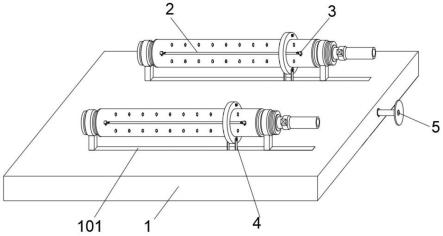
一种自润滑式的导轨内嵌螺杆滑台
1.技术领域
2.本发明涉及直线传动技术领域,尤其涉及一种自润滑式的导轨内嵌螺杆滑台。
背景技术:3.电动滑板(滑台)也称为单轴机械手、直线模组、直线引动器,是通过伺服或步进电机进行驱动的执行机构,是自动化设备中必不可少的运动执行单元,直线滑板作为传动部件用于导向的基础部分,是一种能够提供直线运动的机械结构,可卧式或立式使用,通常用于运输物品,现有的导轨内嵌螺杆滑台需要工作人员经常拆卸、涂抹润滑油,其过程较为繁琐;且无法对导轨内嵌螺杆滑台内的核心部件进行检测,无法可预见性的对核心部件进行检测,当部件损坏时,只能停机更换,严重影响运作效率;针对上述的技术缺陷,现提出一种解决方案。
技术实现要素:4.本发明的目的在于:通过设置安装于工作台上的定位锁止组件可拆卸的定位锁固自润滑导轨,然后通过设置往复驱动组件与自润滑导轨连接并带动其运作,然后通过自润滑导轨运作后通过传送板持续性地运输物品,在此过程中自润滑导轨自动自吸润滑油,且自动将润滑油涂抹在自润滑导轨的部件处,从而保证部件高效传动,且无需工作人员拆卸部件涂抹润滑油,使本发明使用更加简单方便,解决了传统结构部件需要工作人员经常拆卸、涂抹润滑油,其较为繁琐的问题;为了实现上述目的,本发明采用了如下技术方案:一种自润滑式的导轨内嵌螺杆滑台,包括工作台,所述工作台的正上方对称设有自润滑导轨,所述自润滑导轨与工作台的顶端面平行设置,所述自润滑导轨适配有用于锁定自润滑导轨的定位锁止组件和用于驱动其运作的往复驱动组件,所述定位锁止组件和往复驱动组件安装于工作台上,所述自润滑导轨上安装有用于感应自润滑导轨运作时压力的压感防撞组件,所述压感防撞组件电性连接有控制面板;所述自润滑导轨包括轨道管体,所述轨道管体内安装有储油管,所述轨道管体的外端对称开设有第二滑道,且轨道管体的外端滑动套设有连接滑套,所述压感防撞组件有多个,且压感防撞组件设于第二滑道的两端,且压感防撞组件相对设置,所述连接滑套设于两个压感防撞组件之间并与其活动抵接,所述连接滑套的内端固定设有限位滑杆,所述限位滑杆远离连接滑套的一端贯穿第二滑道延伸到轨道管体内并固定连接有挤压弧块,所述挤压弧块抵接有第一升降弧条,所述第一升降弧条的顶端面与挤压弧块的底面抵接,且第一升降弧条对称设有升降杆,两个所述升降杆滑动贯穿储油管的外壁延伸到其内部并固定连接有一个第二升降弧条;所述储油管内安装有吸油弹性件,所述第二升降弧条远离升降杆的端面与吸油弹
性件的外端抵接,所述第二升降弧条的两侧滑动设于储油管内壁,且储油管内开设有适配第二升降弧条的挤压滑槽,所述储油管贯通连接有出油管,所述轨道管体开设有出油微孔,所述出油管的进液口设于吸油弹性件处,且出油管的出液口嵌设于出油微孔内,所述出油管设于两个第二升降弧条之间,所述轨道管体的两端设有螺管部,其中一个所述螺管部贯通连接有连接管,所述连接管上安装有单向阀,所述连接管与储油管贯通连接。
5.进一步的,其中另一个所述螺管部内设有底壳,所述底壳螺纹连接有内六角螺栓,所述内六角螺栓嵌设于螺管部,且内六角螺栓与螺管部抵接,所述底壳的侧面与储油管抵接。
6.进一步的,所述第一升降弧条的端面等距设有抵接弧凸,所述第一升降弧条的一侧设有导向部,所述抵接弧凸与挤压弧块活动抵接,所述导向部与挤压弧块活动抵接。
