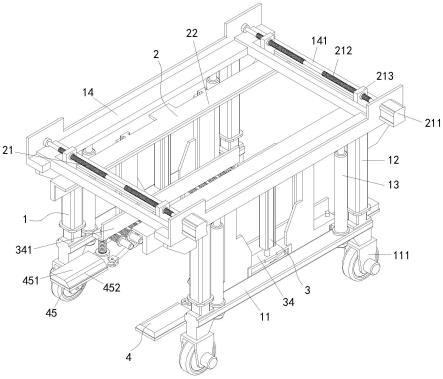
1.本发明涉及装卸机械技术领域,具体提出了一种集装箱自动上下车系统。
背景技术:2.集装箱又称货柜,是指具有一定强度、刚度和规格专供周转使用的大型装货 容器,是能集中装载包装或无包装货进行运输,并便于用机械设备进行装卸搬运 的一种标准化、规格化的成组工具。集装箱最大的成功在于其产品的标准化以及 由此建立的一整套运输体系,能够让一个载重几十吨的庞然大物实现标准化,并 且以此为基础逐步实现建立全球范围内的船舶、港口、航线、公路、中转站、桥 梁、隧道、多式联运相配套的物流运输系统。
3.集装箱按照所装货物、制造材料、结构特征等均可按其标准划分为不同类型 的集装箱。现有的常见的集装箱大多为钢材制造的呈立方体箱式结构。集装箱作 为物流运输系统中货物装载的容量载体需要在物流系统中进行转运输送,在集装 箱堆放基地,在转运过程中,必然需要对集装箱进行上下车的装卸搬运,在现有 的搬运过程中,主要通过专用搬运机械完成对集装箱的上下车搬运,但现有的集 装箱搬运专用机械存在如下问题:1)集装箱存在多种规格尺寸,其尺寸差别主 要体现在集装箱的长度上,现有的常见的专用搬运机械多为用于集装箱长度范围 两端进行包夹抓取的机械卡具,其结构尺寸较大,且需要装配在大型特种搬运车 辆上配合使用,因此整个搬运机械的成本较高。
4.2)现有的集装箱搬运机械多为吊取式机械,即在上下车搬运过程中,基本 未对集装箱底部进行安全承托防护,因此在实际搬运过程中存在掉落的安全隐 患。
技术实现要素:5.为了解决上述问题,本发明提供了一种集装箱自动上下车系统,用于解决上 述背景技术中提到的问题。
6.为了实现上述目的,本发明采用以下技术方案来实现:一种集装箱自动上下 车系统,包括可移动行走的龙门车架,所述龙门车架包括位于顶端升降设置安装 的升降顶框,所述升降顶框上装配有用于集装箱两侧包夹夹紧的包夹机构,所述 包夹机构包括两个可相向运动配合实施包夹动作的包夹板,两个所述包夹板上均 设置有抬落机构,两个所述抬落机构在所述包夹板的运动方向上相对设置。
7.所述抬落机构包括升降设置安装的横梁板,所述横梁板的底端设置有两个竖 板,所述竖板在面向另一侧所述抬落机构的板面上设置有若干沿垂直于所述包夹 板运动方向水平直线分布的弹性抬升杆;所述弹性抬升杆的弹力方向沿所述抱夹 板的运动方向;在位于两个所述抬落机构中的两个所述横梁板的底端均设置有用 于托起集装箱底部的下托机构;所述下托机构包括竖直滑动安装在两个所述竖板 之间的中心板以及两个镜像对称设置在两个所述中心板上的偏转托板组件,所述 偏转托板组件弹性安装在所述横梁板的下方;两个所述偏转托板组件以及所述中 心板可在弹性范围内同步竖直升降。
8.优选的,所述偏转托板组件包括竖直滑动设置在所述横梁板上的转动轴,在 靠近
所述转动轴底端位置水平转动安装有偏转托板,所述转动轴上套设有竖置弹 簧,所述竖置弹簧两端分别固定连接在所述横梁板的底端以及所述转动轴上,所 述偏转托板与所述中心板之间装配有两端铰接连接设置的偏转电动杆。
9.优选的,所述弹性抬升杆包括水平固定在所述竖板上的导杆、滑动配合安装 在所述导杆上的抬升杆和套设在所述导杆上的横置弹簧,所述横置弹簧两端固定 连接在所述竖板与所述抬升杆端部之间。
10.优选的,所述包夹板是由水平板部与竖直板部构成的呈l型结构的长板结 构,所述水平板部偏向两个所述包夹板相对一侧。
11.优选的,所述横梁板上竖直设置有限位靠板,所述限位靠板位于两列所述弹 性抬升杆的上方,且所述限位靠板上用于贴靠的板面与上方相对位置的所述包夹 板中竖直板部用于包夹的板面位于同一竖直面上。
12.优选的,所述抬落机构还包括至少一个竖直固定安装在所述包夹板竖直板部 上的竖直导轨板,至少一个所述竖直导轨板上对应滑动配合安装有竖直滑动臂, 所述包夹板竖直板部上竖直固定安装有二号电动升降杆,所述横梁板固定连接在 所述竖直滑动臂上以及所述二号电动升降杆的输出端上。
