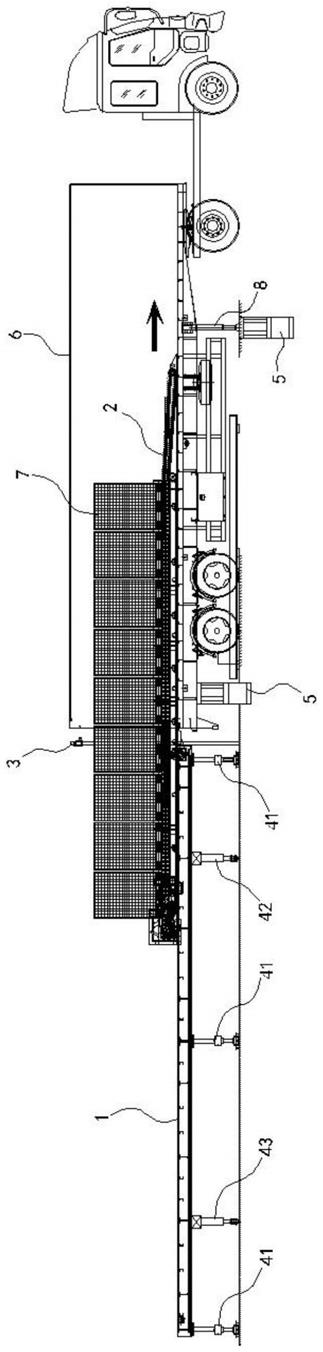
[0001]
本实用新型涉及物流领域,特别涉及一种智能定位自动装车系统。
背景技术:[0002]
自动仓储、自动输送以及智能分拣技术在物流行业已得到越来越多的应用,物流装备自动化技术的创新促进了电子商务及物流运输行业的快速发展。但在物流中心装车作业环节,目前仍然是以传统的人工散件搬运、叉车、地牛等装卸作业方式为主,自动化水平低,需投入大量的装卸作业工人,劳动强度大,生产效率低下。随着人力成本不断上升,劳动力日益短缺,传统的人工或简易装备装卸作业方式已成为影响电子商务及物流运输行业发展的瓶颈之一。
[0003]
现有移动平台的装车系统有以下不足,其一、由于地面没有倒车导向装置,物流车辆倒车倾斜,而主平台无法旋转,移动平台没有浮动定位装置,导致移动平台在实际作业中无法与车辆在水平和左右方向对齐,不能实现货物顺利装车;其二,移动平台采用链条和滚筒驱动输送方式,其无法兼容多种单元规格和散件货物。
技术实现要素:[0004]
本实用新型实施例所要解决的技术问题在于,提供一种智能定位自动装车系统,可以快速方便地完成车辆对齐装货。
[0005]
为达到上述目的,本实用新型公开了一种智能定位自动装车系统,包括:
[0006]
主平台;
[0007]
移动平台,所述移动平台包括支撑主体、设置于所述支撑主体顶面的传送机构、设置于所述支撑主体底面的若干平台滚轮和平台驱动装置,所述若干平台滚轮分别滚动放置于所述主平台的顶面,所述平台驱动装置用于驱动所述移动平台在所述主平台顶面沿车厢深度方向移动;
[0008]
主平台调整装置,所述主平台调整装置包括横向调整机构和纵向调整机构,所述横向调整机构用于驱动所述主平台在车厢的宽度方向上移动,所述纵向调整机构用于驱动所述主平台在车厢的高度方向上移动;
[0009]
车厢调整装置,所述车厢调整装置设置于车厢下方,用于驱动车厢在宽度方向上移动;
[0010]
摄像头,所述摄像头设置于所述主平台与车厢之间朝向所述移动平台与车厢门;
[0011]
控制模块,所述摄像头、横向调整机构、纵向调整机构、车厢调整装置、传送机构和平台驱动装置分别与所述控制模块通信连接。
[0012]
优选的,还包括连接翻板,所述连接翻板摆动设置于所述主平台朝向车厢的一端。
[0013]
优选的,所述移动平台的前端具有向地面倾斜的斜面。
[0014]
优选的,所述主平台的顶面具有若干沟槽,所述移动平台的底面具有若干凸块,所述若干凸块分别滑动设置于所述若干沟槽中。
[0015]
优选的,所述车厢调整装置包括升降底座、车厢托板和车厢驱动装置,所述升降底座可升降的设置于地面上,所述车厢托板可沿车厢宽度方向移动地设置于所述升降底座的顶面,所述车厢驱动装置用于驱动所述车厢托板沿车厢宽度方向移动。
[0016]
优选的,所述横向调整机构包括前、后支柱和前、后横向驱动装置,所述前、后支柱的上端分别与所述主平台前、后端的底面固接,所述前、后支柱的下端分别可沿车厢宽度方向移动地设置于地面上,所述前、后横向驱动装置分别用于驱动所述前、后支柱沿车厢宽度方向移动。
[0017]
优选的,所述纵向调整机构包括若干伸缩顶杆,所述若干伸缩顶杆的伸缩端分别与所述主平台的底面固接,所述若干伸缩顶杆的固定端的底面分别可沿车厢宽度方向移动地设置于地面上。
[0018]
优选的,所述前、后支柱和所述若干伸缩顶杆的底面分别转动设置有若干地面滚轮。
[0019]
优选的,还包括车厢稳定装置,所述车厢稳定装置包括稳定杆,所述稳定杆的一端与车厢前端底面接触,所述稳定杆的另一端与地面接触,所述车厢稳定装置设置于车厢前端的下方,所述车厢调整装置设置于车厢后端的下方,所述升降底座升起时所述车厢托板托住车厢的后端,所述稳定杆用于托住车厢的前端,使车厢受压时高度不降低。
[0020]
优选的,所述传送机构包括链条和链板,所述链条的销轴延伸出托板构成插轴,所述链板的端部具有插孔,所述插轴插装于所述插孔中。
[0021]
相比于现有技术,本实用新型的有益效果在于:
[0022]
通过设置移动平台将货物整体移动至车厢内部,并在移动平台上设置传送机构,在移动平台从车厢内部退出的过程中传送机构将货物垛逐垛放置于车厢内;
