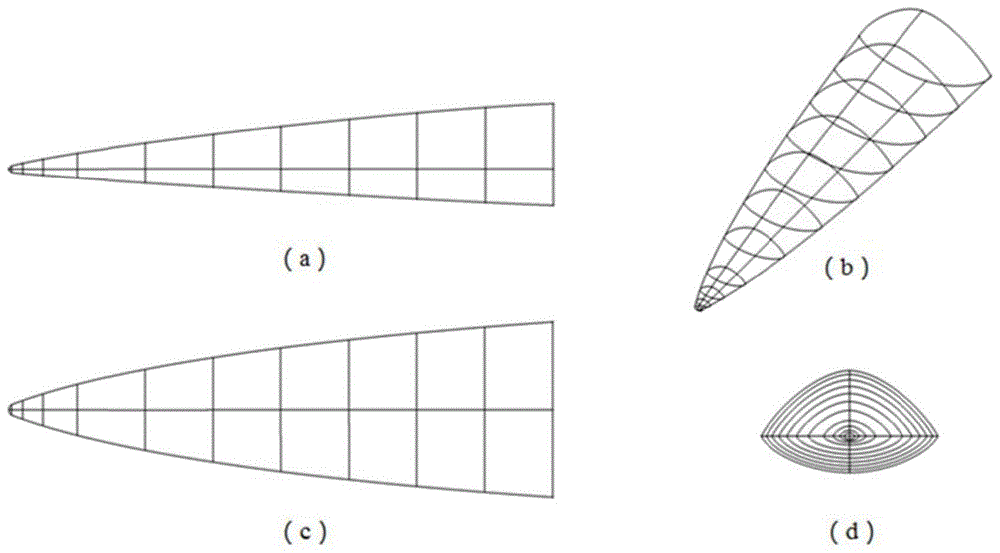
本发明涉及一种适用于面对称布局飞行器的新型升力体标准模型设计方法,属于飞行器气动布局设计领域。
背景技术:
:飞行器标准模型(简称标模)主要用于在风洞中开展特定类型试验,以考核风洞流场品质与测试能力、考察测量仪器设备性能,以及进行试验技术或测试技术验证等。我国在2002年颁布的国军标《高超声速风洞气动力试验方法》中,给出了hscm系列标模。该系列标模的典型气动特征为轴对称旋成体,主要服务于高静稳定裕度、轴对称气动布局研究。近年来,长航程、强机动、高精度正日益成为我国再入飞行器的发展方向。在此趋势下,新型飞行器的气动布局由传统轴对称简单外形向面对称高升力复杂构型方向发展。hscm系列标模对于新型面对称高升力气动布局低静稳定裕度、纵向与横航向气动特性差异显著等特点缺乏考虑,主要体现在不同风洞试验数据之间散差较大和横航向数据测量精度较低两个方面。为提高我国面对称布局飞行器气动特性预示精准度水平,提升精细化设计能力,迫切需要开展新型飞行器标模研制。技术实现要素:本发明解决的技术问题是:针对目前现有技术中,现有hscm系列标模无法体现新型面对称高升力布局飞行器的外形和气动特征,无法满足标模对于地面模拟设备和测试技术的考核要求的问题,提出了一种适用于面对称布局飞行器的新型升力体标准模型设计方法。本发明解决上述技术问题是通过如下技术方案予以实现的:一种适用于面对称布局飞行器的新型升力体标准模型设计方法,步骤如下:(1)确定新型升力体标准模型设计原则,根据该设计原则确定标准模型气动外形设计方案,所述标准模型包括椭球头及升力体;(2)利用数值模拟方法对步骤(1)所得标准模型气动外形进行气动特性计算及验证,并判断该标准模型气动特性是否满足标准模型设计标准,若满足设计标准,则进入步骤(3);若不满足设计标准,则返回步骤(1)对母线设计方程控制参数进行修改;(3)根据标准模型气动外形进行加工及检测。所述步骤(1)中,标准模型气动外形设计方案具体为:(1-1)确定升力体母线设计方程,对升力体母线进行设计;(1-2)根据步骤(1-1)所得升力体母线设计方程确定截面控制点,依据所得截面控制点确定截面曲线;(1-3)根据步骤(1-1)所得母线和(1-2)所得截面曲线确定标准模型气动外形。所述步骤(1)中,所述升力体母线包括上母线、下母线、侧缘母线,所述上母线、下母线、侧缘母线、截面曲线的方程p(u)均为:式中,vi,(i=0,1,2)为曲线的控制顶点坐标,wi,(i=0,1,2)为对应控制顶点的权因子,b2,i(u)为二次bernstein多项式,为组合数,u为控制变量参数。所述步骤(2)中,标准模型设计标准具体为:相同条件下,法向力与侧向力之比最大值不小于10,俯仰力矩与偏航力矩之比最大值不小于10。所述步骤(3)中,标准模型的加工步骤具体为:(3-1)对标准模型进行结构设计;所述标准模型包括前段、后段、隔热套、底盖、隔热垫片,所述隔热套套装于后段上,并与前段接触,所述隔热垫片安装于前段、后段连接处,所述底盖拧紧于后段尾部;(3-2)根据步骤(1)所得结构设计方案,对标准模型进行加工,并对标准模型进行基准面平行度检测;(3-3)基于三坐标检测结果对模型进行整体打光,保证轮廓误差≤±0.05mm。所述前段与后段成h6/g5配合,加工误差≤±0.05mm。