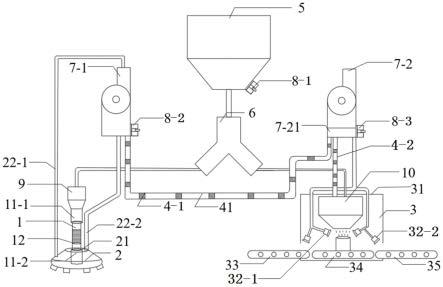
1.本发明涉及一种卸料仓除尘系统,具体是一种卸料仓自动定位高效除尘与粉尘循环利用系统及方法,属于工业除尘技术领域。
背景技术:2.建筑行业作为国民经济的支柱,近些年由于政策的变化和当前形势的影响整体行业有所震荡,但是其整体发展态势依然稳定,尤其是在国家倡导绿色可持续发展的大环境下,建筑建造过程中对于节能、低碳、绿色、环保的关注越来越多。
3.干混砂浆作为建筑行业最常用的一种原材料,可通过在现场加水或配套液体搅拌而成,可根据施工进度、使用量多少灵活掌握,具有品种多、质量优良、使用方便、储存时间长等优点。同时可显著减少工程维护保养费用,更加符合我国全面建设节约型社会的要求。
4.目前,国内的砂浆生产线对于干混砂浆的运输大致采用两种方式:一种是直接通过卸料斗将物料输送至干混砂浆运输车内并运送至施工现场,另一种则是类似于传统水泥运输方式,采用袋装方式并通过机动车运输至施工现场。在使用卸料斗输送物料至干混砂浆运输车时,存在散装机无法精准与车辆连接的问题;卸料过程中,物料从散装机处掉落至车斗内时会激起扬尘,污染作业环境,现有的吸尘罩距离较远、吸程较短,无法完全收集粉尘;袋装过程中,包装机将物料输送至包装袋时也会产生大量的扬尘,并与现场工作人员直接接触,对工人的职业健康产生了极大的损害;同时,现有除尘技术对于除尘器收集的粉尘再利用率较低。
技术实现要素:5.本发明的目的是提供一种卸料仓自动定位高效除尘与粉尘循环利用系统及方法,该系统既能够实现散装机与车辆料斗入口的精确连接,又能实现散装过程的自动化作业,同时,该系统还能实现运输生产线的自动包装作业;再者,该系统能对散装过程和自动包装过程中产生的粉尘进行及时高效的收集,并能在收集后实现粉尘的再利用过程,可有效降低粉尘对工作环境的污染,有助于确保工人身体的健康。该方法步骤简单,自动化程度高,环保性能好,不仅可自动化的实现散装作业和自动包装作业,还能在作业过程中对粉尘进行有效的回收和再利用。
6.为了实现上述目的,本发明提供一种卸料仓自动定位高效除尘与粉尘循环利用系统,包括砂浆罐体、气动三通分料器、散装机、自动定位装置、环形隔尘吸尘装置、除尘风机ⅰ、密闭式自动包装机、除尘风机ⅱ、离心输尘管路a、离心输尘管路b和控制器;所述砂浆罐体上安装有振动电机a,所述气动三通分料器设置在砂浆罐体的下方,气动三通分料器顶部的进料口通过物料输送管路a与砂浆罐体底部的出料口连接;
7.所述散装机通过支架支设在气动三通分料器下方的一侧,其顶部的进料口通过物料输送管路b与三通分料器底部一侧的出料口连接;
8.所述自动定位装置设置在散装机的下方,其由伸缩管ⅰ、伸缩管ⅱ、定位管和图像
采集装置组成;所述伸缩管ⅰ、伸缩管ⅱ均为内外双筒式结构,且外筒可滑动的套设在内筒的外部,且伸缩管ⅰ内筒的顶端与其外筒的顶端之间通过液压装置a进行连接,伸缩管ⅱ外筒的底端与其内筒的底端之间通过液压装置b进行连接;伸缩管ⅰ外筒的顶端与散装机底部的出料口连接;所述定位管的顶端和底端分别与伸缩管ⅰ内筒的底端和伸缩管ⅱ内筒的顶端连接;定位管由上固定环、下固定环、高强度金属波纹管和两组驱动机构组成,两组驱动机构左右相对的设置在高强度金属波纹管内侧壁的相对两侧,每组驱动机构由多个竖连杆、多个定位球和多个横连杆组成,多个竖连杆由上到下依次间隔的分布在上固定环和下固定环之间,且最上端的竖连杆的上端与上固定环的下端固定连接,最下端竖连杆的下端与下固定环的上端固定连接;多个定位球分别位于多个竖连杆形成的多个间隙之中,且每个定位球的下端与其下侧的竖连杆的上端均固定连接,每个定位球的上端中心均开设有容纳槽,并于容纳槽中装配有步进电机,且步进电机的输出轴与所在定位球上方的竖连杆的下端固定连接;多个横连杆与多个定位球一一对应的设置,且横连杆的外端与高强度金属波纹管的内侧壁固定连接,其里端与定位球的外端固定连接;所述图像采集装置安装于伸缩管ⅱ外筒的底端,图像采集装置由红外扫描仪和图像采集卡组成;所述红外扫描仪和图像采集卡连接;
9.所述环形隔尘吸尘装置包括环形气幕吸尘罩、柔性气流管ⅰ、柔性气流管ⅱ;所述环形气幕吸尘罩由呈倒置漏斗状的内罩体和固定连接在内罩体下开口端外侧的环形罩体组成;所述内罩体的上开口端套装在伸缩管ⅱ内筒中部的外侧;所述环形罩体的内部周向均匀的连接有若干个气幕发生器;
10.所述除尘风机ⅰ顶部的排风口通过柔性气流管ⅰ分别与若干个气幕发生器的进气口连接,其底部设置有集尘室,且集尘室底部的吸风口其通过柔性气流管ⅱ与内罩体上的抽气口连接;