7.进一步的,所述压感防撞组件由防撞壳体、压力传感器、压感弹性块、回位滑块、伸缩滑杆和防碰块,所述防撞壳体固定设于第二滑道的端部,且压力传感器、压感弹性块和回位滑块设于防撞壳体内,所述压力传感器固定设于防撞壳体内,且压感弹性块的两端分别与压力传感器和回位滑块抵接,所述回位滑块滑动设于防撞壳体内,且回位滑块远离压感弹性块的中心处与伸缩滑杆的一端固定连接,所述伸缩滑杆的另一端滑动贯穿防撞壳体的内壁延伸到其外部并与防碰块固定连接,所述防碰块与连接滑套活动抵接,所述防碰块设于第二滑道的上方,且防碰块与第二滑道在同一水平线上。
8.进一步的,所述定位锁止组件包括定位推板,所述定位推板滑动设于工作台内,所述定位推板的顶端对称设有第二连接套杆,所述第二连接套杆的一端贯穿工作台的顶壁延伸到其外部,所述第二连接套杆的相对面设有第一连接套杆,所述第一连接套杆固定设于定位推板的顶面,且第一连接套杆与第二连接套杆间隙配合设置,所述定位推板的侧面中心处通过轴承转动连接有螺杆,所述螺杆的一端螺纹贯穿工作台的侧壁延伸到其外部并固定连接有转轮,所述第一连接套杆和第二连接套杆分别与螺管部套接设置,所述第一连接套杆和第二连接套杆处适配有螺母套,所述螺母套与螺管部活动螺纹套接。
9.进一步的,所述往复驱动组件包括丝杆和往复电机,所述丝杆转动设于工作台内,所述丝杆与螺杆在同一中轴线上,所述丝杆的外端螺纹套设有螺母座,所述螺母座固定连接有连接板,所述连接板滑动设于工作台内,且连接板的对称设有固定杆,所述固定杆的顶端滑动贯穿工作台的顶壁延伸到其外部,且固定杆的顶部开设有安装孔,所述连接滑套固定设有适配安装孔的螺纹凸杆,所述螺纹凸杆活动设于安装孔,且螺纹凸杆的外端螺纹套接有螺帽,所述往复电机固定设于工作台内,且往复电机的输出轴与丝杆固定连接。
10.进一步的,所述工作台开设有适配固定杆滑动的第一滑道,所述固定杆的中部滑动设于第一滑道内,所述第一连接套杆固定设于第一滑道的端部处,且第二连接套杆的中部滑动设于第一滑道内,所述固定杆设于第一连接套杆与第二连接套杆之间。
11.进一步的,控制面板包括:信息采集模块,用于采集连接滑套运作时的冲击压力值和用于采集连接滑套运作时的速度并发送给数据储存模块;数据储存模块,用于接收连接滑套运作时的冲击压力值和连接滑套运作时的速度并储存为连接滑套运作时的历史冲击压力值和连接滑套运作时的历史速度;衰变警报模块,用于获取数据储存模块内所有的连接滑套运作时的历史冲击压力
值和连接滑套运作时的历史速度经处理得到连接滑套的量化衰变总量a,还将连接滑套的量化衰变总量与预设值进行比较并生成部件更换信号,且将生成的部件更换信号发生给文本警示编辑模块;文本警示编辑模块,用于接收部件更换信号后,立即编辑部件更换文本并将其发送给显示终端显示,其中部件更换文本的字符为“连接滑套请尽快更换”。
12.进一步的,衰变警报模块的具体工作步骤如下:衰变警报模块获取数据储存模块内所有的连接滑套运作时的历史冲击压力值和连接滑套运作时的历史速度经平均并分别生成连接滑套的累记冲击压力均值q和连接滑套的累记速度均值t,通过连接滑套的累记冲击压力均值q和连接滑套的累记速度均值t经计算得到连接滑套的累记冲击压力标准差qa和连接滑套的累记速度标准差ta;然后依据公式,得到连接滑套的量化衰变因子;其中e1、e2、e3和e4为权重修正系数;将实时产生的连接滑套的量化衰变因子与连接滑套的运作总时长相乘得到连接滑套的量化衰变总量a;还将连接滑套的量化衰变总量a与预设值b进行比较,当a>b时,则产生部件更换信号;反之,则不产信号;还将生成的部件更换信号发生给文本警示编辑模块。
