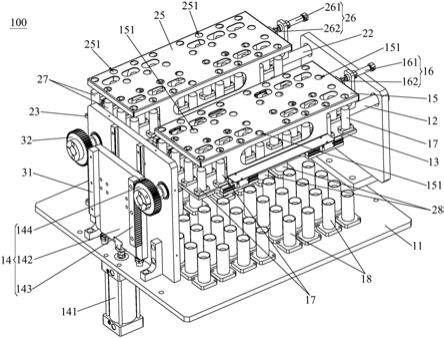
1.本技术涉及采血管移送翻转的技术领域,尤其涉及一种采血管翻转换向装置。
背景技术:2.真空采血管是一种一次性的、可实现定量采血的负压真空玻璃管。在采血管的生产过程中,往往需要对采血管进行翻转变换采血管的管口朝向,以适应不同的加工需求。
3.但是,目前在采血管的生产过程中,对采血管进行翻转的操作方式仍停留在人工手动翻转的方式,需要占用大量的劳动力,作业效率低下,使得生产成本居高不下。而且,人为接触采血管,存在对采血管造成污染的风险,难于保障采血管洁净。
4.因此,急需要一种采血管翻转换向装置来克服上述存在的问题。
技术实现要素:5.本技术实施例的目的在于提供一种采血管翻转换向装置,该采血管翻转换向装置具有结构简单、能够实现自动翻转采血管、作业效率高、能够降低生产成本及避免人为接触采血管的优点。
6.为实现上述目的,本技术实施例的第一方面提供了一种采血管翻转换向装置,包括:基架、第一转轴、第一转动板、转动驱动机构、第一阻挡盖板、第一平移驱动机构、若干第一承载筒及与所述第一承载筒一一对应的第一接料筒,
7.所述第一接料筒呈水平间隔开的竖直固定于所述基架上,所述第一转轴水平枢接于所述基架上,所述第一转动板固定于所述第一转轴上,且所述第一转动板位于所述第一接料筒的上方,所述第一承载筒沿所述第一转动板的平面方向呈间隔开的垂直固定于所述第一转动板上,所述第一转动板具有一第一承接工位及一第一倒出工位;所述第一转动板位于所述第一承接工位时,所述第一承载筒的入料口竖直朝上;所述第一转动板位于所述第一倒出工位时,所述第一承载筒的入料口竖直朝下一一正对于所述第一接料筒;
8.所述转动驱动机构设于所述基架上,所述第一转轴传动连接于所述转动驱动机构上,所述转动驱动机构驱使所述第一转轴带动所述第一转动板往复转动于所述第一承接工位与所述第一倒出工位之间;
9.所述第一阻挡盖板沿平行所述第一转动板的方向移动设于所述第一转动板上,且所述第一承载筒位于所述第一转动板与所述第一阻挡盖板之间;所述第一阻挡盖板具有一第一阻挡位置及一第一避让位置,所述第一阻挡盖板位于所述第一阻挡位置时,所述第一阻挡盖板阻挡于所述第一承载筒的入料口上;所述第一阻挡盖板位于所述第一避让位置时,所述第一阻挡盖板避让于所述第一承载筒的入料口上;
10.所述第一平移驱动机构设于所述第一转动板上,所述第一阻挡盖板传动连接于所述第一平移驱动机构上,所述第一平移驱动机构驱使所述第一阻挡盖板往复移动于所述第一阻挡位置与所述第一避让位置之间。
11.可选地,所述转动驱动机构包括:第一直线驱动器、竖直移动板、第一齿条及第一
齿轮,所述第一直线驱动器竖直固定于所述基架上,所述竖直移动板竖直移动设于所述基架上,所述竖直移动板固定连接于所述第一直线驱动器的输出端;所述第一齿条竖直固定于所述竖直移动板上,所述第一齿轮固定套设于所述第一转轴上,所述第一齿轮啮合配合于所述第一齿条上。
12.可选地,所述第一平移驱动机构包括:第二直线驱动器及第一连接座,所述第二直线驱动器沿所述第一阻挡盖板的移动方向固定于所述第一转动板上,所述第一连接座固定连接于所述第一阻挡盖板上,且所述第一连接座固定连接于所述第二直线驱动器的输出端。
13.可选地,所述第一阻挡盖板开设有与所述第一承载筒一一对应的第一避让孔,所述第一阻挡盖板位于所述第一阻挡位置时,所述第一避让孔错位于所述第一承载筒的入料口;所述第一阻挡盖板位于所述第一避让位置时,所述第一避让孔一一正对于所述第一承载筒的入料口。
