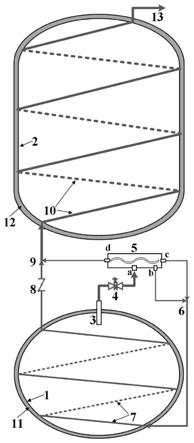
1.本发明涉及低温推进剂空间热管理技术领域,具体涉及一种基于涡流管的液氢贮箱空间排气冷量利用系统。
背景技术:2.液氢、液氧等低温推进剂是运载火箭上面级、空间航天器及未来深空探测等大型空间任务的首选燃料。然而,低温推进剂具有温度低、沸点低等特殊物性,极易在空间复杂热环境下发生气化,造成液体推进剂的损失及推进剂贮箱压力升高,给低温推进剂长期储存及低温贮箱压力控制带来了诸多挑战。
3.在低温推进剂中,液氢的温度和沸点最低,最容易发生气化,若不采取任何热管理措施,液氢贮箱日蒸发量可能超过30%/天,无法保证航天任务的顺利进行。目前,在低温推进剂贮箱外包裹发泡层+真空多层绝热层(mli)是低温推进系统主要采用的被动绝热方式,通过对绝热层材料、厚度、层数、间隔分配等关键参数的大量优化研究,液氢贮箱的在轨日蒸发量可以被控制在3%以内。近年来,研究人员提出了一种利用贮箱排气冷量的蒸气冷却屏装置,结合绝热层包裹可以进一步减少低温箱体的漏热。对于液氧贮箱,通过合理设计绝热层和蒸气冷却屏工作参数,已经能够实现蒸气冷却屏温度不高于液氧储存温度,从而有效阻止外界漏热、实现液氧在轨零蒸发贮存的目标。
4.然而,对于低温液氢贮箱,现有的绝热手段仍然无法避免液氢箱体漏热及液氢蒸发损失,需要进一步探究有效降低液氢在轨蒸发损失的热管理方案。
技术实现要素:5.为了克服上述现有技术的缺点,本发明的目的在于提供一种基于涡流管的液氢贮箱空间排气冷量利用系统,利用涡流管热质分离特性实现对液氢贮箱排气冷能分级利用,通过进一步降低液氢贮箱外壁面温度实现液氢贮箱蒸发量和压力的有效管理,从而延长低温液氢的在轨储存与服务时间。
6.为了达到上述目的,本发明采用以下技术方案:
7.一种基于涡流管的液氢贮箱空间排气冷量利用系统,包括液氢贮箱1,液氢贮箱1的氢箱排气管路3通过氢箱排气阀4与涡流管5的高压入口a连接,涡流管5的冷端液体出口b和冷端气体出口c通过氢箱三通管路6与液氢贮箱1外侧的氢箱蒸气冷却盘管7的入口连接;氢箱蒸气冷却盘管7出口通过止回阀8和氧箱三通管路9一个入口连接,氧箱三通管路9另一个入口和涡流管5的热端气体出口d连接,氧箱三通管路9出口与液氧贮箱2外侧的氧箱蒸气冷却盘管10的入口连接,氧箱蒸气冷却盘管10出口与氧箱排气管路13连接。
8.所述的氢箱排气阀4的开关通过液氢贮箱1的气枕压力反馈进行控制,当液氢贮箱1的气枕压力未达到压力控制上限时,氢箱排气阀4关闭,当液氢贮箱1的气枕压力超过压力控制上限时,氢箱排气阀4开启。
9.所述的涡流管5的长径比l/d根据下式设计:
[0010][0011]
其中:l为涡流管长度,d为涡流管通径;高压入口a侧压力p
in
根据实际工况的压力控制上限确定,冷端液体出口b、冷端气体出口c、热端气体出口d侧压力p
out
取低于液体推进剂贮存温度对应饱和压力10%-20%的值,当液氢工质与涡流管通径d一定时,涡流管长径比越大,其进出口压比越大,长径比依据涡流管进出口压比和涡流管通径d为自变量来确定,具体的依变函数f通过实验测量确定。
[0012]
所述的涡流管5的冷端流量分配比例q
cold
/q
in
按下式设计:
[0013][0014]
其中:q
cold
为冷端气体出口c处流量,q
in
为高压入口a处流量,t
cold
为液氢工质在涡流管冷端液体出口b、冷端气体出口c、热端气体出口d侧压力p
out
下对应的饱和温度,t
in
为涡流管高压入口a流体温度,涡流管热端气体出口d的流量和温度分别通过涡流管进出口质量守恒与能量守恒求解得到。
[0015]
所述的氢箱蒸气冷却盘管7、氧箱蒸气冷却盘管10外部分别包裹氢箱绝热层11、氧箱绝热层12,绝热层采用发泡材料或真空多层绝热材料。
[0016]
本发明的有益效果为:
[0017]
本发明通过蒸气冷却盘管结构使液氢贮箱排气依次与液氢贮箱壁面和液氧贮箱壁面进行换热,利用液氢贮箱排气的冷量进一步降低液氢和液氧贮箱外壁面温度,通过减小低温箱体漏热对低温推进剂蒸发量进行有效控制。
[0018]
本发明利用涡流管的热质分离特性,将压力较高的液氢贮箱排气分流为一股低温低压流体和一股高温低压流体,对液氢贮箱排气的冷量进行了分级利用,相较于传统蒸气冷却屏等排气冷量利用装置,能够以更低温的流体对液氢贮箱壁面进行更强效的冷却降温,通过进一步降低液氢贮箱外壁面温度来降低液氢贮箱漏热量,从而进一步减小液氢的蒸发损失,延长液氢的在轨储存时间。
[0019]