所述步骤(1)中,新型升力体标准模型设计原则具体包括:(a)所述升力体气动布局采用左右面对称、上下非对称高升阻比构型;(b)所述升力体气动布局纵向投影与侧向投影面积不同;(c)无空气舵;(d)底部宽度小于两倍的底部高度。所述标准模型气动外形全长350~450mm,侧缘半径为1.0mm~2.0mm。所述基准面平行度通过检测工装进行检测,检测工装包括检测平面段及连接端,检测平面段与连接端为一体结构,且垂直设置于连接端上远离标准模型一侧。利用检测工装对标准模型基准面平行度进行检测,检测工装上平面与后段夹持基准面平行度≤0.01时标准模型加工合格。本发明与现有技术相比的优点在于:(1)本发明提供的一种适用于面对称布局飞行器的新型升力体标准模型设计方法,通过新型升力体标模能够体现新型面对称高升力布局飞行器的几何特征,同时能够反映低静稳定裕度、纵向与横航向气动特性差异显著等气动特点,该标模外形简单、采用参数化设计,能够在设计过程中通过改变参数改变气动布局外型,并且建立了统一的结构设计方案和工艺技术规范,能够适应不同风洞的测量要求;(2)本发明提供的新型升力体标准模型设计方法,设计的新型升力体标模可满足地面模拟设备和测试技术的考核要求,所形成的标模试验数据库可长期作为面对称高升力布局飞行器研制过程中风洞试验、数值计算方法与软件验证的基础,从而推动新型面对称布局飞行器气动特性预示技术水平的提高,提升精细化设计能力,增强飞行器系统的整体效能。附图说明图1为发明提供的标准模型三维气动布局外形图;图2为发明提供的标准模型外型控制参数示意图;图3为发明提供的标准模型升阻比曲线图;图4为发明提供的标准模型纵向焦点与航向压心曲线图;图5为发明提供的标准模型轴向力、法向力、侧向力系数曲线图;图6为发明提供的标准模型俯仰力矩、偏航力矩、滚转力矩系数曲线图图7为发明提供的标准模型结构示意图;图8为发明提供的加工后标准模型实物图;具体实施方式一种适用于面对称布局飞行器的新型升力体标准模型设计方法,针对现有标准模型无法满足新型飞行器研制需求,提出了椭球头+升力体的外形设计,如图1所示,具体设计方法步骤如下:(1)根据行业内当前设计趋势,确定所需的新型升力体标准模型设计原则,并根据该设计原则确定标准模型气动外形设计方案,标准模型包括椭球头及升力体;其中,新型升力体标准模型设计原则具体包括:(a)采用左右面对称、上下非对称高升阻比升力体气动布局;(b)升力体气动布局纵向投影与侧向投影面积不同;(c)不采用空气舵;(d)底部宽度小于两倍的底部高度;(e)纵向及航向静稳定裕度根据具体需求确定波动范围;(f)焦点随攻角、马赫数在一定范围内波动;标准模型气动外形设计方案具体为:(1-1)确定升力体母线设计方程,对升力体母线进行设计;(1-2)根据步骤(1-1)所得升力体母线设计方程确定截面控制点,依据所得截面控制点确定截面曲线;(1-3)根据步骤(1-1)所得母线和(1-2)所得截面曲线确定标准模型气动外形;在步骤(1)中,对升力体母线包括的上母线、下母线、侧缘母线,所述上母线、下母线、侧缘母线及截面曲线进行设计,曲线方程p(u)均满足方程如下:式中,vi,(i=0,1,2)为曲线的控制顶点坐标,wi,(i=0,1,2)为对应控制顶点的权因子,b2,i(u)为二次bernstein多项式,为组合数,u为控制变量参数;(2)利用数值模拟方法对步骤(1)所得标准模型气动外形进行气动特性计算及验证,并判断该标准模型气动特性是否满足标准模型设计标准,若满足设计标准,则进入步骤(3);若不满足设计标准,则返回步骤(