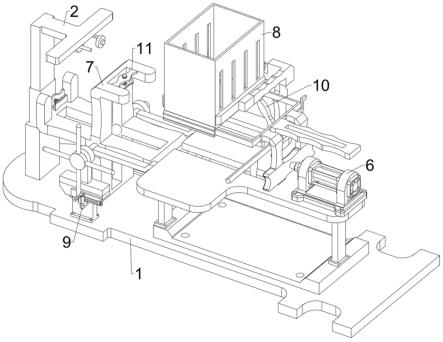
1.本发明涉及一种包装机,尤其涉及一种汽车铅酸蓄电池生产用包装机。
背景技术:2.蓄电池是汽车必不可少的一部分,可分为传统的铅酸蓄电池和免维护型蓄电池,其中酸性蓄电池主要优点是工作电压较高、使用温度宽、高低速率放电性能良好和原料来源丰富,蓄电池在生产加工完成后,需要进行包装。
3.专利授权公告号为cn206984479u的专利公布了一种铅酸蓄电池半自动电池装箱装置,设置于铅酸蓄电池加酸后道生产物流运输包装流水线左右,其特征在于包括:提升气缸、移动气缸、气缸抓手、抓手支撑架、定位气缸、脚踏开关及plc控制柜,所述抓手支撑架设置在蓄电池物流线上方,所述提升气缸的底座固定在抓手支撑架上,且提升气缸位于蓄电池物流线正上方,所述提升气缸的活塞杆端部与移动气缸相接,所述移动气缸上连接有气缸抓手,所述定位气缸位于蓄电池物流线上,且设置在气缸抓手正下方,用于对蓄电池物流线上的电池进行定位,虽然上述专利实现流水线上蓄电池定位后,踩一下脚踏开关,能够使抓手气缸自动下落,抓取电池,同时定位气缸自动下落,实现轻松抓取电池装箱,但上述专利对电池装箱完成后,需要另外使用封箱装置对其进行封箱,从而导致工作效率低下。
4.因此亟需发明一种能够在电池进行装箱的同时,对装箱完成的电池进行封箱的汽车铅酸蓄电池生产用包装机,来解决上述问题很有必要。
技术实现要素:5.为了克服上述专利对电池装箱完成后,需要另外使用封箱装置对其进行封箱的缺点,技术问题:提供一种能够在电池进行装箱的同时,对装箱完成的电池进行封箱的汽车铅酸蓄电池生产用包装机。
6.本发明通过以下技术途径实现:一种汽车铅酸蓄电池生产用包装机,包括有底座、支撑架、滑动件、放置板、支撑杆、推动机构和翻转机构,底座左部固接有支撑架,支撑架上部滑动式设置有滑动件,底座顶部固接有放置板,放置板左侧固接有两根支撑杆,放置板上设置有用于推动电池的推动机构,底座上设置有用于对包装箱进行翻转的翻转机构。
7.更为优选的是,推动机构包括有安装座、气缸、推块和限位块,放置板顶部右侧固接有安装座,安装座内安装有气缸,气缸的伸缩杆上固接有推块,放置板顶部左后侧固接有限位块。
8.更为优选的是,翻转机构包括有支撑座、转轴、转动架和手轮,底座左部前后对称固接有支撑座,支撑座位于支撑架右侧,两个支撑座之间转动式设置有转轴,转轴上固接有转动架,转轴前端固接有手轮。
9.更为优选的是,还包括有用于自动使防护垫进行下料的下料机构,下料机构包括有连接杆、挡板、固定架和下料框,推块顶部固接有两根连接杆,两根连接杆顶部之间固接有挡板,放置板顶部后侧固接有固定架,固定架上部固接有下料框,挡板与下料框下部滑动
式连接。
10.更为优选的是,还包括有用于将手轮卡紧的卡紧机构,卡紧机构包括有固定块、固定套、卡紧件和卡杆,前侧的支撑座前侧固接有固定块,前侧的支撑座前侧固接有固定套,固定套内滑动式设置有卡紧件,手轮与卡紧件接触,卡紧件与固定块之间拆卸式设置有卡杆。
11.更为优选的是,还包括有用于将防护垫推入箱体内的推料机构,推料机构包括有固定座、转动件、推动块、接触块和扭力弹簧,下料框后侧固接有固定座,固定座上转动式设置有转动件,放置板上开有一字槽,转动件底部固接有推动块,推动块穿过一字槽,挡板后侧固接有接触块,接触块向左移动与转动件接触,能够挤压其逆时针转动,接触块向右移动与转动件接触,能够挤压其顺时针转动,转动件与固定座之间连接有扭力弹簧,扭力弹簧套在转动件上。
