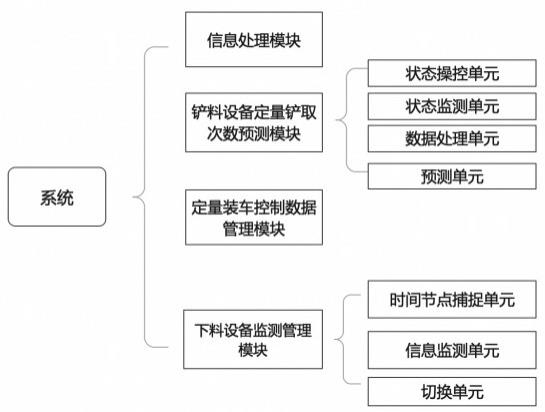
1.本发明涉及定量装车控制技术领域,具体为煤电企业灰渣固体废弃物的定量装车控制系统。
背景技术:2.传统的火电厂固体废弃物处理方式为填埋及露天堆放,不仅会占用大量珍贵的土地资源,而且煤灰中残留的含硫化合物等具备毒性和污染性的物质,会逐渐流向地下土层,造成严重的污染并逐渐扩散,最终导致生态环境遭到毁灭性打击。基于此,对固体废弃物必须做出无害化处理,此举是一切的前提,未经处理的废弃物不能转移到任何地方;再根据一定的原则将经过处理废弃物运送到指定地点,中途必须保证安全,避免出现遗失、泄漏等现象;第三,综合化利用。
3.目前传统火电行业灰渣固体废弃物大多仍采用人工装车的方式,人工装车存在装车量误差较大、人工成本较高的问题,无形中增加了企业运营成本;人工装车作业流程过于粗犷,造成大量的灰渣扬尘,污染环境;灰库车辆的定量装载,可以有效避免厂内粉尘扬尘风险,有效保护人员健康和厂内环境,保障作业人员的人身安全问题,预防职业病。
技术实现要素:4.本发明的目的在于提供煤电企业灰渣固体废弃物的定量装车控制系统,以解决上述背景技术中提出的问题。
5.为了解决上述技术问题,本发明提供如下技术方案:煤电企业灰渣固体废弃物的定量装车控制系统,控制系统包括:信息处理模块、定量装车控制数据管理模块、铲料设备定量铲取次数预测模块、下料设备监测管理模块;信息处理模块,用于存储所有待进行灰渣固体废弃物装车的运输车辆信息,对运输车辆进行车牌号识别和放灰权限判断;定量装车控制数据管理模块,用于接收信息处理模块中的数据,获取对运输车辆进行定量装车的控制数据;铲料设备定量铲取次数预测模块,用于接收定量装车控制数据管理模块中的数据,用于操控铲料设备向下料设备的运输管道处输送灰渣固体废弃物;用于对下料设备中完成的抽灰工作流程进行状态监测;用于对铲料设备进行定量铲取次数的预测;下料设备监测管理模块,用于提取对运输车辆设置的装车设定重量;开启下料设备运输管道与运输车辆车箱之间连接的放料阀门,自动控制下料设备运输管道与运输车辆车箱之间呈现放料角度。
6.进一步的,信息处理模块包括车辆识别单元、权限判断单元;车辆识别单元,用于每当监测到有运输车辆行驶至某个灰库的车牌识别区域时,对运输车辆进行车牌号识别,基于识别出的车牌号信息从控制系统内调取运输车辆的皮重数据、待装灰种;
权限判断单元,用于接收车辆识别单元中的数据,将对运输车辆提取的待装灰种与某个灰库之间实行入库名匹配,若匹配失败,判断运输车辆进错库,不赋予放灰权限;若匹配成功,判断运输车辆正确入库,赋予放灰权限。
7.进一步的,定量装车控制数据管理模块包括:获取当地交管局规定的罐车上路重量,允许根据煤电企业厂内预设时期制定的销售政策设置放灰调整量,根据公式:;其中,表示运输车辆对应的皮重,表示最终对运输车辆设置的装车设定重量。
8.进一步的,铲料设备定量铲取次数预测模块包括状态操控单元、状态监测单元、数据处理单元、预测单元;状态操控单元,用于操控铲料设备不断的将每固定铲满一次的灰渣固体废弃物向下料设备的运输管道处输送,直至在计量装置中显示累计抽取的灰渣固体废弃物的实时重量达到装车设定重量时,停止铲料设备的铲灰工作;状态监测单元,用于接收状态操控单元中的数据,对铲料设备将每固定铲满一次灰渣固体废弃物向下料设备的运输管道处输送的过程进行状态监测;数据处理单元,用于提取历史工作运行监测数据,计算每次定量铲取的灰渣固体废弃物重量与实际抽取存储的灰渣固定废弃物重量之间重量偏差值,分析重量偏差值与完整抽灰工作流程中的影响因子之间的规律关系;预测单元,用于接收状态操控单元、状态监测单元、数据处理单元中的数据,基于重量偏差值与完整抽灰工作流程中的影响因子之间的规律关系,对铲料设备进行定量铲取次数的预测。