1)对母线设计方程控制参数进行修改,其中:标准模型设计标准具体为:相同条件下,法向力与侧向力之比最大值不小于10,俯仰力矩与偏航力矩之比最大值不小于10,满足上述设计标准时,可视为基于步骤(1)提出的设计原则前提下是合格的设计产品;(3)根据标准模型气动外形进行加工及检测,加工步骤具体为:(3-1)对标准模型进行结构设计;所述标准模型包括前段、后段、隔热套、底盖、隔热垫片,所述隔热套套装于后段上,并与前段接触,所述隔热垫片安装于前段、后段连接处,所述底盖拧紧于后段尾部;(3-2)根据步骤(1)所得结构设计方案,利用指定加工技术对标准模型进行加工,并对标准模型进行基准面平行度检测,其中:指定加工技术标准包括:前段与后段成h6/g5配合,加工误差≤±0.05mm,检测工装上平面与后段夹持基准面平行度≤0.01,用于对标准模型进行加工后检测的检测工装通过标准模型气动外形进行设计;(3-3)基于三坐标检测结果对模型进行整体打光,保证轮廓误差≤±0.05mm。在加工过程中,需要使用一些辅助用加工道具进行配合加工。下面结合具体实施例进行进一步说明:本实施例采取的新型升力体标模气动外形方案为“椭球头+升力体”外形,采用参数化设计,上下和侧缘母线均为二次bezier曲线,横截面曲线为二次bezier曲线+圆弧。经优化设计的标模三维外形如图1所示,二维外形控制参数如图2所示。标模外形全长400mm、高76mm、宽130mm,椭球端头长轴8mm、中短轴5mm,侧缘半径为1.5mm。基于标模气动外形,采用数值模拟方法对其气动特性进行计算与分析。如图3所示,为标模升阻比曲线,马赫数8时,层流状态最大升阻比为3.10,湍流状态最大升阻比为2.84。如图4所示,为马赫数8时纵向焦点与航向压心对比曲线。可以看出,纵向焦点与航向压心较为接近,纵向及航向通道均具有较小的静稳定裕度。如图5、图6所示,分别给出了马赫数8时气动力和力矩系数对比。可以看出,法向力要明显大于侧向力和轴向力,俯仰力矩要明显大于偏航力矩和滚转力矩。表1给出了马赫数8时最大气动力、力矩系数比值关系,以最小气动力、力矩系数为单位1。可以看出,法向力为侧向力的13.33倍,俯仰力矩为偏航力矩的11.31倍,反映出纵向和横航向气动特性差异大的特点。表1标模气动系数比值关系(ma=8)气动系数cnczcacmcncl比值13.331.002.3311.311.001.16为开展风洞试验研究,完成了新型升力体标模结构设计,如图7所示。试验模型分为前段和后段两个部分,前、后段加工以各自的夹持作为加工和检测基准,前、后两段成h6/g5配合,各段轮廓加工误差≤±0.05mm;加工统一的检测工装,利用检测工装对标准模型进行检测,检测工装包括检测平面段及连接端,检测平面段与连接端为一体结构,且垂直设置于连接端上远离标准模型一侧,利用检测工装对标准模型基准面平行度进行检测,检测工装上平面与后段夹持基准面平行度≤0.01时标准模型加工合格,用作前、后段装配状态的检测基准;以检测工装平面及模型尾端面为基准,基于三坐标检测结果对模型进行整体打光,保证轮廓误差≤±0.05mm。如图8所示,为加工完成的新型升力体标模。使用三坐标检测仪对模型前段、后段及组合状态进行了检测。经过检测,模型组合状态检测点加工偏差≤0.05mm达标率达到98.64%,满足加工精度要求,该标模可用于后续风洞试验研究。本发明说明书中未作详细描述的内容属于本领域专业技术人员的公知技术。当前第1页1 2 3