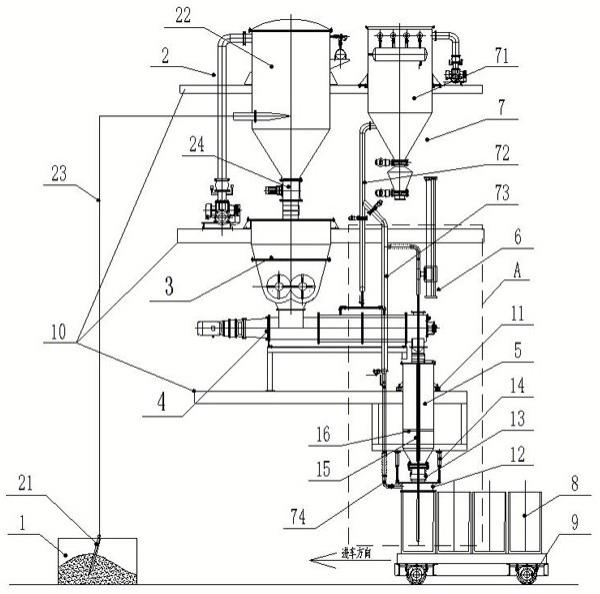
1.本发明涉及一种电池材料石墨化坩埚自动加料填实系统,属于电池材料石墨化技术领域。
背景技术:2.在电池材料石墨化时,需要向坩埚内加入电池材料粉料并填实,现有技术中的操作步骤一般是:首先在称量装置上称量一定重量的粉料,然后人工转运至坩埚加料处,将称量后的粉料加入坩埚内,然后人工借助机械工具对坩埚内的粉料进行压实,以保证尽量多的填装量;上述操作过程主要人工作业,并且压实过程也通常是人工采用机械方式进行,随着社会的不断进步以及人们对产品质量的要求越来越高,人工加料以及压实在实际生产中逐渐暴露出以下弊端:1、操作步骤不连续,并且自动化程度低,生产效率低,工人的劳动强度大。
3.2、上述操作过程,粉料不论在转运、加料以及压实过程中,容易出现粉料泄漏,导致环境污染,同时灰尘会对工人的健康造成损害;3、机械压实效果差,不能满足生产要求,降低产品质量。
4.综上可知,现有技术在实际使用上显然存在不便与缺陷,所以有必要加以改进。
技术实现要素:5.本发明要解决的技术问题是针对以上不足,提供一种电池材料石墨化坩埚自动加料填实系统,可以实现连续化作业,并且实现全程自动化作业,提高工作效率;可以防止粉尘外泄,避免环境污染,提高工作环境安全性;可以提高填料、压实效果。
6.为解决以上技术问题,本发明采用以下技术方案:一种电池材料石墨化坩埚自动加料填实系统,包括沿电池材料粉料输送方向依次连接的气力输送装置、布料装置、螺旋挤压脱气装置、料罐、坩埚;还包括除尘装置,所述除尘装置与螺旋挤压脱气装置、料罐分别连接;所述料罐内设有可上下移动的真空抽气装置,所述真空抽气装置下移可伸入坩埚内,所述真空抽气装置用于对坩埚内粉料进行抽气压实。
7.进一步地,所述螺旋挤压脱气装置水平设置;所述真空抽气装置包括抽气管,所述抽气管为可伸缩管,所述抽气管的伸缩部分滑动贯穿料罐和螺旋挤压脱气装置;所述抽气管的下部设置抽气管段,所述抽气管段管壁上设置有若干个抽气孔,所述抽气孔连通抽气管段内腔;所述抽气孔的直径≤1um;所述抽气管段的长度小于坩埚的内腔高度。
8.进一步地,所述料罐与螺旋挤压脱气装置出料口之间采用软连接方式连接;所述料罐通过称重仪固定在支架的下部。
9.进一步地,所述气力输送装置的进料端与粉料储罐;所述气力输送装置包括吸料管路,所述吸料管路的进料端设置吸料嘴,所述吸料嘴与粉料储罐连接;所述吸料管路的出
料端与气固分离器的进气口连接;所述气固分离器连接真空泵;所述气固分离器为脉冲式布袋除尘器;所述气固分离器的底部设置固料出口。
10.进一步地,所述布料装置包括布料箱,所述布料箱的顶部中心设置进料口;所述布料箱内设置两根平行设置的搅拌轴,所述搅拌轴上布置有左旋叶片和右旋叶片,所述左旋叶片和右旋叶片对称设置在进料口两侧。
11.所述布料箱的底部设有若干个出口,若干个出口沿布料箱长度方向间隔布置;每个出口连接一个螺旋挤压脱气装置。
12.进一步地,所述料罐的底部设置下料口,所述下料口上设置气动插板阀;所述下料口通过伸缩管连接密封对接装置;所述密封对接装置可上下移动,所述密封对接装置的上端与气缸的伸缩杆连接。
13.进一步地,所述密封对接装置包括对接筒,所述对接筒上端与伸缩管连接,所述对接筒的下端设置与坩埚的口部相适配的对接法兰,所述对接法兰上设置密封垫。
