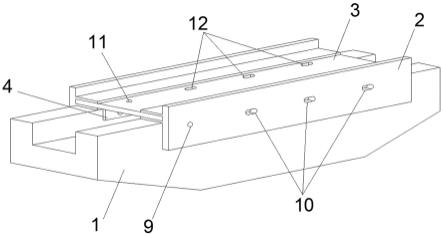
1.本公开一般涉及飞行器发动机技术领域,具体涉及一种外挂冲压发动机连接装置。
背景技术:2.随着各国对高超音速飞行器的重视,越来越多的飞行器及冲压发动机需要进行高空高速飞行验证。因此,冲压发动机安装在飞行器上,一起作为任务载荷捆绑在火箭上,让火箭将载荷推送至指定的速度和高度后再进行器箭分离,进入指定的发动机工作试验窗口。
3.现有的发动机安装在机舱内部,导致发动机占用火箭载荷空间,同时固支机构复杂影响火箭装配。
4.发动机以及火箭在高空中高速飞行时,空气摩擦会使连接装置处产生高温;同时由于具有较高的加速度,连接装置也会承受很高的压力。在恶劣的高温高压环境下,发动机的连接装置由于热胀冷缩,原本的固定安装位置会发生改变,进而产生结构应力。若结构应力长时间得不到释放,一旦结构应力与加速度产生的力相互叠加,则可能会使连接装置处受到的力超出连接装置本身的承力范围。轻则导致连接装置变形影响火箭飞行轨道,严重的则可能导致火箭解体,产生巨大的损失。
技术实现要素:5.鉴于现有技术中的上述缺陷或不足,期望提供一种外挂冲压发动机连接装置。
6.本技术提供一种外挂冲压发动机连接装置,包括:安装槽,所述安装槽设置在发动机的一侧;所述安装槽的侧壁上沿第一方向依次排列设置有:一个固定通孔和多个支撑通孔;转接板,所述转接板具有与所述安装槽侧壁外表面抵接的抵接面和凸出所述安装槽侧壁的凸出面;所述抵接面上沿第一方向依次排列设有一个第一连接孔和多个第一腰型孔;所述凸出面上靠近所述安装槽的一侧设有平行于第一方向的滑槽;机舱底板,所述机舱底板具有平行于第一方向的边缘部,所述边缘部插入所述滑槽;所述机舱底板上设有多个安装孔阵列;所述安装孔阵列包括:沿第一方向依次排列设置有一个第二连接孔和多个第二腰型孔;第一连接件,所述第一连接件设有一个且与所述机舱底板靠近所述安装槽的一侧抵接;所述第一连接件靠近所述转接板的一端设有第三连接孔,靠近所述机舱底板的一侧设有多个第四连接孔;第二连接件,所述第二连接件设有多个且均与所述机舱底板靠近所述安装槽的一侧抵接;所述第二连接件靠近所述转接板的一端设有第五连接孔,靠近所述机舱底板的一侧设有多个第六连接孔;所述第一连接件和多个所述第二连接件沿第一方向依次排列设置;
所述第一连接件与多个所述第二连接件沿第一方向依次设置在所述安装槽内;其中,所述第一连接孔、所述固定通孔和所述第三连接孔之间,所述第一腰型孔、所述支撑通孔和所述第五连接孔之间,所述第四连接孔和所述第二连接孔之间,所述第六连接孔和所述第二腰型孔之间均通过紧固螺栓固定连接。
7.根据本技术实施例提供的技术方案,所述安装槽的两侧壁上分别设有一个固定通孔和多个支撑通孔;所述转接板设有两个且两抵接面分别与所述安装槽两个侧壁的外表面抵接;所述第一连接件的两端均设有所述第三连接孔;两所述第三连接孔均通过所述紧固螺栓与所述安装槽两侧壁上的所述固定通孔固定连接;所述第二连接件的两端均设有所述第五连接孔;两所述第五连接孔均通过所述紧固螺栓与所述安装槽两侧壁上的所述支撑通孔固定连接。
8.根据本技术实施例提供的技术方案,所述机舱底板的边缘部沿第一方向排列设置有多个凸起块,所述凸起块均插入所述滑槽,所述凸起块之间形成形变空间。
9.根据本技术实施例提供的技术方案,所述机舱底板的边缘部沿第一方向开设有密封槽,所述密封槽内设有密封条。
10.根据本技术实施例提供的技术方案,所述密封槽内涂设有润滑脂。
11.根据本技术实施例提供的技术方案,所述边缘部的表面涂设有自润滑涂层。
12.根据本技术实施例提供的技术方案,所述机舱底板的一端设有限位凸起,所述限位凸起与所述滑槽的侧壁抵接。
13.本技术的有益效果在于:由于在发动机上设置安装槽,所述安装槽上设有固定通孔和支撑通孔;转接板与所述安装槽的外侧壁抵接,所述转接板上设有第一连接孔和多个第一腰型孔且靠近所述安装槽的一侧设有滑槽;所述机舱底板插入所述滑槽;所述机舱底板上设有一个第二连接孔和多个第二腰型孔;所述第一连接件和所述第二连接件用于连接所述转接板、发动机和所述机舱底板。通过在所述转接板上设置腰型孔,利用紧固螺栓依次穿过所述第一腰型孔、支撑通孔和第三连接孔固定连接所述转接板、发动机和所述机舱底板;当发动机以及火箭在高空高速飞行产生高温和高压导致火箭和发动机之间的连接装置产生形变和结构应力时,所述紧固螺栓在腰型孔内产生相对滑动来消除结构应力,保证连接装置的稳定。
