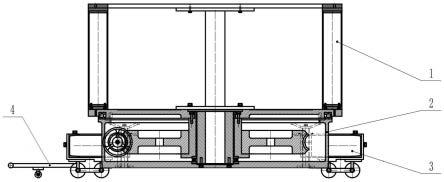
1.本发明涉及卫星生产装配技术领域,特别是一种用于卫星装配、移动、测试和停放的一体化装置。
背景技术:2.以前卫星是按颗研制生产的,随着科技发展,现在改为批量研制生产,这样就需要建立一条流水线来满足批量研制生产的需求。在这条流水线上必须配置一批高精度装配测试移动装置。卫星由许多零件、部件、结构件和连接线等组成,且安装精度要求非常高,在卫星装配完毕后需要对其进行振动、热真空、质量特性、剩磁测试等等试验,所以需要研制一台定位精度高、移动方便的装置,高精度装配测试移动装置就可以实现这个要求。
3.为了能精确安装卫星、快速转移卫星到各个试验工位,完成卫星的各项测试,必须研制一台卫星高精度装配、转移和停放的综合性装置。
技术实现要素:4.本发明的目的是为了解决上述问题,设计了一种用于卫星装配、移动、测试和停放的一体化装置。
5.实现上述目的本发明的技术方案为,一种用于卫星装配、移动、测试和停放的一体化装置,包括方形移动框架,所述方形移动框架上固定安装牵引器,所述方形移动框架上安装旋转转盘,所述旋转转盘的上表面能够转动,所述旋转转盘的上表面安装卫星停放架。
6.所述旋转转盘包括底座,所述底座安装在方形移动框架上,所述底座上设有主轴,所述主轴的下端位于底座内并与底座的底面固定连接,所述主轴上端向上伸到底座的上方,所述主轴上套有轴承外套和转盘台面,所述转盘台面位于轴承外套的上方并通过螺丝与轴承外套的上端固定连接,所述轴承外套的下端通过推力球轴承与底座的底面连接,所述轴承外套上套有蜗轮,所述蜗轮与轴承外套固定连接,所述底座内安装有蜗杆,所述蜗杆与蜗轮啮合,所述蜗杆能够驱动蜗轮、轴承外套和转盘台面围绕主轴同步转动。
7.所述转盘台面的上表面为旋转转盘的上表面,所述转动台面的上表面的中心区域配备台面盖,所述转盘台面的下表面固定安装上推力环,所述上推力环围绕着转盘台面下表面的中心布置,所述底座的上表面固定安装下推力环,所述下推力环的尺寸与上推力环的尺寸相匹配,所述上推力环和下推力环之间布置若干滚珠。
8.所述蜗杆的两端分别穿插在底座的侧壁上,所述蜗杆的两端均通过圆锥滚子轴承与底座的侧壁活动连接,所述蜗杆的一端伸到底座的外侧,所述蜗杆的一端上固定安装手轮,所述蜗杆的一端配备前端盖,所述蜗杆的另一端配备后端盖。
9.所述卫星停放架包括卫星连接板,所述卫星连接板与旋转转盘的上表面平行,所述卫星连接板的和旋转转盘的上表面之间设有若干立柱,若干立柱的长度方向相互平行,所述立柱的上端通过上连接板与卫星连接板的下表面固定连接,所述立柱的下端通过下连接板与旋转转盘的上表面固定连接。
10.所述卫星连接板为圆环形结构,所述立柱是横截面为矩形的柱状结构,所述上连接板和下连接板均为矩形板。
11.所述方形移动框架包括矩形的框架,所述框架的下表面固定安装若干三吨美式滑动轮,所述框架的四角处固定安装三角板,所述框架的内表面上固定安装若干长加强管和若干短加强管,若干长加强管和若干短加强管均位于同一平面内。
12.所述框架内孔的尺寸要大于底座的尺寸,所述底座的下部能够装入框架的内孔,所述框架上的三角板、长加强管和短加强管均用于承载底座。
13.所述三角板上固定安装加强套。
14.所述长加强管和短加强管均是在管件两端固定安装连接板后形成的“工”字形结构。
15.有益效果
16.利用本发明的技术方案制作的一种用于卫星装配、移动、测试和停放的一体化装置,其具有如下优势:
17.1、本装置安全可靠,提高了工作效率近2-3倍,确保卫星的安全,整个装置的通用性非常强,可以用于各种型号卫星的装配、试验、测试,由于其结构简单,安装调试和操作方便,通过增加过渡连接装置就可以适用于不同型号的卫星,可以实现功能的扩展,根据卫星的重量和大小形成一个系列化的高精度装配、转移和停放的装置;
18.2、本装置采用铝合金和不锈钢型材的结构、旋转部分采用腰形滚柱定位轴结构形式、自制平面推力轴承装置和精密蜗轮蜗杆系统装置,能大大提高装置的安装精度和安装使用的效果;
19.3、目前要国内生产的“一套卫星停放架、转移小车、高精度转台”需要129.8万人民币,而本装置只需要88.5万人民币,有效的降低了生产成本;同时,本装置只需要一次吊装就能够满足卫星停放架、转移、转动的使用需求,简化了操作过程,提高了卫星的安全。
附图说明
20.图1是本发明所述一种用于卫星装配、移动、测试和停放的一体化装置的结构示意图;
21.图2是本发明所述卫星停放架的主视图;
22.图3是本发明所述卫星停放架的俯视图;
23.图4是本发明所述方形移动框架的主视图;
24.图5是本发明所述方形移动框架的俯视图;
25.图6是本发明所述旋转转盘的主视图;
26.图7是本发明所述旋转转盘的俯视图;
27.图中,1、卫星停放架;2、旋转转盘;3、方形移动框架;4、牵引器;5、卫星连接板;6、上连接板;7、立柱;8、下连接板;9、底座;10、主轴;11、轴承外套;12、转盘台面;13、推力球轴承;14、涡轮;15、蜗杆;16、上推力环;17、下推力环;18、滚珠;19、圆锥滚子轴承;20、手轮;21、前端板;22、后端板;23、框架;24、三吨美式滑动轮;25、三角板;26、长加强管;27、短加强管;28、加强套;29、连接板;30、台面盖。
具体实施方式
28.下面结合附图对本发明进行具体描述,如图1-7所示;
29.本技术的创造点在于,在方形移动框架上安装旋转转盘2,所述旋转转盘的上表面能够转动,所述旋转转盘的上表面安装卫星停放架1,所述旋转转盘包括底座9,所述底座安装在方形移动框架上,所述底座上设有主轴10,所述主轴的下端位于底座内并与底座的底面固定连接,所述主轴上端向上伸到底座的上方,所述主轴上套有轴承外套11和转盘台面12,所述转盘台面位于轴承外套的上方并通过螺丝与轴承外套的上端固定连接,所述轴承外套的下端通过推力球轴承13与底座的底面连接,所述轴承外套上套有蜗轮14,所述蜗轮与轴承外套固定连接,所述底座内安装有蜗杆15,所述蜗杆与蜗轮啮合,所述蜗杆能够驱动蜗轮、轴承外套和转盘台面围绕主轴同步转动,所述转盘台面的上表面为旋转转盘的上表面,所述转动台面的上表面的中心区域配备台面盖30,所述转盘台面的下表面固定安装上推力环16,所述上推力环围绕着转盘台面下表面的中心布置,所述底座的上表面固定安装下推力环17,所述下推力环的尺寸与上推力环的尺寸相匹配,所述上推力环和下推力环之间布置若干滚珠18,所述蜗杆的两端分别穿插在底座的侧壁上,所述蜗杆的两端均通过圆锥滚子轴承19与底座的侧壁活动连接,所述蜗杆的一端伸到底座的外侧,所述蜗杆的一端上固定安装手轮20,所述蜗杆的一端配备前端盖21,所述蜗杆的另一端配备后端盖22。
30.本技术的创造点还在于,卫星停放架包括卫星连接板5,所述卫星连接板与旋转转盘的上表面平行,所述卫星连接板的和旋转转盘的上表面之间设有若干立柱7,若干立柱的长度方向相互平行,所述立柱的上端通过上连接板6与卫星连接板的下表面固定连接,所述立柱的下端通过下连接板8与旋转转盘的上表面固定连接,所述卫星连接板为圆环形结构,所述立柱是横截面为矩形的柱状结构,所述上连接板和下连接板均为矩形板。
