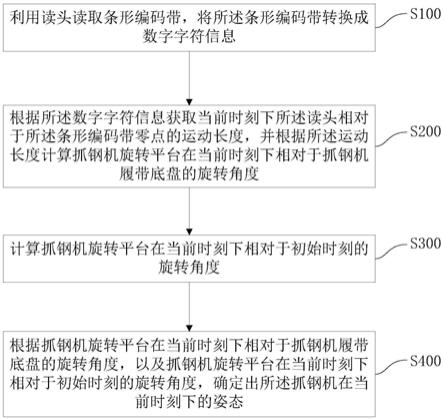
1.本发明涉及钢铁处理技术领域,特别是涉及一种抓钢机姿态确定方法及系统。
背景技术:2.在钢铁厂废钢作业过程中,抓钢机通常用于对废钢等材料进行抓取和装载等工作,由于现有的抓钢机自动化程度较低,工作效率较低,容易产生安全隐患。所以,本技术为了提高抓钢机的自动化程度,需要对现有的抓钢机进行改造,使其能够进行自动化或无人化抓取作业。
3.如果要实现抓钢机的自动化或无人化作业,就必须先知道抓钢机在正常非自动化作业时的位置和姿态,然后根据对应的位置和姿态来控制抓钢机进行自动化作业。对于抓钢机的位置而言,目前可以采用gps(global positioning system,全球定位系统,以下简称gps)来进行定位。但是,对于抓钢机的姿态而言,由于抓钢机在作业时,抓钢机履带底盘和旋转平台会产生旋转运动,例如旋转平台或履带底盘会旋转若干圈;而使用角度传感器测量角度时,角度传感器一般是安装在履带底盘上,电源和工控机都是固定在旋转平台上的,如果要对角度传感器进行供电和传输数据,就必然有电线要从旋转平台连接到履带底盘,但是旋转平台和履带底盘有相对旋转运动,而且可以无限旋转,导致传统方式使用角度传感器测量旋转平台和履带底盘的相对选择角度时,无法解决供电和数据传输的问题。此外,由于抓钢机主要是由钢铁构成,其会影响地磁场,进而影响角度传感器的精度。同时,由于抓钢机在设计制造时没有考虑后续的自动化改造,所以无法在其中央回转接头上安装旋转编码器来测量旋转角度,导致无法准确测量抓钢机的姿态。
技术实现要素:4.鉴于以上所述现有技术的缺点,本发明的目的在于提供一种抓钢机姿态确定方法及系统,用于解决现有技术对抓钢机进行自动化改造时,无法确定抓钢机姿态的问题。
5.为实现上述目的及其他相关目的,本发明提供一种抓钢机姿态确定方法,包括以下步骤:
6.利用读头读取条形编码带,将所述条形编码带转换成数字字符信息;
7.根据所述数字字符信息获取当前时刻下所述读头相对于条形编码带零点的运动长度,并根据所述运动长度计算抓钢机旋转平台在当前时刻下相对于抓钢机履带底盘的旋转角度;
8.计算抓钢机旋转平台在当前时刻下相对于初始时刻的旋转角度;
9.根据抓钢机旋转平台在当前时刻下相对于抓钢机履带底盘的旋转角度,以及抓钢机旋转平台在当前时刻下相对于初始时刻的旋转角度,确定出所述抓钢机在当前时刻下的姿态。
10.可选地,还包括:根据抓钢机旋转平台在当前时刻下相对于抓钢机履带底盘的旋转角度,以及抓钢机旋转平台在当前时刻下相对于初始时刻的旋转角度,计算抓钢机履带
底盘在当前时刻下相对于初始时刻的旋转角度;
11.根据抓钢机旋转平台在当前时刻下相对于抓钢机履带底盘的旋转角度,以及抓钢机履带底盘在当前时刻下相对于初始时刻的旋转角度确定出所述抓钢机在当前时刻下的姿态。
12.可选地,根据所述运动长度计算抓钢机旋转平台在当前时刻下相对于抓钢机履带底盘的旋转角度的公式包括:
[0013][0014]
式中,α为抓钢机旋转平台在当前时刻下相对于抓钢机履带底盘的旋转角度;
[0015]
l为当前时刻下读头相对于所述条形编码带零点的运动长度;
[0016]
r为回转支承的半径。
[0017]
可选地,计算抓钢机旋转平台在当前时刻下相对于初始时刻的旋转角度的公式包括:
[0018][0019]
式中,t为惯性传感器的采样步长时间;
