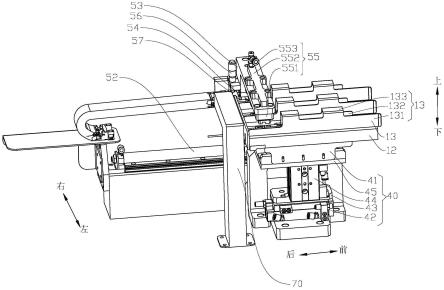
1.本发明涉及电机外壳加工相关技术领域,特别涉及一种快速送料的输送系统及自动打标生产线。
背景技术:2.现有技术中,在电机外壳的加工工艺中,需要对成型的电机外壳进行打标,目前,电机外壳的打标加工一般是经由输送带将电机外壳输送至打标加工工位处,通过工人或者机器进行标签贴合。然而在输送时,大量的电机外壳堆积于输送带上,工人需要将电机外壳摆弄整理才可进行打标,除此之外,输送带的工作方式是运行-停顿-运行,交替进行,上述运行方式下的使得电机外壳打标生产线的生产效率较低,劳动强度较大。
技术实现要素:3.本发明旨在至少解决现有技术中存在的技术问题之一。为此,本发明提出一种快速送料的输送系统,所述快速送料的输送系统运输效率快,生产效率高,劳动强度较低。
4.本发明还提出一种应用上述快速送料的输送系统的自动打标生产线。
5.根据本发明的第一方面实施例的快速送料的输送系统,包括:导料机构,所述导料机构包括用于承接待加工的工件的导料轨道,所述导料轨道沿所述工件被输送方向具有多个工位,沿所述工件被输送的方向,位于最后的所述工位为加工工位,其余所述工位为储料工位;进给推料机构,所述进给推料机构包括可上下移动及前后移动的推送件,所述推送件上设置有多个用于推动所述工件的推送部;移料机构,用于将加工完成的工件移离所述加工工位;
6.其中,所述推送件沿上下方向朝向所述导料轨道移动,以使所述推送部移动至相应所述储料工位的一侧;所述推送件沿前后方向朝所述加工工位移动,以使所述推送部推送相应所述储料工位的所述工件进给至下一所述工位。
7.根据本发明实施例的快速送料的输送系统,至少具有如下有益效果:采用上述结构,通过设置有可上下移动和前后移动的推送件;运输时,多个储料工位中,每个储料工位上放置有待加工的工件,通过推送件沿上下方向朝向导料轨道移动,以使得推送部可插设于相邻的两个储料工位之间,且推送部位于相应的储料工位的一侧,此时,通过推送件沿前后方向朝向加工工位移动,使得推送部将工件朝向加工工位推送,并推送相应储料工位的工件进给下一储料工位,即朝向加工工位向前移动。通过上述运行方式,使得在输送时,当位于加工工位上的工件加工完毕,通过移料机构移离加工工位后,进料推给机构能够快速将工件由储料工位进给至加工工位,且通过合理运行速度控制,使得导料轨道不会出现多个工件堆积情况,能够快速清理导料轨道内的工件,整齐有序且该输送系统无需停顿,能够快速进行运输,提高了生产效率,降低劳动强度。
8.根据本发明的一些实施例,所述导料机构包括:承载台,所述承载台沿其长度方向设置有条形长孔;第一板体,设置于所述承载台的上表面,且所述第一板体位于所述条形长
孔的一侧;第二板体,设置于所述承载台的上表面,且所述第二板体位于所述条形长孔的另一侧,且所述第一板体和所述第二板体二者相向的一侧面配合形成用于与所述工件相适配的所述导料轨道;其中,所述推送部可穿设于所述条形长孔,且所述推送部可相对所述条形长孔上下移动和前后移动。
9.根据本发明的一些实施例,所述第一板体与所述承载台可左右移动地连接,以使所述第一板体与所述第二板体二者相向的一侧面能够靠近或者远离。
10.根据本发明的一些实施例,所述加工工位设置于所述导料轨道一端;所述导料机构还包括设置于所述承载台且用于定位所述工件的定位结构,所述定位结构与所述加工工位对应布置。
11.根据本发明的一些实施例,所述定位结构包括:负压腔室,设置于所述承载台;第一通孔,开设于所述承载台,所述第一通孔位于所述加工工位处,且所述负压腔室的一端与所述第一通孔相连通;第一吸气单元,所述第一吸气单元的吸气端与所述负压腔室的另一端相连通,用于抽取所述负压腔室内空气以形成真空负压。
12.根据本发明的一些实施例,所述进给推料机构包括:第一座体,配置为可相对所述导料轨道前后移动;第一驱动器,所述第一驱动器能够驱动所述第一座体前后移动;第二驱动器,设置于所述第一座体上,所述第二驱动器的输出端设置有第二座体,所述推送件设置于所述第二座体,所述第二驱动器能够驱动所述第二座体上下移动。
