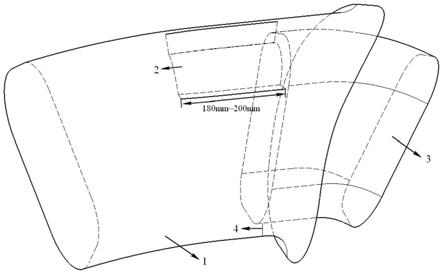
1.本发明涉及直升机空气动力学与气动设计技术领域,尤其涉及一种直升机动力舱散热系统及方法。
背景技术:2.直升机动力舱散热系统一般由发动机主喷管和排气喷管(又称混合管)构成,二者之间的间隙是动力舱引射二次流的出口,是关系动力舱散热能力强弱的关键部位。
3.由于排气喷管的结构设计类似于悬臂梁结构,随着使用年限增加,排气喷管受到重力影响会逐渐出现变形,变形后必然导致引射间隙出现变化。一旦变化超出公差范围,极易导致发动机尾气通过引射间隙回流进入动力舱,造成动力舱内温度过高,影响发动机工作状态,甚至出现火灾。
4.本发明能够在引射间隙超出公差范围后,减弱、甚至避免发动机尾气回流,有效解决动力舱超温、烧蚀等问题,提升排气喷管使用年限。
技术实现要素:5.针对上述技术问题,第一方面,本发明提供了一种直升机动力舱散热系统,包括:排气喷管、发动机主喷管和导流板,所述发动机主喷管设置在所述排气喷管内,且所述发动机主喷管与所述排气喷管之间设置有引射间隙,所述导流板设置在所述排气喷管的热气回流区;
6.其中,所述导流板用于降低直升机动力舱引射口处局部逆压,使发动机排气引射出的二次流顺利排出到动力舱外部,避免发动机高温尾气回流。
7.优选地,所述导流板铆接在所述排气管的热气回流区内,且所述导流板完全覆盖住所述热气回流区。
8.优选地,所述导流板距离所述发动机主喷管出口10-15mm。
9.优选地,所述导流板呈流线型曲面。
10.优选地,所述导流板的安装边高度为所述引射间隙的两倍,所述导流板的曲面截面的长度为所述排气喷管截面周长的12.5%~14.5%。
11.优选地,所述导流板的长度为180mm~200mm。
12.第二方面,本发明提供了一种直升机动力舱散热方法,所述方法包括:
13.基于cfd方法分析飞行状态下直升机排气引射流场特征,确定排气喷管内热气回流区的位置和大小。
14.基于所述热气回流区的位置和大小,确定导流板的几何尺寸和安装位置。
15.优选地,所述方法还包括:
16.基于所述导流板几何尺寸和安装位置再次开展cfd仿真计算,评估热气回流情况得出评估结果;
17.基于所述评估结果判断所述导流板是否满足要求;
18.若所述导流板满足要求,将所述导流板安装在所述排气管内的热气回流区;其中,所述导流板用于降低动力舱引射口处的局部逆压,使发动机排气引射出的二次流顺利排出到动力舱外部,避免发动机高温尾气回流。
19.本发明的有益技术效果:
20.本发明经cfd数值仿真分析,确定本发明能够有效增加动力舱引射量,避免回流进入动力舱出现烧蚀等问题。
附图说明
21.图1是本发明实施例提供的排气喷管、导流板和发动机主喷管的安装结构示意图;
22.图2是本发明实施例提供的排气喷管和导流板的截面图;
23.图3是本发明实施例提供的直升机动力舱散热方法的流程图;
24.其中,1-排气喷管、2-导流板、3-发动机主喷管、4-引射间隙、5-安装边、6-流线型曲面。
具体实施方式
25.请参阅图1-3,本发明涉及直升机空气动力学与气动设计领域,涉及一种被动流动控制技术,通过降低直升机排气喷管内局部逆压梯度,减小动力舱引射二次流的分离区面积,从而增强动力舱散热能力。
26.本发明的目的是:设计一种分流式排气喷管,减弱、甚至避免发动机高温尾气回流进入动力舱内部,提升直升机动力舱引射性能,增加通过引射间隙的有效空气流量数值,从而增强动力舱散热能力,减少动力舱内高温区域面积,提升排气喷管使用年限。