14.可选地,所述采血管翻转换向装置还包括:第一保护垫片,所述第一保护垫片固定于所述第一转动板与所述第一承载筒的底部之间。
15.可选地,所述采血管翻转换向装置还包括:第二转轴、第二转动板、第二阻挡盖板、第二平移驱动机构、若干第二承载筒及与所述第二承载筒一一对应的第二接料筒,所述第二接料筒呈水平间隔开的竖直固定于所述基架上,所述第二转轴沿平行于所述第一转轴的方向枢接于所述基架上,所述第二转动板固定于所述第二转轴上,且所述第二转动板位于所述第二接料筒的上方,所述第二承载筒沿所述第二转动板的平面方向呈间隔开的垂直固定于所述第二转动板上,所述第二转动板具有一第二承接工位及一第二倒出工位;所述第二转动板位于所述第二承接工位时,所述第二承载筒的入料口竖直朝上;所述第二转动板位于所述第二倒出工位时,所述第二承载筒的入料口竖直朝下一一正对于所述第二接料筒;
16.所述第二阻挡盖板沿平行所述第二转动板的方向移动设于所述第二转动板上,且所述第二承载筒位于所述第二转动板与所述第二阻挡盖板之间;所述第二阻挡盖板具有一第二阻挡位置及一第二避让位置,所述第二阻挡盖板位于所述第二阻挡位置时,所述第二阻挡盖板阻挡于所述第二承载筒的入料口上;所述第二阻挡盖板位于所述第二避让位置时,所述第二阻挡盖板避让于所述第二承载筒的入料口上;
17.所述第二平移驱动机构设于所述第二转动板上,所述第二阻挡盖板传动连接于所述第二平移驱动机构上,所述第二平移驱动机构驱使所述第二阻挡盖板往复移动于所述第二阻挡位置与所述第二避让位置之间。
18.可选地,所述采血管翻转换向装置还包括:第二齿条及第二齿轮,所述第二齿条竖直固定于所述竖直移动板上,所述第二齿轮固定套设于所述第二转轴上,所述第二齿轮啮合配合于所述第二齿条上。
19.可选地,所述第二平移驱动机构包括:第三直线驱动器及第二连接座,所述第三直线驱动器沿所述第二阻挡盖板的移动方向固定于所述第二转动板上,所述第二连接座固定连接于所述第二阻挡盖板上,且所述第二连接座固定连接于所述第三直线驱动器的输出端;
20.所述第二阻挡盖板开设有与所述第二承载筒一一对应的第二避让孔,所述第二阻
挡盖板位于所述第二阻挡位置时,所述第二避让孔错位于所述第二承载筒的入料口;所述第二阻挡盖板位于所述第二避让位置时,所述第二避让孔一一正对于所述第二承载筒的入料口。
21.可选地,所述采血管翻转换向装置还包括:第二保护垫片,所述第二保护垫片固定于所述第二转动板与所述第二承载筒的底部之间。
22.可选地,所述第一承载筒、所述第一接料筒、第二承载筒及所述第二接料筒均呈中空贯穿的结构,所述第一承载筒、所述第一接料筒、第二承载筒及所述第二接料筒的入料口均呈喇叭状结构。
23.由于本技术的采血管翻转换向装置的第一接料筒呈水平间隔开的竖直固定于基架上,第一转轴水平枢接于基架上,第一转动板固定于第一转轴上,且第一转动板位于第一接料筒的上方,第一承载筒沿第一转动板的平面方向呈间隔开的垂直固定于第一转动板上,第一转动板具有一第一承接工位及一第一倒出工位;第一转动板位于第一承接工位时,第一承载筒的入料口竖直朝上;第一转动板位于第一倒出工位时,第一承载筒的入料口竖直朝下一一正对于第一接料筒。转动驱动机构设于基架上,第一转轴传动连接于转动驱动机构上,转动驱动机构驱使第一转轴带动第一转动板往复转动于第一承接工位与第一倒出工位之间。