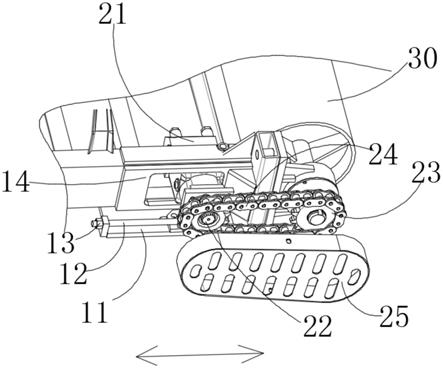
1.本实用新型涉及输送架传动技术领域,具体为一种链条传动的辊筒机构。
背景技术:2.现在常用的液压辊筒是用花键套将液压马达和辊筒体直接相连接,使液压辊筒成为一体,这种方式结构紧凑,零配件加工精度要求高,零配件数量多,成本高,故障率高,目前也有用链条传动的液压辊筒,但其主动链轮和从动链轮之间的轴距是固定的,不可调节,当使用一段时间后链条会伸长,其主要原因是链条中节距变大,因为销轴在套筒内长期的运作,使销轴的外径因磨损变细,如此一来两节套筒之间的距离就增大。
3.这样导致整个液压辊筒不能很好的工作,降低液压马达输出能量效率,并且加大了链条和链轮的摩擦阻力,使链条和链轮磨损加快,降低了其使用寿命。
技术实现要素:4.针对现有技术中存在的问题,本实用新型提供一种新的技术方案,通过对链条传统的辊筒机构进行改进,能够避免链条长时间使用因变长问题而影响输出效率的情况。
5.本实用新型提出的具体方案如下:
6.一种链条传动的辊筒机构,包括输送架和设置在所述输送架上通过链条结构驱动的辊筒,
7.所述链条结构包括驱动件、主动链轮、从动链轮和链条;所述从动链轮安装在所述辊筒的一端,所述主动链轮安装在所述驱动件上,所述链条搭接在所述主动链轮和从动链轮上实现链传动;
8.所述驱动件可移动的设置在所述输送架上使得所述主动链轮相对于所述从动链轮可调节移动的设置。
9.进一步的,所述输送架的大梁上开设有安装孔,所述驱动件可移动的安装在所述安装孔内且所述驱动件的驱动轴朝外。
10.进一步的,所述大梁上位于所述驱动件的位置处焊接有第一加强板,所述第一加强板上设置有调节螺杆和调节螺母,所述驱动件通过安装座设置在所述调节螺杆上,转动所述调节螺杆使得所述驱动件实现移动调节;所述调节螺母设置在所述调节螺杆的一端用于旋紧所述调节螺杆。
11.进一步的,还包括防护罩,所述防护罩固定在所述输送架上罩住所述主动链轮、从动链轮和链条。
12.进一步的,所述辊筒包括空心结构的筒本体和设置在所述筒本体两侧的连接支架,所述连接支架内置在所述筒本体内;
13.所述从动链轮通过第一转轴、轴承与其中一个所述连接支架连接;另一个所述连接支架通过第二转轴与固定在输送架上的轴承座可转动连接。
14.进一步的,所述连接支架包括套筒和呈发散状设置在所述套筒外壁上的承板,每
个所述承板与所述筒本体的内壁连接固定。
15.进一步的,所述驱动件为电机或者液压马达。
16.进一步的,所述输送架的大梁上还设置有第二加强板,所述第二加强板位于所述安装孔处。
17.采用本技术方案所达到的有益效果为:
18.采用上述技术方案,本实用新型与现有液压辊筒机构对比,具有以下优点:零配件少、成本低且加工精度要求不高,结构简单便于维护;同时因为主动链轮能够相对于从动链轮之间的轴距可调,使得整个辊筒机构始终保持高效率的运转状态,故障率低,使用寿命长。
附图说明
19.图1为本方案链条传动的辊筒机构整体结构图。
20.图2为链条结构的组成结构图。
21.图3为图1中a处的局部放大图,展示辊筒的结构。
22.其中:10输送架、11第一加强板、12调节螺杆、13调节螺母、14第二加强板、21驱动件、22主动链轮、23从动链轮、24链条、25防护罩、30辊筒、31筒本体、32连接支架、321套筒、322承板。
具体实施方式
23.以下结合附图对本实用新型的原理和特征进行描述,所举实例只用于解释本实用新型,并非用于限定本实用新型的范围。
24.本实施例提供了一种链条传动的辊筒机构,通过设置可以调节的主传动链轮,在长时间的使用过程中,操作者能够对主动链轮相对从动链轮的位置进行适当的调节,始终保证链条处于合适的套接啮合状态,避免出现如传统的因链条变长影响输出传动效率的问题。
25.具体的,参见图1-图2,本方案提供的辊筒机构包括输送架10和设置在输送架10上通过链条结构驱动的辊筒30,其中链条结构包括驱动件21、主动链轮22、从动链轮23和链条24;从动链轮23安装在辊筒30的一端,主动链轮22安装在驱动件21上,链条24搭接在主动链轮22和从动链轮23上实现链传动。
26.链条24与主动链轮22、从动链轮23之间的安装啮合为常见的连接方式,这里不再对其进行赘述;上文描述的驱动件21可移动的设置在输送架10上使得主动链轮22相对于从动链轮23可调节移动的设置。
