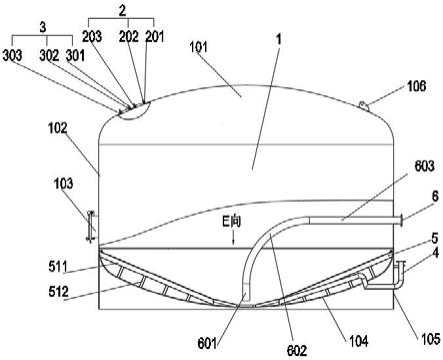
1.本发明涉及散料罐技术领域,具体地涉及一种运输船用散料罐。
背景技术:2.海上船用散料罐,可为钻井平台运输散料,也可为民用运输大量水泥等。中国专利cn205634186u公开了一种散料输送系统及其流化床,其中,输送系统,包括一散料罐、一流化床、一排料管、一进气装置及一空气压缩机,该流化床包括一设于该散料罐底部的支撑架、设于该支撑架上的一气流均衡装置,该支撑架上沿该散料罐的中心轴环形阵列若干进风区,该支撑架下设有一安装座,该安装座对应该支撑架的进风区开设若干通风区,该气流均衡装置包括正对该支撑架的进风区铺设于该支撑架上的若干塔板及铺设于对应的塔板上的若干气流均衡片,每一塔板开设有贯通对应的进风区的若干通风孔,该进气装置包括连接于该空气压缩机与该支撑架对应的进风区之间的若干进风管。而常规的船用散料罐,剩灰率高,流化装置仍存在设计不合理的问题。
技术实现要素:3.本发明的目的在于克服现有技术存在的缺点,提出设计一种流化更加均匀、剩灰率低的运输船用散料罐。
4.本发明解决其技术问题所采取的技术方案是:一种运输船用散料罐,包括罐体、位于罐体内底部的流化系统和与流化系统连通的进气管汇;所述流化系统通过气室立板分割为相互独立的流化室,所述流化室包括环形布置的相互独立的第一类流化室和位于第一类流化室中心的第二类流化室;所述进气管汇包括分别与每个流化室连通的进气管。流化装置与进气管汇的配合设计,使各进气管分别通到各独立的流化室中,可为每个流化室单独供气,可以在单位时间内加大供气量,减少罐体流化和输送时间;还能够根据罐体流化情况,多种组合的选择流化面积,使流化更加均匀,有效减少剩灰率;另一方面,能够防止流化装置出现问题时,必须全部停止操作的弊病,同时,第二类流化室位于第一类流化室中心,起到底封的作用。
5.进一步的,所述气室立板上设置用于贯穿进气管的进气管通孔。
6.进一步的,相邻所述第一类流化室之间通过直立板间隔开,第一类流化室与第二类流化室通过环形立板间隔开;所述第一类流化室上部环形布置覆盖有第一类多孔板,第二类流化室上部覆盖有第二类多孔板;环形立板和直立板与上部的第一类多孔板联合形成独立密封的第一类流化室,环形立板与上部的第二类多孔板联合形成第二类流化室。
7.进一步的,所述第一类多孔板和第二类多孔板上均开设透气孔。
8.进一步的,所述流化室下部通过工字钢作为骨架,工字钢下部通过支撑管安装在罐体内侧底部。
9.进一步的,所述罐体包括上封头、筒体和下封头;所述上封头和下封头均采用凸形封头,可为椭圆封头、碟形封头,优选为浅碟形封头,同样高度下罐体容积大,能够降低罐的
重心高度,提高了在海上运输的安全系数。
10.进一步的,所述第一类多孔板和第二类多孔板上方为气化层,所述气化层通过螺栓与第一类多孔板、第二类多孔板连接且连接处设置有橡胶密封条。
11.进一步的,所述环形立板包括第五立板e和第六立板f,所述第六立板f内嵌于第五立板e内侧,第五立板e、第六立板f与上部的第二类多孔板联合形成第二类流化室。所述第六立板f起到加固流化装置的作用。
12.进一步的,所述第六立板f下部开设有多个三角形通孔,方便罐内通气。
13.进一步的,所述罐体顶部设置均采用嵌入式法兰型的进料管汇和排空管汇。进料管汇和排空管汇采用嵌入式法兰型式,相对于常规的接管和法兰式设计,一方面方便与外部输送系统的连接,方向和高度都不受限制,另一方面,在船舱内,可降低罐体的高度,结构简单。
14.进一步的,所述罐体顶部设置排空口和进料口;所述排空口包括第一螺纹盲孔、第一全螺纹螺栓和排空法兰;所述排空法兰嵌入第一螺纹盲孔中;所述进料口包括第二全螺纹螺栓、第二螺纹盲孔和进料法兰,所述进料法兰嵌入第二螺纹盲孔中,实现所述进料管汇和排空管汇的嵌入式法兰型式连接。