14.进一步地,所述除尘装置包括布袋除尘器,所述布袋除尘器与真空泵连接;所述布袋除尘器的进气口连接第一进气管,所述第一进气管的下端与螺旋挤压脱气装置连通;所述第一进气管的中部连接第二进气管,所述第二进气管的下端软连接有连接管,所述连接管与对接筒连接;进一步地,所述料罐内沿轴线设置套管;所述抽气管套设在套管内;所述抽气管通过波纹软管与除尘装置连接;所述抽气管通过升降气缸驱动伸缩。
15.进一步地,所述搅拌轴的两端与布料箱侧壁转动连接;所述搅拌轴的一端穿出布料箱,所述搅拌轴的穿出端设置有齿轮,两个搅拌轴上的齿轮相啮合;两个齿轮设置在齿轮箱内,所述齿轮箱固定在布料箱上;其中一根搅拌轴连接驱动马达,所述驱动马达固定在齿轮箱上;所述坩埚成列设置在轨道运输车上,每列中的坩埚与料罐一一对应。
16.本发明采用以上技术方案后,与现有技术相比,具有以下优点:1、本发明可以通过真空抽气装置在坩埚填料时进行抽气压实,压实效果较机械压实明显提高。
17.2、本发明同时采用真空抽气装置和螺旋挤压脱气装置,螺旋挤压脱气装置对粉料进行挤压脱气,同时可以实现初步加密;真空抽气装置对坩埚内的粉料进行抽气加密,实现最终压实,显著提高了压实效果。
18.3、本发明气力输送装置的设置,可以实现自动上料,降低劳动强度,提高效率,同时避免人工上料对工人造成的健康损害。
19.4、本发明采用可升降的密封对接装置与坩埚密封对接,对接速度快,节约对接时间。
20.4、本发明布料装置的设置可以将粉料比较均匀的分散到多个螺旋挤压脱气装置内,从而较均匀的进入多个料罐内。
21.5、本发明吸尘装置的设置可以对实现自动吸尘,防止粉尘外泄,避免环境污染。
22.6、本发明吸尘装置的布袋除尘器连接第一进气管、第二进气管,第一进气管与螺旋挤压脱气装置,实现抽气脱气以及除尘处理;第二进气管与密封对接装置中的对接筒连接,可以对料罐进行除尘处理。
23.7、本发明可以同时完成多个坩埚的加料填实,生产效率显著提高。
24.下面结合附图和实施例对本发明进行详细说明。
附图说明
25.图1是本发明的结构示意图;图2是布料装置的结构示意图;图3是图2的右视图;图4是图1中a处放大图;图5是图4中b处放大图。
26.图中,1-粉料储罐,2-气力输送装置,21-吸料嘴,22-气固分离器,23-吸料管路,24-固料出口,3-布料装置,31-布料箱,32-搅拌轴,33-齿轮,34-出口,35-驱动马达,36-齿轮箱,37-左旋叶片,38-右旋叶片,39-进料口,4-螺旋挤压脱气装置,5-料罐,51-下料口,52-气动插板阀,6-真空抽气装置,61-抽气管,62-波纹软管,63-升降气缸,64-抽气管段,7-除尘装置,71-布袋除尘器,72-第一进气管,73-第二进气管,74-连接管,8-坩埚,9-轨道运输车,10-支架,11-称重仪,12-密封对接装置,121-对接筒,122-对接法兰,123-密封垫,13-伸缩管,14-气缸,15-套管,16-支撑杆。
具体实施方式
27.为了对本发明的技术特征、目的和效果有更加清楚的理解,现对照附图说明本发明的具体实施方式。