13.根据本发明的一些实施例,所述移料机构包括:移动座,配置为可前后移动;第一驱动单元,所述第一驱动单元与所述移动座传动连接;升降座,配置为可相对所述移动座上下移动;第二驱动单元,设置于所述移动座,所述第二驱动单元能够驱动所述升降座上下移动;取料结构,设置于所述升降座,所述取料结构用于将所述加工完成的所述工件移离所述加工工位。
14.根据本发明的一些实施例,所述取料结构包括:吸附载座,设置于所述升降座,所述吸附载座设置有吸附通道和用于与所述工件接触的吸附面,所述吸附面设置有与所述吸附通道相连通的第二通孔;负压板,设置于所述升降座,所述负压板设置有负压气道,所述负压气道的一端连通所述吸附通道;第二吸气单元,所述第二吸气单元的吸气端与所述负压气道的另一端相连通,用于抽取所述负压气道内空气以形成真空负压。
15.根据本发明的一些实施例,还包括吸尘机构,所述吸尘机构位于所述导料机构的一侧,所述吸尘机构用于吸取所述工件加工时产生的灰尘。
16.根据本发明的第二方面实施例的自动打标生产线,包括上述第一方面实施例所述的快速送料的输送系统。
17.根据本发明实施例的自动打标生产线,至少具有如下有益效果:采用上述结构,通过设置有可上下移动和前后移动的推送件;运输时,多个储料工位中,每个储料工位上放置有待加工的工件,通过推送件沿上下方向朝向导料轨道移动,以使得推送部可插设于相邻的两个储料工位之间,且推送部位于相应的储料工位的一侧,此时,通过推送件沿前后方向朝向加工工位移动,使得推送部将工件朝向加工工位推送,并推送相应储料工位的工件进给下一储料工位,即朝向加工工位向前移动。通过上述运行方式,使得在输送时,当位于加工工位上的工件加工完毕,通过移料机构移离加工工位后,进料推给机构能够快速将工件由储料工位进给至加工工位,且通过合理运行速度控制,使得导料轨道不会出现多个工件
堆积情况,能够快速清理导料轨道内的工件,整齐有序且该输送系统无需停顿,能够快速进行运输,提高了生产效率,降低劳动强度。
18.本发明的附加方面和优点将在下面的描述中部分给出,部分将从下面的描述中变得明显,或通过本发明的实践了解到。
附图说明
19.本发明的上述和/或附加的方面和优点从结合下面附图对实施例的描述中将变得明显和容易理解,其中:
20.图1为本发明实施例的输送系统的第一视角结构示意图;
21.图2为本发明实施例的输送系统的第二视角结构示意图;
22.图3为图2中a处结构的放大示意图;
23.图4为本发明实施例的输送系统的第一截面示意图,其中推送部未插入至相邻两个储料工位之间;
24.图5为图4中b处结构的放大示意图;
25.图6为导料机构、工件以及推送件的配合示意图,其中推送部插入至相邻两个储料工位之间;
26.图7为本发明实施例的输送系统的第二截面示意图;
27.图8为本发明实施例的输送系统的分解示意图;
28.图9为导料机构的结构示意图;
29.图10为图9中c处结构的放大示意图;
30.附图标记:
31.导料机构10、导料轨道11、承载台12、条形长孔121、安装孔122、第一板体13、第一侧壁131、第二侧壁132、连接顶壁133、弯折面1321、条形凹位1322、第二板体14;
32.工件20、加工工位30、进给推料机构40、推送件41、推送部411、第一座体42、第一驱动器43、第二驱动器44、第二座体45;
33.移料机构50、移动座51、第一驱动单元52、升降座53、第二驱动单元54、取料结构55、吸附载座551、吸附通道5511、吸附面5512、第二通孔5513、负压板552、
34.负压气道5521、第二吸气单元553、精度调节器56、配合块57;
35.负压腔室61、第一通孔62、吸尘罩70、吸尘通道71、吸尘孔72。
具体实施方式
36.下面详细描述本发明的实施例,所述实施例的示例在附图中示出,其中自始至终相同或类似的标号表示相同或类似的元件或具有相同或类似功能的元件。下面通过参考附图描述的实施例是示例性的,仅用于解释本发明,而不能理解为对本发明的限制。
