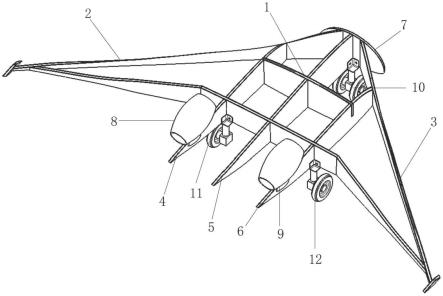
1.本实用新型涉及非载人器技术领域,具体地,涉及一种复合材料非载人器骨架。
背景技术:2.由于非载人器在结构设计上不需要考虑人的生理续航能力的限制,所以在设计时可以更加注重无人机的机动性,这使得它在选材上有了一些不同于载人飞机的新特点。此外,非载人器还经常用于执行空中侦察、监视、通信、反潜、电子干扰等特殊任务。传统金属材料在非载人器骨架的应用上有一定的局限性,如抗疲劳和抗振动的特性不足,同时采用传统金属材料也存在制造成本高的问题,这就使得纤维复合材料在许多方面显示出其应用优势。
3.经现有技术检索发现,中国实用新型专利公告号为cn210653613u,公开了一种无人机骨架,所述无人机骨架包括骨架前部以及骨架后部,所述骨架后部包括与所述骨架前部相连的第一部分和与所述第一部分相连的第二部分,所述第二部分用于安装所述无人机的电路板组件,所述第一部分和所述第二部分使得所述骨架后部整体呈l形;所述骨架前部和所述骨架后部均设置有用于安装无人机机臂的机臂安装结构;所述骨架后部的所述第一部分和所述第二部分还设有散热结构,所述散热结构形成用于给所述电路板组件散热的散热通道。该实用新型就存在上述问题。
4.基于上述问题,本实用新型进行优化设计,改善目前存在的问题。非载人器往往具有翼身一体化程度较高的飞翼整体气动外形,因此在结构上需要采用大面积整体式机身成型技术。经过仿真和模拟计算,纤维复合材料不仅可以大面积成型,还可以通过压制、在高压釜外固化等工艺下整体成型,并可以引入汽车生产线生产工艺,提高生产效率,大大降低制造成本,非常适合非载人器机身结构的大规模制造。与此同时,非载人器骨架构造尽可能简单,也可以降低生产成本,提高生产效率。
5.与传统金属材料相比,复合材料具有比强度和比刚度高、热膨胀系数小、抗疲劳和抗振动能力强等特点。与传统非载人器材料相比,采用碳纤维复合材料的无人机整体重量减轻约25%-30%。另外,与其他复合材料相比,碳纤维复合材料具有高比强度和高比刚度、良好的耐腐蚀性和耐热性、可植入芯片或合金导体等优点,随着无人机消费市场的崛起和碳纤维复合材料技术的进步,碳纤维复合材料在未来无人机领域的应用不可估量。因此,本实用新型设计简单,但实用性强,能够解决上述问题,实际使用效果更好。
技术实现要素:6.针对现有技术中的缺陷,本实用新型的目的是提供一种复合材料非载人器骨架。
7.根据本实用新型提供的一种复合材料非载人器骨架,包括机身、发动机以及起落架,所述机身前端固定设置有机头,所述机身左右两端固定设置有机翼,所述机身后端固定设置有尾翼;
8.所述发动机固定设置在所述尾翼上,所述起落架固定设置在所述机身、所述机翼
以及所述尾翼上。
9.一些实施方式中,所述机身包括泡沫夹芯板机身,所述机头包括泡沫夹芯板机头,所述机身与所述机头上固定设置有卡槽,所述机身的前端卡扣并胶接设置所述机头。
10.一些实施方式中,所述机翼包括泡沫夹芯板机翼,所述机翼包括左机翼和右机翼,所述左机翼与所述右机翼上固定设置有卡槽,所述左机翼卡扣并胶接设置在所述机身左端,所述右机翼卡扣并胶接设置在所述机身右端。
11.一些实施方式中,所述尾翼包括泡沫夹芯板尾翼,所述尾翼包括尾翼一、尾翼二以及尾翼三,所述尾翼一、所述尾翼二以及所述尾翼三上固定设置有卡槽,所述尾翼一、所述尾翼二以及所述尾翼三卡扣并胶接设置在所述机身后端。
12.一些实施方式中,其特征在于,所述泡沫夹芯板的整体结构厚度设置为16mm-21mm。
13.一些实施方式中,所述机身、所述机头、所述机翼以及所述尾翼之间设置有胶接层,所述胶接层的厚度设置为1mm-3mm。
14.一些实施方式中,所述发动机包括发动机一和发动机二,所述尾翼一上卡扣并胶接设置所述发动机一,且所述发动机一通过螺栓连接设置在所述尾翼一上,所述尾翼三上卡扣并胶接设置所述发动机二,且所述发动机二通过螺栓连接设置在所述尾翼三上。
15.一些实施方式中,所述发动机与所述尾翼之间设置有胶接层,所述胶接层的厚度设置为1mm-2mm,所述发动机与所述尾翼之间固定设置有螺栓,所述螺栓的连接规格设置为m8-m12。
16.一些实施方式中,所述起落架包括起落架一、起落架二以及起落架三,所述起落架一通过复合材料垫片胶接并螺栓连接设置在所述机身上,所述起落架二通过复合材料垫片胶接并螺栓连接设置在所述尾翼一与所述左机翼的交接处,所述起落架三通过复合材料垫片胶接并螺栓连接设置在所述尾翼三与所述右机翼的交接处。