[0020]
θ
′n为第n个时刻采样时惯性传感器在参考坐标系上的角速度;
[0021]
θ0为初始时刻下所述抓钢机旋转平台在所述参考坐标系下的夹角;
[0022]
θ为当前时刻下抓钢机旋转平台相对于初始时刻的旋转角度;
[0023]
n=1,2,
…
,k,k为自然数。
[0024]
可选地,根据抓钢机旋转平台在当前时刻下相对于抓钢机履带底盘的旋转角度,以及抓钢机旋转平台在当前时刻下相对于初始时刻的旋转角度,计算抓钢机履带底盘在当前时刻下相对于初始时刻的旋转角度的过程包括:
[0025]
β=θ-α;
[0026]
式中,θ为抓钢机旋转平台在当前时刻下相对于初始时刻的旋转角度;
[0027]
α为抓钢机旋转平台在当前时刻下相对于抓钢机履带底盘的旋转角度;
[0028]
β为抓钢机履带底盘在当前时刻下相对于初始时刻的旋转角度。
[0029]
可选地,在利用读头读取条形编码带前,还包括对所述条形编码带进行预处理;
[0030]
所述预处理包括:对所述条形编码带进行擦拭、标定所述条形编码带的零点。
[0031]
本发明还提供一种抓钢机姿态确定系统,包括有:
[0032]
数据采集模块,用于利用读头读取条形编码带,将所述条形编码带转换成数字字符信息;
[0033]
第一旋转角度计算模块,用于根据所述数字字符信息获取当前时刻下所述读头相对于所述条形编码带零点的运动长度,并根据所述运动长度计算抓钢机旋转平台在当前时刻下相对于抓钢机履带底盘的旋转角度;
[0034]
第二旋转角度计算模块,用于计算抓钢机旋转平台在当前时刻下相对于初始时刻的旋转角度;
[0035]
姿态确定模块,用于根据抓钢机旋转平台在当前时刻下相对于抓钢机履带底盘的旋转角度,以及抓钢机旋转平台在当前时刻下相对于初始时刻的旋转角度,确定出抓钢机在当前时刻下的姿态。
[0036]
可选地,所述系统还包括:第三旋转角度计算模块,用于根据抓钢机旋转平台在当前时刻下相对于抓钢机履带底盘的旋转角度,以及抓钢机旋转平台在当前时刻下相对于初始时刻的旋转角度,计算抓钢机履带底盘在当前时刻下相对于初始时刻的旋转角度。
[0037]
可选地,所述系统还包括有通信模块,所述通信模块分别与所述数据采集模块、第一旋转角度计算模块、第二旋转角度计算模块、第三旋转角度计算模块和姿态确定模块连接,所述通信模块用于实现通信连接。
[0038]
可选地,所述系统还包括有对电源模块,所述电源模块分别与所述数据采集模块、第一旋转角度计算模块、第二旋转角度计算模块、第三旋转角度计算模块和姿态确定模块连接,用于提供电源。
[0039]
如上所述,本发明提供一种抓钢机姿态确定方法及系统,具有以下有益效果:
[0040]
通过预先固定安装在回转支承上部的读头读取条形编码带,并将条形编码带上的白条和黑条转换成对应的模拟电信号;其中,条形编码带预先固定安装在回转支承下部,且条形编码带的安装位置与读头正对;将模拟电信号转化成数字电信号,并利用译码接口电路将数字电信号译成数字字符信息;根据数字字符信息获取当前时刻下抓钢机相对于条形编码带零点的运动长度,并根据运动长度和回转支承的半径,计算抓钢机旋转平台在当前时刻下相对于抓钢机履带底盘的旋转角度;利用惯性测量装置计算抓钢机旋转平台在当前时刻下相对于初始时刻的旋转角度;根据抓钢机旋转平台在当前时刻下相对于抓钢机履带底盘的旋转角度,以及抓钢机旋转平台在当前时刻下相对于初始时刻的旋转角度,计算抓钢机履带底盘在当前时刻下相对于初始时刻的旋转角度;根据抓钢机旋转平台在当前时刻下相对于抓钢机履带底盘的旋转角度,以及抓钢机履带底盘在当前时刻下相对于初始时刻的旋转角度确定抓钢机在当前时刻下的姿态。