37.在本发明的描述中,需要理解的是,涉及到方位描述,例如上、下、前、后、左、右等指示的方位或位置关系为基于附图所示的方位或位置关系,仅是为了便于描述本发明和简化描述,而不是指示或暗示所指的装置或元件必须具有特定的方位、以特定的方位构造和操作,因此不能理解为对本发明的限制。
38.在本发明的描述中,如果有描述到第一、第二只是用于区分技术特征为目的,而不
能理解为指示或暗示相对重要性或者隐含指明所指示的技术特征的数量或者隐含指明所指示的技术特征的先后关系。
39.本发明的描述中,除非另有明确的限定,设置、安装、连接等词语应做广义理解,所属技术领域技术人员可以结合技术方案的具体内容合理确定上述词语在本发明中的具体含义。
40.如图1至图10所示,根据本发明的第一方面实施例的快速送料的输送系统,包括:导料机构10,导料机构10包括用于承接待加工的工件20的导料轨道11,导料轨道11沿工件20被输送方向具有多个工位,沿工件被输送的方向,位于最后的工位为加工工位30,其余工位为储料工位;进给推料机构40,进给推料机构40包括可上下移动及前后移动的推送件41,推送件41上设置有多个用于推动工件20的推送部411;移料机构50,用于将加工完成的工件20移离加工工位30;
41.其中,推送件41沿上下方向朝向导料轨道11移动,以使推送部411移动至相应储料工位的一侧;推送件41沿前后方向朝加工工位30移动,以使推送部411推送相应储料工位的工件20进给至下一工位。
42.可以理解的是,在本实施例中,上述加工工位30为用于打标的加工工位30,工件20即电机外壳;当然地,在一些实施例中,加工工位30亦可用于对电机外壳进行其他加工工序,在此不做限定。
43.需要说明的是,如图4、图6、图8和图9所示,在本发明的一些实施例中,上述推送部411的数量为五个,五个推送部411沿推送件41的横向等间距布置,推送部411为向上凸起的凸块,通过推动部即凸块上朝后的一侧面与工件20上朝前的一侧面相抵接,以使得在推送件41朝后移动时能够将工件20朝向加工工位30依次有序进给,结构简单,工作可靠。当然地,上述推送件41和导料轨道11的数量在此不做限定,推送件41和导料轨道11亦可设置为一个,两个或者四个以上等,推送部411亦可根据需求设定相应的数量,推送部411设置为三个、四个等,在此不做限定。
44.根据本发明实施例的快速送料的输送系统,采用上述结构,通过设置有可上下移动和前后移动的推送件41;运输时,多个储料工位中,每个储料工位上放置有待加工的工件20,通过推送件41沿上下方向朝向导料轨道11移动,以使得推送部411可插设于相邻的两个储料工位之间,且推送部411位于相应的储料工位的一侧,此时,通过推送件41沿前后方向朝向加工工位30移动,使得推送部411将工件20朝向加工工位30推送,并推送相应储料工位的工件20进给下一储料工位,即朝向加工工位30向前移动。通过上述运行方式,使得在输送时,当位于加工工位30上的工件20加工完毕,通过移料机构50移离加工工位30后,进料推给机构能够快速将工件20由储料工位进给至加工工位30,且通过合理运行速度控制,使得导料轨道11不会出现多个工件20堆积情况,能够快速清理导料轨道11内的工件20,整齐有序且该输送系统无需停顿,能够快速进行运输,提高了生产效率,降低劳动强度。
45.可以理解的是,如图1至图10所示,在本发明的一些实施例中,导料机构10包括:承载台12,承载台12沿其长度方向设置有条形长孔121;第一板体13,设置于承载台12的上表面,且第一板体13位于条形长孔121的一侧;第二板体14,设置于承载台12的上表面,且第二板体14位于条形长孔121的另一侧,且第一板体13和第二板体14二者相向的一侧面配合形成用于与工件20相适配的导料轨道11;其中,推送部411可穿设于条形长孔121,且推送部
411可相对条形长孔121上下移动和前后移动。采用上述结构,通过推送部411依次伸入条形长孔121和导料轨道11,在推送部411运行时,能够起到导向作用,便于稳定对电机外壳进行进给推送,运行可靠,且结构简单,便于制造。