9.进一步的,状态监测单元包括:提取对运输车辆设置的装车设定重量;将下料设备的运输管道对铲料设备一次定量铲取并放置的灰渣固体废弃物实现最大重量抽取的过程设为一次完整抽灰工作流程;获取铲料设备每次定量铲取的灰渣固体废弃物重量,对铲料设备每次放置重量为的灰渣固定废弃物的位置进行监测获取;捕捉重量为的灰渣固定废弃物的放置位置与下料设备的运输管道横截面之间的最短距离,捕捉重量为的灰渣固定废弃物在放置位置处所形成的灰堆与下料设备运输管道横截面之间的最大相对面积;同时捕捉在计量装置中显示下料设备每次实际抽取存储的灰渣固定废弃物重量;因在实际工作过程中,下料设备的运输管道随着灰库内部,灰渣固体废弃物的存放堆积情况,与铲料设备定量铲取的灰渣固体废弃物放置区域之间的空间位置会发生变化,导致管道实际能抽取的废弃物发生变化,捕捉上述数据,是为后续预测铲料设备定量铲取次数时所需的必要技术铺垫。
10.进一步的,数据处理单元包括:提取历史工作运行监测数据,捕捉得到每次定量铲取的灰渣固体废弃物重量与实际抽取存储的灰渣固定废弃物重量之间的重量偏差值;同时获取在每一次完
整抽灰工作流程中捕捉到的最短距离和最大相对面积;对每一次完整抽灰工作流程中的影响因子进行计算,;提取每一次完整抽灰工作流程中的重量偏差值与影响因子,作为一组数据,进行线性拟合,得到重量偏差值与影响因子之间满足的线性关系;其中,r表示重量偏差值与影响因子之间的相关系数,b表示常数。
11.进一步的,预测单元包括:构建铲料设备定量铲取次数的实时预测模型,实时对每次完整抽灰工作流程中的影响因子进行捕捉输入,得到对铲料设备预测的动态铲取次数n,向铲料设备发送提醒控制指令,控制铲料设备在完成最后一次定量铲取时自动停止;对计量装置中显示的灰渣固定废弃物重量进行捕捉,当达到对运输车辆设置的装车设定重量时,停止下料设备运输管道的抽灰工作,根据此时实时预测模型中得到的n,以及铲料设备此时实际完成的铲取次数对实时预测模型中的相关系数进行调整。
12.进一步的,下料设备监测管理模块包括时间节点捕捉单元、信息监测单元、切换单元;时间节点捕捉单元,用于捕捉当车箱内灰渣固体废弃物形成的灰堆高度达到虚位预警高度线时,下料设备运输管道持续放料的时间节点;信息监测单元,用于接收时间节点捕捉单元中的数据,将时间节点作为控制下料设备切换运输管道与运输车辆车箱之间呈现放料角度的时间节点,对下料设备的下料时间进行监测;切换单元,用于接收信息监测单元中的数据,自动控制下料设备运输管道与运输车辆车箱连接之处的转向;实现自动控制下料设备在运输车辆车箱内均匀下料。
13.进一步的,时间节点捕捉单元包括:提取对运输车辆设置的装车设定重量;开启下料设备运输管道与运输车辆车箱之间连接的放料阀门,捕捉单位时间t内流经下料设备运输管道横截面的灰渣固体废弃物的体积;设置下料设备运输管道与运输车辆车箱之间呈现的初始放料角度为垂直角度,即,下料设备运输管道横截面平行于运输车辆车箱的底面;获取运输车辆对应待装灰种的密度,获取单位时间t内流经下料设备运输管道横截面的灰渣固体废弃物的重量;计算得到下料设备基于每单位时间t放料的速度完成放量装车设定重量的标准时间;基于运输车辆车箱高度,设置下料设备运输管道与车箱内灰渣固体废弃物之间的虚位预警高度线;安装监控摄像装置,提取历史放料监测数据,捕捉每当垂直于运输车辆车箱底部持续放料,直至车箱内灰渣固体废弃物形成的灰堆高度达到虚位预警高度线