11.所述密闭式自动包装机通过支架支设在散装机下方的另一侧,其由整体密闭罩、包装料斗、侧吸罩a、侧吸罩b、自动称重皮带机、包装输送机和物料输送机组成;所述整体密闭罩的下端开口;所述包装料斗安装在整体密闭罩内腔的上部,其顶部的进料口通过物料输送管路c与三通分料器底部另一侧的出料口连接,其底部的出料口设置有卸料阀;一对侧吸罩a分别设置于包装料斗底部出料口的相对两侧,一对侧吸罩a的吸气口相对的设置,其出气口上均连接有抽气管路a,抽气管路a上串接有电磁阀a;一对侧吸罩b分别设置在整体密闭罩下端两侧的开口处,一对侧吸罩b的吸气口相背离的设置,其出气口上均连接有抽气管路b,抽气管路b上串接有电磁阀b;所述自动称重皮带机设置在整体密闭罩下开口端内部的下方;所述包装输送机设置在自动称重皮带机的上游侧,且其出料端由外部延伸到整体密闭罩的内部并与自动称重皮带机的进料端连续接合;所述物料输送机设置在自动称重皮带机的下游侧,且其进料端由外部延伸到整体密闭罩的内部并与自动称重皮带机的出料端连续接合;
12.所述除尘风机ⅱ顶部的排风口与外部大气连通,其底部设置有临时储尘仓,且临时储尘仓底部的吸风口通过吸气管路同时与一对抽气管路a和一对抽气管路b连接;
13.所述离心输尘管路a和离心输尘管路b的结构相同,均由柔性骨架风管、离心扇叶和固定支架组成,多个离心扇叶均匀的分布于柔性骨架风管的内部,且通过多个对应的固定支架与柔性骨架风管的内侧壁连接;所述离心输尘管路a的进风侧和出风侧分别与除尘
风机ⅰ的集尘室和除尘风机ⅱ的临时储尘仓贯通连接,所述离心输尘管路b的进风侧和出风侧分别与除尘风机ⅱ的临时储尘仓和包装料斗的进料口贯通连通;
14.所述控制器分别与图像采集卡、控制液压装置a伸缩的电磁换向阀a、步进电机、控制液压装置b伸缩的电磁换向阀b、散装机、除尘风机ⅰ、除尘风机ⅱ、振动电机a、离心扇叶、包装料斗中的卸料阀、电磁阀a、电磁阀b、自动称重皮带机、包装输送机和物料输送机连接。
15.进一步,为了保证连接强度,所述环形气幕吸尘罩的上端通过周向均匀分布的三根金属杆与伸缩管ⅱ内筒的筒身固定连接;为了保证环形隔尘吸尘装置能够有效地除去散装机下料时产生的粉尘,提高生产线处的空气质量,避免粉尘的飞扬,在伸缩管ⅱ处于最长状态时,环形气幕吸尘罩的底部位于伸缩管ⅱ底部上方的10-15cm处。
16.进一步,为了提高除尘风机的集尘效果,所述除尘风机ⅰ的外部安装有振动电机b,所述这除尘风机ⅱ的外部安装有振动电机c;所述振动电机b和振动电机c均与控制器连接。
17.作为一种优选,所述液压装置为液压油缸。
18.进一步,为了方便选择工作模式,还包括控制面板,所述控制面板上设置有散装模式选择按键和自动包装模式选择按键,散装模式选择按键和自动包装模式选择按键均与控制器连接。
19.本发明中,通过自动定位装置的设置,可以通过红外扫描仪对干混砂浆生产线下料处车辆的驶入情况进行自动扫描,并能通过图像采集卡利用实时传输的图像判断车辆是否为干混砂浆运输车,这样,可有效避免了其他车辆驶入带来的误判;另外,在运输车驶入且停车后,红外扫描仪能够自动扫描运输车进料口图像并传输至图像采集卡,以便于图像采集卡能够计算出所需伸缩的距离和所需弯曲的角度数据;通过在伸缩管ⅰ内筒的顶端与其外筒的顶端之间设置液压装置a,在伸缩管ⅱ内筒的底端与其外筒的底端之间设置液压装置b,可以自动化的实伸缩管ⅰ和伸缩管ⅱ的伸缩过程;通过在定位管中设置有由多个定位球、多个竖连杆、多个横连杆和多个步进电机,并使定位球通过横向杆与高强度金属波纹管的内侧壁固定连接,可以自动化的调节定位管的弯曲度,从而能适应不同位置的定位需求;通过控制器的设置能够根据所需伸缩的距离和所需弯曲的角度数据控制对应的液压装置进行一定行程的伸缩,从而保证了散装机出料口所连接的管路能够伸入到车辆的进料口内。相较于传统方式散装机进料口位置固定、车辆进料口较小,需要干混砂浆运输车多次调整位置来保证物料的装车的方式,本发明具有操作过程便捷、自动化程度高、人工干预操作较少、反应迅速的优点。通过环形隔尘吸尘装置的设置,可以利用外侧环形罩体上的若干个气幕发生器产生的环形气幕有效粉尘的外溢,同时,能利用内侧的内罩体从多角度吸除装料过程中逸散的粉尘,这样,便实现了隔尘吸尘的功能;相较于传统吸尘罩距离较远、吸尘方向单一、难以完全除去扬尘的方式,本发明可有效避免粉尘飘散至周围的环境中,同时,能使未被一次吸降的粉尘在气幕内悬浮以便于被再次吸除,其具有除尘效率高、除尘效果好、无粉尘逸散现象的优点。通过密闭式自动包装机的设置,能够实现包装运输、砂料装卸、袋装砂料运输过程的全自动化操作,并能粉尘回收及再利用过程;利用设置在自动称重皮带机上的位置检测传感器对包装袋是运输到包装料斗下方进行检测,同时,利用设置在自动称重皮带机上的荷重单元检测包装袋内的砂料质量,能方便的实现包装料斗中砂料的自动卸料和停止卸料的操作,进而极大地提升了自动化程度,这样,不仅减少了现场工人的劳动负荷,还避免了工人与粉尘的直接接触,保障了现场工人的身体健康;通过分别安设于包