第一阻挡盖板沿平行第一转动板的方向移动设于第一转动板上,且第一承载筒位于第一转动板与第一阻挡盖板之间;第一阻挡盖板具有一第一阻挡位置及一第一避让位置,第一阻挡盖板位于第一阻挡位置时,第一阻挡盖板阻挡于第一承载筒的入料口上,以阻挡第一承载筒内所承载的采血管脱离于第一承载筒;第一阻挡盖板位于第一避让位置时,第一阻挡盖板避让于第一承载筒的入料口上,以避让第一承载筒内所承载的采血管脱离于第一承载筒。第一平移驱动机构设于第一转动板上,第一阻挡盖板传动连接于第一平移驱动机构上,第一平移驱动机构驱使第一阻挡盖板往复移动于第一阻挡位置与第一避让位置之间。则,转动驱动机构驱使第一转轴带动第一转动板转动至第一承接工位时,第一平移驱动机构驱使第一阻挡盖板移动至第一避让位置,第一承载筒的入料口竖直朝上且未被第一阻挡盖板阻挡,外部的机械手即可将所抓取的采血管放入到对应的第一承载筒内。然后,再由第一平移驱动机构驱使第一阻挡盖板移动至第一阻挡位置,第一阻挡盖板即可阻挡于第一承载筒的入料口上,以阻挡第一承载筒内所承载的采血管脱离于第一承载筒。接着,由转动驱动机构驱使第一转轴带动第一转动板转动至第一倒出工位,再由第一平移驱动机构驱使第一阻挡盖板移动至第一避让位置,使得第一承载筒的入料口竖直朝下一一正对于第一接料筒,第一承载筒内所承载的采血管即可向下脱离于第一承载筒掉落至第一接料筒内,从而完成采血管翻转180
°
的翻转操作,落入第一接料筒的采血管即可经第一接料筒流入后续的加工工序中。从而实现自动翻转采血管,替代人工手动翻转的方式,节省了大量的劳动力,作业效率大大提高,从而降低了生产成本。而且,避免了人为接触采血管,防止对采血管造成人为接触污染的风险,能够更好的保障采血管洁净。再者,本技术的采血管翻转换向装置还具有结构简单的优点。
附图说明
24.图1为本技术实施例中采血管翻转换向装置的组合立体示意图。
25.图2为本技术实施例中采血管翻转换向装置的第一转轴、第一转动板、第一阻挡盖
板、第一平移驱动机构、第一承载筒及第一保护垫片的组合立体示意图。
26.图3为本技术实施例中采血管翻转换向装置的第一接料筒立体结构示意图。
27.图4为本技术实施例中采血管翻转换向装置的第一承载筒立体结构示意图。
28.图5为本技术实施例中采血管翻转换向装置的第二转轴、第二转动板、第二阻挡盖板、第二平移驱动机构、第二承载筒及第二保护垫片的组合立体示意图。
29.图6为本技术实施例中采血管翻转换向装置的第二接料筒立体结构示意图。
30.图7为本技术实施例中采血管翻转换向装置的第二承载筒立体结构示意图。
具体实施方式
31.下面结合附图和优选实施例对本技术作进一步的描述,但本技术的实施方式不限于此。
32.请参阅图1至图4,本技术的采血管翻转换向装置100包括:基架11、第一转轴12、第一转动板13、转动驱动机构14、第一阻挡盖板15、第一平移驱动机构16、若干第一承载筒17及与第一承载筒17一一对应的第一接料筒18。第一接料筒18呈水平间隔开的竖直固定于基架11上,第一转轴12水平枢接于基架11上,第一转动板13固定于第一转轴12上,且第一转动板13位于第一接料筒18的上方,第一承载筒17沿第一转动板13的平面方向呈间隔开的垂直固定于第一转动板13上,第一转动板13具有一第一承接工位及一第一倒出工位;第一转动板13位于第一承接工位时,第一承载筒17的入料口竖直朝上;第一转动板13位于第一倒出工位时,第一承载筒17的入料口竖直朝下一一正对于第一接料筒18。转动驱动机构14设于基架11上,第一转轴12传动连接于转动驱动机构14上,转动驱动机构14驱使第一转轴12带动第一转动板13往复转动于第一承接工位与第一倒出工位之间。