时,灰堆在车箱底面所占的最大圆面积;计算得到车箱内灰渣固体废弃物形成的灰堆高度达到虚位预警高度线时,下料设备运输管道持续放料的时间为: 将时间作为控制下料设备切换运输管道与运输车辆车箱之间呈现放料角度的时间节点,对下料设备的下料时间进行监测;由于在对运输车辆车箱下料过程中,会出现因下料口的输送管道对同一片区域持续下料,导致该片区域内出现灰料堆积形成两边低中间高的“小山堆”,且当“小山堆”的中间高度达到车箱预警高位线,会导致下料中断,而此时计量装置显示车箱内并未实际装满到达车设定重量需要,往往需要通过操控运输车辆达到摇匀装载灰料进而继续放料的现象,所以对下料设备进行下料时间监测,是为了在车箱内堆积的“小山堆”快要到达车箱预警高位线,操控下料设备切换运输管道与运输车辆车箱之间呈现的放料角度,避免下料中断,减少对运输车辆的外带附加性操控,提高工作流程的智能自动化。
14.进一步的,切换单元包括:设置每次角度切换的过渡时间tr;当监测到下料设备持续垂直于车箱底面放料的时间达到-tr,开始控制下料设备运输管道向左转进行角度切换,直至切换后出现的放料位置处于垂直放料角度对应的最大圆面积之外停止;保持持续放料一段时间后,开始控制下料设备运输管道向右转进行角度切换,直至切换后出现的放料位置处于垂直放料角度对应的最大圆面积之外停止;其中,运输管道在左右角度进行放料的持续时长分别为。
15.与现有技术相比,本发明所达到的有益效果是:本发明主要作用于粉煤灰的装料运输环节,系统实现业务流程高效、透明管理,体现现代工业控制与现代企业管理技术深度融合的发展理念;本发明可实现对现场设备的精准控制,实现对下料的精准把控,达到“量到即停”的效果,大大提高了现场的安全系数,避免了“扬尘“、”冒灰“等生产问题,系统的高效率同时也极大程度的创造了更多经济效益;在本发明中,可解决在对运输车辆车箱下料过程中,因下料口对同一片区域持续下料,导致该片区域内出现灰料堆积形成两边低中间高的“小山堆”,且因“小山堆”的中间高度达到车箱预警高位线,导致下料中断,需要操控运输车辆摇匀装载灰料的现象,本发明可实现智能切转下料口在运输车辆车箱内的下料方向,实现对运输车辆的均匀下料,进一步实现智能化定量装载控制。
附图说明
16.附图用来提供对本发明的进一步理解,并且构成说明书的一部分,与本发明的实
施例一起用于解释本发明,并不构成对本发明的限制。在附图中:图1是本发明煤电企业灰渣固体废弃物的定量装车控制系统的结构示意图;图2是本发明煤电企业灰渣固体废弃物的定量装车控制系统中,控制下料设备运输管道向运输车辆车箱放料的示意图。
具体实施方式
17.下面将结合本发明实施例中的附图,对本发明实施例中的技术方案进行清楚、完整地描述,显然,所描述的实施例仅仅是本发明一部分实施例,而不是全部的实施例。基于本发明中的实施例,本领域普通技术人员在没有做出创造性劳动前提下所获得的所有其他实施例,都属于本发明保护的范围。
18.请参阅图1-图2,本发明提供技术方案:煤电企业灰渣固体废弃物的定量装车控制系统,控制系统包括:信息处理模块、定量装车控制数据管理模块、铲料设备定量铲取次数预测模块、下料设备监测管理模块;信息处理模块,用于存储所有待进行灰渣固体废弃物装车的运输车辆信息,对运输车辆进行车牌号识别和放灰权限判断;其中,信息处理模块包括车辆识别单元、权限判断单元;车辆识别单元,用于每当监测到有运输车辆行驶至某个灰库的车牌识别区域时,对运输车辆进行车牌号识别,基于识别出的车牌号信息从控制系统内调取运输车辆的皮重数据、待装灰种;权限判断单元,用于接收车辆识别单元中的数