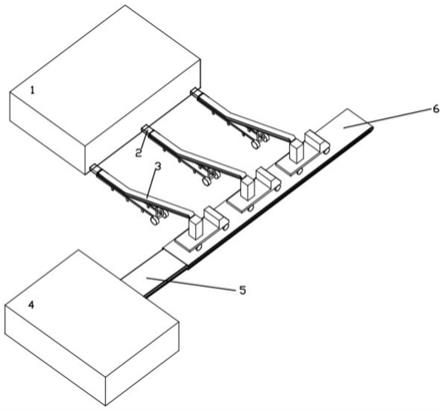
1.本发明涉及自动化装箱领域,具体涉及一种散改集自动化装箱装置及系统。
背景技术:2.散货是指煤炭、铁矿石、粮食等颗粒状物料,也是港口最大宗的货类。传统散货码头作业包括装船和卸船两种形态。装船作业时,堆场上的物料由斗轮取料机挖取后放入皮带机系统,输送到码头前沿的装船机上,通过装船机的移动和输料悬臂的仰俯,将物料装满各个船舱。卸船作业时,码头前沿的卸船机将物料从船舱中取出,抓斗式卸船机抓取的物料放入漏斗后落在皮带机上,输送到码头后方堆场,连续式卸船机挖取的物料经卸船机垂直提升机放入皮带机,输送到堆场通过堆料机进行布放。
3.散改集,即将散货改为集装箱的方式进行运输,主要应用于包含海、铁的多式联运。散改集是目前我国航运领域一项重要的创新,目的是顺应绿色化的时代要求,加速多式联运的探索,深化运输方面的技术改革,目前,国内大多数海港已经开始在多式联运中落实此项创新。然而,由于目前港口装箱工艺尚未及时改进,仍使用传统作业技术,导致一系列的问题随之产生,并阻碍创新此进程。
4.一方面,港区码头散改集集装箱的装箱过程中,自动化程度较低,即装箱地点与散货船卸货堆场并未连成一个整体,另一方面,皮带机位置固定,需要人工将集装箱运送至皮带机装箱位置,效率较低;同时,现用集装箱为普通集装箱,其最大承重低于散货集装箱,导致大量集装箱被损坏,减少使用寿命。
5.目前,国内应对散改集技术的发明较少,而上述背景问题不利于此项创新的可持续发展,亟需一种结合信息化技术、提高效率和经济性的发明应对现有技术困境。
技术实现要素:6.本发明的目的是解决上述现有技术的不足,提供一种散改集自动化装箱装置及系统,优化港口装箱过程,提高每个过程的衔接程度以及作业效率。
7.为了达到上述目的,本发明提供了一种散改集自动化装箱装置,包括:
8.陆上散装堆场,用于堆放及存储散货;
9.若干皮带机,用于将散货由所述陆上散装堆场传送至集装箱内,其末端向上倾斜;
10.翻转仓库,用于放置空集装箱,并将集装箱翻转至箱门向上;
11.感应引导通道,其一端连接所述翻转仓库,用于将集装箱从所述翻转仓库中运出;及
12.装箱通道,与所述感应引导通道的另一端相连;
13.集装箱由所述翻转仓库经所述感应引导通道,运至所述装箱通道上,使每个集装箱的箱门对准所述皮带机的末端;装箱完成后,集装箱沿所述装箱通道被运出所述装箱装置。
14.优选地,所述感应引导通道包括:
15.第一传送带,用于承载并传送集装箱;
16.警示区,位于所述感应引导通道靠近所述装箱通道的一端;
17.等待区,除所述警示区外的区域均为等待区;及
18.第一重量传感器。
19.优选地,所述装箱通道包括:
20.第二传送带,用于承载并传送集装箱;
21.若干装配区,每个所述装配区设于所述皮带机末端的下方,每个所述装配区包括第二重量传感器。
22.优选地,每个所述装配区还包括位置传感器,用于监测空集装箱是否运送到位。
23.优选地,还包括若干待装封闭通道,其一端连接陆上散装堆场,用于将散货从陆上散装堆场中运出,另一端连接所述皮带机的始端。
24.优选地,所述待装封闭通道包括:
25.单元门,其设于所述待装封闭通道与陆上散装堆场连接的一端;
26.第三传送带,用于承载并传送散货;及
27.第三重量传感器。
28.优选地,所述待装封闭通道还包括控制器,用于控制单元门的开关。
29.优选地,所述第三传送带为可逆向转动。
30.一种散改集自动化装箱系统,用于所述的装箱装置,所述的系统包括:
31.数据采集系统,采集所述第一传感器、第二传感器和第三传感器将所述的重量信号,并转化为电信号;采集所述单元门的开关信号,并转化为电信号;