13.综上所述,由于采用了上述技术方案,本发明的有益效果是:1、本发明通过设置安装于工作台上的定位锁止组件可拆卸的定位锁固自润滑导轨,然后通过设置往复驱动组件与自润滑导轨连接并带动其运作,然后通过自润滑导轨运作后通过传送板持续性地运输物品,在此过程中自润滑导轨自动自吸润滑油,且自动将润滑油涂抹在自润滑导轨的部件处,从而保证部件高效传动,且无需工作人员拆卸部件涂抹润滑油,使本发明使用更加简单方便,解决了传统结构部件需要工作人员经常拆卸、涂抹润滑油,其较为繁琐的问题;2、本发明通过设置信息采集模块、数据储存模块、衰变警报模块和文本警示编辑模块,实现了对连接滑套衰变程度信息的预采集、储存、量化、计算得到连接滑套的量化衰变总量,然后通过对比分析得到部件更换信号并立即编辑部件更换文本,从而预见性地提醒工作人员在机器空闲时间提前更换连接滑套,保证部件后续的高效运作。
附图说明
14.图1示出了本发明的立体图;图2示出了自润滑导轨的立体图;图3示出了自润滑导轨的剖面图;图4示出了图3的a-a处剖视图;图5示出了压感防撞组件的结构示意图;图6示出了工作台处的剖面示意图;图7示出了本发明的流程图;
图例说明:1、工作台;2、自润滑导轨;3、压感防撞组件;4、定位锁止组件;5、往复驱动组件;101、第一滑道;201、轨道管体;202、连接滑套;203、第二滑道;204、限位滑杆;205、挤压弧块;206、第一升降弧条;207、升降杆;208、储油管;209、第二升降弧条;210、吸油弹性件;211、出油管;212、出油微孔;213、螺管部;214、连接管;215、单向阀;216、底壳;217、内六角螺栓;218、导向部;219、抵接弧凸;220、螺纹凸杆;301、防撞壳体;302、压力传感器;303、压感弹性块;304、回位滑块;305、伸缩滑杆;306、防碰块;401、第一连接套杆;402、第二连接套杆;403、螺母套;404、定位推板;405、螺杆;406、转轮;501、往复电机;502、丝杆;503、螺母座;504、连接板;505、固定杆;506、安装孔。
具体实施方式
15.下面将结合本发明实施例中的附图,对本发明实施例中的技术方案进行清楚、完整地描述,显然,所描述的实施例仅仅是本发明一部分实施例,而不是全部的实施例。基于本发明中的实施例,本领域普通技术人员在没有作出创造性劳动前提下所获得的所有其它实施例,都属于本发明保护的范围。
16.实施例1:如图1-6所示,一种自润滑式的导轨内嵌螺杆滑台,包括工作台1,工作台1的正上方对称设有自润滑导轨2,自润滑导轨2与工作台1的顶端面平行设置,自润滑导轨2适配有定位锁止组件4和往复驱动组件5,定位锁止组件4和往复驱动组件5安装于工作台1上,自润滑导轨2上安装有用于感应自润滑导轨2运作时压力的压感防撞组件3,压感防撞组件3电性连接有控制面板,定位锁止组件4用于锁定自润滑导轨2,往复驱动组件5驱动自润滑导轨2运作,且通过定位锁止组件4使自润滑导轨2可拆卸设置,从而便于更换自润滑导轨2的易损部件;自润滑导轨2包括轨道管体201,轨道管体201内安装有储油管208,轨道管体201的外端对称开设有第二滑道203,且轨道管体201的外端滑动套设有连接滑套202,压感防撞组件3有多个,且压感防撞组件3设于第二滑道203的两端,且压感防撞组件3相对设置,连接滑套202设于两个压感防撞组件3之间并与其活动抵接,连接滑套202的内端固定设有限位滑杆204,限位滑杆204远离连接滑套202的一端贯穿第二滑道203延伸到轨道管体201内并固定连接有挤压弧块205,挤压弧块205抵接有第一升降弧条206,第一升降弧条206的端面等距设有抵接弧凸219,第一升降弧条206的一侧设有导向部218,抵接弧凸219与挤压弧块205活动抵接,导向部218与挤压弧块205