附图说明
14.通过阅读参照以下附图所作的对非限制性实施例所作的详细描述,本技术的其它特征、目的和优点将会变得更明显:图1为本技术提供的一种外挂冲压发动机连接装置的结构示意图;图2为本技术提供的一种外挂冲压发动机连接装置的又一结构示意图;图3为机舱底板的结构示意图;图4为限位凸起的结构示意图;图5为第一连接件的结构示意图;图6位第二连接件的结构示意图;其中:1、发动机;2、转接板;3、机舱底板;4、第一连接件;5、第二连接件;6、滑槽;7、
固定通孔;8、支撑通孔;9、第一连接孔;10、第一腰型孔;11、第二连接孔;12、第二腰型孔;13、第三连接孔;14、第四连接孔;15、第五连接孔;16、第六连接孔;17、密封槽;18、限位凸起。
具体实施方式
15.下面结合附图和实施例对本技术作进一步的详细说明。可以理解的是,此处所描述的具体实施例仅仅用于解释相关发明,而非对该发明的限定。另外还需要说明的是,为了便于描述,附图中仅示出了与发明相关的部分。
16.需要说明的是,在不冲突的情况下,本技术中的实施例及实施例中的特征可以相互组合。下面将参考附图并结合实施例来详细说明本技术。
17.请参考图1、图2、图5和图6,为本实施例提供的一种外挂冲压发动机连接装置示意图,包括:安装槽,所述安装槽设置在发动机1的一侧;所述安装槽的侧壁上沿第一方向依次排列设置有:一个固定通孔7和多个支撑通孔8;转接板2,所述转接板2具有与所述安装槽侧壁外表面抵接的抵接面和凸出所述安装槽侧壁的凸出面;所述抵接面上沿第一方向依次排列设有一个第一连接孔9和多个第一腰型孔10;所述凸出面上靠近所述安装槽的一侧设有平行于第一方向的滑槽6;机舱底板3,所述机舱底板3具有平行于第一方向的边缘部,所述边缘部插入所述滑槽6;所述机舱底板3上设有多个安装孔阵列;所述安装孔阵列包括:沿第一方向依次排列设置有一个第二连接孔11和多个第二腰型孔12;第一连接件4,所述第一连接件4设有一个且与所述机舱底板3靠近所述安装槽的一侧抵接;所述第一连接件4靠近所述转接板2的一端设有第三连接孔13,靠近所述机舱底板3的一侧设有多个第四连接孔14;第二连接件5,所述第二连接件5设有多个且均与所述机舱底板3靠近所述安装槽的一侧抵接;所述第二连接件5靠近所述转接板2的一端设有第五连接孔15,靠近所述机舱底板3的一侧设有多个第六连接孔16;所述第一连接件4和多个所述第二连接件5沿第一方向依次排列设置;所述第一连接件4与多个所述第二连接件5沿第一方向依次设置在所述安装槽内;其中,所述第一连接孔9、所述固定通孔7和所述第三连接孔13之间,所述第一腰型孔10、所述支撑通孔8和所述第五连接孔15之间,所述第四连接孔14和所述第二连接孔11之间,所述第六连接孔16和所述第二腰型孔12之间均通过紧固螺栓固定连接。
18.具体地,本技术提供的一种外挂冲压发动机连接装置设置在火箭外部,不占用火箭内部的荷载空间,能够提高火箭的荷载空间。
19.具体地,通过在所述第一连接孔9、所述固定通孔7和所述第三连接孔13之间安装紧固螺栓来固定所述发动机1、转接板2和第一连接件4之间的相对位置。
20.通过在所述第四连接孔14和所述第二连接孔11之间安装紧固螺栓来固定所述机舱底板3和所述第一连接件4之间的相对位置。
21.通过在所述第一腰型孔10、所述支撑通孔8和所述第五连接孔15之间安装紧固螺栓来固定发动机1、转接板2和所述第二连接件5之间的相对位置。
22.通过在所述第六连接孔16和所述第二腰型孔12之间安装紧固螺栓来固定所述机舱底板3和所述第二连接件5之间的相对位置。
23.工作原理:当产生热胀冷缩导致机舱底板3、转接板2、或第二连接件5产生变形时,与所述第一连接件4连接处的所述机舱底板3和转接板2的位置相对固定。与所述第二连接件5连接处的所述机舱底板3和转接板2之间产生轻微相对滑动,分别带动与所述第一腰型孔10连接的紧固螺栓在所述第一腰型孔10内产生相对滑动。与所述第二腰型孔12连接的紧固螺栓在所述第二腰型孔12内产生相对滑动;进而使产生的结构应力得到释放,保证连接装置的稳定。