15.本发明的技术效果:与现有技术相比,本发明的一种运输船用散料罐,将第一类多孔板环形布置覆盖在流化室的上部,下部采用工字钢作为骨架,工字钢下部采用钢管作为支撑管,然后通过立板和一块环形立板加上上部的第一类多孔板形成若干个独立密封的气室,位于中心的气室是环形立板环绕与上部的第二类多孔板联合形成,起到底封的作用;若干进气管分别通到若干个独立的流化室中,可为各流化室单独供气;流化装置与进气管汇的配合设计,能够使每个流化室单独供气,可以在单位时间内加大供气量,减少罐体流化和输送时间;还能够多种组合的选择流化面积,使流化更加均匀,减少剩灰率;能够防止流化装置出现问题时,必须全部停止操作的弊病。另外,进料管汇和排空管汇采用嵌入式法兰型式,相对于常规的接管和法兰式设计,一方面方便与外部输送系统的连接,方向和高度都不受限制,另一方面,在船舱内,可降低罐体的高度,结构简单。
附图说明
16.图1为本发明主体结构示意图;图2为本发明图1的e向视图;图3为本发明的第一类多孔板结构示意图;图4为本发明的第二类多孔板结构示意图;图5为本发明的立板结构示意图;图6为本发明图2 的a
‑
a剖视图;图7为本发明图2 的b
‑
b剖视图;图8为本发明图2 的c
‑
c剖视图;图9为本发明图2 的d
‑
d剖视图;图10为本发明的第六立板展开图。
17.图中,罐体1、排空口2、进料口3、进气管汇4、流化系统5、出料管汇6、第一类流化室
7、第二类流化室8;上封头101、筒体102、检修人孔103、下封头104、裙座105、吊耳106;第一螺纹盲孔201、第一全螺纹螺栓202、排空法兰203;第二全螺纹螺栓301、第二螺纹盲孔302、进料法兰303;第一进气管401、 第二进气管402、第三进气管403、第四进气管404、第五进气管405;第一室内进气管口401a、第二室内进气管口402a、第三室内进气管口403a、第四室内进气管口404a、第五室内进气管口405a;第一类多孔板501、第二类多孔板502、气室立板503、进气管通孔504、塞焊用工艺孔505、透气孔506、螺栓507、螺母508、压条509、气化层510、密封条511、工字钢512、支撑管513、三角形通孔514;第一立板503a、第二立板503b、第三立板503c、第四立板503d、第五立板503e、第六立板503f;第一直管601、弯管602、第二直管603。
具体实施方式
18.为使本发明实施例的目的、技术方案和优点更加清楚,下面结合说明书附图,对本发明实施例中的技术方案进行清楚、完整地描述。
19.实施例1:如图1所示,本实施例涉及的一种运输船用散料罐,包括罐体1、位于罐体1内底部的流化系统5和与流化系统5连通的进气管汇4。
20.如图1所示,所述罐体1包括上封头101、筒体102和下封头104;所述上封头101和下封头104均采用浅碟形封头;罐体1底部设置出料管汇6,所述出料管汇6包括依次连接的第一直管601、第二直管603和大直径弯管弯管602。
21.如图1、图2和图7所示,所述流化系统5通过气室立板503分割为五个相互独立的流化室;所述流化室下部通过工字钢512作为骨架,工字钢512下部通过支撑管513安装在下封头104上,所述支撑管513采用钢管。所述流化室包括环形布置的四个相互独立的第一类流化室7和位于四个第一类流化室7中心的第二类流化室8。
22.如图2所示,所述进气管汇4包括五个进气管,五个进气管通过相应的通孔504分别与每个流化室连通,所述气室立板503上设置用于贯穿进气管的通孔504。流化装置与进气管汇的配合设计,使各进气管分别通到各独立的流化室中,可为每个流化室单独供气,可以在单位时间内加大供气量,减少罐体流化和输送时间;还能够根据罐体流化情况,多种组合的选择流化面积,如从四个第一类流化室7中选择其中一个第一类流化室7与第二类流化室8组合,或四个第一类流化室7中选择其中两个第一类流化室7与第二类流化室8组合,或选择其中两个或三个第一类流化室7等,实现多种组合的选择流化面积,能够防止流化装置出现问题时,必须全部停止操作的弊病,流化更加均匀,减少剩灰率,同时,第二类流化室8位于四个第一类流化室7中心,起到底封的作用。
23.如图2所示,相邻所述第一类流化室7之间通过直立板间隔开,所述直立板包括第一立板503a、第二立板503b、第三立板503c、第四立板503d;第一立板503a与第二立板503b
之间为第一个第一类流化室7,第二立板503b与第三立板503c之间为第二个第一类流化室7,第三立板503c与第四立板503d之间为第三个第一类流化室7,第四立板503d与第一立板503a之间为第四个第一类流化室7。