本发明针对抓钢机工作时的特点,提出了基于识别条形编码带的方式,通过计算出抓钢机履带底盘和旋转平台的相对旋转角度,然后再结合旋转平台上的惯性测量装置(inertial measurement unit,简称imu),从而可以得到抓钢机运动时的姿态。同时,再根据所得到的姿态对抓钢机进行自动化改造,从而可以帮助抓钢机实现无人化或自动化作业。本发明不仅可以改造现有设备,无需新购抓钢机;而且可以方便对传感器供电、传输数据,不干涉抓钢机的旋转运动;同时还可以降低设备环境对传感器精度的影响,提高姿态定位的精度;同时抓钢机实现无人化作业,降低了人工操作区域内扬尘造成的职业健康伤害。此外,还能对堆场内废钢堆存的精确跟踪,有助于实现废钢智能化管理;所以,本发明不仅能够减少设备成本和人力成本,还可以增加了地面运控管理的效率。
附图说明
[0041]
图1为一实施例提供的抓钢机姿态确定方法的流程示意图;
[0042]
图2为一实施例提供的抓钢机姿态确定系统的硬件结构示意图。
具体实施方式
[0043]
以下通过特定的具体实例说明本发明的实施方式,本领域技术人员可由本说明书所揭露的内容轻易地了解本发明的其他优点与功效。本发明还可以通过另外不同的具体实施方式加以实施或应用,本说明书中的各项细节也可以基于不同观点与应用,在没有背离
本发明的精神下进行各种修饰或改变。需说明的是,在不冲突的情况下,以下实施例及实施例中的特征可以相互组合。
[0044]
需要说明的是,本实施例中所提供的图示仅以示意方式说明本发明的基本构想,遂图式中仅显示与本发明中有关的组件而非按照实际实施时的组件数目、形状及尺寸绘制,其实际实施时各组件的型态、数量及比例可为一种随意的改变,且其组件布局型态也可能更为复杂。
[0045]
请参阅图1,本实施例提供一种抓钢机姿态确定方法,包括以下步骤:
[0046]
s100,利用读头读取条形编码带,将所述条形编码带转换成数字字符信息。作为示例,例如可以利用预先固定安装在回转支承上部的读头读取条形编码带,将所述条形编码带上的白条和黑条转换成对应的模拟电信号;然后通过模拟数字转换器将模拟电信号转化成2进制数字电信号,并利用译码接口电路将所述2进制数字电信号译成10进制数字字符信息。其中,所述条形编码带预先固定安装在回转支承下部,且所述条形编码带的安装位置与所述读头正对。作为示例,本实施例根据条形编码带上的白条和黑条,以及白条宽度、黑条宽度来转换形成对应的模拟电信号。
[0047]
s200,根据所述数字字符信息获取当前时刻下所述读头相对于所述条形编码带零点的运动长度,并根据所述运动长度计算抓钢机旋转平台在当前时刻下相对于抓钢机履带底盘的旋转角度。作为示例,例如可以根据数字字符信息获取当前状态下编码带读头正对着的编码带位置,由于编码带每一节都有起始符、数据符、分隔符、校验符、终止符构成的标记信号,因此可以根据编码带的位置信息,得到读头抓钢机相对于所述条形编码带零点的运动长度,由于读头是固定安装在回转支承上的,因此读头回转运动的长度,即为回转支承旋转时扫过的长度。
[0048]
s300,计算抓钢机旋转平台在当前时刻下相对于初始时刻的旋转角度。