装料斗底部两侧的一对侧吸罩a,可以通过与卸料阀同步工作的方式来有效减少包装过程中粉尘的产生,同时在整体密闭罩底部与包装输送机、物料输送机接触的开口处内侧设置了一对侧吸罩b,可以使其在自动包装作业过程中全程保持开启状态,进而能有效避免了自动包装过程中粉尘通过开口泄露至外部环境的情况发生,相较于传统工人手动包装、运输方式,具有节省人力、操作过程简便、自动化程度高、无粉尘接触等优点。通过离心输尘管路a的设置,可以利用设置于柔性骨架风管中的多个离心扇叶来将除尘风机ⅰ底部集尘室中的粉尘输送到除尘风机ⅱ底部的临时储尘仓中,实现了粉尘的集中式回收;通过离心输尘管路b的设置,可以利用设置于柔性骨架风管中的多个离心扇叶来将临时储尘仓中粉尘输送到包装料斗中,进而实现了粉尘的有效回收再利用过程;与传统螺旋输送机的输送方式相比,离心输尘管路能够更加有效地输送粉尘,同时,利用多个离心扇叶有效避免了粉尘堵塞于管路内部的情况发生,再者,柔性骨架管路能够随意弯曲,适用于多种工作环境,相较于传统工艺具有易于铺设、不易漏尘的优点,提高了干混砂浆物料的回收利用率。
20.本发明还提供了一种卸料仓自动定位高效除尘与粉尘循环利用方法,包括一种卸料仓自动定位高效除尘与粉尘循环利用系统,还包括以下步骤:
21.当散装模式选择按键按下时,散装模式选择按键向控制器发出散装模式选择信号,控制器接收到散装模式选择信号后执行步骤一;当自动包装模式选择按键按下时,自动包装模式选择按键向控制器发出自动包装模式选择信号,控制器接收动包装模式选择信号后执行步骤二;
22.步骤一:散装模式启动:
23.s11:通过红外扫描仪实时监测散装机下方车辆的进入情况,当车辆驶入生产线时,红外扫描仪自动扫描识别车辆属性,并将扫描到的车辆图像传输至图像采集卡处,由图像采集卡判断车辆是否符合设定特征,若车辆为干混砂浆运输车,且保持停止状态达10s以上时,执行s12;
24.s12:通过红外扫描仪继续扫描车辆进料口的图像信息,并将数据传输至图像采集卡,由图像采集卡对图像处理后发送给控制器;
25.s13:当控制器接收到数据后,先确定车辆进料口的位置信息,并自动计算出伸缩管ⅰ和伸缩管ⅱ所需伸缩的距离,以及定位管所需弯曲的角度,再根据距离和角度数据生成对应的控制信息;然后,先向电磁换向阀a发出对应的控制信号,通过控制液压装置a伸缩部分的伸缩来使伸缩管ⅰ进行伸缩动作,直至达到指定距离时停止;再向对应的步进电机发出对应的控制信号,通过对应步进电机的来驱动其上方对应竖连杆的旋转,进而带动该竖连杆上端的定位球和横连杆进行旋转,以带动高强度金属波纹管内侧壁上的一个部分发生移动,通过多个横连杆来带动高强度金属波纹管内侧壁上的多点进行移动,从而使定位管进行弯曲动作,直至达到指定的弯曲角度,且伸缩管ⅱ的底部位于车辆进料口的上方时停止;最后,向电磁换向阀b发出对应的控制信号,通过控制液压装置b伸缩部分的伸缩来使伸缩管ⅱ进行伸缩动作,直至伸缩管ⅱ的底端伸入至干混砂浆运输车进料口顶盖下方10cm处时停止;完成上述所有操作后,执行s14;
26.s14:控制器发送下料信号至散装机、发送工作信号到除尘风机ⅰ,控制散装机在设定时间内进行下料作业,同时,同步控制除尘风机ⅰ工作,通过柔性气流管ⅰ向若干个气幕发生器供入高速气流并于内罩体外围形成环形气幕,以防止粉尘外溢,通过柔性气流管ⅱ将
环形气幕内侧的粉尘吸到除尘风机ⅰ底部的集尘室进行收集;
27.s15:当散装下料作业结束后,按照s13的逆操作过程控制自动定位装置复位至原始位置;
28.步骤二:自动包装模式启动;
29.s21:控制器发送控制信号控制自动称重皮带机、包装输送机、物料输送机和除尘风机ⅱ开启,包装输送机启动后自动运输包装袋至自动称重皮带机处,并经自动称重皮带机继续输送;同时,控制电磁阀b开启,以在整个自动包装过程中利用一对侧吸罩b对整体密闭罩下端开口处的粉尘进行同步吸收;