12.更为优选的是,还包括有用于将箱体压紧的压紧机构,压紧机构包括有支撑板、滑动杆、压块和第二弹性件,转动架上均匀间隔固接有支撑板,支撑板上滑动式设置有滑动杆,滑动杆底端固接有压块,压块与支撑板之间连接有第二弹性件,第二弹性件套在滑动杆上。
13.更为优选的是,还包括有第一弹性件,卡紧件与固定套之间连接有第一弹性件,第一弹性件套在卡紧件上。
14.采用了上述对本发明结构的描述可知,本发明的设计出发点、理念及优点是:1、通过逆时针转动手轮,可以使转动架和包装箱逆时针转动,当包装箱位于滑动件下方时,能够将胶带套在滑动件上进行封箱作业,同时可以将空箱放置于两根支撑杆之间进行装箱作业,从而实现了在电池进行装箱的同时,对装箱完成的电池进行封箱,进而能够提高工作效率。
15.2、通过推块向左移动带动连接杆向左移动,能够使挡板向左移动不再将下料框挡住,此时下料框内能够掉出一个防护垫至电池上方,如此实现了自动下料的功能。
16.3、通过将卡杆取出,能够逆时针转动手轮,使其挤压卡紧件向右移动,当卡紧件向右移动与手轮脱离时,第一弹性件复位带动卡紧件向左移动复位,使得卡紧件再次将手轮抵住,然后将卡杆插回原处,如此能够将手轮固定,从而能够防止转轴和转动架转动,对电池包装作业带来影响。
附图说明
17.图1为本发明的立体结构示意图。
18.图2为本发明的第一种部分立体结构示意图。
19.图3为本发明的第二种部分立体结构示意图。
20.图4为本发明推动机构的部分立体结构示意图。
21.图5为本发明翻转机构的部分立体结构示意图。
22.图6为本发明下料机构的第一种部分立体结构示意图。
23.图7为本发明下料机构的第二种部分立体结构示意图。
24.图8为本发明卡紧机构的部分立体结构示意图。
25.图9为本发明推料机构的第一种部分立体结构示意图。
26.图10为本发明推料机构的第二种部分立体结构示意图。
27.图11为本发明压紧机构的部分立体结构示意图。
28.附图中各零部件的标记如下:1、底座,2、支撑架,3、滑动件,4、放置板,5、支撑杆,6、推动机构,601、安装座,602、气缸,603、推块,604、限位块,7、翻转机构,701、支撑座,702、转轴,703、转动架,704、手轮,8、下料机构,801、连接杆,802、挡板,803、固定架,804、下料框,9、卡紧机构,901、固定块,902、固定套,903、卡紧件,904、第一弹性件,905、卡杆,10、推料机构,1001、固定座,1002、转动件,1003、一字槽,1004、推动块,1005、接触块,1006、扭力弹簧,11、压紧机构,1101、支撑板,1102、滑动杆,1103、压块,1104、第二弹性件。
具体实施方式
29.下面将对本发明实施例中的技术方案进行清楚、完整地描述,显然,所描述的实施例仅是本发明的一部分实施例,而不是全部的实施例。基于本发明中的实施例,本领域普通技术人员在没有做出创造性劳动前提下所获得的所有其它实施例,都属于本发明保护的范围。
30.实施例1
31.一种汽车铅酸蓄电池生产用包装机,参阅图1-图5所示,包括有底座1、支撑架2、滑动件3、放置板4、支撑杆5、推动机构6和翻转机构7,底座1左部通过焊接的方式设置有支撑架2,支撑架2上部滑动式设置有滑动件3,底座1顶部固接有放置板4,放置板4左侧固接有两根支撑杆5,放置板4上设置有推动机构6,推动机构6用于推动电池,底座1上设置有翻转机构7,翻转机构7用于对包装箱进行翻转。
32.参阅图1和图4所示,推动机构6包括有安装座601、气缸602、推块603和限位块604,放置板4顶部右侧固接有安装座601,安装座601内安装有气缸602,气缸602的伸缩杆上固接有推块603,放置板4顶部左后侧固接有限位块604。