[0049]
s400,根据抓钢机旋转平台在当前时刻下相对于抓钢机履带底盘的旋转角度,以及抓钢机旋转平台在当前时刻下相对于初始时刻的旋转角度,确定出所述抓钢机在当前时刻下的姿态。
[0050]
本方法针对抓钢机工作时的特点,提出了基于识别条形编码带的方式,通过计算出抓钢机履带底盘和旋转平台的相对旋转角度,然后再结合旋转平台上的惯性测量装置imu,从而可以得到抓钢机运动时的姿态。同时,再根据所得到的姿态对抓钢机进行自动化改造,从而可以帮助抓钢机实现无人化或自动化作业。本方法不仅可以改造现有设备,无需新购抓钢机;而且可以方便对传感器供电、传输数据,不干涉抓钢机的旋转运动;同时还可以降低设备环境对传感器精度的影响,提高姿态定位的精度;同时抓钢机实现无人化作业,降低了人工操作区域内扬尘造成的职业健康伤害。此外,还能对堆场内废钢堆存的精确跟踪,有助于实现废钢智能化管理;所以,本方法不仅能够减少设备成本和人力成本,还可以增加了地面运控管理的效率。
[0051]
根据上述记载,在一示例性实施例中,还包括:根据抓钢机旋转平台在当前时刻下相对于抓钢机履带底盘的旋转角度,以及抓钢机旋转平台在当前时刻下相对于初始时刻的旋转角度,计算抓钢机履带底盘在当前时刻下相对于初始时刻的旋转角度;根据抓钢机旋转平台在当前时刻下相对于抓钢机履带底盘的旋转角度,以及抓钢机履带底盘在当前时刻下相对于初始时刻的旋转角度确定出所述抓钢机在当前时刻下的姿态。
[0052]
在一示例性实施例中,根据所述运动长度计算抓钢机旋转平台在当前时刻下相对于抓钢机履带底盘的旋转角度的公式包括:
[0053][0054]
式中,α为抓钢机旋转平台在当前时刻下相对于抓钢机履带底盘的旋转角度;l为当前时刻下读头相对于所述条形编码带零点的运动长度;r为回转支承的半径。
[0055]
在一示例性实施例中,计算抓钢机旋转平台在当前时刻下相对于初始时刻的旋转角度的公式包括:
[0056][0057]
式中,t为惯性传感器的采样步长时间;其中,惯性传感器位于惯性测量装置imu中。θ
′n为第n个时刻采样时惯性传感器在参考坐标系上的角速度;θ0为初始时刻下所述抓钢机旋转平台在所述参考坐标系下的夹角;θ为当前时刻下抓钢机旋转平台相对于初始时刻的旋转角度;n=1,2,
…
,k,k为自然数。在本实施例中,惯性传感器可能不会一直提供稳定准确的数据,因此本实施例还包括采用卡尔曼滤波算法得到对应的修正值。
[0058]
在一示例性实施例中,根据抓钢机旋转平台在当前时刻下相对于抓钢机履带底盘的旋转角度,以及抓钢机旋转平台在当前时刻下相对于初始时刻的旋转角度,计算抓钢机履带底盘在当前时刻下相对于初始时刻的旋转角度的过程包括:
[0059]
β=θ-α;
[0060]
式中,θ为抓钢机旋转平台在当前时刻下相对于初始时刻的旋转角度;α为抓钢机旋转平台在当前时刻下相对于抓钢机履带底盘的旋转角度;β为抓钢机履带底盘在当前时刻下相对于初始时刻的旋转角度。由此可知,本实施例通过融合惯性测量装置imu的角度信息和条形编码带的角度信息,可以计算出履带底盘相对于初始地面位置的旋转角度。
[0061]
根据上述记载,在一示例性实施例中,在利用读头读取条形编码带前,还包括对所述条形编码带进行预处理;所述预处理包括:对所述条形编码带进行擦拭、标定所述条形编码带的零点。其中,擦拭过程:安装编码带读头时,附带在读头后面安装了一个柔性雨刷,运动转台一周,即可完成编码带的擦拭。标定过程:运动转台到抓钢机出厂时的初始位置,记录此时编码带读头正对着的编码带位置,即为编码带的零点。