第一阻挡盖板15沿平行第一转动板13的方向移动设于第一转动板13上,且第一承载筒17位于第一转动板13与第一阻挡盖板15之间;第一阻挡盖板15具有一第一阻挡位置及一第一避让位置,第一阻挡盖板15位于第一阻挡位置时,第一阻挡盖板15阻挡于第一承载筒17的入料口上,以阻挡第一承载筒17内所承载的采血管脱离于第一承载筒17;第一阻挡盖板15位于第一避让位置时,第一阻挡盖板15避让于第一承载筒17的入料口上,以避让第一承载筒17内所承载的采血管脱离于第一承载筒17。第一平移驱动机构16设于第一转动板13上,第一阻挡盖板15传动连接于第一平移驱动机构16上,第一平移驱动机构16驱使第一阻挡盖板15往复移动于第一阻挡位置与第一避让位置之间。则,转动驱动机构14驱使第一转轴12带动第一转动板13转动至第一承接工位时,第一平移驱动机构16驱使第一阻挡盖板15移动至第一避让位置,第一承载筒17的入料口竖直朝上且未被第一阻挡盖板15阻挡(如图1所示),外部的机械手即可将所抓取的采血管放入到对应的第一承载筒17内。然后,再由第一平移驱动机构16驱使第一阻挡盖板15移动至第一阻挡位置,第一阻挡盖板15即可阻挡于第一承载筒17的入料口上,以阻挡第一承载筒17内所承载的采血管脱离于第一承载筒17。接着,由转动驱动机构14驱使第一转轴12带动第一转动板13转动至第一倒出工位,再由第一平移驱动机构16驱使第一阻挡盖板15移动至第一避让位置,使得第一承载筒17的入料口竖直朝下一一正对于第一接料筒18,第一承载筒17内所承载的采血管即可向下脱离于第一承载筒17掉落至第一接料筒18内,从而完成采血管翻转180
°
的翻转操作,落入第一接料筒18的采血管即可经第一接料筒18流入后续的加工工序中。从而实现自动翻转采血管,替代人工手动翻转的方式,节省了大
量的劳动力,作业效率大大提高,从而降低了生产成本。而且,避免了人为接触采血管,防止对采血管造成人为接触污染的风险,能够更好的保障采血管洁净。具体地,如下:
33.请参阅图1,转动驱动机构14包括:第一直线驱动器141、竖直移动板142、第一齿条143及第一齿轮144,第一直线驱动器141可选择为气缸,但并不以此为限,第一直线驱动器141竖直固定于基架11上,竖直移动板142竖直移动设于基架11上,竖直移动板142固定连接于第一直线驱动器141的输出端;第一齿条143竖直固定于竖直移动板142上,第一齿轮144固定套设于第一转轴12上,第一齿轮144啮合配合于第一齿条143上。则,由第一直线驱动器141驱使竖直移动板142带动第一齿条143升降移动,使得第一齿条143驱动第一齿轮144带动第一转轴12往复转动,即可实现驱使第一转轴12带动第一转动板13往复转动于第一承接工位与第一倒出工位之间,结构简单合理。
34.请参阅图1及图2,第一平移驱动机构16包括:第二直线驱动器161及第一连接座162,第二直线驱动器161可选择为气缸,但并不以此为限,第二直线驱动器161沿第一阻挡盖板15的移动方向固定于第一转动板13上,第一连接座162固定连接于第一阻挡盖板15上,且第一连接座162固定连接于第二直线驱动器161的输出端。则,通过第二直线驱动器161即可驱使第一连接座162带动第一阻挡盖板15往复移动于第一阻挡位置与第一避让位置之间,结构更为简单合理。