33.参阅图1和图5所示,翻转机构7包括有支撑座701、转轴702、转动架703和手轮704,底座1左部前后对称固接有支撑座701,支撑座701位于支撑架2右侧,两个支撑座701之间转动式设置有转轴702,转轴702上固接有转动架703,转轴702前端固接有手轮704。
34.当要使用本装置时,工作人员将电池放到放置板4上,使其后侧与限位块604接触,随后工作人员将防护垫放到电池上方,工作人员再将包装箱放到两根支撑杆5之间,然后将防护垫横放入包装箱内,随后工作人员开启气缸602,气缸602的伸缩杆伸长带动推块603向左移动,推块603向左移动推动电池和防护垫向左移动进入包装箱内,从而完成了对电池的装箱作业,然后工作人员逆时针转动手轮704,手轮704逆时针转动带动转轴702和转动架703逆时针转动,转动架703逆时针转动带动包装箱逆时针转动,当包装箱位于滑动件3下方时,工作人员停止转动手轮704,然后工作人员将胶带套在滑动件3上,再揭开胶带对包装箱进行封箱作业,滑动件3能够前后移动,进而便于工作人员对包装箱进行封箱作业,工作人员在进行封箱作业的同时,可以再次将包装箱放到两根支撑杆5之间,此时气缸602的伸缩杆缩短带动推块603向右移动复位,重复上述操作,能够再次将电池装入箱中,当电池再次完成装箱作业时,前一个包装箱已封箱完成,此时工作人员可以再次逆时针转动手轮704,进而能够使转动架703带动两个包装箱逆时针转动,当未封箱的电池转动于滑动件3下方时,工作人员可再次对其进行封箱作业,同时封箱完成的包装箱逆时针转动到合适位置,从
而能够掉落至底座1上,进而便于工作人员将其取出,重复上述操作,可以再次对电池进行包装作业,当不需要使用本装置后,工作人员将气缸602关闭即可。
35.实施例2
36.在实施例1的基础之上,参阅图1、图6和图7所示,还包括有下料机构8,下料机构8用于自动将防护垫进行下料,下料机构8包括有连接杆801、挡板802、固定架803和下料框804,推块603顶部固接有两根连接杆801,两根连接杆801顶部之间固接有挡板802,放置板4顶部后侧固接有固定架803,固定架803上部固接有下料框804,挡板802与下料框804下部滑动式连接。
37.当要对电池进行包装时,工作人员将防护垫放入下料框804内,当推块603向左移动时,推块603能够带动连接杆801向左移动,连接杆801向左移动带动挡板802向左移动,当挡板802向左移动不再将下料框804挡住时,下料框804内能够掉出一个防护垫至电池上方,如此实现了自动下料的功能,此时挡板802继续向左移动能够再次将下料框804内挡住,推块603继续向左移动则能够将电池和防护垫向左推入包装箱内,当推块603向右移动时,推块603能够带动连接杆801和挡板802向右移动,当挡板802向右移动不再将下料框804挡住时,下料框804内能够再次掉落出一个防护垫,在此过程中,工作人员能够逆时针转动手轮704,进而能够使装箱完成的电池逆时针转动到合适位置后,进行封箱作业,然后工作人员将空箱放到两个支撑杆5上,再将放置板4上的防护垫推入空箱内,随后工作人员能够再次将电池放到放置板4上,重复上述操作,能够再次使防护垫掉落至电池上,然后进行装箱作业。
38.参阅图1和图8所示,还包括有卡紧机构9,卡紧机构9用于将手轮704卡紧,卡紧机构9包括有固定块901、固定套902、卡紧件903、第一弹性件904和卡杆905,前侧的支撑座701前侧固接有固定块901,前侧的支撑座701前侧固接有固定套902,固定套902内滑动式设置有卡紧件903,手轮704与卡紧件903接触,卡紧件903与固定套902之间连接有第一弹性件904,第一弹性件904套在卡紧件903上,卡紧件903与固定块901之间拆卸式设置有卡杆905。