30.s22:利用设置在自动称重皮带机上的位置检测传感器在包装袋运输至包装料斗底部出料口下方时向控制器发送包装到位信号,控制器接收到包装到位信号后控制自动称重皮带机停止运行,并控制包装料斗中的卸料阀开启设定时间进行下料,控制电磁阀a开启以在下料过程中利用一对侧吸罩a对包装料斗底部出料口处产生的粉尘进行同步吸收,同时,利用自动称重皮带机上的荷重单元将实时监测皮带上方的质量信号,并实时发送给控制器,控制器根据重量信号获得物料质量m,当物料质量m达到设定质量m0后,控制包装料斗中的卸料阀关闭以停止包装下料作业,并控制电磁阀a关闭以停止吸尘作业,控制自动称重皮带机继续运动,经物料输送机将包装完成的物料输送至整体密闭罩的外侧;持续这一过程直至完成所有包装袋的自动包装作业。
31.进一步,为了实现粉尘的有效回收,在步骤一的s14中,当下料作业持续设定时间后,通过控制器控制离心输尘管路a中的多个离心扇叶启动,利用柔性骨架风管将除尘风机ⅰ底部集尘室中的粉尘输送至除尘风机ⅱ底部的临时储尘仓中。
32.进一步,为了实现粉尘的有效回收,在步骤二的s22中,当下料作业持续设定时间后,通过控制器控制离心输尘管路b中的多个离心扇叶启动,利用柔性骨架风管将除尘风机ⅱ底部临时储尘仓中的粉尘输送至包装料斗中。
33.本方法步骤简单,自动化程度高,环保性能好,不仅可自动化的实现散装作业和自动包装作业,还能在作业过程中对粉尘进行有效的回收和再利用。
附图说明
34.图1为本发明的整体结构示意图;
35.图2为本发明的自动定位装置的结构示意图;
36.图3为本发明的自动定位装置定位前的截面图;
37.图4为本发明的自动定位装置定位后的截面图;
38.图5为本发明的环形隔尘吸尘装置结构示意图;
39.图6为本发明的离心输尘管路的内部结构示意图;
40.图7为本发明的工作原理电路框图。
41.图中:1、自动定位装置,2、环形隔尘吸尘装置,3、密闭式自动包装机,4-1、离心输尘管路a,4-2、离心输尘管路b,5、砂浆罐体,6、气动三通分料器,7-1、除尘风机ⅰ,7-2除尘风机ⅱ,7-21、临时储尘仓,8-1、振动电机a,8-2、振动电机b,8-3、振动电机c,9、散装机,10、包装料斗,11-1、伸缩管ⅰ,11-2伸缩管ⅱ,12、定位管,13、图像采集装置,13-1、红外扫描仪,13-2、图像采集卡,13-3、控制器,14-1、液压装置a,14-2、定位球,14-3、液压装置b,14-4、竖
连杆,14-5、横连杆,14-6、高强度金属波纹管,14-7、上固定环,14-8、下固定环,21、环形气幕吸尘罩,22-1、柔性气流管ⅰ,22-2、柔性气流管ⅱ,22-3、气幕发生器,22-4、金属杆,31、整体密闭罩,32-1、侧吸罩a,32-2、侧吸罩b,33、包装输送机,34、自动称重皮带机,35、物料输送机,41、离心扇叶,42、柔性骨架风管,43、固定支架。
具体实施方式
42.下面结合附图对本发明做进一步说明。
43.如图1至图7所示,一种卸料仓自动定位高效除尘与粉尘循环利用系统,包括砂浆罐体5、气动三通分料器6、散装机9、自动定位装置1、环形隔尘吸尘装置2、除尘风机ⅰ7-1、密闭式自动包装机3、除尘风机ⅱ7-2、离心输尘管路a4-1、离心输尘管路b4-2和控制器13-3;所述砂浆罐体5上安装有振动电机a8-1,所述气动三通分料器6设置在砂浆罐体5的下方,气动三通分料器6顶部的进料口通过物料输送管路a与砂浆罐体5底部的出料口连接;
44.所述散装机9通过支架支设在气动三通分料器6下方的一侧,其顶部的进料口通过物料输送管路b与三通分料器6底部一侧的出料口连接;
45.所述自动定位装置1设置在散装机9的下方,其由伸缩管ⅰ11-1、伸缩管ⅱ11-2、定位管12和图像采集装置13组成;所述伸缩管ⅰ11-1、伸缩管ⅱ11-2均为内外双筒式结构,且外筒可滑动的套设在内筒的外部,且伸缩管ⅰ11-1内筒的顶端与其外筒的顶端之间通过液压装置a14-1进行连接,伸缩管ⅱ11-2外筒的底端与其内筒的底端之间通过液压装置b14-3进行连接;伸缩管ⅰ11-1外筒的顶端与散装机9底部的出料口连接;定位管12的顶端和底端分别与伸缩管ⅰ11-1内筒的底端和伸缩管ⅱ11-2内筒的顶端连接;定位管12由上固定环14-7、下固定环14-8、高强度金属波纹管14-6和两组驱动机构组成,两组驱动机构左右相对的设置在高强度金属波纹管14-6内侧壁的相对两侧,每组驱动机构由多个竖连杆14-4、多个定位球14