35.详细地,第一阻挡盖板15开设有与第一承载筒17一一对应的第一避让孔151,第一阻挡盖板15位于第一阻挡位置时,第一避让孔151错位于第一承载筒17的入料口,使得第一阻挡盖板15阻挡于第一承载筒17的入料口上,以阻挡第一承载筒17内所承载的采血管脱离于第一承载筒17。第一阻挡盖板15位于第一避让位置时,第一避让孔151一一正对于第一承载筒17的入料口,使得第一阻挡盖板15避让于第一承载筒17的入料口上,以避让第一承载筒17内所承载的采血管脱离于第一承载筒17,结构简单合理。
36.请参阅图2,较优者,在本实施中,本技术的采血管翻转换向装置100还包括:第一保护垫片19,第一保护垫片19固定于第一转动板13与第一承载筒17的底部之间,在采血管落入第一承载筒17内时,避免采血管直接撞击到第一转动板13,而对第一转动板13造成撞击损伤及产生飞屑,能更好的保护第一转动板13,结构更为合理。
37.请参阅图1及图5至图7,可选择的,在本实施例中,本技术的采血管翻转换向装置100还包括:第二转轴22、第二转动板23、第二阻挡盖板25、第二平移驱动机构26、若干第二承载筒27及与第二承载筒27一一对应的第二接料筒28,第二接料筒28呈水平间隔开的竖直固定于基架11上,第二转轴22沿平行于第一转轴12的方向枢接于基架11上,第二转动板23固定于第二转轴22上,且第二转动板23位于第二接料筒28的上方,第二承载筒27沿第二转动板23的平面方向呈间隔开的垂直固定于第二转动板23上,第二转动板23具有一第二承接工位及一第二倒出工位;第二转动板23位于第二承接工位时,第二承载筒27的入料口竖直朝上;第二转动板23位于第二倒出工位时,第二承载筒27的入料口竖直朝下一一正对于第二接料筒28。第二阻挡盖板25沿平行第二转动板23的方向移动设于第二转动板23上,且第二承载筒27位于第二转动板23与第二阻挡盖板25之间;第二阻挡盖板25具有一第二阻挡位置及一第二避让位置,第二阻挡盖板25位于第二阻挡位置时,第二阻挡盖板25阻挡于第二承载筒27的入料口上,以阻挡第二承载筒27内所承载的采血管脱离于第二承载筒27;第二阻挡盖板25位于第二避让位置时,第二阻挡盖板25避让于第二承载筒27的入料口上,以避
让第二承载筒27内所承载的采血管脱离于第二承载筒27。再者,第二平移驱动机构26设于第二转动板23上,第二阻挡盖板25传动连接于第二平移驱动机构26上,第二平移驱动机构26驱使第二阻挡盖板25往复移动于第二阻挡位置与第二避让位置之间。再者,本技术的采血管翻转换向装置100还包括:第二齿条31及第二齿轮32,第二齿条31竖直固定于竖直移动板142上,第二齿轮32固定套设于第二转轴22上,第二齿轮32啮合配合于第二齿条31上。则,由第一直线驱动器141驱使竖直移动板142同步带动第一齿条143及第二齿条31升降移动,由第二齿条31驱动第二齿轮32带动第二转轴22往复转动,即可实现驱使第二转轴22带动第二转动板23往复转动于第二承接工位与第二倒出工位之间,结构更为紧凑、简单合理。
38.请参阅图1及图5,第二平移驱动机构26包括:第三直线驱动器261及第二连接座262,第三直线驱动器261可选择为气缸,但并不以此为限,第三直线驱动器261沿第二阻挡盖板25的移动方向固定于第二转动板23上,第二连接座262固定连接于第二阻挡盖板25上,且第二连接座262固定连接于第三直线驱动器261的输出端。则,通过第三直线驱动器261即可驱使第二连接座262带动第二阻挡盖板25往复移动于第二阻挡位置与第二避让位置之间,结构更为简单合理。