28.实施例1如图1-5共同所示,本发明提供一种电池材料石墨化坩埚自动加料填实系统,包括沿电池材料输送方向依次连接的气力输送装置2、布料装置3、螺旋挤压脱气装置4、料罐5、坩埚8;所述料罐5内设有可上下移动的真空抽气装置6,所述真空抽气装置6下移可伸入坩埚8内,用于抽吸坩埚8内粉料中的空气,具有压实粉料的作用,抽真空压实效果较现有的机械方式压实效果好。
29.所述电池材料石墨化坩埚自动加料填实系统还包括除尘装置7,所述除尘装置7与螺旋挤压脱气装置4、料罐5分别连接,避免粉料泄漏,防止环境污染。
30.所述气力输送装置2的进料端与粉料储罐1;所述气力输送装置2包括吸料管路23,所述吸料管路23的进料端设置吸料嘴21,所述吸料嘴21与粉料储罐1连接;所述吸料管路23的出料端与气固分离器22的进气口连接,所述气固分离器22固定在支架10的上部;所述气固分离器22连接真空泵,所述气固分离器22为脉冲式布袋除尘器;所述气固分离器22的底部设置固料出口24,所述固料出口24上设置卸料阀。
31.所述布料装置3包括布料箱31,所述布料箱31的顶部中心设置进料口39,所述进料口39与固料出口24连接。所述布料箱31内设置两根平行设置的搅拌轴32,所述搅拌轴32上布置有左旋叶片37和右旋叶片38,所述左旋叶片37和右旋叶片38对称设置在进料口39两侧,以将从进料口39进入至布料箱31的粉料向两端分布,实现布料。
32.所述搅拌轴32的两端与布料箱31侧壁转动连接;所述搅拌轴32的一端穿出布料箱
31,所述搅拌轴32的穿出端设置有齿轮33,两个搅拌轴32上的齿轮33相啮合;两个齿轮33设置在齿轮箱36内,所述齿轮箱36固定在布料箱31上。其中一根搅拌轴32连接驱动马达35,所述驱动马达35固定在齿轮箱36上。
33.所述布料箱31的底部设有若干个出口34,若干个出口34沿布料箱31长度方向间隔布置。每个出口34连接一个螺旋挤压脱气装置4,所述螺旋挤压脱气装置4是本技术人已授权专利cn202022696189.6公开,在此不再赘述。
34.所述布料装置3、螺旋挤压脱气装置4设置在支架10的中部。
35.每个螺旋挤压脱气装置4的出料口下方设置一个料罐5,所述料罐5与螺旋挤压脱气装置4出料口之间采用软连接方式连接,比如采用软管连接;所述螺旋挤压脱气装置4的出料口上设置开关阀;所述料罐5通过称重仪11固定在支架10的下部。
36.所述料罐5为竖向设置的圆筒结构;所述料罐5的底部为锥形结构,所述料罐5的底部设置下料口51,所述下料口51上设置气动插板阀52。
37.所述下料口51通过伸缩管13连接密封对接装置12,所述伸缩管13为橡胶波纹管。所述密封对接装置12可上下移动,所述密封对接装置12的上端与气缸14的伸缩杆连接,所述气缸14固定在支架10上。
38.作为一种优选,所述密封对接装置12包括对接筒121,所述对接筒121上端与伸缩管13连接,所述对接筒121的下端设置与坩埚8的口部相适配的对接法兰122,所述对接法兰122上设置密封垫123。
39.所述料罐5内沿设置套管15,所述套管15沿料罐5的轴线设置,所述套管15通过支撑杆16固定在料罐5内壁上。
40.所述真空抽气装置6包括抽气管61,所述抽气管61为可伸缩管,所述螺旋挤压脱气装置4水平设置;所述真空抽气装置6包括抽气管61,为可伸缩管,所述抽气管61的伸缩部分滑动贯穿料罐5和螺旋挤压脱气装置4。