32.数据处理系统,接收数据采集系统的电信号,根据电信号,判断装箱过程的运行状态,下发指令;
33.机械控制系统,接收数据处理系统的指令,控制第一传送带、第二传送带和第三传送带的运行;
34.所述数据采集系统、数据处理系统和机械控制系统之间电连接。
35.本发明的有益效果为:
36.(1)解决集装箱损坏问题:装箱通道上的重量传感器可以监测装箱货物重量,达到临界重量时,停止装货,既保证经济效益(最大装货量),又满足不超过最大承重的要求。
37.(2)解决现有装卸技术衔接不紧密问题:将陆上散装堆场和装箱作业连成一个整体,即包括卸货地、装箱地和集装箱翻转地。卸货至陆上散装堆场,皮带机与陆上散装堆场连接,感应引导通道使集装箱翻转箱门后直接运输至指定位置,无需再人工进行位置对应,形成一体化作业模式,减少损耗时间。
38.(3)解决换装导致效率较低问题:每次每箱装货完成后,皮带机无需停止作业,通过待装封闭通道暂存待装散货,减少等待所需时间。
附图说明
39.图1为本发明的散改集自动化装箱装置的示意图。
40.图2为本发明的散改集自动化装箱装置的翻转仓库、感应引导通道和装箱通道示意图。
41.图3为本发明的散改集自动化装箱系统示意图。
42.图4为本发明的散改集自动化装箱装置的装箱过程流程图。
43.图中,1
‑
陆上散装堆场,2
‑
待装封闭通道,3
‑
皮带机,4
‑
翻转仓库,5
‑
感应引导通道,51
‑
等待区,52
‑
警示区,6
‑
装箱通道,61
‑
装配区,62
‑
位置传感器,63
‑
第二重量传感器。
具体实施方式
44.下面将结合附图对本发明的技术方案进行清楚、完整地描述,显然,所描述的实施例是本发明一部分实施例,而不是全部的实施例。基于本发明中的实施例,本领域普通技术人员在没有做出创造性劳动前提下所获得的所有其他实施例,都属于本发明保护的范围。
45.如图1所示,本发明公开的散改集自动化装箱装置包括集成为一个整体系统的陆上散装堆场1、若干个待装封闭通道2、若干个皮带机3、翻转仓库4、感应引导通道5和装箱通道6。待装封闭通道2和皮带机3一一对应设置。
46.散货堆放并存储在陆上散装堆场1中。陆上散装堆场1置于散货船靠泊岸边,代替传统散装堆场,其规模满足国家建设标准,为长方体,在一实施例中,陆上散装堆场1的长为54米,高为4米,宽将根据港口具体规模自行设置。陆上散装堆场1根据存储重量不同分为三类:2.5
‑
5万吨、5.1
‑
15万吨以及15万吨以上。
47.待装封闭通道2为圆形管道,两侧封闭,与集装箱材质相同。待装封闭通道2的具体数量可根据港区需要自行确定,最多可设置数量为陆上散装堆场1总长度/[2.5(集装箱宽)+安全距离]。每个待装封闭通道2包括单元门、第三传送带和第三重量传感器。待装封闭通道2与地面平行,其一端与陆上散装堆场1焊接,另一端与皮带机3相连。在本例中,待装封闭通道2与皮带机3相互搭接。单元门设于待装封闭通道2与陆上散装堆场1的连接处,本例采用推拉式单元门,发挥卡口功能,即可人工手动开关单元门,也可设置控制器,通过控制器遥控单元门的开关。单元门打开,装箱过程开始;单元门关闭,装箱过程结束。第三传送带为可逆传送带,在装箱过程结束后,能够通过逆向运转,将其内残余的散货反向运输至陆上散装堆场1中。第三重量传感器能够测量待装封闭通道2内残余散货的重量,当集装箱装满后,若第三重量传感器测得的重量大于0,则第三传送带逆向运输,直至第三重量传感器测得的重量等于0。由于待装封闭通道2为全封闭式结构,煤炭等散货存储于其内时,能防止散货不被吹散至空气中,造成环境污染。
[0048]
皮带机3用于将散货由所述陆上散装堆场1传送至集装箱内。皮带机3的始端连接待装封闭通道2,末端向上倾斜,使皮带机3的高度高于集装箱的箱门处。
