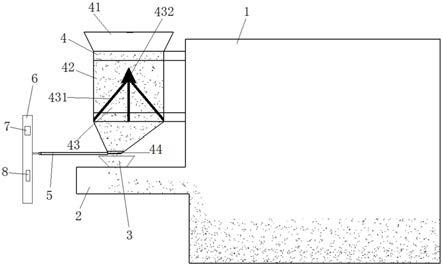
1.本实用新型涉及一种加硅料斗装置,特别涉及一种硅铝混合炉用加硅料斗装置。
背景技术:2.现采用的加硅方式是通过混合炉炉门口,把所需的工业硅,整袋放在加硅平台上,使用叉车整袋推入空混合炉中,然后关闭炉门,点火,入铝,开始熔硅。待铝液入完,炉温达到780度左右时,开始使用扒渣车搅炉继续熔硅,这种加硅方式,工业硅实收率低,只有94%。其次,炉内未完全熔化的工业硅颗粒较多,影响铸损指标及生产成本。最后,能耗损失较多,在加硅和搅炉过程中,都需要开启炉门进行作业,造成吨铝天然气能耗指标超过32nm/t
‑
al,远高于行业水平。
技术实现要素:3.本实用新型为了解决上述问题,提出了一种硅铝混合炉用加硅料斗装置,包括混合炉,所述混合炉一侧设置有铝溜槽,所述铝溜槽上设置有接料口;
4.所述接料口上方安装有料斗装置,所述料斗装置与所述混合炉固定连接,所述料斗装置包括形状为倒置的等腰棱台体的硅料斗,所述硅料斗连接有长方形下料腔,所述下料腔内安装有尖锥体,所述尖锥体包括与所述下料腔固定连接的网锥体和尖刺部分,所述下料腔连接有形状为不规则棱台体的出料口,所述出料口与所述接料口对应,所述出料口底部安装有滑行轨道,所述轨道上安装有可来回滑动的闸板,所述闸板连接有电动伸缩杆,所述伸缩杆连接有固定柱,所述固定柱上嵌入有控制装置和报警装置。
5.进一步的,所述接料口为漏斗状。
6.进一步的,所述硅料斗容积为0.6立方米至1立方米。
7.进一步的,所述下料腔为正方体,容积为1.2立方米至1.5立方米。
8.进一步的,所述尖刺部分为箭头状。
9.与现有技术相比,本实用新型的有益效果是:
10.1、本实用新型一种硅铝混合炉用加硅料斗装置,利用电解高温铝液加热硅颗粒,减少单纯地用天然气加热硅颗粒的天然气用量,使吨铝天然气单耗降低到20nm/t
‑
al。
11.2、本实用新型一种硅铝混合炉用加硅料斗装置,加硅不再开启混合炉的门,保证了炉膛温度不降低,减少天然气消耗。
12.3、本实用新型一种硅铝混合炉用加硅料斗装置,快速流动的高温铝液冲涮硅颗粒,使两者形成相对运动,不仅增加硅颗粒的溶解速度,而且减少硅颗粒被铝灰包裹浮在铝液表面的数量,铸损指标由2.3%降低到1.8%,降低了0.5%。
13.4、本实用新型一种硅铝混合炉用加硅料斗装置,减少了扒渣车搅混合炉的次数,提升了硅的化学成分均匀性。
14.5、本实用新型一种硅铝混合炉用加硅料斗装置,使用后的工业硅吨袋不再烧损浪费,可回收后集中拍卖,创造额外利润收入,也不会造成环境污染。
15.6、本实用新型一种硅铝混合炉用加硅料斗装置,工业硅的实收率得到提高,从94%提高到97%;也减少了叉车叉运输硅袋的次数,减少叉车燃油消耗,也减少了环境污染。
16.7、本实用新型一种硅铝混合炉用加硅料斗装置,通过以往数据分析可知,在混合炉接料口处上方加装料斗装置,改变了加硅的方式,工业硅实收率由94%提高到97%,提高了3%,若按工业硅(3303#)市场价格13000元/吨,年消耗0.72万吨计算,年节约280.08万元,故同时也降低了生产成本。
附图说明
17.为了更清楚的说明本实用新型的技术方案,下面将对实施例中所需要使用的附图作简要的介绍,显而易见地,对于本领域普通技术人员而言,在不付出创造性的前提下,还可以根据这些附图获得其他的附图。
18.图1为本实用新型整体结构图。
19.图2为本实用新型料斗装置示意图。
20.图3为本实用新型滑行轨道、闸板和电动伸缩杆仰视图。
21.图中:1
‑
混合炉、2
‑
铝溜槽、3
‑
接料口、4
‑
料斗装置、41
‑
硅料斗、42
‑
下料腔、43
‑
尖锥体、431
‑
网锥体、432
‑
尖刺部分、44
‑
出料口、45
‑
滑行轨道、46
‑
闸板、5
‑
电动伸缩杆、6
‑
固定柱、7
‑