41.具体地,所述抽气管61伸缩部分套设在套管15内,所述抽气管61的下部设置抽气管段64,所述抽气管段64管壁上设置有若干个抽气孔,所述抽气孔连通抽气管段64内腔;所述抽气孔的直径≤1um,抽气孔的直径小于电池材料细度,电池材料细度细度一般≥1.94 um,可以避免粉料被抽走;所述抽气管段64的长度小于坩埚8的内腔高度。
42.所述抽气管61的上端可滑动穿出料罐5,并穿过螺旋挤压脱气装置4的出料口后从滑动螺旋挤压脱气装置4上部穿出。所述抽气管61的上端连接波纹软管62,所述波纹软管62与除尘装置7连接;所述抽气管61通过升降气缸63驱动实现伸缩,所述升降气缸63固定在支架10上。
43.所述除尘装置7包括布袋除尘器71,所述布袋除尘器71与真空泵连接。
44.所述布袋除尘器71的进气口连接第一进气管72,所述第一进气管72的下端与螺旋挤压脱气装置4连通;所述第一进气管72的中部连接第二进气管73,所述第二进气管73的下端软连接有连接管74,所述连接管74与对接筒121连接。
45.所述第二进气管73的上部通过波纹软管62与抽气管61连接。
46.进一步地,所述布料箱31上出口34的数量优选为五个,五个出口34通过螺旋挤压脱气装置4可以分别与五个料罐5连接,以实现一次对五个坩埚8进行填料。
47.所述坩埚8成列设置在轨道运输车9上,便于坩埚运输,每列中的坩埚8与料罐5一
一对应。
48.本发明的工作过程:粉料储罐中的电池材料粉料依次经吸料嘴、吸料管路进入气固分离器,气固分离器将粉料分离出来并经出口进入至布料装置内,经布料装置进入螺旋挤压脱气装置进行挤压脱气,能对物料进行初步加密,提高其比重增加坩埚装料量;然后经螺旋挤压脱气装置出料口进入料罐内,待称重仪称量料罐内的粉料达到预定重量,停止进料;然后通过气缸驱动密封对接装置下移,与坩埚口部密封对接,打开料罐上的气动插板阀,粉料进入坩埚内;同时升降气缸驱动抽气管下移至抽气管段插入坩埚内,在与除尘装置连接的真空泵作用下,对坩埚内填入的粉料进行抽气加密,实现最终压实。
49.上述过程中,吸尘装置的设置可以对实现自动吸尘,防止粉尘外泄,避免环境污染。
50.本发明吸尘装置的布袋除尘器连接第一进气管、第二进气管,第一进气管与螺旋挤压脱气装置,实现抽气脱气以及除尘处理;第二进气管与密封对接装置中的对接筒连接,可以对料罐进行除尘处理。
51.本发明可以通过真空抽气装置在坩埚填料时进行抽气压实,压实效果较机械压实明显提高。
52.本发明同时采用真空抽气装置和螺旋挤压脱气装置,螺旋挤压脱气装置对粉料进行挤压脱气,同时可以实现初步加密;真空抽气装置对坩埚内的粉料进行抽气加密,实现最终压实,显著提高了压实效果。
53.本发明气力输送装置的设置,可以实现自动上料,降低劳动强度,提高效率,同时避免人工上料对工人造成的健康损害。
54.本发明采用可升降的密封对接装置与坩埚密封对接,对接速度快,节约对接时间。
55.本发明可以同时完成多个坩埚的加料填实,生产效率显著提高。
56.以上所述为本发明最佳实施方式的举例,其中未详细述及的部分均为本领域普通技术人员的公知常识。本发明的保护范围以权利要求的内容为准,任何基于本发明的技术启示而进行的等效变换,也在本发明的保护范围之内。