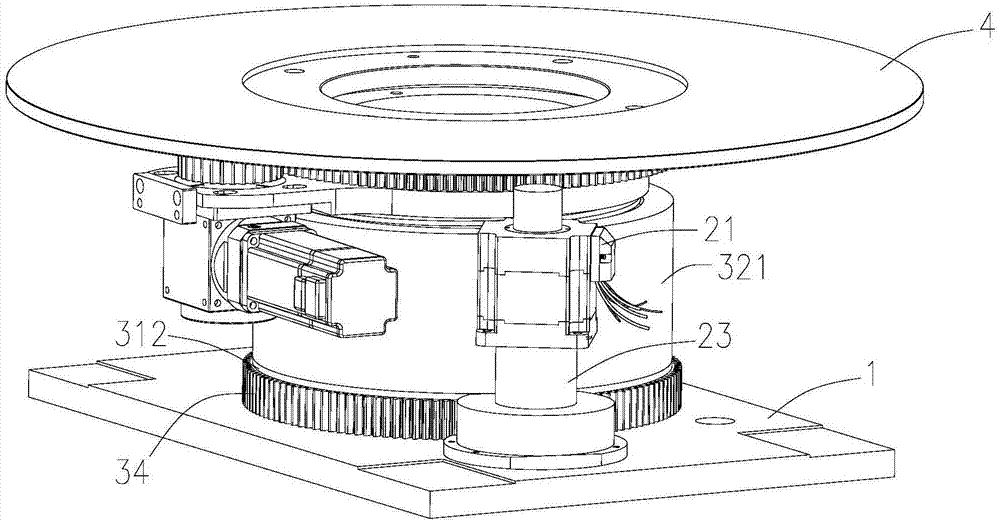
本发明属于作业与运输
技术领域:
,具体涉及一种举升装置传动机构的设计方法及举升装置。
背景技术:
随着人力成本的提高和工业自动化运输的需求,agv在企业中逐渐成为重要的搬运工具,传统的背负式agv仅能运输物料,为了扩大agv的应用范围,往往会增设其他功能设备配合agv使用,从而提高agv的使用性能。目前,较多配合agv使用的功能设备为举升装置,而在使用使用中,带举升及旋转功能的agv不仅能实现举升货物的功能,而且还具有实现货物相对地面旋转的功能,以便调整物料上料的角度,使用方便。现有的旋转举升装置通常采用的是梯形螺纹副进行举升传动,然而,现有梯形螺纹传动举升的方式,传动效率和传动精度低,需要大功率电机负载,越大功率的电机以及配套的减速机尺寸更大,因此导致举升装置功耗大以及占用空间大,且影响agv续航能力。技术实现要素:本发明的目的在于克服现有技术的不足,提供一种使举升装置举升后具有自锁功能,同时保证传动效率的举升装置传动机构的设计方法。为了达到上述目的,本发明采用以下技术方案:一种举升装置传动机构的设计方法,所述举升装置包括底座、驱动电机、减速器、滚珠丝杠副、托盘和相互啮合的第一齿轮和第二齿轮,滚珠丝杠副包括传动丝杠和传动螺母,托盘设于传动丝杠上,传动螺母与第二齿轮连接,驱动电机通过减速器驱动第一齿轮转动。所述设计方法包括以下步骤:a.确定托盘所需负载的重量m,托盘所需举升速度v、传动丝杠的中径d;b.通过直线-回转逆效率关系图表,选用滚珠丝杠副摩擦系数μ,并确定滚珠丝杠副传动效率η0<50%时,其导程角的范围为(0,λ0);c.根据λ=arctan(p/πd),得出滚珠丝杠副的导程的范围为(0,p0),确定使用的导程p1=p0/s,其中s为安全系数;d.根据λ=arctan(p/πd)和导程p1结合逆效率关系图表,确定滚珠丝杠副的设计传动效率η1和使用的螺旋升角λ1;e.由t=mg*p/(2πη),得出传动丝杠驱动托盘的需要的转矩t0;f.根据传动丝杠驱动托盘的设计转矩t1=tm*i0*η,通过选用驱动电机的输出扭矩tm以及选取驱动电机结合减速器传动和齿轮传动机械传动耗损的总传动效率η,其中η∈[0.8,0.9],使t1≥t0;并且,使托盘举升速度v≈n*p/(i0*60),其中n为选取驱动电机的转速,并且约等于误差小于2;从而设计得出第二齿轮、第一齿轮和减速器的总传动比i0。优选的,托盘直径d=[1.25d,2.5d];通过这样设置,保证托盘被传动丝杠举升时处于较为平稳的状态。优选的,选取滚珠丝杠副摩擦系数μ=0.01;通过这样设置,选取摩擦系数较低的滚珠丝杠副情况下,控制选材成本。优选的,总传动效率η选取为0.8,η为驱动电机、减速器传动和齿轮传动三者组合机械耗损后的总传动效率,电机效率一般为0.97减速器效率一般为0.95至0.97,齿轮效率一般为0.85至0.9三者相乘取最低值0.8,故η选取0.8;通过这样设置,选取最低总传动效率η,可以提高产品设计的容错率。优选的,安全系数s=1.25;通过这样设置,提高产品设计的可靠度。