27.可以理解为,为了保证驱动件21安装的稳定,传统的设置方式为将驱动件21直接在输送架10上进行固定,即保证驱动件21的位置恒定不变,也正是因为驱动件21无法调节移动,使得由驱动件21驱动的主动链轮22和从动链轮23之间的轴距始终一定,这样链条24因长时间的使用变长后松散的连接在主动链轮22和从动链轮23上;因此本方案基于以上问题,设计驱动件21能够在输送架10上位置可调整,这里的调整具体是指通过调整驱动件21,使得主动链轮22和从动链轮23之间的轴距得以改变,这样即使链条24变长也能够很好地与主动链轮22和从动链轮23进行啮合传动。
28.本方案中,在输送架10的大梁上开设有安装孔,驱动件21可移动的安装在安装孔内且驱动件21的驱动轴朝外,这是因为为了实现对主动链轮22的转动驱动,这里的驱动件21一般采用拥有输出转轴类的装置,比如伺服电机、步进电机或者液压马达等;主动链轮22安装在输出转轴上并朝外,而驱动件21的主体部分位于输送架10内(朝内),这样不仅能够使得主动链轮22和从动链轮23更好的对应,还能够有效地保护驱动件21的主体部分,避免驱动件21的主体外露出现磕碰或者损伤,从而影响了整体的传动。
29.本方案中,考虑到在大梁上开设置安装孔,其强度可能存在下降的情况,因此在大梁上位于驱动件21的位置处焊接有第一加强板11,这里的第一加强板11可以提升此处大梁的强度;同时驱动件21的具体移动也是在第一加强板11上实现的,即第一加强板11上设置有调节螺杆12和调节螺母13,驱动件21通过安装座设置在调节螺杆12上,转动调节螺杆12使得驱动件21实现移动调节;调节螺母13设置在调节螺杆12的一端用于旋紧调节螺杆12。
30.可以理解为驱动件21的移动是通过螺旋移动的方式实现的,当发现链条24的长度明显变长时,操作者通过旋动调节带有螺纹的调节螺杆12,将使得驱动件21在调节螺杆12的作用下进行直线移动调节(图中的箭头方向为移动调节的方向);调节到位后,再通过旋紧调节螺母13,保持调节螺杆12此时的位置不动;在下一次需要调节时,同样通过采用以上方案,使得主动链轮22能够相对从动链轮23完成不断的调节,始终保持与链条24较佳的连接状态;这样对于传动效率的保证和企业成本的节约均具有极大地提升。
31.可选的,在输送架10的大梁上还设置有第二加强板14,第二加强板14位于安装孔处做进一步的加强,保证驱动件21安装固定的稳定性。
32.考虑到操作使用过程中的安全性,这里还设置了防护罩25,防护罩25固定在输送架10上罩住主动链轮22、从动链轮23和链条24,通过防护罩25避免整个链条结构外漏,防止误伤人员和防止外物损伤链轮及链条。
33.可选的,在防护罩25上开设多个透气散热孔,保证链条结构的有效散热。
34.本方案中,参见图3,为了方便维护,对辊筒30的机构同样作出了进一步的设计,传统的辊筒一般为整体式,这样使得重量较重导致安装不便,因此本方案将辊筒30设计为由多个零部件组成的组合体,即辊筒30包括空心结构的筒本体31和设置在筒本体31两侧的连接支架32,连接支架32内置在筒本体31内。
35.可以理解为,为了达到减重的目的,提出的筒本体31为空心结构而非实心,并且通过在筒本体31的两端设置连接支架32实现与输送架10、链条结构之间的传动连接。
36.具体的,链条结构中的从动链轮23通过第一转轴、轴承与其中一个连接支架32连接;另一个连接支架32通过第二转轴与固定在输送架10上的轴承座可转动连接;即筒本体31一侧通过连接支架32与从动链轮23连接,另一侧通过另一连接支架32与输送架10可转动连接,这样在主动链轮22的驱动下,从动链轮23可以带动筒本体31实现转动。
37.本方案中,连接支架32包括套筒321和呈发散状设置在套筒321外壁上的承板322,每个承板322与筒本体31的内壁连接固定;通过这样的结构设置,保证连接支架32结构稳定的同时,也减轻了连接支架32的重量。
38.本技术方案与现有液压辊筒机构对比,零配件少、成本低且加工精度要求不高,结构简单便于维护;同时因为主动链轮能够相对于从动链轮之间的轴距可调,使得整个辊筒机构始终保持高效率的运转状态,故障率低,使用寿命长。
39.以上所述仅为本实用新型的较佳实施例,并不用以限制本实用新型,凡在本实用新型的精神和原则之内,所做的任何修改、等同替换、改进等,均应包含在本实用新型的保护范围之内。