31.本技术的创造点还在于,方形移动框架包括矩形的框架23,所述框架的下表面固定安装若干三吨美式滑动轮24,所述框架的四角处固定安装三角板25,所述框架的内表面上固定安装若干长加强管26和若干短加强管27,若干长加强管和若干短加强管均位于同一平面内。
32.本技术技术方案在实施过程中,卫星连接板的材料主要特性在铝材料中加入少量cd、ti、v、b、zr等微量元素的铝-铜合金,通过添少量cd以加速合金的人工时效,,加少量ti以细化晶粒,并降低合金中有害杂质的含量,加少量v、b、zr等微量能进一步提高合金的热强性,显著提高合金的力学性能,选择合适的热处理工艺而获得σb达437/m
㎡
的高强度耐热铸铝合金。主轴和轴承外套上涂有二硫化钼,二硫化钼具有较好的抗水、较好的机械安定性和耐压性,实现较重负荷的机械的润滑作用。
33.卫星连接板是整体铸制而成的铝合金(zl104)零件,卫星连接板的铸造工艺流程为:1、去毛刺是用倒角工具倒去零件表面的尖角,防止在氧化过程中尖端放电,2、超声波清洗是用超声波清洗机清洗零件,把零件表面及螺孔的多余物和杂质去掉;3、碱性除油清洗是在碱水槽中清洗,槽液(naoh)的温度是在50-58℃,槽液在滚动的情况下对零件表面进行清洗;4、漂洗是把清洗好的零件在蒸馏水槽中,槽液呈滚动状态下进行清洗;5、冷硬氧化处理是在浓度为28-32%的硫酸溶液槽中进行处理,槽液(h2so4)温度为1-2℃情况下,氧化时间为2.5-2.6小时,并在零件表面加入直流电源,电压为36-40v,电流按2.5a/dm2来通电,在零件表面生成一层非常硬的氧化膜(al2o3)氧化膜的厚度为0.03mm,氧化膜表面的硬度
(hrc)为50;6、再漂洗是是把冷硬氧化处理好的零件在蒸馏水槽中,槽液呈滚动状态下进行清洗;7、验收人员对产品按图纸要求进行逐项检查;8、把加工完成的零件放入库房,等待装配。
34.上连接板、立柱、下连接板是采用铝合金材料制成的,将上连接板和下连接板分别焊接在立柱的二端,进行回火处理后进行机加工保证4个组件尺寸一致,相对尺寸误差在0.02mm。用16组轻型弹簧垫圈(6)平垫圈-c级(6)和内六角圆柱头螺钉(m6x25)将立柱组件安装在转盘台面,用16组平垫圈-c级(8)、标准型弹簧垫圈(8)和六角头铰制孔用螺栓-b级(m8x35)与卫星连接板连接。
35.转盘台面也是整体铸制而成的铝合金(zl104)零件,加工工艺流程与卫星连接板所示一致、上推力环和下推力环采用是高碳铬轴承钢(gcr15),高碳铬轴承钢含碳(c)量为1%左右;含铬(cr)量为1.5%左右,我们对高碳轴承钢的质量要求很高,必须严格控制硫、磷、氢等含量、非金属夹杂物、碳化物的数量、大小和分布状况,因为非金属夹杂物和碳化物的数量、大小和分布状况对高碳铬轴承钢的使用寿命影响很大,会使高碳铬轴承钢的失效,在大的夹杂或碳化物周围产生的微裂纹而影响精度,而且要检查钢材在低倍组织必须无缩孔、皮下气泡、白点及显微孔隙、中心疏松、一般疏松不得超过1.5级,偏析不得超过2级,钢材的退火组织应为均匀分布的细粒状珠光体。上推力环和下推力环毛坯料是圆环型坯料。