本发明的另一目的在于提供一种举升装置,包括底座、举升传动组件、驱动组件和托盘,所述驱动组件包括驱动电机、减速器和第一齿轮,所述驱动电机通过减速器驱动第一齿轮转动,所述举升传动组件包括第一回转支承、滚珠丝杠副和导向件,所述第一回转支承的内圈与底座固定连接,所述第一回转支承外圈设有与第一齿轮啮合的第二齿轮,所述导向件固定设于所述第一回转支承的内圈上,所述滚珠丝杠副包括传动丝杠和传动螺母,所述传动丝杠环设在所述所述导向件的外周,所述导向件与传动丝杠之间通过第一导向机构连接,所述第一导向机构限制传动丝杠转动,所述传动螺母环设在所述传动丝杠的外周并且固定安装在第一回转支承外圈上端,所述托盘设于所述传动丝杠的上端,所述传动丝杠与传动螺母之间形成的螺旋滚道填充有滚珠;所述传动丝杠的举升中径d=240mm、托盘直径d=[1.25d,2.5d];滚珠丝杠副的摩擦系数μ=0.01、导程角λ=0.92、导程p=12mm;第二齿轮与第一齿轮的传动比i1=118:40,减速器的传动比i2=10;驱动电机功率为400w,其输出扭矩tm=1.27n·m,转速n=3000r/min,利用滚珠丝杠副导程角小于螺旋副的当量摩擦角使满足自锁条件,从而举升后的举升装置通过滚珠丝杠副实现机械自锁,保证传动效率和工作精度的同时减少了举升装置需要电机抱闸造成的空间损失以及减少电量功耗损失而影响agv续航能力。进一步的,所述第一导向机构包括设于传动螺母内壁上的竖向导向槽,以及对应所述导向槽设置在导向件外壁上的导向轮;采用导向轮与导向槽配合的导向机构,使丝杆实现垂直升降功能,导向平稳、摩擦损耗低。通过本设计方法可根据实际对举升重量、举升速度和丝杠中径的需求,设计出一种应用了滚珠丝杆副的举升装置,由于本发明举升装置运用了滚珠丝杆副,其传动效率比现有的梯形螺纹副的举升装置要高50%至80%,举升的时间也大幅减少,同时通过本设计方法设计的举升装置还具有自锁的功能,并不需要电机对举升装置锁死或外设自锁装置,节约了制造成本和agv车体上的安装空间,同时减少了电机抱闸引起的功耗损失而影响agv续航能力。附图说明图1为举升装置的示意图;图2为举升装置的剖视图;图3为举升装置分解状态的示意图;图4为直线-回转逆效率关系图表;图5为梯形丝杠举升装置工作时的实测转矩图;图6为滚珠丝杠举升装置工作时的实测转矩图。具体实施方式以下结合附图说明本发明的技术方案:实施例一:参见图1至图4,一种举升装置传动机构的设计方法,所述举升装置包括底座1、驱动电机21、减速器23、滚珠丝杠副、托盘4和相互啮合的第一齿轮(图中未示出)和第二齿轮34,滚珠丝杠副包括传动丝杠322和传动螺母321,托盘4设于传动丝杠322上,传动螺母322与第二齿轮34连接,驱动电机21通过减速器23驱动第一齿轮转动。所述设计方法包括以下步骤:a.确定托盘4所需负载的重量m,托盘4所需举升速度v,传动丝杠322的中径d和托盘4直径d。b.参见图4,通过查阅直线-回转逆效率关系图表,选用滚珠丝杠副摩擦系数μ,并确定滚珠丝杠副传动效率η0<50%时,其导程角的范围为(0,λ0);由于螺纹自锁条件是导程角小于螺旋副的当量摩擦角,即滚珠丝杠副传动效率η0<50%时,滚珠丝杠副满足自锁条件。c.根据λ=arctan(p/πd),得出滚珠丝杠副的导程的范围为(0,p0),确定使用的导程p1=p0/s,其中s为安全系数。d.根据λ=arctan(p/πd)和导程p1结合查阅逆效率关系图表,确认滚珠丝杠副的设计传动效率η1和使用的螺旋升角λ1。e.由t=mg*p/(2πη),得出传动丝杠322驱动托盘4的需要的转矩t0。f.根据传动丝杠322驱动托盘4的设计转矩t1=tm*i0*η,通过选用驱动电机21的输出扭矩tm以及选取驱动电机21结合减速器23传动和齿轮传动机械传动耗损后总传动效率η,其中η∈[0.8,0.9],使t1≥t0。并且,使托盘4举升速度v≈n*p/(i0*60),其中n为选取驱动电机21的转速,并且约等于误差小于2,优选约等于误差小于1。