24.第一类流化室7与第二类流化室8通过环形立板间隔开;所述环形立板包括第五立板503e和第六立板503f,所述第六立板503f内嵌于第五立板503e内侧。
25.所述第一类流化室7上部环形布置覆盖有第一类多孔板501,第二类流化室8上部覆盖有第二类多孔板502,所述第一类多孔板501和第二类多孔板502上均开设透气孔506;环形立板和直立板与上部的第一类多孔板501联合形成四个独立密封的第一类流化室7;环形立板与上部的第二类多孔板502联合形成第二类流化室8,即第五立板503e、第六立板503f与上部的第二类多孔板502联合形成第二类流化室8。
26.如图10所示,所述第六立板503f下部开设有多个三角形通孔514,方便罐内通气;所述第六立板503f起到加固流化装置的作用。
27.如图2所示,所述进气管汇4包括第一进气管401、第二进气管402、第三进气管403、第四进气管404、第五进气管405;所述第一进气管401的第一室内进气管口401a与第一个第一类流化室7连通,第二进气管402的第二室内进气管口402a与第四个第一类流化室7连通,第四进气管404的第四室内进气管口404a与第三个第一类流化室7连通,第五进气管405的第五室内进气管口405a与第二个第一类流化室7连通,所述第三进气管403的第三室内进气管口403a与第二类流化室8连通。
28.所述第一类多孔板501、第二类多孔板502与相应气室立板503焊接。具体的,所述第一类多孔板501、第二类多孔板502上开设有塞焊用工艺孔505,优选的,所述塞焊用工艺孔505为椭圆形,多孔板沿工字钢512部分设有均布的椭圆形塞焊用工艺孔505,该种工艺方便多孔板与工字钢512进行塞焊固定;多孔板搭接在气室立板503顶部的两边,需要进行连续焊接,实现密封;气室立板503下部和端部与下封头104也需要进行连续焊接,目的是使气室不漏气。
29.所述第一类多孔板501和第二类多孔板502上方为气化层510,所述气化层510通过螺栓507与第一类多孔板501、第二类多孔板502连接且连接处设置有橡胶密封条511。气化层510采用流化布,流化布采用螺栓507固定。多孔板上的螺栓507采用螺栓焊机分别焊到多孔板上,安装时,流化布下部先加橡胶密封条511,再加流化布;流化布接头处,流化布需要重叠压住流化布接头,上面用扁钢压条509,然后再用螺母508进行固定,工作效率快,定位尺寸精度高。
30.所述上封头101上设置吊耳106,所述罐体1上设置检修人孔103,所述下封头104位于裙座105上。
31.所述罐体1顶部设置采用嵌入式法兰型的进料管汇和排空管汇。具体的,所述上封头101设置排空口2和进料口3;所述排空口2包括第一螺纹盲孔201、第一全螺纹螺栓202和排空法兰203;所述排空法兰203嵌入第一螺纹盲孔201中;所述进料口3包括第二全螺纹螺栓301、第二螺纹盲孔302和进料法兰303,所述进料法兰303嵌入第二螺纹盲孔302中。进料管汇和排空管汇采用嵌入式法兰型式,相对于常规的接管和法兰式设计,一方面方便与外部输送系统的连接,方向和高度都不受限制,另一方面,在船舱内,可降低罐体的高度,结构简单。
32.本发明将第一类多孔板环形布置覆盖在流化室的上部,下部采用若干工字钢作为骨架,工字钢下部采用钢管作为支撑管,然后通过四块立板和一块环形立板加上上部的第一类多孔板形成四个独立密封的气室,位于中心的气室是环形立板环绕与上部的第二类多孔板联合形成,起到底封的作用;五个进气管分别通到五个独立的流化室中,可为各流化室单独供气;流化装置与进气管汇的配合设计,能够使每个流化室单独供气,可以在单位时间内加大供气量,减少罐体流化和输送时间;还能够多种组合的选择流化面积,使流化更加均匀,减少剩灰率;能够防止流化装置出现问题时,必须全部停止操作的弊病。
33.上述具体实施方式仅是本发明的具体个案,本发明的专利保护范围包括但不限于上述具体实施方式的产品形态和式样,任何符合本发明权利要求书且任何所属技术领域的普通技术人员对其所做的适当变化或修饰,皆应落入本发明的专利保护范围。