控制装置、8
‑
报警装置。
具体实施方式
22.为了使本技术领域的人员更好地理解本技术中的技术方案,下面将结合附图,对本技术实施例中的技术方案进行清楚完整的描述。
23.如图1、图2和图3所示,本实用新型,一种硅铝混合炉用加硅料斗装置,包括混合炉1,混合炉1一侧设置有铝溜槽2,铝溜槽2上设置有接料口3;
24.接料口3上方安装有料斗装置4,料斗装置4与混合炉1固定连接,料斗装置4包括形状为倒置的等腰棱台体的硅料斗41,硅料斗41连接有长方形下料腔42,下料腔42内安装有尖锥体43,尖锥体43包括与下料腔42固定连接的网锥体431和尖刺部分432,下料腔42连接有形状为不规则棱台体的出料口44,出料口44与接料口3对应,出料口44底部安装有滑行轨道45,轨道上安装有可来回滑动的闸板46,闸板46连接有电动伸缩杆5,伸缩杆连接有固定柱6,固定柱6上嵌入有控制装置7和报警装置8。
25.具体的,接料口3为漏斗状。
26.具体的,硅料斗41容积为0.6立方米至1立方米。
27.具体的,下料腔42为正方体,容积为1.2立方米至1.5立方米。
28.具体的,尖刺部分432为箭头状。
29.本实用新型工作原理:在混合炉1的铝溜槽2上方,接料口3正上方安装自制的料斗装置4,料斗装置4的总体容积大概为1.8立方米至2.5立方米,料斗装置4包括形状为倒置的等腰棱台体的硅料斗41,硅料斗41连接有长方形下料腔42,下料腔42内安装有尖锥体43,使用时用天车将工业硅吨袋吊运到料斗装置4上方,即硅料斗41正上方,硅吨袋伸入料斗装置4内直至底部与下料腔42内的尖锥体43相碰,尖锥体43将硅吨袋底部划开,利用吨袋本身的
自重,工业硅从吨硅袋底部划破的地方掉出并将吨硅袋底部划开的口子撕裂更大,工业硅颗粒落入硅料斗41。待入铝时,人员打开硅料斗41底部闸板46,工业硅颗粒在自重条件下,经接料口3落入铝溜槽2中,被高温、快速流动的铝液冲入到混合炉1中。
30.电动伸缩杆5控制闸板46的开启、关闭和开启的大小,实现混合后的出料,同时保证硅颗粒匀速落下。电动伸缩杆5通过固定柱6上的控制装置7进行控制。当出料口44出料速度慢,甚至卡料时,当出料速度低于预设速度时,报警装置8会自动发出报警,提醒工作人员前来查看。
31.利用电解高温铝液加热硅颗粒,减少单纯地用天然气加热硅颗粒的天然气用量,使吨铝天然气单耗降低到20nm/t
‑
al;加硅不再开启混合炉1的门,保证了炉膛温度不降低,减少天然气消耗;快速流动的高温铝液冲涮硅颗粒,使两者形成相对运动,不仅增加硅颗粒的溶解速度,而且减少硅颗粒被铝灰包裹浮在铝液表面的数量,铸损指标由2.3%降低到1.8%,降低了0.5%;同时也减少了扒渣车搅混合炉1的次数,提升了硅的化学成分均匀性;而使用后的工业硅吨袋不再烧损浪费,可回收后集中拍卖,创造额外利润收入,也不会造成环境污染;工业硅的实收率得到提高,从94%提高到97%;也减少了叉车叉运输硅袋的次数,减少叉车燃油消耗,也减少了环境污染。
32.通过以往数据分析可知,在混合炉1接料口3处上方加装料斗装置4,改变了加硅的方式,工业硅实收率由94%提高到97%,提高了3%,若按工业硅(3303#)市场价格13000元/吨,年消耗0.72万吨计算,年节约280.08万元,故同时也降低了生产成本。
33.本领域技术人员在考虑说明书及实践这里公开的申请后,将容易想到本技术的其他实施方案。本技术旨在涵盖本技术的任何变型、用途或者适应性变化,这些变型、用途或者适应性变化遵循本技术的一般性原理并包含本技术公开的本技术领域中的公知常识或惯用技术手段。说明书和实施例仅被视为实例性的,本技术的真正范围由权利要求指出。
34.应当理解的是,本技术并不局限于上面已经描述并在附图中示出的精确结构,并且可以在不脱离其范围进行各种修改和改变。以上所述的本技术实施方式并不构成对本技术保护范围的限定。