从而设计得出第二齿轮34、第一齿轮和减速器23的总传动比i0。通过本设计方法可根据实际对举升重量、举升速度和丝杠中径的需求,设计出一种应用了滚珠丝杆副的举升装置,由于本发明举升装置运用了滚珠丝杆副,其传动效率比现有的梯形螺纹副的举升装置要高50%至80%,举升的时间也大幅减少,同时通过本设计方法设计的举升装置还具有自锁的功能,并不需要电机对举升装置锁死或外设自锁装置,节约了制造成本和agv车体上的安装空间,同时减少了电机抱闸引起的功耗损失而影响agv续航能力。作为优选方案,托盘4直径d=[1.25d,2.5d];通过这样设置,保证托盘4被传动丝杠322举升时处于较为平稳的状态。作为优选方案,选取滚珠丝杠副摩擦系数μ=0.01;通过这样设置,选取摩擦系数较低的滚珠丝杠副情况下,控制选材成本。作为优选方案,总传动效率η选取为0.8;η为驱动电机、减速器传动和齿轮传动三者组合机械耗损后的有效传动效率,电机效率一般为0.97减速器效率一般为0.95至0.97,齿轮效率一般为0.85至0.9三者相乘取最低值0.8,故η选取0.8;通过这样设置,选取最低总传动效率η,可以提高产品设计的容错率。作为优选方案,驱动电机21的转速选取n=3000r/min。为了更好地说明本发明的技术方案,以下通过一个具体的实施例子解释本发明的设计方法。本发明的技术方案的举升装置,原始采用梯形丝杠传动举升,梯形丝杠导程p=64mm,驱动电机功率p=750w,该驱动电机的转矩t=2.37n·m;第一齿轮、第二齿轮和减速器总传动比i=177;托盘负载总量为m=650kg,参见图5,梯形丝杠举升装置举升过程中实测驱动电机电机最高负载率为0.76。从而得出:梯形丝杠实际输出转矩t=t1*i*有效传动效率*电机负载率=2.37*177*0.8*0.76=255n·m。其中,有效传动效率为驱动电机结合减速器传动和齿轮传动机械耗损后的有效传动效率。负载f=mg=650*9.8=6370n。实际传动效率η=f*p/(2πt)=25%。举升速度=n*p/(i*60)=3000*64/(177*60)=18mm/s。显然,使用梯形丝杠传动效率低,需要匹配大功率电机以及及大减速器,举升装置整体占空间大。基于上述梯形丝杠传动方式缺点,对举升装置采用本发明的设计方法进行设计。目标需求降低驱动电机功率,且传动丝杠举升速度提升至20mm/s,满足机械自锁功能即传动效率低于50%。根据举升稳定性和防倾覆需求传动丝杠的举升中径d/托盘直径d=1:2.5,取d=240mm。举升装置负载自锁受力情况为直线—回转受力,因此取逆效率图表;取摩擦系数μ=0.01,当逆效率≤50%时,导程角λ0≤1.2。螺旋升角λ=arctan(p/πd),从而得出导程p≤15mm。基于结构安全程度,确定设计导程p1=p0/s=15/1.25=12mm。根据逆效率关系图表和λ=arctan(p/πd),确定λ=0.92时,传动效率η=42%。根据t=mg*p/(2πη),其中,mg=650*9.8=6370n、p=12mm、η=42%;得出传动丝杠驱动托盘的需要的转矩t0=29n·m。功率400w750w11001500额定转速3000r/min3000r/min3000r/min3000r/min额定转矩1.27n·m2.37n·m3.50n·m4.77n·m在上述国标伺服电机规格表中,选取驱动电机选取伺服电机400w,其输出扭矩tm=1.27n·m,转速n=3000r/min;总传动效率η选取0.8。当然,在其他实施方式中,可根据使用需求选取其它功率和扭矩的驱动电机。