本发明提出了涡流管长径比和冷端流量比的设计,给涡流管冷端出口压力、温度和流量以及氢箱冷却盘管换热效果的优化设计提供计算依据。
附图说明
[0020]
图1是本发明实施例的结构示意图。
具体实施方式
[0021]
下面结合附图和实施例来进一步说明本发明的技术方案。
[0022]
参照图1,一种基于涡流管的液氢贮箱空间排气冷量利用系统,包括液氢贮箱1,液氢贮箱1的氢箱排气管路3通过氢箱排气阀4与涡流管5的高压入口a连接,涡流管5的冷端液体出口b和冷端气体出口c通过氢箱三通管路6与液氢贮箱1外侧的氢箱蒸气冷却盘管7的入口连接;氢箱蒸气冷却盘管7出口通过止回阀8和氧箱三通管路9一个入口连接,氧箱三通管路9另一个入口和涡流管5的热端气体出口d连接,氧箱三通管路9出口与液氧贮箱2外侧的
氧箱蒸气冷却盘管10的入口连接,氧箱蒸气冷却盘管10出口与氧箱排气管路13连接。
[0023]
所述的氢箱排气阀4的开关通过液氢贮箱1的气枕压力反馈进行控制,当液氢贮箱1的气枕压力未达到压力控制上限时,氢箱排气阀4关闭,当液氢贮箱1的气枕压力超过压力控制上限时,氢箱排气阀4开启。
[0024]
所述的涡流管5的长径比l/d根据下式设计:
[0025][0026]
其中:l为涡流管长度,d为涡流管通径。高压入口a侧压力p
in
根据实际工况的压力控制上限确定,冷端液体出口b、冷端气体出口c、热端气体出口d侧压力p
out
取低于液体推进剂贮存温度对应饱和压力10%-20%的值,当液氢工质与涡流管通径d一定时,涡流管长径比越大,其进出口压比越大,长径比依据涡流管进出口压比和涡流管通径d为自变量来确定,具体的依变函数f通过实验测量确定。
[0027]
所述的涡流管5的冷端流量分配比例q
cold
/q
in
按下式设计:
[0028][0029]
其中:q
cold
为冷端气体出口c处流量,q
in
为高压入口a处流量,t
cold
为液氢工质在涡流管冷端液体出口b、冷端气体出口c、热端气体出口d侧压力p
out
下对应的饱和温度,t
in
为涡流管高压入口a流体温度,涡流管热端气体出口d的流量和温度分别通过涡流管进出口质量守恒与能量守恒求解得到。
[0030]
由于液氢工质在氢箱蒸气冷却盘管7内流动产生的沿程阻力损失和局部阻力损失,氢箱蒸气冷却盘管7出口处压力将低于涡流管5热端气体出口d压力,因此,氢箱蒸气冷却盘管7出口液氢工质与涡流管5的热端气体出口d出口液氢工质混合后,氧箱三通管路9处压力将高于氢箱蒸气冷却盘管7出口压力,为防止流体向氢箱蒸气冷却盘管7内倒流,需安装止回阀8。
[0031]
所述的氢箱蒸气冷却盘管7、氧箱蒸气冷却盘管10外部分别包裹氢箱绝热层11、氧箱绝热层12,绝热层采用发泡材料、真空多层绝热材料等。
[0032]
本发明的工作原理是:
[0033]
在持续漏热作用下,液氢贮箱1内液氢工质逐渐升温并发生气化,从而引起液氢贮箱1内气枕压力逐渐升高,当液氢贮箱1的气枕压力达到压力控制上限时,氢箱排气阀4开启,液氢贮箱1内高压气体通过氢箱排气管路3排出,经过高压入口a进入涡流管5。
[0034]
涡流管5能够回收高压气体的压力能并实现热质分离,实现排气冷能的梯级利用:一方面,涡流管5冷端分离出的温度低于液氢饱和温度的低温液体和气体,分别通过冷端液体出口b和冷端气体出口c排出,流经氢箱三通管路6形成一股气液混合流体后进入氢箱蒸气冷却盘管7;低温的气液两相流通过沸腾换热与对流换热对在液氢贮箱1外壁面进行冷却降温,有效降低液氢贮箱1的漏热影响;另一方面,涡流管5热端气体出口d分离出的温度低于液氧饱和温度的气体,与经过氢箱蒸气冷却盘管7换热升温后的流体,通过氧箱三通管路9混合形成一股温度介于液氢饱和温度和液氧饱和温度之间的气体,进入氧箱蒸气冷却盘管10对液氧贮箱2的外壁面进行冷却降温,有效降低液氧贮箱2的漏热影响。
[0035]
经过氧箱蒸气冷却盘管10进一步换热升温后的气体通过排气管路13排放;液氢贮箱1、液氧贮箱2的外壁面温度分别在氢箱蒸气冷却盘管7、氧箱蒸气冷却盘管10的换热作用下逐渐降低,使得外界环境漏热通过氢箱绝热层11、氧箱绝热层12分别向液氢贮箱1、液氧贮箱2的热传输过程不再平衡,进而导致液氢贮箱1的蒸发排气流量产生变化,从而进一步影响氢箱蒸气冷却盘管7和氧箱蒸气冷却盘管10的冷却降温作用。经过长时间的运行后,整个漏热传输过程将逐渐趋于新的动态稳定,液氢贮箱1的蒸发排气流量、氢箱蒸气冷却盘管7和氧箱蒸气冷却盘管10的冷却降温作用、液氢贮箱1和液氧贮箱2的外壁面温度、以及氢箱绝热层11和氧箱绝热层12内的温度分布都将趋于稳定;最终,液氢贮箱1将稳定在更低的蒸发量水平,实现更有效的长期储存。