24.在一些实施方式中,采用后固前支的连接方式:一端通过常规的连接孔固定连接,另一端通过腰型孔固定连接;一端通过腰型孔固定的连接方式,能够保证发动机与火箭之间连接稳定的同时有效消除结构应力。
25.进一步地,所述安装槽的两侧壁上分别设有一个固定通孔7和多个支撑通孔8;所述转接板2设有两个且两抵接面分别与所述安装槽两个侧壁的外表面抵接;所述第一连接件4的两端均设有所述第三连接孔13;两所述第三连接孔13均通过所述紧固螺栓与所述安装槽两侧壁上的所述固定通孔7固定连接;所述第二连接件5的两端均设有所述第五连接孔15;两所述第五连接孔15均通过所述紧固螺栓与所述安装槽两侧壁上的所述支撑通孔8固定连接。
26.在一些实施方式中,所述转接板2设有两个,两侧的所述转接板2使用相同的方式与所述发动机1连接,能够进一步提高连接装置的结构稳定性。
27.进一步地,参考图3,所述机舱底板3的边缘部沿第一方向排列设置有多个凸起块,所述凸起块均插入所述滑槽6,所述凸起块之间形成形变空间。
28.在一些实施方式中,在高速飞行产生高温与高压时,所述机舱底板3会在高温与高压的环境下产生形变,边缘部由于插入滑槽6中,产生的形变会与滑槽6的内侧壁相互挤压。设置多个凸起块形成形变空间,能够针对所述机舱底板3边缘部插入滑槽6的部分有效地消除产生的结构应力。
29.进一步地,所述机舱底板3的边缘部沿第一方向开设有密封槽17,所述密封槽17内设有密封条。
30.在一些实施方式中,所述边缘部设有密封槽17,所述密封槽17内设有密封条;密封槽17与所述密封条的两端涂有密封胶。能够使机舱底板3与滑槽6之间的空气相互隔绝,防止外界空气进入机舱产生危险。
31.进一步地,所述密封槽17内涂设有润滑脂。
32.在一些实施方式中,所述密封槽17内涂设有润滑脂,能够防止在安装密封条时密封槽17划伤密封条;进一步保证密封槽17的气密性。
33.进一步地,所述边缘部的表面涂设有自润滑涂层。
34.在一些实施方式中,所述边缘部的表面涂设有自润滑涂层,能够在所述机舱底板3插入所述滑槽6时减小摩擦,方便安装。
35.进一步地,参考图4,所述机舱底板3的一端设有限位凸起18,所述限位凸起18与所述滑槽6的侧壁抵接。
36.在一些实施方式中,所述机舱底板3的一端设有限位凸起18,能够起到对机舱底板
3的限位作用,使所述机舱底板3完全插入滑槽6时的相对位置固定,方便第四连接孔14与第二连接孔11之间的对齐、第六连接孔16与第二腰型孔12之间的对齐,进而方便紧固螺栓的安装固定。
37.安装过程:一、将所述第一连接件4和多个所述第二连接件5沿第一方向依次放入所述安装槽使所述第三连接孔13和固定通孔7对应、第五连接孔15和支撑通孔8对应。
38.二、将两所述转接板2设置在所述安装槽的两侧并抵接,使两所述滑槽6位于两所述转接板2相互靠近的一侧;同时使所述第一连接孔9与固定通孔7对应,第一腰型孔10与支撑通孔8对应。
39.三、在所述机舱底板3的边缘部涂设自润滑涂层;在密封槽17内涂设润滑脂。
40.四、将密封条放入所述密封槽17,并在密封条与所述密封槽17的两端涂设密封胶。
41.五、将所述机舱底板3插入所述滑槽6,使所述限位凸起18与所述滑槽6的侧壁抵接。
42.六、利用紧固螺栓固定连接所述第一连接孔9、所述固定通孔7和所述第三连接孔13;固定连接所述第一腰型孔10、所述支撑通孔8和所述第五连接孔15;固定连接所述第四连接孔14和所述第二连接孔11;固定连接所述第六连接孔16和所述第二腰型孔12。
43.以上描述仅为本技术的较佳实施例以及对所运用技术原理的说明。本领域技术人员应当理解,本技术中所涉及的发明范围,并不限于上述技术特征的特定组合而成的技术方案,同时也应涵盖在不脱离所述发明构思的情况下,由上述技术特征或其等同特征进行任意组合而形成的其它技术方案。例如上述特征与本技术中公开的(但不限于)具有类似功能的技术特征进行互相替换而形成的技术方案。