活动抵接,第一升降弧条206的顶端面与挤压弧块205的底面抵接,且第一升降弧条206对称设有升降杆207,两个升降杆207滑动贯穿储油管208的外壁延伸到其内部并固定连接有一个第二升降弧条209;储油管208内安装有吸油弹性件210,第二升降弧条209远离升降杆207的端面与吸油弹性件210的外端抵接,第二升降弧条209的两侧滑动设于储油管208内壁,且储油管208内开设有适配第二升降弧条209的挤压滑槽,储油管208贯通连接有出油管211,轨道管体201开设有出油微孔212,出油管211的进液口设于吸油弹性件210处,且出油管211的出液口嵌设于出油微孔212内,出油管211设于两个第二升降弧条209之间,轨道管体201的两端设有螺管部213,其中一个螺管部213贯通连接有连接管214,连接管214上安装有单向阀215,连接管214与储油管208贯通连接;
往复驱动组件5启动使自润滑导轨2运作,自润滑导轨2运作的具体工作步骤如下:连接滑套202在轨道管体201的外表面做左右往复滑动后带动与其固定的限位滑杆204沿第二滑道203的内壁做左右往复滑动,限位滑杆204左右往复滑动后带动与其固定的且设于轨道管体201内的挤压弧块205沿第一升降弧条206的表面做左右往复滑动,且第一升降弧条206的端面等距设有抵接弧凸219,因此会使第一升降弧条206沿轨道管体201的内壁做往复升降运动,第一升降弧条206做往复升降运动后通过升降杆207带动与其固定的第二升降弧条209沿储油管208的内壁做往复升降运动,第二升降弧条209沿储油管208的内壁做往复升降运动后会持续挤压和放松吸油弹性件210,并使吸油弹性件210收缩和扩张,当吸油弹性件210收缩后使吸油弹性件210内润滑油被挤压从出油管211的进口进入,润滑油从出油管211的出口出来并从出油微孔212内挤出,此时在轨道管体201的外表面做左右往复滑动的连接滑套202正好将出油微孔212挤出的润滑油推动,使润滑油均匀附着于轨道管体201的外表面和连接滑套202的内端,当吸油弹性件210扩张时,吸油弹性件210膨胀并产生吸力,从而吸取连接管214外接油箱的润滑油,且在连接管214的上安装单向阀215,使润滑油只能进入到吸油弹性件210内,无法在吸油弹性件210收缩时,润滑油重新返流到油箱内,从而保证自润滑部件,使自润滑导轨2运作时自动润滑无需人工定时润滑;其中另一个螺管部213内设有底壳216,底壳216螺纹连接有内六角螺栓217,内六角螺栓217嵌设于螺管部213,且内六角螺栓217与螺管部213抵接,底壳216的侧面与储油管208抵接,通过底壳216抵接储油管208,使储油管208的进口嵌入连接管214内,通过安装内六角螺栓217将储油管208彻底锁死固定,通过拆卸内六角螺栓217和底壳216,使储油管208可拆卸,便于更换;压感防撞组件3由防撞壳体301、压力传感器302、压感弹性块303、回位滑块304、伸缩滑杆305和防碰块306,防撞壳体301固定设于第二滑道203的端部,且压力传感器302、压感弹性块303和回位滑块304设于防撞壳体301内,压力传感器302固定设于防撞壳体301内,且压感弹性块303的两端分别与压力传感器302和回位滑块304抵接,回位滑块304滑动设于防撞壳体301内,且回位滑块304远离压感弹性块303的中心处与伸缩滑杆305的一端固定连接,伸缩滑杆305的另一端滑动贯穿防撞壳体301的内壁延伸到其外部并与防碰块306固定连接,防碰块306与连接滑套202活动抵接,防碰块306设于第二滑道203的上方,且防碰块306