景技术:2.当前,船舶内部仓库为了实现通用化存储,要求地板对存储对象具有通用化的支撑、系固等功能,因此其地板不再使用简单的钢板构件,往往设计为功能化地板。功能化地板若简单的以钢制材料进行制造,会大大增加船体结构重量,对于船体总体指标、资源消耗均造成严重浪费,因此,功能化地板的轻量化设计成为一个亟待解决的问题。由于海上环境恶劣复杂,工作温度范围在-55~60℃,长期处在盐雾环境中,且有阻燃性要求,因此常见的轻量化地板材料几乎无法满足要求。当前舰船上典型的功能化地板材料采用轻质聚合物混凝土基材,虽具有一定的承载能力,但密度仍然较高,且该种材料脆性大易开裂,甚至局部脱落现象,无法适应船体变形工况,同时存在铺装工艺复杂、养护困难的问题,且密度与强度指标无法兼顾,因此需要寻求新型材料进行优化替代。
3.专利公开号为cn202017325u的中国专利公开一种金属复合地板,通过金属复合板和木质板压制而成的复合板材,解决了木质板材强度不足的问题,但木质板材属于易燃材料,不可以应用在舰船上。
4.专利公开号为cn110273530a的中国专利公开一种双层抗压亚克力地板,通过一种特殊的结构将两块亚克力板进行扣合,增强亚克力板材的强度,但亚克力板材本身不具备阻燃能力,且其材料本身质地硬而脆,无法适应船体变形和重载冲击工况,因此不可以应用在舰船上。
技术实现要素:5.针对现有的地板材料没有专门针对船体甲板和舱室甲板的材料,在材料的重量和强度方面无法做到兼顾的问题,本实用新型提供一种船用低密高强非金属复合地板,可以满足低密度高强度的应用场景,尤其是船用低密高强通用化地板铺装的迫切现实需求,解决了当前同类材料比重和强度无法兼顾的技术难题。
6.本实用新型的目的是以下述方式实现的:
7.一种船用低密高强非金属复合地板,包括塑料骨架,所述塑料骨架包括上部表面层和下部格栅结构,塑料骨架的格栅结构内填充有泡沫混凝土或泡沫铝,塑料骨架的表面层涂覆有一层耐磨层。
8.耐磨层为聚氨酯层。
9.塑料骨架的表面层与格栅结构一体成型。
10.所述塑料骨架材质为改性聚苯醚。
11.塑料骨架的格栅结构内表面涂刷聚氨酯胶水。
12.本实用新型提出的船用低密高强非金属复合地板材料,包括塑料骨架,塑料骨架包括上部表面层和下部格栅结构,塑料骨架的格栅结构内填充有泡沫混凝土或泡沫铝,塑料骨架的表面层涂覆有一层耐磨层。塑料骨架具有重量轻、强度高的特点;塑料骨架上下不对称设计,上部表面层提供高强度表面支撑,下部栅格结构用于减重,且格栅结构的空腔中填充泡沫混凝土或泡沫铝,增加阻燃性,同时提高格栅结构的支撑力;对填充过泡沫混凝土的表面层涂覆耐磨层,增强板材表面的耐磨性;本实用新型通过多元异构材料耦合技术途径,解决了铺装材料在重量和强度之间的兼顾性问题;本实用新型尤其适用于船体及其舱室甲板(如通用化贮存舱室)对于铺设材料的密度、强度和阻燃性都有较高要求的场合,且格栅结构内填充泡沫混凝土或泡沫铝不易开裂,也不会出现局部脱落现象,可以很好的适应船体变形工况,同时具有良好的铺装工艺性、耐磨性,很好的解决了上述工程问题,亦适用于其他同类应用场合。
附图说明
13.图1是塑料骨架的三视图。
14.图2是塑料骨架的格栅结构填充泡沫混凝土或泡沫铝后的三视图。
15.图3是本实用新型的整体结构示意图。
16.其中,1-塑料骨架,11-表面层,12-格栅结构,2-泡沫混凝土或泡沫铝,3-耐磨层。
具体实施方式
17.如图1-图3所示,一种船用低密高强非金属复合地板,包括塑料骨架1,塑料骨架具有重量轻、强度高的特点;所述塑料骨架1包括上部表面层11和下部格栅结构12,塑料骨架上下不对称设计,上部表面层11提供高强度表面支撑,下部栅格结构12用于减重;塑料骨架的格栅结构12内填充有泡沫混凝土或泡沫铝2,增加阻燃性,同时提高格栅结构的支撑力,填充泡沫混凝土或泡沫铝之前,在塑料骨架的格栅结构内表面涂刷聚氨酯胶水,增强塑料骨架的格栅结构与泡沫混凝土或泡沫铝的结合力;塑料骨架1的表面层涂覆有一层耐磨层3,增强非金属复合地板板材表面的耐磨性,耐磨层3可选用聚氨酯层。