据,将对运输车辆提取的待装灰种与某个灰库之间实行入库名匹配,若匹配失败,判断运输车辆进错库,不赋予放灰权限;若匹配成功,判断运输车辆正确入库,赋予放灰权限;定量装车控制数据管理模块,用于接收信息处理模块中的数据,获取对运输车辆进行定量装车的控制数据;其中,定量装车控制数据管理模块包括:获取当地交管局规定的罐车上路重量,允许根据煤电企业厂内预设时期制定的销售政策设置放灰调整量,根据公式:;其中,表示运输车辆对应的皮重,表示最终对运输车辆设置的装车设定重量;铲料设备定量铲取次数预测模块,用于接收定量装车控制数据管理模块中的数据,用于操控铲料设备向下料设备的运输管道处输送灰渣固体废弃物;用于对下料设备中完成的抽灰工作流程进行状态监测;用于对铲料设备进行定量铲取次数的预测;其中,铲料设备定量铲取次数预测模块包括状态操控单元、状态监测单元、数据处理单元、预测单元;状态操控单元,用于操控铲料设备不断的将每固定铲满一次的灰渣固体废弃物向下料设备的运输管道处输送,直至在计量装置中显示累计抽取的灰渣固体废弃物的实时重量达到装车设定重量时,停止铲料设备的铲灰工作;状态监测单元,用于接收状态操控单元中的数据,对铲料设备将每固定铲满一次灰渣固体废弃物向下料设备的运输管道处输送的过程进行状态监测;
其中,状态监测单元包括:提取对运输车辆设置的装车设定重量;将下料设备的运输管道对铲料设备一次定量铲取并放置的灰渣固体废弃物实现最大重量抽取的过程设为一次完整抽灰工作流程;获取铲料设备每次定量铲取的灰渣固体废弃物重量,对铲料设备每次放置重量为的灰渣固定废弃物的位置进行监测获取;捕捉重量为的灰渣固定废弃物的放置位置与下料设备的运输管道横截面之间的最短距离,捕捉重量为的灰渣固定废弃物在放置位置处所形成的灰堆与下料设备运输管道横截面之间的最大相对面积;同时捕捉在计量装置中显示下料设备每次实际抽取存储的灰渣固定废弃物重量;数据处理单元,用于提取历史工作运行监测数据,计算每次定量铲取的灰渣固体废弃物重量与实际抽取存储的灰渣固定废弃物重量之间重量偏差值,分析重量偏差值与完整抽灰工作流程中的影响因子之间的规律关系;其中,数据处理单元包括:提取历史工作运行监测数据,捕捉得到每次定量铲取的灰渣固体废弃物重量与实际抽取存储的灰渣固定废弃物重量之间的重量偏差值;同时获取在每一次完整抽灰工作流程中捕捉到的最短距离和最大相对面积;对每一次完整抽灰工作流程中的影响因子进行计算,;提取每一次完整抽灰工作流程中的重量偏差值与影响因子,作为一组数据,进行线性拟合,得到重量偏差值与影响因子之间满足的线性关系;其中,r表示重量偏差值与影响因子之间的相关系数,b表示常数;预测单元,用于接收状态操控单元、状态监测单元、数据处理单元中的数据,基于重量偏差值与完整抽灰工作流程中的影响因子之间的规律关系,对铲料设备进行定量铲取次数的预测;其中,预测单元包括:构建铲料设备定量铲取次数的实时预测模型,实时对每次完整抽灰工作流程中的影响因子进行捕捉输入,得到对铲料设备预测的动态铲取次数n,向铲料设备发送提醒控制指令,控制铲料设备在完成最后一次定量铲取时自动停止;对计量装置中显示的灰渣固定废弃物重量进行捕捉,当达到对运输车辆设置的装车设定重量时,停止下料设备运输管道的抽灰工作,根据此时实时预测模型中得到的n,以及铲料设备此时实际完成的铲取次数对实时预测模型中的相关系数进行调整;下料设备监测管理模块,用于提取对运输车辆设置的装车设定重量;开启下料设备运输管道与运输车辆车箱之间连接的放料阀门,自动控制下料设备运输管道与运输车辆车箱之间呈现放料角度;