13.优选的,所述包夹机构还包括装配在所述升降顶框上的包夹驱动组件,在所 述包夹驱动组件的驱动下两个所述包夹板方向运动。
14.优选的,所述龙门车架还包括两个行走底梁,所述行走底梁上设置有至少一 个伸缩立柱和至少一个一号电动升降杆,所述升降顶框水平固定安装在所有的所 述伸缩立柱顶端以及所有的所述一号电动升降杆的输出端上,两个所述包夹板以 及两个所述抬落机构均一一对应分布在两个所述行走底梁同一侧。
15.上述技术方案具有如下优点或者有益效果:1.本发明提供了一种集装箱自动 上下车系统,本发明提供系统的结构简单合理,设备成本较低,能够独立完成对 集装箱的上下车搬运操作,且采用上下、左右包夹的方式,大大提高了集装箱搬 运过程中的稳定性,另外,对集装箱底部采用双重承托防护的方式,不管是在集 装箱搬运转运途中还是在落放集装箱的过程中,都能提高安全防护,降低搬运过 程中的安全风险。
16.2.本发明提供了一种集装箱自动上下车系统,能够在包夹机构的驱动下, 通过两个包夹板的竖直板部以及两个限位靠板能够对集装箱的左右两侧的靠近 上下端的位置进行包夹,能够在抬落机构的升降驱动下,使得集装箱的上下端包 夹在两个包夹板的水平板部以及两组伸向集装箱起吊孔内的弹性抬升杆之间,从 而在集装箱上下车搬运过程中形成上下、左右的全面包夹,大大提高了搬运的安 全性。
17.3.本发明提供了一种集装箱自动上下车系统,设置的下托机构能够在弹性 抬升杆完成对集装箱的抬升后进一步对集装箱底端进行底端承托,能够形成双重 承托,从而提高了对集装箱搬运过程中的安全防护,另外,对偏转托板采用偏转 设计,能够很方便地伸向集装箱底部或从底部撤出。
附图说明
18.通过阅读参照以下附图对非限制性实施例所作的详细描述,本发明及其特 征、外形和优点将会变得更加明显。在全部附图中相同的标记指示相同的部分, 并未刻意按照比
例绘制附图,重点在于示出本发明的主旨。
19.图1是本发明提供的一种集装箱自动上下车系统在一个视角下的立体结构 示意图。
20.图2是本发明提供的一种集装箱自动上下车系统在另一个视角下的立体结 构示意图。
21.图3是图2中a处的局部放大示意图。
22.图4是图2中b处的局部放大示意图。
23.图5是本发明提供的一种集装箱自动上下车系统的俯视图。
24.图6是图5中c-c的剖视图。
25.图7是本发明提供的一种集装箱自动上下车系统的底视图。
26.图8是本发明提供的一种集装箱自动上下车系统的正视图。
27.图中:1、龙门车架;11、行走底梁;111、电动行走轮;12、伸缩立柱;13、 一号电动升降杆;14、升降顶框;141、导轨梁;2、包夹机构;21、包夹驱动组 件;211、驱动电机;212、双向丝杠;213、滑块;22、包夹板;3、抬落机构; 31、竖直导轨板;32、竖直滑动臂;33、二号电动升降杆;34、横梁板;341、 限位靠板;342、竖板;3421、滑槽;35、弹性抬升杆;351、导杆;352、;抬 升杆;353、横置弹簧;4、下托机构;41、中心板;42、偏转托板组件;43、转 动轴;44、竖置弹簧;45、偏转托板;451、承托垫;452、坡口;46、偏转电动 杆。
具体实施方式
28.下面对照附图,通过对实施例的描述,对本发明的具体实施方式作进一步详 细的说明,目的是帮助本领域的技术人员对本发明的构思、技术方案有更完整、 准确和深入的理解,并有助于其实施,但不作为对本发明的限定。
29.如图1、图5、图6和图8所示,一种集装箱自动上下车系统,该系统可用 于集装箱进行上下车搬运操作,因为在实际搬运过程中,将集装箱从车上卸下与 将集装箱搬运上车的过程基本大致相同,因此在本实施中,以将集装箱从车上卸 下为例进行事例性阐述说明;该系统包括可移动行走的龙门车架1,龙门车架1 包括位于顶端升降设置安装的升降顶框14,龙门车架1还包括两个行走底梁11, 行走底梁11的底端装配有两个电动行走轮111,通过电动行走轮111可以带动 整个系统自由移动,行走底梁11上设置有两个伸缩立柱12和两个一号电动升降 杆13,两个伸缩立柱12以及两个一号电动升降杆13在行走底梁11长度方向上 分布设置,且两个一号电动升降杆13位于两个伸缩立柱12之间,升降顶框14 水平焊接在四个伸缩立柱12顶端以及四个一号电动升降杆13的输出端上。在对 集装箱进行上下车搬运过程中,通过同步启动四个一号电动升降杆13可带动升 降顶框14升降,因此龙门车架1具备主升降功能。