与第二滑道203在同一水平线上;当连接滑套202在轨道管体201的外表面做左右往复滑动后带动与其固定的限位滑杆204沿第二滑道203的内壁做左右往复滑动的过程中,压感防撞组件3保证了限位滑杆204不会抵接到第二滑道203的两端内壁,从而保护限位滑杆204防撞,且连接滑套202在轨道管体201的外表面做左右往复滑动挤压到压感防撞组件3后,压感防撞组件3的防碰块306具有一定的弹性,且防碰块306被连接滑套202挤压移动并带动与其固定的伸缩滑杆305向防撞壳体301内收缩,伸缩滑杆305向防撞壳体301内收缩后带动与其固定回位滑块304沿防撞壳体301的内壁滑动并挤压压感弹性块303,使压感弹性块303被挤压变形收缩,压感弹性块303被挤压变形收缩后其反向作用了作用于压力传感器302上,此时压力传感器302感应到连接滑套202运作时的冲击压力值,连接滑套202运作时的冲击压力值为防碰块306的挤压连接滑套202的最大压力值,且最大压力值达到预设压力范围时,控制连接滑套202脱离与防碰块306的挤压状态,则防碰块306回位,压力传感器302的压力恢复,最大压力值为瞬
时压力,因此需要预设压力范围限位连接滑套202,保证限位滑杆204不会碰撞到第二滑道203的端壁,能够较准确控制限位滑杆204的往复运作的距离,加强设备的智能化;定位锁止组件4包括定位推板404,定位推板404滑动设于工作台1内,定位推板404的顶端对称设有第二连接套杆402,第二连接套杆402的一端贯穿工作台1的顶壁延伸到其外部,第二连接套杆402的相对面设有第一连接套杆401,第一连接套杆401固定设于定位推板404的顶面,且第一连接套杆401与第二连接套杆402间隙配合设置,定位推板404的侧面中心处通过轴承转动连接有螺杆405,螺杆405的一端螺纹贯穿工作台1的侧壁延伸到其外部并固定连接有转轮406,第一连接套杆401和第二连接套杆402分别与螺管部213套接设置,第一连接套杆401和第二连接套杆402处适配有螺母套403,螺母套403与螺管部213活动螺纹套接;将自润滑导轨2的其中一个螺管部213插入固定设于工作台1顶面的第一连接套杆401内,然后托住自润滑导轨2平行与工作台1,然后旋转转轮406并带动与其固定的螺杆405旋转,螺杆405旋转后带动与其通过轴承转动的定位推板404向左滑动,定位推板404向左滑动后带动与其固定的第二连接套杆402沿第一滑道101滑动并套设于自润滑导轨2的另一个螺管部213,直到第二连接套杆402和第一连接套杆401高度挤压轨道管体201,然后停止旋转转轮406,然后将两个螺母套403分别旋套在螺管部213的外端并分别挤压第二连接套杆402或第一连接套杆401,从而将螺管部213定位锁止,定位锁止组件4使自润滑导轨2可拆卸设置,便于后期易耗部件的拆卸更换;往复驱动组件5包括丝杆502和往复电机501,启动安装于工作台1内的往复电机501并控制其输出轴往复旋转,往复电机501的输出轴往复旋转后带动与其固定的并转动设有工作台1内的丝杆502往复旋转,丝杆502往复旋转后带动与其外端螺纹套接的螺母座503左右往复移动,螺母座503左右往复移动后带动与其固定的连接板504沿工作台1的内壁左右往复滑动,连接板504沿工作台1的内壁左右往复滑动后带动与其固定的固定杆505沿工作台1开设的第一滑道101左右往复滑动,且固定杆505的顶部开设有安装孔506,连接滑套202固定设有适配安装孔506的螺纹凸杆220,螺纹凸杆220活动设于安装孔506,且螺纹凸杆220的外端螺纹套接有螺帽,通过设置安装孔506、螺帽和