其中,下料设备监测管理模块包括时间节点捕捉单元、信息监测单元、切换单元;时间节点捕捉单元,用于捕捉当车箱内灰渣固体废弃物形成的灰堆高度达到虚位预警高度线时,下料设备运输管道持续放料的时间节点;其中,时间节点捕捉单元包括:提取对运输车辆设置的装车设定重量;开启下料设备运输管道与运输车辆车箱之间连接的放料阀门,捕捉单位时间t内流经下料设备运输管道横截面的灰渣固体废弃物的体积;设置下料设备运输管道与运输车辆车箱之间呈现的初始放料角度为垂直角度,即,下料设备运输管道横截面平行于运输车辆车箱的底面;如图2所示,下料设备运输管道向运输车辆车箱之间是垂直车箱放料的;获取运输车辆对应待装灰种的密度,获取单位时间t内流经下料设备运输管道横截面的灰渣固体废弃物的重量;计算得到下料设备基于每单位时间t放料的速度完成放量装车设定重量的标准时间;基于运输车辆车箱高度,设置下料设备运输管道与车箱内灰渣固体废弃物之间的虚位预警高度线;安装监控摄像装置,提取历史放料监测数据,捕捉每当垂直于运输车辆车箱底部持续放料,直至车箱内灰渣固体废弃物形成的灰堆高度达到虚位预警高度线时,灰堆在车箱底面所占的最大圆面积;计算得到车箱内灰渣固体废弃物形成的灰堆高度达到虚位预警高度线时,下料设备运输管道持续放料的时间为: 将时间作为控制下料设备切换运输管道与运输车辆车箱之间呈现放料角度的时间节点,对下料设备的下料时间进行监测;例如说,下料设备基于每单位时间1min放料的速度完成放量装车设定重量的标准时间;基于运输车辆装载的是一级粉煤灰的密度换算得到一立方米为0.5kg;所以每单位时间1min放料能放料2立方米;捕捉到每当垂直于运输车辆车箱底部持续放料,直至车箱内灰渣固体废弃物形成的灰堆高度达到虚位预警高度线4m时,灰堆在车箱底面所占的最大圆面积为6平方米;下料设备运输管道持续放料的时间min;所以在持续放料4min时控制下料设备切换运输管道与运输车辆车箱之间呈现放料角度;信息监测单元,用于接收时间节点捕捉单元中的数据,将时间节点作为控制下料
设备切换运输管道与运输车辆车箱之间呈现放料角度的时间节点,对下料设备的下料时间进行监测;切换单元,用于接收信息监测单元中的数据,自动控制下料设备运输管道与运输车辆车箱连接之处的转向;实现自动控制下料设备在运输车辆车箱内均匀下料;其中,切换单元包括:设置每次角度切换的过渡时间tr;当监测到下料设备持续垂直于车箱底面放料的时间达到-tr,开始控制下料设备运输管道向左转进行角度切换,直至切换后出现的放料位置处于垂直放料角度对应的最大圆面积之外停止;保持持续放料一段时间后,开始控制下料设备运输管道向右转进行角度切换,直至切换后出现的放料位置处于垂直放料角度对应的最大圆面积之外停止;其中,运输管道在左右角度进行放料的持续时长分别为。
19.需要说明的是,在本文中,诸如第一和第二等之类的关系术语仅仅用来将一个实体或者操作与另一个实体或操作区分开来,而不一定要求或者暗示这些实体或操作之间存在任何这种实际的关系或者顺序。而且,术语“包括”、“包含”或者其任何其他变体意在涵盖非排他性的包含,从而使得包括一系列要素的过程、方法、物品或者设备不仅包括那些要素,而且还包括没有明确列出的其他要素,或者是还包括为这种过程、方法、物品或者设备所固有的要素。
20.最后应说明的是:以上所述仅为本发明的优选实施例而已,并不用于限制本发明,尽管参照前述实施例对本发明进行了详细的说明,对于本领域的技术人员来说,其依然可以对前述各实施例所记载的技术方案进行修改,或者对其中部分技术特征进行等同替换。凡在本发明的精神和原则之内,所作的任何修改、等同替换、改进等,均应包含在本发明的保护范围之内。