[0049]
正常运输时,集装箱的箱门在侧面,直接打开箱门即可装卸货物。装运散货时,散货是通过皮带机3运送至集装箱内,因此,本装箱装置设置翻转仓库4,用于放置空集装箱,并将集装箱翻转至箱门向上。装箱过程结束后,使用场站专有设备恢复至水平状态。
[0050]
如图2所示,感应引导通道5的一端连接翻转仓库4,另一端连接装箱通道6,用于将待装集装箱由翻转仓库4引导至装箱通道6上。感应引导通道5包括第一传送带和第一重量传感器。第一传送带用以承载和传送待装集装箱。感应引导通道5靠近装箱通道6的一端设有警示区52,其余区域为等待区51。当第一重量传感器感知到第一个待装集装箱通过警示区52后,待装封闭通道2和皮带机3开始启动。在一个装箱过程中,当前一批次的集装箱在装箱通道6处装运散货时,后一批次的待装集装箱在感应引导通道5处的等待区51依次等待。
[0051]
装箱通道6上设有第二传送带,用于承载并传送集装箱。装箱通道6上包括若干装配区61,每个装配区61设于皮带机3末端的下方,每个装配区61都包括一个第二重量传感器63。当同一批次的待装集装箱都到达装配区61时,皮带机3上的散货被运送至集装箱内;当第二重量传感器63测得的重量达到满箱重量时,该批次的集装箱装配完成,第二传送带将该批次的集装箱运出;同时,将下一批次的待装集装箱传送到装配区61。在本例中,每个装配区61还包括一个位置传感器62,以监测空集装箱是否运送到位。位置传感器62可以是光敏传感器、红外传感器等。在不设有位置传感器62的实施例中,第二重量传感器63能够起到监测空集装箱是否运送到位的作用。当第二重量传感器63测得的重量为0时,待装集装箱未运送到位,当第二重量传感器63测得的重量为空集装箱的重量时,待装集装箱运送到位。
[0052]
为确定每装箱一轮最小长度,可利用如下方法。从装箱通道6开始工作时,采集瞬时速度v,通过计算可以得到一段微小时间内的距离,因此将时间作如下处理:以100ms为基本单位,在每个100ms开始时采集瞬时速度v
i
,并计算出每个区域间隔距离s
i
:瞬时速度的计算公式为v=n
×
s
×
π
×
d;其中,n为电机每分钟转速,s为减速机变速比,d为电机直径;工作一次需要最小总距离为l=s1+s2+
…
+s
n
。
[0053]
如图3所示,本发明还提供了一种散改集自动化装箱系统,包括:
[0054]
数据采集系统,采集所述第一传感器、第二传感器和第三传感器将所述的重量信号,并转化为电信号;采集所述单元门的开关信号,并转化为电信号;
[0055]
数据处理系统,接收数据采集系统的电信号,根据电信号,判断装箱过程的运行状态,下发指令;
[0056]
机械控制系统,接收数据处理系统的指令,控制第一传送带、第二传送带和第三传送带的运行;
[0057]
所述数据采集系统、数据处理系统和机械控制系统之间电连接。三个子系统之间均通过无线传输方式发出控制指令,且以串联工作模式相连,构成全自动数字化信息系统,各系统间不可越级进行,且整个装箱过程停止前,均循环操作之前装箱过程。
[0058]
如图4所示,本发明的一个装箱过程包括如下步骤:
[0059]
1)装箱过程启动:
[0060]
打开待装封闭通道2的单元门,装箱过程开启;
[0061]
待装集装箱在翻转仓库4内由箱门在侧面翻转至箱门向上,并由运载车从翻转仓库4中运至感应引导通道5上,此时感应引导通道5的第一传送带的速度为v1;
[0062]
运有待装集装箱的运载车,被感应引导通道5上的第一传送带运至警示区52时,待装封闭通道2和皮带机3启动;
[0063]
运有待装集装箱的运载车全部运送至装箱通道6上的装配区61后,皮带机3将散货运送至集装箱中。