46.可以想到的是,如图2、图8和图9所示,在本发明的一些实施例中,第一板体13与承载台12可左右移动地连接,以使第一板体13与第二板体14二者相向的一侧面能够靠近或者远离。采用上述结构,能够快速调节导料轨道11的宽度,以适应不同宽度尺寸的工件20,操作便捷,适应范围广。
47.具体地,如图1、图2、图8和图9所示,在本实施例中,上述第一板体13包括第一侧壁131、第二侧壁132以及将第一侧壁131和第二侧壁132二者相连接的连接顶壁133,第一侧壁131位于第一板体13的一侧,第二侧壁132位于第二板体14的另一侧,连接顶壁133位于第二板体14的上方,且连接顶壁133的宽度大于第二板体14的宽度,以使得第一板体13可相对第二板体14左右移动,第二侧壁132上背离连接顶壁133的一端设置有弯折面1321,弯折面1321上开设有条形凹位1322,承载台12上设置有安装孔122,可通过螺栓等紧固件穿设条形凹位1322和安装孔122以将第一板体13固定于承载台12;调节第一板体13和第二板体14二者之间的导料轨道11的宽度时,可通过松脱螺栓等紧固件,使得第一板体13与第二板体14相向或者背向移动;当然地,上述承载台12亦可设置为条形孔,弯折面1321开设有安装孔122,在此不过限定。采用上述结构,不仅结构简单,且操作便捷,制造成本较低。
48.可以理解的是,如图4至图6以及图8至图10所示,在本发明的一些实施例中,加工工位30设置于导料轨道11一端;导料机构10还包括设置于承载台12且用于定位工件20的定位结构,定位结构与加工工位30对应布置。通过上述设置,定位结构定位工件20,使得电机外壳在加工即打标时,能够避免受到碰撞发生晃动而出现错位情况,操作简单,定位效果好。
49.具体地,如图4至图6以及图8至图10所示,在本发明的一些实施例中,定位结构包括:负压腔室61,设置于承载台12;第一通孔62,开设于承载台12,第一通孔62位于加工工位30处,且负压腔室61的一端与第一通孔62相连通;第一吸气单元,第一吸气单元的吸气端与负压腔室61的另一端相连通,用于抽取负压腔室61内空气以形成真空负压。采用上述结构,通过第一通孔62与电机外壳上与承载台12相接触的侧面对应,能够实现对电机外壳的负压稳定吸附,装卸作业高效,不会对产品外表面产生压接损,稳定性较好,作业更高效流畅,结构精简,操作便捷,有效提高电机外壳的生产效率。
50.当然地,在一些实施例中,上述定位结构亦可包括两个可相向或者背向移动的定位块,定位块设置有与电机外壳相接触的柔性胶垫,以便于在保持电机外壳在打标时的稳定,且避免磨损电机外壳;或者定位结构亦可为其他结构,在此不做限定。
51.可以理解的是,如图1、图2、图4、图7和图8所示,进给推料机构40包括:第一座体42,配置为可相对导料轨道11前后移动;第一驱动器43,第一驱动器43能够驱动第一座体42前后移动;第二驱动器44,设置于第一座体42上,第二驱动器44的输出端设置有第二座体45,推送件41设置于第二座体45,第二驱动器44能够驱动第二座体45上下移动。采用上述结构,运行时,第一驱动器43驱动第一座体42朝向加工工位30移动即朝向后移动,通过第二驱动器44驱动第二座体45朝向导料轨道11移动即朝上移动,使得推送部411位于两个储料工位之间,继而,通过第一驱动器43驱动第一座体42接着朝前移动,使得相应储料工位的电机
外壳进给于加工工位30。当加工工位30处的电机外壳打标完成后,通过第二驱动器44带动第二座体45向下移动,以使得推送部411向下移动脱离导料轨道11,接着通过第一驱动器43驱动第一座体42背向加工工位30即朝前移动,第二驱动器44驱动第二座体45朝向导料轨道11移动,以使推动部再次位于相邻两个储料工位之间,使得相邻下一储料工位进给至相邻上一个储料工位,实现了自动对工件20进给推送,无需停歇,大大提高了生产效率,提高了自动化程度,为企业降低了人力成本。