[0062]
综上所述,本方法通过预先固定安装在回转支承上部的读头读取条形编码带,并将条形编码带上的白条和黑条转换成对应的模拟电信号;其中,条形编码带预先固定安装在回转支承下部,且条形编码带的安装位置与读头正对;将模拟电信号转化成数字电信号,并利用译码接口电路将数字电信号译成数字字符信息;根据数字字符信息获取当前时刻下抓钢机相对于条形编码带零点的运动长度,并根据运动长度和回转支承的半径,计算抓钢机旋转平台在当前时刻下相对于抓钢机履带底盘的旋转角度;利用惯性测量装置计算抓钢机旋转平台在当前时刻下相对于初始时刻的旋转角度;根据抓钢机旋转平台在当前时刻下相对于抓钢机履带底盘的旋转角度,以及抓钢机旋转平台在当前时刻下相对于初始时刻的旋转角度,计算抓钢机履带底盘在当前时刻下相对于初始时刻的旋转角度;根据抓钢机旋转平台在当前时刻下相对于抓钢机履带底盘的旋转角度,以及抓钢机履带底盘在当前时刻下相对于初始时刻的旋转角度确定抓钢机在当前时刻下的姿态。本方法针对抓钢机工作时的特点,提出了基于识别条形编码带的方式,通过计算出抓钢机履带底盘和旋转平台的相
对旋转角度,然后再结合旋转平台上的惯性测量装置imu中,从而可以得到抓钢机运动时的姿态。同时,再根据所得到的姿态对抓钢机进行自动化改造,从而可以帮助抓钢机实现无人化或自动化作业。本方法不仅可以改造现有设备,无需新购抓钢机;而且可以方便对传感器供电、传输数据,不干涉抓钢机的旋转运动;同时还可以降低设备环境对传感器精度的影响,提高姿态定位的精度;同时抓钢机实现无人化作业,降低了人工操作区域内扬尘造成的职业健康伤害。此外,还能对堆场内废钢堆存的精确跟踪,有助于实现废钢智能化管理;所以,本方法不仅能够减少设备成本和人力成本,还可以增加了地面运控管理的效率。
[0063]
如图2所示,本发明还提供了一种抓钢机姿态确定系统,包括有:
[0064]
数据采集模块m10,用于利用读头读取条形编码带,将所述条形编码带转换成数字字符信息。例如可以利用预先固定安装在回转支承上部的读头读取条形编码带,将所述条形编码带上的白条和黑条转换成对应的模拟电信号;然后通过模拟数字转换器将模拟电信号转化成2进制数字电信号,并利用译码接口电路将所述2进制数字电信号译成10进制数字字符信息。其中,所述条形编码带预先固定安装在回转支承下部,且所述条形编码带的安装位置与所述读头正对。作为示例,本实施例根据条形编码带上的白条和黑条,以及白条宽度、黑条宽度来转换形成对应的模拟电信号。
[0065]
第一旋转角度计算模块m20,用于根据所述数字字符信息获取当前时刻下所述读头相对于所述条形编码带零点的运动长度,并根据所述运动长度计算抓钢机旋转平台在当前时刻下相对于抓钢机履带底盘的旋转角度;
[0066]
第二旋转角度计算模块m30,用于计算抓钢机旋转平台在当前时刻下相对于初始时刻的旋转角度;
[0067]
姿态确定模块m40,用于根据抓钢机旋转平台在当前时刻下相对于抓钢机履带底盘的旋转角度,以及抓钢机旋转平台在当前时刻下相对于初始时刻的旋转角度,确定出抓钢机在当前时刻下的姿态。
[0068]