17.一些实施方式中,所述起落架与所述机身、所述尾翼以及所述机翼之间设置有胶接层,所述胶接层的厚度设置为1mm-1.5mm,所述起落架与所述机身、所述尾翼以及所述机翼之间设置有螺栓,所述螺栓的连接规格设置为m8-m12。
18.与现有技术相比,本实用新型具有如下的有益效果:
19.本实用新型通过设置采用泡沫夹芯板相互连接形成骨架,整体骨架重量轻,便于航空飞行;泡沫夹芯板之间以及泡沫夹芯板与发动机之间均是以卡槽和胶接形式相互连接,保证了结构整体强度;结构设计巧妙,可以提高生产效率,降低生产成本,整体结构匀称且具有美观性。
附图说明
20.通过阅读参照以下附图对非限制性实施例所作的详细描述,本实用新型的其它特征、目的和优点将会变得更明显:
21.图1为本实用新型复合材料非载人器骨架的结构示意图。
22.附图标记:
23.具体实施方式
24.下面结合具体实施例对本实用新型进行详细说明。以下实施例将有助于本领域的技术人员进一步理解本实用新型,但不以任何形式限制本实用新型。应当指出的是,对本领域的普通技术人员来说,在不脱离本实用新型构思的前提下,还可以做出若干变化和改进。这些都属于本实用新型的保护范围。
25.如图1所示为本实用新型复合材料非载人器骨架的结构示意图。包括机身1、发动机以及起落架,机身1前端固定设置有机头7,机身1左右两端固定设置有机翼,机身1后端固定设置有尾翼。发动机固定设置在尾翼上,起落架固定设置在机身1、机翼以及尾翼上。
26.机身1包括泡沫夹芯板机身,机头7包括泡沫夹芯板机头,机身1与机头7上固定设置有卡槽,且每两部分卡槽的接触面积为三分之一至三分之二范围,机身1的前端卡扣并胶接设置机头7。机翼包括泡沫夹芯板机翼,机翼包括左机翼2和右机翼3,左机翼2与右机翼3上固定设置有卡槽,且每两部分卡槽的接触面积为三分之一至三分之二范围,左机翼2卡扣并胶接设置在机身1左端,右机翼3卡扣并胶接设置在机身1右端。尾翼包括泡沫夹芯板尾翼,尾翼包括尾翼一4、尾翼二5以及尾翼三6,尾翼一4、尾翼二5以及尾翼三6上固定设置有卡槽,且每两部分卡槽的接触面积为三分之一至三分之二范围,尾翼一4、尾翼二5以及尾翼三6卡扣并胶接设置在机身1后端。
27.泡沫夹芯板分成若干部分,每部分均是纤维增强高密度泡沫制备而成,高密度泡沫厚度为10mm-15mm,泡沫夹芯板的整体结构厚度设置为16mm-21mm,泡沫夹芯板整体采用袋压成型或热压罐成型。机身1、机头7、机翼以及尾翼之间设置有胶接层,胶接层的厚度设置为1mm-3mm,胶接可以以结构胶或者胶膜形式。
28.发动机为外采定制件,发动机包括发动机一8和发动机二9,尾翼一4上卡扣并胶接设置发动机一8,且发动机一8通过螺栓连接设置在尾翼一4上,尾翼三6上卡扣并胶接设置发动机二9,且发动机二9通过螺栓连接设置在尾翼三6上。发动机与尾翼之间设置有胶接层,胶接层的厚度设置为1mm-2mm,胶接可以以结构胶或者胶膜形式,发动机与尾翼之间固定设置有螺栓,螺栓的连接规格设置为m8-m12。
29.起落架包括起落架一10、起落架二11以及起落架三12,起落架一10通过复合材料垫片胶接并螺栓连接设置在机身1上,起落架二11通过复合材料垫片胶接并螺栓连接设置在尾翼一4与左机翼2的交接处,起落架三12通过复合材料垫片胶接并螺栓连接设置在尾翼三6与右机翼3的交接处。复合材料垫片采用真空灌注树脂注射成型、预浸料袋压成型、模压成型或热压罐成型。起落架与机身1、尾翼以及机翼之间设置有胶接层,胶接层的厚度设置
为1mm-1.5mm,胶接可以以结构胶或者胶膜形式,起落架与机身1、尾翼以及机翼之间设置有螺栓,螺栓的连接规格设置为m8-m12。
30.在本技术的描述中,需要理解的是,术语“上”、“下”、“前”、“后”、“左”、“右”、“竖直”、“水平”、“顶”、“底”、“内”、“外”等指示的方位或位置关系为基于附图所示的方位或位置关系,仅是为了便于描述本技术和简化描述,而不是指示或暗示所指的装置或元件必须具有特定的方位、以特定的方位构造和操作,因此不能理解为对本技术的限制。
31.以上对本实用新型的具体实施例进行了描述。需要理解的是,本实用新型并不局限于上述特定实施方式,本领域技术人员可以在权利要求的范围内做出各种变化或修改,这并不影响本实用新型的实质内容。在不冲突的情况下,本技术的实施例和实施例中的特征可以任意相互组合。