52.可以想到的是,如图1、图2、图4、图7和图8所示,在本发明的一些实施例中,移料机构50包括:移动座51,配置为可前后移动;第一驱动单元52,第一驱动单元52与移动座51传动连接;升降座53,配置为可相对移动座51上下移动;第二驱动单元54,设置于移动座51,第二驱动单元54能够驱动升降座53上下移动;取料结构55,设置于升降座53,取料结构55用于将加工完成的工件20移离加工工位30。采用上述结构,通过第二驱动单元54驱动升降座53上下移动,以便于取料结构55拿取加工工位30上加工完成的电机外壳,且通过第一驱动单元52驱动移动座51前后移动,以便于将电机外壳运输至下一工序,拿取及卸料便捷,结构合理,传动可靠。
53.需要说明的是,在本实施例中,移动座51包括竖直部和水平部,水平部位于加工工位30的上方,竖直部位于导料机构10的一侧且与第二驱动单元54传动连接;升降座53安装有可伸缩的精度调节器56,移动座51上设置有与精度调节器56的伸缩端抵接配合的配合块57,通过精度调节器56和配合块57配合,以设定升降座53和移动座51二者相对移动的上下移动行程范围,精准调节,传动可靠,操作便捷,能够准确拿放电机外壳,不易对电机外壳造成伤害;上述第一驱动单元52为伸缩气缸或者电动推杆等,在此不做限定。
54.具体地,如图1、图2、图4、图7和图8所示,在本发明的一些实施例中,取料结构55包括:吸附载座551,设置于升降座53,吸附载座551设置有吸附通道5511和用于与工件20接触的吸附面5512,吸附面5512设置有与吸附通道5511相连通的第二通孔5513;负压板552,设置于升降座53,负压板552设置有负压气道5521,负压气道5521的一端连通吸附通道5511;第二吸气单元553,第二吸气单元553的吸气端与负压气道5521的另一端相连通,用于抽取负压气道5521内空气以形成真空负压。采用上述结构,通过吸附载座551吸附电机外壳,以移送至下一工序,能实现对电机外壳的负压稳定吸附,装卸作业高效,不会对产品外表面产生压接损,作业更高效流畅,结构精简,操作便捷,有效提高电机外壳的生产效率。当然地,在一些实施例中,上述取料结构55亦可设置为夹持结构,在此不做限定。
55.可以理解的是,如图1、图2、图4和图8所示,在本发明的一些实施例中,还包括吸尘机构,吸尘机构位于导料机构10的一侧,吸尘机构用于吸取工件20加工时产生的灰尘,有利于保证工作环境的空气质量。
56.需要说明的是,在本实施例中,上述吸尘机构包括吸尘罩70和抽风机,吸尘罩70上设置有吸尘通道71和与吸尘通道71相连通的多个吸尘孔72,抽风机与吸尘通道71相连通,且吸尘孔72的通口朝向加工工位30。
57.根据本发明的第二方面实施例的自动打标生产线,包括上述第一方面实施例的快速送料的输送系统。
58.根据本发明实施例的自动打标生产线,采用上述结构,通过设置有可上下移动和前后移动的推送件41;运输时,多个储料工位中,每个储料工位上放置有待加工的工件20,
通过推送件41沿上下方向朝向导料轨道11移动,以使得推送部411可插设于相邻的两个储料工位之间,且推送部411位于相应的储料工位的一侧,此时,通过推送件41沿前后方向朝向加工工位30移动,使得推送部411将工件20朝向加工工位30推送,并推送相应储料工位的工件20进给下一储料工位,即朝向加工工位30向前移动。通过上述运行方式,使得在输送时,当位于加工工位30上的工件20加工完毕,通过移料机构50移离加工工位30后,进料推给机构能够快速将工件20由储料工位进给至加工工位30,且通过合理运行速度控制,使得导料轨道11不会出现多个工件20堆积情况,能够快速清理导料轨道11内的工件20,整齐有序且该输送系统无需停顿,能够快速进行运输,提高了生产效率,降低劳动强度。
59.以上实施例的各技术特征可以进行任意的组合,为使描述简洁,未对上述实施例中的各个技术特征所有可能的组合都进行描述,然而,只要这些技术特征的组合不存在矛盾,都应当认为是本说明书记载的范围。
60.当然,本发明创造并不局限于上述实施方式,熟悉本领域的技术人员在不违背本发明精神的前提下还可作出等同变形或替换,这些等同的变型或替换均包含在本技术权利要求所限定的范围内。