-2和多个横连杆14-5组成,多个竖连杆14-4由上到下依次间隔的分布在上固定环14-7和下固定环14-8之间,且最上端的竖连杆14-4的上端与上固定环14-7的下端固定连接,最下端竖连杆14-4的下端与下固定环14-8的上端固定连接;多个定位球14-2分别位于多个竖连杆14-4形成的多个间隙之中,且每个定位球14-2的下端与其下侧的竖连杆14-4的上端均固定连接,每个定位球14-2的上端中心均开设有容纳槽,并于容纳槽中装配有步进电机,且步进电机的输出轴与所在定位球14-2上方的竖连杆14-4的下端固定连接;多个横连杆14-5与多个定位球14-2一一对应的设置,且横连杆14-5的外端与高强度金属波纹管14-6的内侧壁固定连接,其里端与定位球14-2的外端固定连接;所述图像采集装置13安装于伸缩管ⅱ11-2外筒的底端,图像采集装置13由红外扫描仪13-1和图像采集卡13-2组成;所述红外扫描仪13-1和图像采集卡13-2连接;
46.所述环形隔尘吸尘装置2包括环形气幕吸尘罩21、柔性气流管ⅰ22-1、柔性气流管ⅱ22-2;所述环形气幕吸尘罩21由呈倒置漏斗状的内罩体和固定连接在内罩体下开口端外侧的环形罩体组成;所述内罩体的上开口端套装在伸缩管ⅱ11-2内筒中部的外侧;所述环形罩体的内部周向均匀的连接有若干个气幕发生器22-3;
47.所述除尘风机ⅰ7-1顶部的排风口通过柔性气流管ⅰ22-1分别与若干个气幕发生器22-3的进气口连接,其底部设置有集尘室,且集尘室底部的吸风口其通过柔性气流管ⅱ22-2与内罩体上的抽气口连接;
48.所述密闭式自动包装机3通过支架支设在散装机9下方的另一侧,其由整体密闭罩31、包装料斗10、侧吸罩a32-1、侧吸罩b32-2、自动称重皮带机34、包装输送机33和物料输送机35组成;所述整体密闭罩31的下端开口;所述包装料斗10安装在整体密闭罩31内腔的上部,其顶部的进料口通过物料输送管路c与三通分料器6底部另一侧的出料口连接,其底部的出料口设置有卸料阀;一对侧吸罩a32-1分别设置于包装料斗10底部出料口的相对两侧,一对侧吸罩a32-1的吸气口相对的设置,其出气口上均连接有抽气管路a,抽气管路a上串接有电磁阀a;一对侧吸罩b32-2分别设置在整体密闭罩31下端两侧的开口处,一对侧吸罩b32-2的吸气口相背离的设置,其出气口上均连接有抽气管路b,抽气管路b上串接有电磁阀b;所述自动称重皮带机34设置在整体密闭罩31下开口端内部的下方;所述包装输送机33设置在自动称重皮带机34的上游侧,且其出料端由外部延伸到整体密闭罩31的内部并与自动称重皮带机34的进料端连续接合;所述物料输送机35设置在自动称重皮带机34的下游侧,且其进料端由外部延伸到整体密闭罩31的内部并与自动称重皮带机34的出料端连续接合;
49.所述除尘风机ⅱ7-2顶部的排风口与外部大气连通,其底部设置有临时储尘仓7-21,且临时储尘仓7-21底部的吸风口通过吸气管路同时与一对抽气管路a和一对抽气管路b连接;
50.所述离心输尘管路a4-1和离心输尘管路b4-2的结构相同,均由柔性骨架风管42、离心扇叶41和固定支架43组成,多个离心扇叶41均匀的分布于柔性骨架风管42的内部,且通过多个对应的固定支架43与柔性骨架风管42的内侧壁连接;所述离心输尘管路a4-1的进风侧和出风侧分别与除尘风机ⅰ7-1的集尘室和除尘风机ⅱ7-2的临时储尘仓7-21贯通连接,所述离心输尘管路b4-2的进风侧和出风侧分别与除尘风机ⅱ7-2的临时储尘仓7-21和包装料斗10的进料口贯通连通;
51.所述控制器13-3分别与图像采集卡13-2、控制液压装置a14-1伸缩的电磁换向阀a、步进电机、控制液压装置b14-3伸缩的电磁换向阀b、散装机9、除尘风机ⅰ7-1、除尘风机ⅱ7-2、振动电机a8-1、离心扇叶41、包装料斗10中的卸料阀、电磁阀a、电磁阀b、自动称重皮带机34、包装输送机33和物料输送机35连接。
52.为了保证连接强度,所述环形气幕吸尘罩21的上端通过周向均匀分布的三根金属杆22-4与伸缩管ⅱ11-2内筒的筒身固定连接;为了保证环形隔尘吸尘装置能够有效地除去散装机下料时产生的粉尘,提高生产线处的空气质量,避免粉尘的飞扬,在伸缩管ⅱ11-2处于最长状态时,环形气幕吸尘罩21的底部位于伸缩管ⅱ11-2底部上方的10-15cm处。
53.为了提高除尘风机的集尘效果,所述除尘风机ⅰ7-1的外部安装有振动电机b8-2,所述这除尘风机ⅱ7-2的外部安装有振动电机c8-3;所述振动电机b8-2和振动电机c8-3均与控制器13-3连接。