39.初始时,卡紧件903将手轮704抵住,当需要转动手轮704时,工作人员将卡杆905从卡紧件903和固定块901之间取出,然后工作人员能够逆时针转动手轮704,手轮704逆时针转动能够挤压卡紧件903向右移动,第一弹性件904随之被压缩,当卡紧件903向右移动与手轮704脱离时,第一弹性件904能够复位带动卡紧件903向左移动复位,从而能够使卡紧件903再次将手轮704抵住,然后工作人员将卡杆905插回原处,如此能够将手轮704固定,从而能够防止转轴702和转动架703随意转动,对电池包装作业带来影响。
40.参阅图1、图9和图10所示,还包括有推料机构10,推料机构10用于将防护垫推入箱体内,推料机构10包括有固定座1001、转动件1002、推动块1004、接触块1005和扭力弹簧1006,下料框804后侧固接有固定座1001,固定座1001上转动式设置有转动件1002,放置板4上开有一字槽1003,转动件1002底部固接有推动块1004,推动块1004穿过一字槽1003,挡板802后侧固接有接触块1005,接触块1005向左移动与转动件1002接触,能够挤压其逆时针转动,接触块1005向右移动与转动件1002接触,能够挤压其顺时针转动,转动件1002与固定座1001之间连接有扭力弹簧1006,扭力弹簧1006套在转动件1002上。
41.当挡板802向左移动时,挡板802能够带动接触块1005向左移动,当接触块1005向左移动与转动件1002接触时,接触块1005能够挤压转动件1002带动推动块1004逆时针转
动,扭力弹簧1006随之发生形变,当接触块1005向左移动与转动件1002脱离接触时,扭力弹簧1006随之复位带动转动件1002和推动块1004顺时针转动复位,当挡板802向右移动复位时,挡板802能够带动接触块1005向右移动,当接触块1005向右移动与转动件1002接触时,接触块1005可以挤压转动件1002带动推动块1004顺时针转动,使得扭力弹簧1006再次发生形变,推动块1004顺时针转动从而能够将掉落至放置板4上的防护垫推入箱体内,如此实现了自动推料的功能,当接触块1005向右移动与转动件1002脱离接触时,扭力弹簧1006随之复位带动转动件1002和推动块1004逆时针转动复位。
42.参阅图1和图11所示,还包括有压紧机构11,压紧机构11用于将箱体压紧,压紧机构11包括有支撑板1101、滑动杆1102、压块1103和第二弹性件1104,转动架703上均匀间隔固接有四个支撑板1101,支撑板1101上滑动式设置有滑动杆1102,滑动杆1102底端固接有压块1103,压块1103与支撑板1101之间连接有第二弹性件1104,第二弹性件1104套在滑动杆1102上。
43.当工作人员将包装箱放到两个支撑杆5之间时,包装箱能够将压块1103挤压向外移动,第二弹性件1104随之被压缩,压块1103向外移动能够带动滑动杆1102向外移动,如此能够使压块1103将包装箱压紧,从而能够防止包装箱转动时从转动架703上掉出,当工作人员将包装箱取出时,第二弹性件1104随之复位带动滑动杆1102和压块1103向内移动复位。
44.以上所述仅为本发明的较佳实施例,并不用以限制本发明,凡在本发明的精神和原则之内,所作的任何修改、等同替换、改进等,均应包含在本发明的保护范围之内。