[0023]
通过设置摄像头自动检测移动平台与车厢的长度方向是否对正、高度是否一致,并通过设置横向调整机构和纵向调整机构分别调整主平台的横向位置和纵向位置,使得移动平台与车厢的长度方向对正且高度一致;
[0024]
由于主平台较长,当车厢与主平台之间的长度方向上存在轻微的角度时,远离车厢一端的主平台就需要调整很长的距离才能与车厢对齐,通过设置车厢调整装置,使得车厢也可参与对齐调整,调整距离更短,速度更快,可以容纳的停车误差更大;
[0025]
车厢调整装置包括升降底座使得车厢托板可升降,升降底座升起时车厢托板托住车厢的后端,同时在车厢前端设置了稳定杆用于托住车厢前端,使得移动平台和货物进入车厢内部时,车厢不会受压而高度下降,从而保持车厢内平稳;
[0026]
通过设置连接翻板将主平台和车厢连在一起,使得移动平台可以在平台滚轮的作用下从主平台移动进入车厢内部;
[0027]
通过设置凸块和沟槽相互配合,使得移动平台的一端移动进入车厢后,另一端依然受限位使移动平台的移动轨迹稳定可控,不会因为偏移而撞击车厢内壁等;
[0028]
通过将传送机构设置为链条链板的形式,并将链条的销轴延伸出托板构成插轴用于插装链板,使得传送机构整体厚度大大减小,节省了车厢内宝贵的高度空间。
附图说明
[0029]
图1为本实用新型实施例整体结构示意图;
[0030]
图2为本实用新型实施例主平台结构示意图;
[0031]
图3为本实用新型实施例移动平台结构示意图;
[0032]
图4为本实用新型实施例横向调整机构结构示意图;
[0033]
图5为本实用新型实施例车厢调整装置结构示意图;
[0034]
图6为本实用新型实施例传送机构结构示意图。
具体实施方式
[0035]
为使本实用新型的目的、技术方案和优点更加清楚,下面将结合图1-图6的附图对本实用新型作进一步地详细描述。
[0036]
参照图1-图6所示,一种智能定位自动装车系统,包括主平台1、移动平台2、主平台调整装置、车厢调整装置5、摄像头3、车厢稳定装置和控制模块。
[0037]
参照图2、4所示,主平台1是由钢骨架构成的平板状的平台,主平台1朝向车厢6的端部摆动设置有连接翻板11,连接翻板11由翻板驱动装置12驱动摆动,从而将主平台1的端部与车厢6内的地板连接起来,使得移动平台2可以在主平台1和车厢6内地板之间顺畅移动;主平台1的下方设置有主平台调整装置用于调整主平台1的高度位置和车厢6宽度方向上的位置,主平台调整装置包括横向调整机构和纵向调整机构。
[0038]
纵向调整机构包括若干伸缩顶杆41,本实施例伸缩顶杆41优选采用为电液推杆,若干伸缩顶杆41的伸缩端分别与主平台1的底面固接,若干伸缩顶杆41的固定端的底面分别可沿车厢宽度方向移动地设置于地面上,伸缩顶杆41的伸缩端伸缩时联动主平台1升降高度。
[0039]
横向调整机构包括横向调整机构包括分别与主平台1前、后端底面固接的前、后支柱42、43;前支柱42包括分别与主平台1前端底面固接的左前、右前支柱421、422,左前、右前支柱421、422的下端分别可沿车厢宽度方向移动地设置于地面上,左前、右前支柱421、422之间设置有固接于地面上的前横向驱动装置423,前横向驱动装置423与前丝杠424传动连接,前丝杠424的两端分别与左前、右前支柱421、422螺纹连接,使得前横向驱动装置423驱动前丝杠424转动时左前、右前支柱421、422沿前丝杠424左右滑动联动主平台1沿车厢宽度方向移动。左前、右前支柱421、422优选采用可伸缩支柱,伸缩支柱的伸缩端与主平台1固接,使得主平台1升降时不会音箱前丝杠424与左前、右前支柱421、422的螺纹连接。
[0040]
后支柱43包括与左前、右前支柱421、422结构相同、设置方式相同的左后、右后支柱,还包括与前横向驱动装置423、前丝杠424结构相同、设置方式相同的后横向驱动装置、后丝杠。
[0041]
本实施例优选在前、后支柱42、43和若干伸缩顶杆41的底面分别转动设置有若干地面滚轮44,从而实现前、后支柱42、43和若干伸缩顶杆41可沿车厢宽度方向移动。
[0042]