27.本发明的核心思路是:在常规排气喷管内增加导流板设计(图1和图2),降低动力舱引射口处局部逆压梯度,使发动机排气引射出的二次流顺利排出到动力舱外部,避免发动机高温尾气出现大面积分离,并通过引射间隙回流进入动力舱内部,出现动力舱内壁面烧蚀或发动机关键部件超温等一系列问题。
28.本发明的设计特征,主要包括以下:
29.a)排气喷管构型:由排气喷管1与“凹字形”导流板2构成,其中排气喷管1截面形状与发动机主喷管3截面形状相同,一端通过铆接方式连接在动力舱整流罩上,另一端悬空暴露的空气中;导流板2截面为“凹字形”,“凹字形”开口处与排气喷管1连接。排气喷管1和导流板2,可通过铆接或焊接方式连接,也可以使用3d打印技术一体化加工制造,见图1。
30.b)导流板构型:由与排气喷管1局部平行的流线型曲面6和两条垂直于流线型曲面6安装边5构成,导流板2截面为“凹字形”,流线型曲面6与安装边5可通过3d打印技术或钣金加工技术一体化加工制造,也可以通过铆接或焊接方式连接,见图2。
31.c)导流板几何尺寸:导流板2安装边5高度约为两倍的引射间隙4大小,流线型曲面6截面长度约为排气喷管1截面周长的12.5%~14.5%,长度约为180mm~200mm,见图1。
32.d)导流板安装位置:导流板2必须安装在混合管内引射二次流分离区处,且能够完全覆盖因引射二次流分离引起回流区,距离发动机主喷管3垂直距离约为10mm~15mm,见图1。
33.请参阅图3,本发明提供的散热方法,主要包括以下步骤:
34.步骤s1:采用cfd(计算流体动力学)方法计算分析安装常规排气喷管(无导流板)直升机各任务状态下的直升机动力舱排气引射流场特征,任务状态主要包含巡航飞行、有地效悬停、无地效悬停、正侧飞、起飞、降落等,动力舱排气引射流场特征主要包括动力舱引射二次流的方向、流速大小、分离区以及温度分布情况,计算动力舱排气引射流场时必须考虑旋翼下洗流场,以及飞行时刻的大气环境。根据动力舱排气引射流场特征,确定混合管内引射二次流分离区和热气回流区位置和大小。
35.步骤s2:根据步骤s1确定的混合管内引射二次流分离区和热气回流区位置和大小,初步设计导流板几何尺寸和安装位置方案,确保导流板能够完全覆盖直升机巡航飞行、有地效悬停、无地效悬停、正侧飞、起飞、降落等任务状态下的引射二次流分离区和热气回流区,并根据重量最小化原则,从材料、结构强度、刚度等专业方面对初步导流板方案进行迭代设计,而后确定导流板方案。
36.步骤s3:根据导流板几何尺寸和安装位置初步设计方案,建立高保真性的cfd计算网格模型。网格模型由六面体结构网格、四面体非结构网格和金字塔网格混合构成,六面体结构网格主要布置与动力舱引射间隙处,且保证不少于25层,四面体非结构网格与六面体结构网格之间通过金字塔网格过渡,过渡处网格纵横比不超过1.2,整个计算网格模型构建时必须创建粘性网格,且粘性网格层数不少于30层,增长比例不大于1.25。
37.在本技术实施例中,在计算网格模型基础上,利用cfd仿真计算方法,采用可实现的两方程k-ε湍流模型求解直升机动力舱二次流引射流场。流场求解时必须考虑流体介质的高温、高压条件下的可压缩属性,固体介质热传导和辐射属性。流场求解完成后,分析动力舱引射二次流场的气动特性,评估引射二次流分离情况、热气回流情况和动力舱内温度分布情况等,而后根据评估结果判断导流板是否满足设计要求。
38.步骤s4:如果步骤s3的分析结果不满足设计要求,重新开始步骤s1;如果满足设计要求,设计流程结束。
39.大量的直升机试飞数据表明,本发明能够有效增加动力舱引射流量,避免发动机高温尾气回流进入动力舱内出现烧蚀等问题。