螺纹凸杆220的结构将连接滑套202与固定杆505锁固,使固定杆505沿第一滑道101左右往复滑动后带动与其固定的连接滑套202在轨道管体201的外表面做左右往复滑动,当连接滑套202做左右往复滑动后,可在连接滑套202的外顶面设传送板,并配合机械臂,传送物料,从而带动自润滑导轨2运作;工作原理:本发明通过设置安装于工作台1上的定位锁止组件4可拆卸的定位锁固自润滑导轨2,然后通过设置往复驱动组件5与自润滑导轨2连接并带动其运作,然后通过自润滑导轨2运作后通过传送板持续性地运输物品,在此过程中自润滑导轨2自动自吸润滑油,且自动将润滑油涂抹在自润滑导轨2的部件处,从而保证部件高效传动,且无需工作人员拆卸部件涂抹润滑油,使本发明使用更加简单方便,解决了传统结构部件需要工作人员经常拆卸、涂抹润滑油,其较为繁琐的问题。
17.实施例2:如图7所示,通过在连接滑套202安装传送板,通过传送板持续回位带动物品,对其进行输送,在连接滑套202运作时由于其需要输送物品,且连接滑套202又经常冲击压感防撞组件3,因此当长久使用时,无法较为方便地检测其使用的衰变程度,无法对其进行提前
预测性的预更换,而不做预测性更换,当连接滑套202超过极限时,直接破损,更加地影响部件运作的效率,影响其使用;基于实施例1,控制面板包括信息采集模块、数据储存模块、衰变警报模块和文本警示编辑模块;核心部件的具体检测过程如下:信息采集模块采集连接滑套202运作时的冲击压力值和用于采集连接滑套202运作时的速度并发送给数据储存模块;其中连接滑套202运作时的速度由速度传感器采集得到;数据储存模块接收连接滑套202运作时的冲击压力值和连接滑套202运作时的速度并储存为连接滑套202运作时的历史冲击压力值和连接滑套202运作时的历史速度;衰变警报模块获取数据储存模块内所有的连接滑套202运作时的历史冲击压力值和连接滑套202运作时的历史速度经平均并分别生成连接滑套202的累记冲击压力均值q和连接滑套202的累记速度均值t,通过连接滑套202的累记冲击压力均值q和连接滑套202的累记速度均值t经计算得到连接滑套202的累记冲击压力标准差qa和连接滑套202的累记速度标准差ta;然后依据公式,得到连接滑套202的量化衰变因子;其中e1、e2、e3和e4为权重修正系数,权重修正系数使计算的结果更加的接近真实值,e2>e4>e1>e3,e1+e2+e3+e4=7.89;将实时产生的连接滑套202的量化衰变因子与连接滑套202的运作总时长相乘得到连接滑套202的量化衰变总量a;还将连接滑套202的量化衰变总量a与预设值b进行比较,当a>b时,则产生部件更换信号;反之,则不产信号;还将生成的部件更换信号发生给文本警示编辑模块。
18.文本警示编辑模块,用于接收部件更换信号后,立即编辑部件更换文本并将其发送给显示终端显示,其中部件更换文本的字符为“连接滑套请尽快更换”。
19.工作人员看到部件更换文本后对连接滑套202进行更换;工作原理:本发明通过设置信息采集模块、数据储存模块、衰变警报模块和文本警示编辑模块,实现了对连接滑套202衰变程度信息的预采集、储存、量化、计算得到连接滑套202的量化衰变总量,然后通过对比分析得到部件更换信号并立即编辑部件更换文本,从而预见性地提醒工作人员在机器空闲时间提前更换连接滑套202,保证部件后续的高效运作。
20.以上所述,仅为本发明较佳的具体实施方式,但本发明的保护范围并不局限于此,任何熟悉本技术领域的技术人员在本发明揭露的技术范围内,根据本发明的技术方案及其发明构思加以等同替换或改变,都应涵盖在本发明的保护范围之内。