参照图3、4所示,移动平台2包括支撑主体23、设置于支撑主体23顶面的传送机构22、设置于支撑主体23底面的若干平台滚轮24和平台驱动装置26,若干平台滚轮24分别滚动放置于主平台1的顶面,平台驱动装置26用于驱动平台滚轮24转动联动移动平台2在主平台1顶面沿车厢6深度方向移动;主平台1的顶面具有若干沟槽13,移动平台2的底面具有若干凸块27,若干凸块27分别滑动设置于若干沟槽13中,使移动平台2移动过程中受到限位,移动轨迹更准确不会偏移。移动平台2的前端具有向地面倾斜的斜面21使货物从移动平台2
移动到车厢6地板上时更顺畅。
[0043]
参照图6所示,传送机构22优选采用为链条链板的形式,其中链条221的销轴226延伸出托板225构成插轴223,链板222的端部具有插孔224,插轴223插装于插孔224中。使得链条、链板处于同一厚度内,减少了对车厢高度空间的占用。链条由链条驱动装置25驱动传送。
[0044]
参照图5所示,车厢调整装置5设置于车厢6下方,用于驱动车厢5在宽度方向上移动;车厢调整装置5包括升降底座51、车厢托板52和车厢驱动装置53,升降底座51可升降的设置于地面上,车厢托板52可沿车厢宽度方向移动地设置于升降底座51的顶面,车厢驱动装置53用于驱动车厢托板52沿车厢宽度方向移动;本实施例优选在升降底座51的顶面设置滑轨511,在车厢托板52的底面设置滑块521,滑块521滑动套装于滑轨511上,车厢托板2底面还固接有齿条522,车厢驱动装置53与齿条522传动连接用于驱动齿条522移动,联动车厢托板52沿滑轨511在车厢宽度方向上移动。
[0045]
车厢稳定装置可为垫块、撑杆等用于支撑车厢前端的支撑物,本实施例优选车厢稳定装置为稳定杆8,稳定杆8优选采用为电液推杆。稳定杆8液压伸出时一端与底面接触,另一端与车厢6前端底面接触,用于支撑车厢6的前端,此时车厢调整装置5的升降底座51保持升起,使车厢托板52与车厢6后端的底面保持接触,用于支撑车厢6的后端,从而使车厢6整体收到支撑,不会因为重物下压而车载板簧变形、车厢高度下降。稳定杆8的下方还可设置第二个车厢调整装置5用于承载稳定杆8,使得车厢6整体可横移、升降,更便于调整位置;或者用第二个车厢稳定装置5直接替换车厢稳定装置实现。
[0046]
主平台1与车厢6之间设置有摄像头3,摄像头3朝向移动平台2与车厢6后门用于识别两者是否对正。摄像头3采用能够构建深度信息的双目摄像头,如海康威视mv-db1612-05b双目立体相机。
[0047]
控制模块分别与摄像头3、横向调整机构、纵向调整机构、车厢调整装置5、传送机构22和平台驱动装置26通信连接。
[0048]
参照图1-图6,本实用新型实现快速自动对正装车的过程为:
[0049]
货物7码垛在移动平台2顶面的传送机构22上,货车驶入装卸位置即车厢调整装置5的上方;
[0050]
随后摄像头3对车厢6的后门位置进行识别,控制模块根据摄像头3的信息计算出车厢6与移动平台2的高度方向上的差值,并计算出两者的长度方向构成的角度;
[0051]
随后车厢调整装置5的升降底座51升起,车厢托板52托住车厢6的后端并沿车厢宽度方向移动,用于消除车厢6的长度方向与移动平台2的长度方向之间的夹角;
[0052]
随后横向调整机构驱动主平台1沿车厢宽度方向移动联动移动平台2移动,用于消除车厢6的长度方向与移动平台2的长度方向之间的夹角且使两者的中轴线对正;
[0053]
随后纵向调整机构驱动主平台1升降,用于消除车厢6与移动平台2之间的高度差值,完成移动平台2与车厢6的对正;
[0054]
随后移动平台2的滚轮转动使得移动平台2托着所有货物7一起移动进入车厢6内;
[0055]
随后移动平台2一边后退,传送机构22一边传送使货物7沿斜面21滑落在车厢6内,使得移动平台2离开车厢而货物7停留在车厢6内,完成整车快速装货。
[0056]
当然上述实施例只为说明本实用新型的技术构思及特点,其目的在于让熟悉此项
技术的人能够了解本实用新型的内容并据以实施,并不能以此限制本实用新型的保护范围,凡根据本实用新型主要技术方案的精神实质所做的修饰,都应涵盖在本实用新型的保护范围之内。