54.作为一种优选,所述液压装置14为液压油缸。
55.为了方便选择工作模式,还包括控制面板,所述控制面板上设置有散装模式选择按键和自动包装模式选择按键,散装模式选择按键和自动包装模式选择按键均与控制器13-3连接。
56.本发明中,通过自动定位装置的设置,可以通过红外扫描仪对干混砂浆生产线下料处车辆的驶入情况进行自动扫描,并能通过图像采集卡利用实时传输的图像判断车辆是否为干混砂浆运输车,这样,可有效避免了其他车辆驶入带来的误判;另外,在运输车驶入
且停车后,红外扫描仪能够自动扫描运输车进料口图像并传输至图像采集卡,以便于图像采集卡能够计算出所需伸缩的距离和所需弯曲的角度数据;通过在伸缩管ⅰ内筒的顶端与其外筒的顶端之间设置液压装置a,在伸缩管ⅱ内筒的底端与其外筒的底端之间设置液压装置b,可以自动化的实伸缩管ⅰ和伸缩管ⅱ的伸缩过程;通过在定位管中设置有由多个定位球、多个竖连杆、多个横连杆和多个步进电机,并使定位球通过横向杆与高强度金属波纹管的内侧壁固定连接,可以自动化的调节定位管的弯曲度,从而能适应不同位置的定位需求;通过控制器的设置能够根据所需伸缩的距离和所需弯曲的角度数据控制对应的液压装置进行一定行程的伸缩,从而保证了散装机出料口所连接的管路能够伸入到车辆的进料口内。相较于传统方式散装机进料口位置固定、车辆进料口较小,需要干混砂浆运输车多次调整位置来保证物料的装车的方式,本发明具有操作过程便捷、自动化程度高、人工干预操作较少、反应迅速的优点。通过环形隔尘吸尘装置的设置,可以利用外侧环形罩体上的若干个气幕发生器产生的环形气幕有效粉尘的外溢,同时,能利用内侧的内罩体从多角度吸除装料过程中逸散的粉尘,这样,便实现了隔尘吸尘的功能;相较于传统吸尘罩距离较远、吸尘方向单一、难以完全除去扬尘的方式,本发明可有效避免粉尘飘散至周围的环境中,同时,能使未被一次吸降的粉尘在气幕内悬浮以便于被再次吸除,其具有除尘效率高、除尘效果好、无粉尘逸散现象的优点。通过密闭式自动包装机的设置,能够实现包装运输、砂料装卸、袋装砂料运输过程的全自动化操作,并能粉尘回收及再利用过程;利用设置在自动称重皮带机上的位置检测传感器对包装袋是运输到包装料斗下方进行检测,同时,利用设置在自动称重皮带机上的荷重单元检测包装袋内的砂料质量,能方便的实现包装料斗中砂料的自动卸料和停止卸料的操作,进而极大地提升了自动化程度,这样,不仅减少了现场工人的劳动负荷,还避免了工人与粉尘的直接接触,保障了现场工人的身体健康;通过分别安设于包装料斗底部两侧的一对侧吸罩a,可以通过与卸料阀同步工作的方式来有效减少包装过程中粉尘的产生,同时在整体密闭罩底部与包装输送机、物料输送机接触的开口处内侧设置了一对侧吸罩b,可以使其在自动包装作业过程中全程保持开启状态,进而能有效避免了自动包装过程中粉尘通过开口泄露至外部环境的情况发生,相较于传统工人手动包装、运输方式,具有节省人力、操作过程简便、自动化程度高、无粉尘接触等优点。通过离心输尘管路a的设置,可以利用设置于柔性骨架风管中的多个离心扇叶来将除尘风机ⅰ底部集尘室中的粉尘输送到除尘风机ⅱ底部的临时储尘仓中,实现了粉尘的集中式回收;通过离心输尘管路b的设置,可以利用设置于柔性骨架风管中的多个离心扇叶来将临时储尘仓中粉尘输送到包装料斗中,进而实现了粉尘的有效回收再利用过程;与传统螺旋输送机的输送方式相比,离心输尘管路能够更加有效地输送粉尘,同时,利用多个离心扇叶有效避免了粉尘堵塞于管路内部的情况发生,再者,柔性骨架管路能够随意弯曲,适用于多种工作环境,相较于传统工艺具有易于铺设、不易漏尘的优点,提高了干混砂浆物料的回收利用率。
57.本发明还提供了一种卸料仓自动定位高效除尘与粉尘循环利用方法,包括一种卸料仓自动定位高效除尘与粉尘循环利用系统,还包括以下步骤:
58.当散装模式选择按键按下时,散装模式选择按键向控制器13-3发出散装模式选择信号,控制器13-3接收到散装模式选择信号后执行步骤一;当自动包装模式选择按键按下时,自动包装模式选择按键向控制器13-3发出自动包装模式选择信号,控制器13-3接收动包装模式选择信号后执行步骤二;
59.步骤一:散装模式启动:
60.s11:通过红外扫描仪13-1实时监测散装机9下方车辆的进入情况,当车辆驶入生产线时,红外扫描仪13-1自动扫描识别车辆属性,并将扫描到的车辆图像传输至图像采集卡13-2处,由图像采集卡13-2判断车辆是否符合设定特征,若车辆为干混砂浆运输车,且保持停止状态达10s以上时,执行s12;