本系统针对抓钢机工作时的特点,提出了基于识别条形编码带的方式,通过计算出抓钢机履带底盘和旋转平台的相对旋转角度,然后再结合旋转平台上的惯性测量装置imu,从而可以得到抓钢机运动时的姿态。同时,再根据所得到的姿态对抓钢机进行自动化改造,从而可以帮助抓钢机实现无人化或自动化作业。本系统不仅可以改造现有设备,无需新购抓钢机;而且可以方便对传感器供电、传输数据,不干涉抓钢机的旋转运动;同时还可以降低设备环境对传感器精度的影响,提高姿态定位的精度;同时抓钢机实现无人化作业,降低了人工操作区域内扬尘造成的职业健康伤害。此外,还能对堆场内废钢堆存的精确跟踪,有助于实现废钢智能化管理;所以,本系统不仅能够减少设备成本和人力成本,还可以增加了地面运控管理的效率。
[0069]
根据上述记载,在一示例性实施例中,所述系统还包括:第三旋转角度计算模块m50,用于根据抓钢机旋转平台在当前时刻下相对于抓钢机履带底盘的旋转角度,以及抓钢机旋转平台在当前时刻下相对于初始时刻的旋转角度,计算抓钢机履带底盘在当前时刻下相对于初始时刻的旋转角度;且姿态确定模块m40还可以用于根据抓钢机旋转平台在当前时刻下相对于抓钢机履带底盘的旋转角度,以及抓钢机旋转平台在当前时刻下相对于初始时刻的旋转角度,确定出抓钢机在当前时刻下的姿态。
[0070]
根据上述记载,所述系统还包括有通信模块m60和电源模块m70,所述通信模块m60
分别与所述数据采集模块m10、第一旋转角度计算模块m20、第二旋转角度计算模块m30、第三旋转角度计算模块m50和姿态确定模块m40连接,所述通信模块用于实现通信连接。所述电源模块m70分别与所述数据采集模块m10、第一旋转角度计算模块m20、第二旋转角度计算模块m30、第三旋转角度计算模块m50和姿态确定模块m40连接,用于提供电源。
[0071]
根据上述记载,在一示例性实施例中,还包括:根据抓钢机旋转平台在当前时刻下相对于抓钢机履带底盘的旋转角度,以及抓钢机旋转平台在当前时刻下相对于初始时刻的旋转角度,计算抓钢机履带底盘在当前时刻下相对于初始时刻的旋转角度;根据抓钢机旋转平台在当前时刻下相对于抓钢机履带底盘的旋转角度,以及抓钢机履带底盘在当前时刻下相对于初始时刻的旋转角度确定出所述抓钢机在当前时刻下的姿态。
[0072]
在一示例性实施例中,根据所述运动长度计算抓钢机旋转平台在当前时刻下相对于抓钢机履带底盘的旋转角度的公式包括:
[0073][0074]
式中,α为抓钢机旋转平台在当前时刻下相对于抓钢机履带底盘的旋转角度;l为当前时刻下读头相对于所述条形编码带零点的运动长度;r为回转支承的半径。
[0075]
在一示例性实施例中,计算抓钢机旋转平台在当前时刻下相对于初始时刻的旋转角度的公式包括:
[0076][0077]
式中,t为惯性传感器的采样步长时间;其中,惯性传感器位于惯性测量装置imu中。θ
′n为第n个时刻采样时惯性传感器在参考坐标系上的角速度;θ0为初始时刻下所述抓钢机旋转平台在所述参考坐标系下的夹角;θ为当前时刻下抓钢机旋转平台相对于初始时刻的旋转角度;n=1,2,
…
,k,k为自然数。在本实施例中,惯性传感器可能不会一直提供稳定准确的数据,因此本实施例还包括采用卡尔曼滤波算法得到对应的修正值。
[0078]
在一示例性实施例中,根据抓钢机旋转平台在当前时刻下相对于抓钢机履带底盘的旋转角度,以及抓钢机旋转平台在当前时刻下相对于初始时刻的旋转角度,计算抓钢机履带底盘在当前时刻下相对于初始时刻的旋转角度的过程包括:
[0079]