使传动丝杠驱动托盘的设计转矩t1=tm*i0*η=1.27*0.8*i0>t0=29n·m;以及使托盘举升速度v=n*p1/(i0*60)=600/i0≥20。为了满足上述要求,选取第二齿轮与第一齿轮的传动比i1=118:40;选取减速器传动比i2=10,故总传动比i0=i1*i2=(118/40)*10=29.5。满足1.27*0.8*29.5=30>t0=29n·m,且v=n*p1/(i0*60)=600/i0=20.3>20mm/s,符合要求。故托盘的举升速度为20.3mm/s,传动丝杠驱动托盘的设计转矩t1=30n·m符合设计要求。上述第二齿轮与第一齿轮i1和减速器传动比i2的选取可采用现有的齿轮规格和减速器规格进行选择和验算并最终确认选取,也可以考虑驱动电机和举升组件是否干涉和举升装置整体结构的紧凑性进行齿轮规格和减速器规格的选择。通过实验检测,参见图6,滚珠丝杠举升装置举升过程中,驱动电机实际最高负载率为0.72,负载为500kg。传动丝杠实现输出转矩=t1*0.72=30*0.72=21.36n·m。实际传动效率η=f*p/(2πt)=5000*12/(2*3.14*21.3*1000)=45%,低于50%。在实际运用中改进后的举升装置结构传动效率更高,且有自锁功能,不需要电机有抱闸功能,省电省空间。实施例二:参见图1至3,本实施例提供一种举升装置,其包括底座1、举升传动组件、驱动组件和托盘4,所述驱动组件包括驱动电机21、减速器23和第一齿轮,所述驱动电机21通过减速器23驱动第一齿轮转动,所述举升传动组件包括第一回转支承31、滚珠丝杠副和导向件33,所述第一回转支承31的内圈311与底座1固定连接,所述第一回转支承31外圈312设有与第一齿轮啮合的第二齿轮34,所述导向件33固定设于所述第一回转支承31的内圈311上,所述滚珠丝杠副包括传动丝杠322和传动螺母321,所述传动丝杠322环设在所述所述导向件33的外周,所述导向件33与传动丝杠322之间通过第一导向机构连接,所述第一导向机构限制传动丝杠322转动,所述传动螺母321环设在所述传动丝杠321的外周并且固定安装在第一回转支承31外圈312上端,所述托盘4设于所述传动丝杠322的上端,所述传动丝杠322与传动螺母321之间形成的螺旋滚道323填充有滚珠324。作为优选方案,所述第一导向机构包括设于传动螺母321内壁上的竖向导向槽51,以及对应所述导向槽51设置在导向件33外壁上的导向轮52,为了增强导向作用,所述导向轮52可沿导向槽51的方向设有多个。所述导向轮52包括连接部521和滚动部522,所述滚动部522可相对连接部521转动,所述连接部521固定在导向件33上,滚动部522安装在导向槽51内并且与导向槽51的内壁滚动配合。所述第一导向机构结构简单紧凑,当内螺纹零件转动时,导向轮52与导向槽51的配合限制了传动螺母321只能上下移动而不能转动,起到了导向的作用,另外,传动螺母321升降的时候,导向轮52相对传动螺母321沿导向槽51滚动,与现有的导向机构相比,导向轮52将滑动摩擦转换成滚动摩擦,从而减少了第一导向机构在升降时的摩擦,从而降低其损耗,延长其寿命。根据上述说明书的揭示和教导,本发明所属领域的技术人员还可以对上述实施方式进行变更和修改。因此,本发明并不局限于上面揭示和描述的具体实施方式,对本发明的一些修改和变更也应当落入本发明的权利要求的保护范围内。此外,尽管本说明书中使用了一些特定的术语,但这些术语只是为了方便说明,并不对本发明构成任何限制。当前第1页12