30.如图1和图6所示,升降顶框14上装配有用于集装箱两侧包夹夹紧的包夹 机构2,包夹机构2包括两个可相向运动配合实施包夹动作的包夹板22,两个包 夹板22一一对应分布在两个行走底梁11同一侧,包夹板22是由水平板部与竖 直板部构成的呈l型结构的长板结构,水平板部偏向两个包夹板22相对一侧。 包夹机构2还包括装配在升降顶框14上的包夹驱动组件21,在包夹驱动组件21 的驱动下两个包夹板22方向运动。在本实施例中,包夹驱动组件21的个数为两 个,升降顶框14为矩形框状结构,升降顶框14上设置有两个相对行
走底梁11 长度方向垂直设置的导轨梁141,两个包夹驱动组件21一一对应分布设置在两 个导轨梁141的位置,包夹驱动组件21包括通过螺栓固定安装在升降顶框14 侧壁上的驱动电机211、水平转动安装在升降顶框14上的双向丝杠212以及两 个水平滑动安装在导轨梁141上的滑块213,两个滑块213一一对应螺纹连接在 双向丝杠212的两个螺纹段上,两个包夹板22设置在两个包夹驱动组件21之间, 且包夹板22的水平板部焊接在两个相对位置的滑块213上。包夹机构2可在集 装箱上下车搬运过程中起到包夹作用,通过同步启动两个驱动电机211,两个双 向丝杠212将同步转动,双向丝杠212将驱动滑块213相向运动,继而两个包夹 板22将随之相向运动,最终集装箱将被包夹在两个包夹板22的竖直板部之间。
31.如图1、图2、图3、图6和图7所示,两个包夹板22上均设置有抬落机构 3,两个抬落机构3在包夹板22的运动方向上相对设置,两个抬落机构3一一对 应分布在两个行走底梁11同一侧。抬落机构3包括升降设置安装的横梁板34, 横梁板34上竖直设置有限位靠板341,限位靠板341位于两列弹性抬升杆35的 上方,且限位靠板341上用于贴靠的板面与上方相对位置的包夹板22中竖直板 部用于包夹的板面位于同一竖直面上,在实际搬运操作时,限位靠板341与包夹 板22的竖直板部均将贴靠在集装箱外侧壁上,抬落机构3还包括两个竖直焊接 在包夹板22竖直板部上的竖直导轨板31,两个竖直导轨板31上对应滑动配合 安装有竖直滑动臂32,包夹板22竖直板部上竖直焊接有二号电动升降杆33,两 个竖直滑动臂32对称分布在二号电动升降杆33的两侧,横梁板34焊接在竖直 滑动臂32上以及二号电动升降杆33的输出端上。在对集装箱进行上下搬运过程 中,通过启动二号电动升降杆33,并在竖直导轨板31与竖直滑动臂32的导向 配合下,横梁板34将随之升降,抬落机构3起到副升降功能,在实际作业时, 主要通过抬落机构3对集装箱进行起吊和落地。
32.如图2、图3和图6所示,横梁板34的底端设置有两个竖板342,竖板342 在面向另一侧抬落机构3的板面上设置有若干沿垂直于包夹板22运动方向水平 直线分布的弹性抬升杆35;弹性抬升杆35的弹力方向沿抱夹板的运动方向;弹 性抬升杆35包括水平焊接在竖板342上的导杆351、滑动配合安装在导杆351 上的抬升杆352和套设在导杆351上的横置弹簧353,横置弹簧353两端焊接在 竖板342与抬升杆352端部之间。
33.实际的集装箱结构,一般为了方便进行抬升和吊运,在位于集装箱的长边侧 壁上靠近上下长边位置处均预留有两个起吊孔,但是不同长度尺寸的集装箱其两 个起吊孔的间距也不尽相同,在本系统中,两列弹性抬升杆35是与两个处于靠 近集装箱下方长边位置的起吊孔对应设置,考虑到实际两个起吊孔分布间距的不 同,通过若干个弹性抬升杆35的分布设计,使得在对集装箱进行包夹的过程中, 两列中必然会有合适位置的两个弹性抬升杆35自动对应伸向两个起吊孔中,而 其余的弹性抬升杆35的抬升杆352端部都将抵紧在集装箱侧壁上,此时,横置 弹簧353呈压缩状态,随着运动,直到集装箱贴靠在限位靠板341上为止。通过 这种若干分布设置,使得无需根据集装箱中两个起吊孔的间距进行调节,操作更 加方便。