61.s12:通过红外扫描仪13-1继续扫描车辆进料口的图像信息,并将数据传输至图像采集卡13-2,由图像采集卡13-2对图像处理后发送给控制器13-3;
62.s13:当控制器13-3接收到数据后,先确定车辆进料口的位置信息,并自动计算出伸缩管ⅰ11-1和伸缩管ⅱ11-2所需伸缩的距离,以及定位管12所需弯曲的角度,再根据距离和角度数据生成对应的控制信息;然后,先向电磁换向阀a发出对应的控制信号,通过控制液压装置a14-1伸缩部分的伸缩来使伸缩管ⅰ11-1进行伸缩动作,直至达到指定距离时停止;再向对应的步进电机发出对应的控制信号,通过对应步进电机的来驱动其上方对应竖连杆14-4的旋转,进而带动该竖连杆14-4上端的定位球14-2和横连杆14-5进行旋转,以带动高强度金属波纹管14-6内侧壁上的一个部分发生移动,通过多个横连杆14-5来带动高强度金属波纹管14-6内侧壁上的多点进行移动,从而使定位管12进行弯曲动作,直至达到指定的弯曲角度,且伸缩管ⅱ11-2的底部位于车辆进料口的上方时停止;最后,向电磁换向阀b发出对应的控制信号,通过控制液压装置b14-3伸缩部分的伸缩来使伸缩管ⅱ11-2进行伸缩动作,直至伸缩管ⅱ11-2的底端伸入至干混砂浆运输车进料口顶盖下方10cm处时停止;完成上述所有操作后,执行s14;
63.s14:控制器13-3发送下料信号至散装机9、发送工作信号到除尘风机ⅰ7-1,控制散装机9在设定时间内进行下料作业,同时,同步控制除尘风机ⅰ7-1工作,通过柔性气流管ⅰ22-1向若干个气幕发生器22-3供入高速气流并于内罩体外围形成环形气幕,以防止粉尘外溢,通过柔性气流管ⅱ22-2将环形气幕内侧的粉尘吸到除尘风机ⅰ7-1底部的集尘室进行收集;
64.s15:当散装下料作业结束后,按照s13的逆操作过程控制自动定位装置1复位至原始位置;
65.步骤二:自动包装模式启动;
66.s21:控制器13-3发送控制信号控制自动称重皮带机34、包装输送机33、物料输送机35和除尘风机ⅱ7-2开启,包装输送机33启动后自动运输包装袋至自动称重皮带机34处,并经自动称重皮带机34继续输送;同时,控制电磁阀b开启,以在整个自动包装过程中利用一对侧吸罩b32-2对整体密闭罩31下端开口处的粉尘进行同步吸收;
67.s22:利用设置在自动称重皮带机34上的位置检测传感器在包装袋运输至包装料斗10底部出料口下方时向控制器13-3发送包装到位信号,控制器13-3接收到包装到位信号后控制自动称重皮带机34停止运行,并控制包装料斗10中的卸料阀开启设定时间进行下料,控制电磁阀a开启以在下料过程中利用一对侧吸罩a32-1对包装料斗10底部出料口处产生的粉尘进行同步吸收,同时,利用自动称重皮带机34上的荷重单元将实时监测皮带上方的质量信号,并实时发送给控制器13-3,控制器13-3根据重量信号获得物料质量m,当物料质量m达到设定质量m0后,控制包装料斗10中的卸料阀关闭以停止包装下料作业,并控制电磁阀a关闭以停止吸尘作业,控制自动称重皮带机34继续运动,经物料输送机35将包装完成
的物料输送至整体密闭罩31的外侧;持续这一过程直至完成所有包装袋的自动包装作业。
68.为了实现粉尘的有效回收,在步骤一的s14中,当下料作业持续设定时间后,通过控制器13-3控制离心输尘管路a4-1中的多个离心扇叶41启动,利用柔性骨架风管42将除尘风机ⅰ7-1底部集尘室中的粉尘输送至除尘风机ⅱ7-2底部的临时储尘仓7-21中。
69.为了实现粉尘的有效回收,在步骤二的s22中,当下料作业持续设定时间后,通过控制器13-3控制离心输尘管路b4-2中的多个离心扇叶41启动,利用柔性骨架风管42将除尘风机ⅱ7-2底部临时储尘仓7-21中的粉尘输送至包装料斗10中。
70.本方法步骤简单,自动化程度高,环保性能好,不仅可自动化的实现散装作业和自动包装作业,还能在作业过程中对粉尘进行有效的回收和再利用。
71.实施例1:
72.本实施例中整体系统的操作流程如下所示:
73.①
:储存于砂浆罐体5中的干混砂浆原料通过振动电机a8-1的振动作用下落入气动三通分料器6中,并通过物料输送管路b流入散装机9,或者通过物料输送管路c流入包装料斗10亦或者同时流入二者中;
74.②