[0064]
2)装箱过程中:
[0065]
感应引导通道5的第一传送带的速度为v2,v2接近于0;
[0066]
第二重量传感器63测得的重量达到满箱重量时,该批次的集装箱装配完成:
[0067]
a)若感应引导通道5的等待区51的重量不为0,说明仍有待装集装箱还未装箱,此
时待装封闭通道2的第三传送带低速工作,皮带机3暂停工作,由装箱通道6的第二传送带将已装满的集装箱运出装箱通道6,再由运载车运送集装箱驶离;之后,感应引导通道5的第二传送带的速度变为v1,将待装集装箱运送至装箱通道6的装配区61上,皮带机3将散货运送至集装箱中;
[0068]
b)若感应引导通道5的等待区51域重量为0,进一步判断等待时间,等待时间指的是从待装集装箱运送到装配区61,至该待装集装箱装满的时间,该时间由人为提前设定:
[0069]
i.若实际的等待时间低于设定的等待时间,说明翻转仓库4中的翻箱过程延迟,此时待装封闭通道2的第三传送带低速工作,皮带机3暂停工作,等待翻转仓库4继续完成翻箱;
[0070]
ii.若实际等待时间大于等于设定的等待时间,说明所有待装集装箱均已完成装箱;
[0071]
3)装箱结束:
[0072]
所有待装集装箱均完成装箱后,皮带机3停止工作;
[0073]
若待装封闭通道2上第三重量传感器测得的重量大于0,说明待装封闭通道2内还有残余散货,则待装封闭通道2的第三传送带逆向运行,将残余散货运回陆上散装堆场1;
[0074]
若待装封闭通道2上第三重量传感器测得的重量等于0,说明待装封闭通道2内的散货已运尽,关闭待装封闭通道2的单元门,装箱过程结束。
[0075]
本发明能够提高自动化装箱工艺的效率。相较于传统散货装箱流程的装箱过程,做如下假设:假设w为散货船上待卸载散货的总重量,w表示单个集装箱装载的重量,t
cs
表示散货从散货船到存储区,再经过皮带机3的总工作时间,规定散货开始从散货船上卸货为开始计时时刻,皮带机3停止工作为计时终止时刻;t
s
表示当前集装箱装货结束至下一个连续空集装箱到达的时间,也为自动卡口一次工作时间,t
s1
表示传统的换箱时间,t
s2
表示自动化装箱条形带的换箱时间;t0表示货物一次装箱时间;l表示当前正在装载的集装箱几何中心与下一个连续空集装箱几何中心在装箱条形带上投射的实际距离,即装箱条形带工作一次前进的距离。因此可以计算得到传统散货装箱作业总时间为:以及所设计的自动化装箱作业总时间:其中因此,相比较传统的装箱作业,自动化装箱过程的效率在装箱效率上有:联立上式
①②③④
可得其中传统换箱时间t
s1
、货物装箱时间t0、散货从船到离开皮带机3的总时间t
cs
以及待卸货的散货总重量w为完成一次装箱任务后实际测得的量,集装箱之间的距离l、单个集装箱最大装载重量w、装箱条形带运行平均速度均为已知量。以宁
波某散货码头为例,一艘装载5000吨煤炭的散货船,用最大载重量为20吨的20英寸集装箱运输,煤炭从散货船通过带抓斗的工具以及皮带机3到达装箱点的时间约为5分钟,装箱时间约为20分钟,此外优化前待装集装箱之间的间隔大约为3分钟,假设设计时采用充足的间距,取8m(l必须大于运载集装箱agv的宽度),装箱条形带的平均运行速度为0.4m/s,此时优化后提升的效率至少为9.54%。(即一次装箱任务需要24小时的话,采用该自动化装箱工艺可以节省至少2.39个小时)。
[0076]
尽管本发明的内容已经通过上述优选实施例作了详细介绍,但应当认识到上述的描述不应被认为是对本发明的限制。在本领域技术人员阅读了上述内容后,对于本发明的多种修改和替代都将是显而易见的。因此,本发明的保护范围应由所附的权利要求来限定。