34.如图1、图4、图6和图7所示,在位于两个抬落机构3中的两个横梁板34 的底端均设置有用于托起集装箱底部的下托机构4;下托机构4包括竖直滑动安 装在两个竖板342之间的中心板41以及两个镜像对称设置在两个中心板41上 的偏转托板组件42,竖板342上配合设置有用于中心板41竖直滑动导向的滑槽 3421。偏转托板组件42弹性安装在横梁板34的下方;两个偏转托板组件42以 及中心板41可在弹性范围内同步竖直升降。偏转托板组件42
包括竖直滑动设置 在横梁板34上的转动轴43,在靠近转动轴43底端位置水平转动安装有偏转托 板45,为了实现缓冲以及为了实现尺寸上的柔性补偿,在位于偏转托板45上端 面上安装有橡胶材料的承托垫451,且承托垫451上位于偏转托板45偏向切入 集装箱底部的一侧设置有引导切入的坡口452,转动轴43上套设有竖置弹簧44, 竖置弹簧44两端分别焊接在横梁板34的底端以及转动轴43上,偏转托板45与 中心板41之间装配有两端铰接连接设置的偏转电动杆46。
35.以下以对集装箱进行下车搬运进行说明,在对集装箱进行下车搬运时:
36.首先,通过启动电动行走轮111带动整个系统移动至搬运工作位置,即使得 集装箱位于两个包夹板22之间,且使得两个下托机构4位于托运车辆车板的上 方。
37.随后,通过龙门车架1主升降结构带动升降顶框14下降,使得同列弹性升 降杆下降至处于下方起吊孔的同一高度位置,此时,偏转托板45底端将压紧在 车板端面上,在逐渐下降过程中,竖置弹簧44将逐渐压缩,且中心板41将顺着 滑槽3421向上滑动;随后,通过移动龙门车架1,使得位于同个抬落机构3中 的两列弹性抬升杆35中均有弹性抬升杆35对准两个起吊孔。
38.接着,通过启动抱夹机构,使得两个包夹板22相向运动,而集装箱两侧最 终将被夹紧在两个包夹板22竖直板部之间;在包夹运动过程中,两个抬落机构 3将随之同步相向运动,集装箱两侧也将同时包夹在两个限位靠板341之间,且 位于集装箱两侧下方的四个起吊孔中均对应有弹性抬升杆35插入。
39.随后,通过龙门车架1的主升降功能使得升降顶框14上升,继而四个弹性 抬升杆35将集装箱抬升至位于车板上方的一定高度,使得偏转托板45脱离接触 车板为止,接着通过两个抬落机构3的副升降功能,使得两个横梁板34同步上 升,继而四个弹性抬升杆35将对集装箱继续抬升,直到集装箱顶部与包夹板22 的水平板部接触为止,继而集装箱将上下稳定包夹在两个包夹板22水平板部与 四个弹性抬升杆35之间。
40.然后,同步启动七个偏转电动杆46,使得偏转电动杆46拉动偏转托板45 向着集装箱底部的方向偏转,继而偏转托板45从坡口452一侧顺势进入到集装 箱的底部,四个偏转托板45将共同承托在集装箱的底部,且此时竖直弹簧呈拉 伸状态,通过偏转托板45将提供双保险,与弹性抬升杆35配合共同对集装箱进 行承托抬升,大大保证了集装箱上下车搬运转移的安全性和稳定性。
41.最后,再次通过龙门车架1带动完成包夹抬升后的集装箱搬运下车,并通过 转运移动至放置位置点,同步启动两个抬落机构3将集装箱下落至靠近放置平面 的位置,随后退回弹性抬升杆35并抽出偏转托板45即可。
42.本领域技术人员应该理解,本领域技术人员结合现有技术以及上述实施例可 以实现所述变化例,在此不予赘述。这样的变化例并不影响本发明的实质内容, 在此不予赘述。
43.以上对本发明的较佳实施例进行了描述。需要理解的是,本发明并不局限于 上述特定实施方式,其中未尽详细描述的设备和结构应该理解为用本领域中的普 通方式予以实施;任何熟悉本领域的技术人员,在不脱离本发明技术方案作出许 多可能的变动和修饰,或修改为等同变化的等效实施例,这并不影响本发明的实 质内容。因此,凡是未脱离本发明技术方案的内容,依据本发明的技术实质对以 上实施例所做的任何简单修改、等同变
化及修饰,均仍属于本发明技术方案保护 的范围内。