:当散装机9开启时,物料通过气动三通分料器6流入散装机9,并通过图像采集装置13实时监测散装机9下方车辆的进入情况、车料进料口的情况,并通过控制器13-3进行车辆进料口位置信息的确认,再生成对应的控制信号来控制伸缩管ⅰ11-1和伸缩管ⅱ11-2的伸缩行程,控制位管12的弯曲角度,从而使得伸缩管ⅱ11-2的底部可以伸入干混砂浆运输车内部,保证物料能够准确无误地进入运输车,同时,确保伸缩管ⅱ11-2的底部伸入车辆顶层10cm内,能够减少粉尘的飞扬;
75.③
:当自动定位装置1完成定位时,由于环形隔尘吸尘装置2固定于自动定位装置1底部,因此其将随自动定位装置1发生位移到达干混砂浆运输车进料口上部,当完成定位后,控制器13-3控制散装机9开始下料后,同步控制除尘风机ⅰ7-1工作,这样,环形隔尘吸尘装置2随散装机9同步的开启工作,外侧环形罩体上的若干个气幕发生器21-3将形成环形风幕,将粉尘隔绝在内部,避免了产生的粉尘逸散至生产线其他区域;内罩体上连接的柔性气流管ⅱ22-2同时进行粉尘的收集作业,以吸除进料过程中产生的粉尘,同时部分未能一次性吸出的粉尘将被隔绝于气幕内,并被再次吸除,保证了下料过程中产生的粉尘能被完全吸出;
76.④
:当包装料斗10开启时,物料通过气动三通分料器6流入包装料斗10中,此时包装输送机33将持续向整体密闭罩31内部输送原包装袋,经由自动称重皮带机34上设置的位置检测传感器检测到位情况进行下料控制,再通过荷重单元称量从上方包装料斗10落下的物料质量,当达到预设质量时将停止下料,并由物料输送机35输送至整体密闭罩31外;在下料过程中,安设于包装料斗10左右两侧的两个侧吸罩b32-2将同步吸尘,避免下料过程产生的粉尘逸散,安设于整体密闭罩31下方左右两侧开口处内侧的两个侧吸罩a32-1在下料过程中也将持续开启,避免粉尘流向整体密闭罩31外侧;
77.⑤
:环形隔尘吸尘装置2吸出的粉尘汇集于除尘风机ⅰ7-1底部的集尘室中,利用离心输尘管路a4-1将除尘风机ⅰ7-1底部的粉尘输送到除尘风机ⅱ7-2底部的临时储尘仓7-21中,利用利用离心输尘管路b4-2将临时储尘仓7-21中的粉尘输送到包装料斗10中,从而使得砂浆原料得到了有效的回收,还减少了除尘风机ⅰ7-1、除尘风机ⅱ7-2卸灰这一步骤。
78.实施例2:
79.自动定位装置1能够按照如下步骤进行自动定位连接干混砂浆运输车的进料口并进行输料:
80.①
:红外扫描仪13-1能够实时监测散装机9下方车辆进入情况,当车辆驶入生产线时,将自动扫描识别车辆属性,将图像传输至图像采集卡13-2处,由图像采集卡13-2处理后发送给控制器13-3,控制器13-3由此判断车辆是否为干混砂浆运输车;若车辆符合设定特征,将自动进行下一步操作;
81.②
:当干混砂浆运输车保持停止状态达10s以上时,红外扫描仪13-1将扫描车辆进料口图像信息,并将数据传输至图像采集卡13-2处,由图像采集卡13-2处理后发送给控制器13-3,控制器13-3由此确定车辆进料口位置,并自动计算出伸缩管ⅰ11-1、伸缩管ⅱ11-2所需伸缩的距离与定位管12所需弯曲的角度,再生成对应的控制器,随后通过控制器13-3依次发送信号给控制液压装置a14-1的电磁换向阀a、步进电机,进而产生需要的伸缩位移与弯曲的角度;
82.③
:当电磁换向阀a接收到信号后,其接通液压油源与液压装置a14-1无杆腔之间的油路,高压油进入到无杆腔内并推动活塞杆向外部伸出,进而使伸缩管ⅰ11-1进行伸长操作,当伸长位移至指定距离时,控制电磁换向阀a切断液压油源与液压装置a14-1无杆腔之间的油路,使伸缩管ⅰ11-1保持该伸长状态;随后,对应的步进电机接收到信号后,其驱动其上方的竖连杆旋转,进而带动其上方定位球和横连杆发生旋转,继而带动高强度金属波纹管内侧壁上的某一点移动,该过程中,通过控制不同位置步进电机的旋转角度来使定位管12的角度发生设定的弯曲,当弯曲至指定角度时,停止对步进电机的控制,使定位管12保持该弯曲状态;最后,电磁换向阀b接收到信号后,其接通液压油源与液压装置b14-3无杆腔之间的油路,高压油进入到无杆腔内并推动活塞杆向外部伸出,进而使伸缩管ⅱ11-2进行伸长操作,当伸长位移至指定距离时,控制电磁换向阀b切断液压油源与液压装置b14-3无杆腔之间的油路,使伸缩管ⅱ11-2保持该伸长状态;液压装置b14-3控制伸缩管ⅱ11-2进行伸长操作,当伸缩管ⅱ11-2的底部伸入至车辆进料口顶盖下方10cm处时,停止伸长;完成所有操作后,控制器13-3发送信号至散装机9处开始下料;
83.④
:当完成下料后,自动定位装置1将按照以上步骤的逆操作回归至原位置。