39.详细地,第二阻挡盖板25开设有与第二承载筒27一一对应的第二避让孔251,第二阻挡盖板25位于第二阻挡位置时,第二避让孔251错位于第二承载筒27的入料口,使得第二阻挡盖板25阻挡于第二承载筒27的入料口上,以阻挡第二承载筒27内所承载的采血管脱离于第二承载筒27。第二阻挡盖板25位于第二避让位置时,第二避让孔251一一正对于第二承载筒27的入料口,使得第二阻挡盖板25避让于第二承载筒27的入料口上,以避让第二承载筒27内所承载的采血管脱离于第二承载筒27,结构简单合理。
40.请参阅图5,较优者,在本实施中,本技术的采血管翻转换向装置100还包括:第二保护垫片29,第二保护垫片29固定于第二转动板23与第二承载筒27的底部之间,在采血管落入第二承载筒27内时,避免采血管直接撞击到第二转动板23,而对第二转动板23造成撞击损伤及产生飞屑,能更好的保护第二转动板23,结构更为合理。
41.可选择的,在本实施例中,请参阅图3、图4、图6及图7,第一承载筒17、第一接料筒18、第二承载筒27及第二接料筒28均呈中空贯穿的结构,以简化第一承载筒17、第一接料筒18、第二承载筒27及第二接料筒28的加工工艺,而且,通过第一接料筒18及第二接料筒28能够将所承接的采血管导入至后续的加工工序中,结构更为合理。更优是,在本实施例中,第一承载筒17、第一接料筒18、第二承载筒27及第二接料筒28的入料口均呈喇叭状结构,使得采血管能够更为顺畅的滑入第一承载筒17、第一接料筒18、第二承载筒27及第二接料筒28内,结构更为合理。
42.则,通过增加设置第二转轴22、第二转动板23、第二阻挡盖板25、第二平移驱动机构26、第二承载筒27、第二接料筒28、第二齿条31及第二齿轮32,即可实现由同一个第一直线驱动器141来同步驱使第一转动板13及第二转动板23同步转动,同步翻转更多数量的采血管,使得作业效率大幅度提升,而且结构更为合理紧凑。
43.结合附图,对本技术的采血管翻转换向装置100的工作原理作详细说明:
44.首先,由第一直线驱动器141驱使竖直移动板142带动第一齿条143及第二齿条31同步竖直移动,由第一齿条143驱动第一齿轮144驱使第一转轴12带动第一转动板13转动至第一承接工位,同步地,由第二齿条31驱动第二齿轮32驱使第二转轴22带动第二转动板23
转动至第二承接工位。
45.然后,由第二直线驱动器161驱使第一阻挡盖板15移动至第一避让位置,同步地,由第三直线驱动器261驱使第二阻挡盖板25移动至第二避让位置,使得第一承载筒17的入料口竖直朝上且未被第一阻挡盖板15阻挡,以及第二承载筒27的入料口竖直朝上且未被第二阻挡盖板25阻挡(如图1所示),然后,外部的机械手即可将所抓取的采血管放入到对应的第一承载筒17、第二承载筒27内。
46.然后,再由第二直线驱动器161驱使第一阻挡盖板15移动至第一阻挡位置,同步地,由第三直线驱动器261驱使第二阻挡盖板25移动至第二阻挡位置。
47.接着,由第一直线驱动器141驱使竖直移动板142带动第一齿条143及第二齿条31同步反向竖直移动,由第一齿条143驱动第一齿轮144驱使第一转轴12带动第一转动板13反向转动至第一倒出工位,同步地,由第二齿条31驱动第二齿轮32驱使第二转轴22带动第二转动板23反向转动至第二倒出工位。