18.塑料骨架的表面层与格栅结构一体成型。
19.所述工程塑料为改性聚苯醚,所述改性聚苯醚密度1.06g/cm3,阻燃性为v0(ul94),拉伸强度63mpa(10kn,20,mm/min) ,弯曲强度82mpa(3kn,20,mm/min),简支梁冲击强度27(2j,2.9m/s)。
20.本实用新型通过多元异构材料耦合技术途径,解决了铺装材料在重量和强度之间的兼顾性问题;本实用新型尤其适用于船体及其舱室甲板(如通用化贮存舱室)对于铺设材料的密度、强度和阻燃性都有较高要求的场合,亦适用于其他同类应用场合,可以很好的适应船体变形工况,同时具有良好的铺装工艺性、耐磨性,很好的解决了现有材料脆性大易开裂,甚至出现局部脱落现象的问题。
21.船用低密高强非金属复合地板的制备工艺
22.聚苯醚塑料骨架1按照已有的设计图纸进行注塑成型,在其下部格栅结构12内进行泡沫混凝土或泡沫铝2填充,具体步骤如下:
23.a)施工前用刷子在聚苯醚格栅结构12的内部全部涂刷一层阻燃型聚氨酯胶水,以
提高聚苯醚材料与泡沫混凝土之间的粘结性,所述聚苯醚格栅结构12的内部为格栅结构与填充物相接触的部位,涂刷完成后,静置干燥24小时后进行后续施工;
24.b)将水泥、粉煤灰、发泡剂等原材料根据工程需要按照设定比例进行搅拌发泡,混合均匀,制成泡沫混凝土2;
25.c)将发泡好的泡沫混凝土2填入聚苯醚塑料骨架的格栅结构12中,并修平;
26.d)静置12小时后进行保湿养护,养护时间不小于24小时,复合形成标准规格的聚苯醚-泡沫混凝土块,如图2所示;
27.e)对制备的聚苯醚-泡沫混凝土块进行打磨,使表面层11粗糙,用于增强聚氨酯耐磨层3与塑料骨架2的表面层11之间的粘接强度,打磨完毕后对聚苯醚-泡沫混凝土块上下表面进行双组份聚氨酯耐磨层3喷涂,达到上下全覆盖效果,耐磨层厚度可以根据需求进行调整。喷涂完毕后等待5-7天,待耐磨层完全硬化后,对其表面不平整的地方进行打磨,最终制成一块低密度高强度非金属复合地板材料。
28.所制备的非金属船用甲板材料密度小于1.3 g/cm3,抗压强度指标大于15mpa,6t载重(4轮)碾压耐磨试验大于5000次条件下,复合地板表面无明显磨痕。
29.船用低密高强非金属复合地板作为船用甲板上的铺设工艺
30.1)甲板预处理
31.将甲板上的杂物和铁锈清除干净,生锈严重的部位应用角磨机进行打磨干净,不用特意打磨平滑;清理甲板时可以用水冲洗甲板,也可以用风机或吸尘器清理,只要保证甲板表面清洁,甲板表面潮湿,可以进行施工作业,不影响效果,但施工时甲板表面不能有游离水,应用海绵吸干。
32.2)铺设复合地板板材
33.为保证船体或舱室甲板表面与复合地板板材粘接牢固,需要对船体或舱室甲板表面、复合地板板材底面(塑料骨架的格栅结构所在的面)进行除污处理,保证平面干净、无杂物;将聚氨酯胶水和有机填料混合,在船体或舱室甲板表面上涂抹均匀,达到找平厚度,然后将复合地板板材铺设在船体或舱室甲板表面上,并进行修平处理;
34.3)填充缝
35.由于船体或舱室甲板面积大,单块复合地板板材面积较小,需要多块复合地板板材依次铺设,相邻复合地板板材之间留有一定缝隙,使用具有粘接和弹性变形能力的填充缝材料进行填充,可保证铺设完成的地板的平整度和整体性,减少因船体变形导致的地板开裂、崩碎现象。为保证填充缝粘接牢固,待铺设好的复合地板板材固化后,需保证复合地板板材之间的缝隙干净、无杂物,将填充缝材料挤入缝隙中,并使用抹刀抹平,静置24小时,待7天后完全固化,完成铺设。
36.铺设完成后的甲板具有平整光滑的表面,其内部的聚苯醚-泡沫混凝土复合材质可以承载大应力而不发生破坏,表面的聚氨酯耐磨层提高了甲板整体的耐久性和耐磨性。整体材料具有阻燃、低毒、低密、高强的特点,基于该技术制作的材料,在密度1.2g/cm3的前提下,抗压强度指标可以达到15mpa以上。
37.以上所述的仅是本实用新型的优选实施方式,应当指出,对于本领域的技术人员来说,在不脱离本实用新型整体构思前提下,还可以作出若干改变和改进,这些也应该视为本实用新型的保护范围。