36.底座是整体铸制而成的铝合金(zl104)零件,加工工艺流程与卫星连接板一致,蜗轮是h62y2材料制造的,h62y2是代表半硬状态的黄铜。黄铜是由铜和锌所组成的合金。由铜、锌组成的黄铜就叫作普通黄铜。用半硬状态的黄铜黄制造的涡轮其耐磨性大大提高了,用前端盖、2个圆锥滚子轴承(30000型30210)和后端盖将蜗杆安装在底座上调整蜗杆和涡轮之间的间隙及咬合率,因为前端盖与底座的配合间隙为0.5mm保证可以上下左右进行调整蜗杆和涡轮之间的间隙,调整完毕后在前端盖与底座打二个的定位销。推力球轴承(51000型51138)24是安装在底座上,主轴用6个m10x50的内六角螺钉、6个的小垫圈和6个的轻型弹簧垫圈安装在底座上,轴承外套的内孔尺寸与主轴的外圆尺寸的差值为:9.97mm,实现高精度腰形滚柱结构组成的的轴承目的,滚腰形珠30的直经是腰形滚珠的长8mm,108个腰形滚珠的的误差在0.001mm,高精度密滚珠轴承加工装配的步序:
37.一、加工轴承外套的内孔精确测量内孔的尺寸;
38.二、按轴承外套的内孔尺寸减去9.97mm,再加工主轴外圆的尺寸误差在0.01mm;
39.三、将主轴用6个m10x45的内六角螺钉、6个的小垫圈和6个的轻型弹簧垫圈安装在底座上;
40.四、把推力球轴承(51000型51138)安装在底座上;
41.五、把滚珠隔离套和108个腰形滚柱从下到上一圈一圈安装在主轴的外圆上;
42.六、把轴承外套安装到滚珠隔离套和108个腰形滚柱上保证过盈量为:0.015mm;
43.七、用二个平键把涡轮安装到轴承外套上;
44.八、把下推力环安装在底座上;
45.九、把168个滚珠安装在下推力环上;
46.十、将已经安装好上推力环的转盘台面装配到轴承外套上,用4个m10x40内六螺钉、4个的小垫圈和4个的轻型弹簧垫圈固定,确保系统无轴向窜动,360
°
旋转灵活。
47.十一、用4个m4x10的沉头螺钉把台面盖安装到转盘台面上,
48.高精度密滚珠轴承加工装配完成。
49.最后进行蜗杆安装在底座上,调整蜗杆和涡轮之间的间隙及咬合率。
50.三吨美式滑动轮的特点:承载大每一个滑动轮能承载3吨。移动平稳,框架,三角板,长加强管,短加强管,连接板,加强套全部采用铝型材和铝材用氩弧焊接而成,焊接后进行低温回火处理去除焊接应力,然后加工内测面的连接面,最后整体进行冷硬氧化处理。冷硬氧化处理是在浓度为28-32%的硫酸溶液槽中进行处理,槽液(h2so4)温度为1-2℃情况下,氧化时间为2.5-2.6小时,并在零件表面加入直流电源,电压为36-40v,电流按2.5a/dm2来通电,在零件表面生成一层非常硬的氧化膜(al2o3)氧化膜的厚度为0.03mm,氧化膜表面的硬度(hrc)达到hrc:50。
51.本发明的技术方案克服了原来卫星装配、试验操作时间长,安全可靠性差等问题,也节省了卫星工装的研制经费41.3万。同时操作方便、安全可靠,提高了工作效率近2-3倍,确保卫星的安全,得到了科研人员的一致好评实际效果非常好。已应用于卫星装配、试验、测试中,得到了各级科研人员的一致好评,实际效果非常好。本发明的通用性非常强,可以用于各种型号卫星的装配、试验、测试。
52.需要说明的是,在本文中,诸如第一和第二等之类的关系术语仅仅用来将一个实体或者操作与另一个实体或操作区分开来,而不一定要求或者暗示这些实体或操作之间存在任何这种实际的关系或者顺序。而且,术语“包括”、“包含”或者其任何其他变体意在涵盖非排他性的包含,从而使得包括一系列要素的过程、方法、物品或者设备不仅包括那些要素,而且还包括没有明确列出的其他要素,或者是还包括为这种过程、方法、物品或者设备所固有的要素。在没有更多限制的情况下。由语句“包括一个......限定的要素,并不排除在包括所述要素的过程、方法、物品或者设备中还存在另外的相同要素”。
53.上述技术方案仅体现了本发明技术方案的优选技术方案,本技术领域的技术人员对其中某些部分所可能做出的一些变动均体现了本发明的原理,属于本发明的保护范围之内。