β=θ-α;
[0080]
式中,θ为抓钢机旋转平台在当前时刻下相对于初始时刻的旋转角度;α为抓钢机旋转平台在当前时刻下相对于抓钢机履带底盘的旋转角度;β为抓钢机履带底盘在当前时刻下相对于初始时刻的旋转角度。由此可知,本实施例通过融合惯性测量装置imu的角度信息和条形编码带的角度信息,可以计算出履带底盘相对于初始地面位置的旋转角度。
[0081]
根据上述记载,在一示例性实施例中,在利用读头读取条形编码带前,还包括对所述条形编码带进行预处理;所述预处理包括:对所述条形编码带进行擦拭、标定所述条形编码带的零点。其中,擦拭过程:安装编码带读头时,附带在读头后面安装了一个柔性雨刷,运动转台一周,即可完成编码带的擦拭。标定过程:运动转台到抓钢机出厂时的初始位置,记录此时编码带读头正对着的编码带位置,即为编码带的零点。
[0082]
综上所述,本系统通过预先固定安装在回转支承上部的读头读取条形编码带,并将条形编码带上的白条和黑条转换成对应的模拟电信号;其中,条形编码带预先固定安装在回转支承下部,且条形编码带的安装位置与读头正对;将模拟电信号转化成数字电信号,
并利用译码接口电路将数字电信号译成数字字符信息;根据数字字符信息获取当前时刻下抓钢机相对于条形编码带零点的运动长度,并根据运动长度和回转支承的半径,计算抓钢机旋转平台在当前时刻下相对于抓钢机履带底盘的旋转角度;利用惯性测量装置计算抓钢机旋转平台在当前时刻下相对于初始时刻的旋转角度;根据抓钢机旋转平台在当前时刻下相对于抓钢机履带底盘的旋转角度,以及抓钢机旋转平台在当前时刻下相对于初始时刻的旋转角度,计算抓钢机履带底盘在当前时刻下相对于初始时刻的旋转角度;根据抓钢机旋转平台在当前时刻下相对于抓钢机履带底盘的旋转角度,以及抓钢机履带底盘在当前时刻下相对于初始时刻的旋转角度确定抓钢机在当前时刻下的姿态。本系统针对抓钢机工作时的特点,提出了基于识别条形编码带的方式,通过计算出抓钢机履带底盘和旋转平台的相对旋转角度,然后再结合旋转平台上的惯性测量装置imu中,从而可以得到抓钢机运动时的姿态。同时,再根据所得到的姿态对抓钢机进行自动化改造,从而可以帮助抓钢机实现无人化或自动化作业。本系统不仅可以改造现有设备,无需新购抓钢机;而且可以方便对传感器供电、传输数据,不干涉抓钢机的旋转运动;同时还可以降低设备环境对传感器精度的影响,提高姿态定位的精度;同时抓钢机实现无人化作业,降低了人工操作区域内扬尘造成的职业健康伤害。此外,还能对堆场内废钢堆存的精确跟踪,有助于实现废钢智能化管理;因此,本系统不仅能够减少设备成本和人力成本,还可以增加了地面运控管理的效率。所以,本发明有效克服了现有技术中的种种缺点而具高度产业利用价值。
[0083]
上述实施例仅例示性说明本发明的原理及其功效,而非用于限制本发明。任何熟悉此技术的人士皆可在不违背本发明的精神及范畴下,对上述实施例进行修饰或改变。因此,举凡所属技术领域中具有通常知识者在未脱离本发明所揭示的精神与技术思想下所完成的一切等效修饰或改变,仍应由本发明的权利要求所涵盖。
[0084]
应当理解的是,尽管在本发明实施例中可能采用术语第一、第二、第三等来描述预设范围等,但这些预设范围不应限于这些术语。这些术语仅用来将预设范围彼此区分开。例如,在不脱离本发明实施例范围的情况下,第一预设范围也可以被称为第二预设范围,类似地,第二预设范围也可以被称为第一预设范围。