48.然后,再由第二直线驱动器161驱使第一阻挡盖板15移动至第一避让位置,同步地,由第三直线驱动器261驱使第二阻挡盖板25移动至第二避让位置,使得第一承载筒17的入料口竖直朝下一一正对于第一接料筒18,以及第二承载筒27的入料口竖直朝下一一正对于第二接料筒28,则,第一承载筒17内所承载的采血管即可向下脱离于第一承载筒17掉落至对应的第一接料筒18内,以及第二承载筒27内所承载的采血管即可向下脱离于第二承载筒27掉落至对应的第二接料筒28内,从而完成采血管翻转180
°
的翻转操作,落入第一接料筒18、第二接料筒28的采血管即可经第一接料筒18、第二接料筒28流入后续的加工工序中。
49.由于本技术的采血管翻转换向装置100的第一接料筒18呈水平间隔开的竖直固定于基架11上,第一转轴12水平枢接于基架11上,第一转动板13固定于第一转轴12上,且第一转动板13位于第一接料筒18的上方,第一承载筒17沿第一转动板13的平面方向呈间隔开的垂直固定于第一转动板13上,第一转动板13具有一第一承接工位及一第一倒出工位;第一转动板13位于第一承接工位时,第一承载筒17的入料口竖直朝上;第一转动板13位于第一倒出工位时,第一承载筒17的入料口竖直朝下一一正对于第一接料筒18。转动驱动机构14设于基架11上,第一转轴12传动连接于转动驱动机构14上,转动驱动机构14驱使第一转轴12带动第一转动板13往复转动于第一承接工位与第一倒出工位之间。第一阻挡盖板15沿平行第一转动板13的方向移动设于第一转动板13上,且第一承载筒17位于第一转动板13与第一阻挡盖板15之间;第一阻挡盖板15具有一第一阻挡位置及一第一避让位置,第一阻挡盖板15位于第一阻挡位置时,第一阻挡盖板15阻挡于第一承载筒17的入料口上,以阻挡第一承载筒17内所承载的采血管脱离于第一承载筒17;第一阻挡盖板15位于第一避让位置时,第一阻挡盖板15避让于第一承载筒17的入料口上,以避让第一承载筒17内所承载的采血管脱离于第一承载筒17。第一平移驱动机构16设于第一转动板13上,第一阻挡盖板15传动连接于第一平移驱动机构16上,第一平移驱动机构16驱使第一阻挡盖板15往复移动于第一阻挡位置与第一避让位置之间。则,转动驱动机构14驱使第一转轴12带动第一转动板13转动至第一承接工位时,第一平移驱动机构16驱使第一阻挡盖板15移动至第一避让位置,第一承载筒17的入料口竖直朝上且未被第一阻挡盖板15阻挡,外部的机械手即可将所抓取的采血管放入到对应的第一承载筒17内。然后,再由第一平移驱动机构16驱使第一阻挡盖板15移动至第一阻挡位置,第一阻挡盖板15即可阻挡于第一承载筒17的入料口上,以阻挡第一
承载筒17内所承载的采血管脱离于第一承载筒17。接着,由转动驱动机构14驱使第一转轴12带动第一转动板13转动至第一倒出工位,再由第一平移驱动机构16驱使第一阻挡盖板15移动至第一避让位置,使得第一承载筒17的入料口竖直朝下一一正对于第一接料筒18,第一承载筒17内所承载的采血管即可向下脱离于第一承载筒17掉落至第一接料筒18内,从而完成采血管翻转180
°
的翻转操作,落入第一接料筒18的采血管即可经第一接料筒18流入后续的加工工序中。从而实现自动翻转采血管,替代人工手动翻转的方式,节省了大量的劳动力,作业效率大大提高,从而降低了生产成本。而且,避免了人为接触采血管,防止对采血管造成人为接触污染的风险,能够更好的保障采血管洁净。再者,本技术的采血管翻转换向装置100还具有结构简单的优点。
50.以上结合实施例对本技术进行了描述,但本技术并不局限于以上揭示的实施例,而应当涵盖各种根据本技术的本质进行的修改、等效组合。